Отливка уретана в сравнении с литьем под давлением — руководство DFM
Проектирование для производства (DFM) включает в себя оптимизацию конструкции деталей, чтобы производители могли изготавливать высококачественные детали с минимально возможной стоимостью единицы продукции. Принимая во внимание метод производства и связанные с ним ограничения, дизайнеры могут сократить время производства, сократить расходы и предотвратить значительные изменения конструкции.
Рекомендации DFM различаются в зависимости от продукта, который вы производите, и выбранного вами метода производства. Хотя литье под давлением и литье из уретана являются технологиями литья, которые могут создавать формованные пластиковые детали, они имеют разные рекомендации по DFM. Вот все, что вам нужно знать.
Отливка уретана в сравнении с литьем под давлением
Прежде чем приступить к изготовлению деталей для литья под давлением, необходимо разработать и изготовить соответствующие инструменты с помощью станков с ЧПУ. Геометрия вашей детали напрямую повлияет на ваши инструменты, поэтому, если у вас есть сложный компонент, вам понадобятся сложные инструменты. Сложные детали, возможно, должны включать в конструкцию пресс-формы скользящие механизмы, подъемники или съемные стержни. В процессе литья под давлением сердечник и полость соединяются. Затем расплавленный пластик будет впрыскиваться в инструмент, охлаждаться, затвердевать и выталкиваться для создания пригодной для использования детали.
Литье уретана начинается с мастер-модели, которая создается с помощью станков с ЧПУ или 3D-печати. Оператор помещает мастер-модель в форму, наполняет ее жидким силиконом, а затем отверждает. После завершения процесса отверждения форму разрезают пополам, чтобы удалить мастер-модель. Остается полость в форме детали, которая будет формоваться. Затем полость заполняется уретановой заливочной смолой и помещается в нагретую вакуумную камеру для отверждения.
- Хотя оба процесса включают заполнение полости формы пластиковым материалом, между литьем уретана и литьем под давлением есть некоторые ключевые различия.
- Формы для литья под давлением часто изготавливают из стали или алюминия, что делает их гораздо более прочными, чем силиконовые формы, используемые при литье уретана.
- Создание формы для литья уретана дешевле, чем создание формы для литья под давлением. Сложные формы для литья под давлением могут стоить десятки тысяч долларов, но изготовление формы для литья уретана обычно стоит сотни или тысячи долларов.
- На стадию производства пресс-формы для литья под давлением может уйти несколько месяцев, однако изготовление форм для литья уретана может занять менее двух недель.
- Литье из уретана более щадящее в отношении толщины стенок и поднутрений, чем литье под давлением.
Если вы планируете крупносерийное производство или имеете жесткие допуски, рассмотрите возможность литья под давлением. Металлические формы более прочные и жесткие, чем силиконовые формы, а металл обеспечивает стабильное качество деталей. Кроме того, у вас будет гораздо больший контроль при литье под давлением по сравнению с литьем из уретана. Производитель может контролировать не только расход материала и скорость охлаждения, но также температуру и место впрыска при литье под давлением. Хотя стоимость изготовления пресс-формы для литья под давлением поначалу может показаться высокой, она становится рентабельной, если разделить ее на тысячи деталей.
С другой стороны, литье из уретана идеально подходит для разработки прототипов или мелкосерийного производства, поскольку мягкие инструменты обеспечивают скорость, гибкость и доступность. Если у вас есть высокий спрос на ваш продукт, но ваша постоянная оснастка еще не готова, вы можете начать производство с литья уретана.
Основные проблемы DFM для литья уретана и литья под давлением
Когда дело доходит до DFM для литья уретана или литья под давлением, вы должны помнить о допусках, толщине стенки и поднутрениях.
Допуски
Ни один производственный процесс не идеален, поэтому дизайнеры и инженеры допускают эти вариации, устанавливая приемлемые допуски. Детали сравниваются с этими допустимыми отклонениями размеров от базовых размеров, поэтому те, размеры которых соответствуют этим ограничениям, будут считаться приемлемыми. Те, размеры которых превышают величину, указанную в допуске, не будут работать должным образом. Эти допуски устанавливаются в процессе проектирования и определяют, какие производственные процессы можно использовать.
Добиться жестких допусков с литым уретаном очень сложно, если вообще возможно, потому что формы изготовлены из гибкого силикона, который может перемещаться под действием вакуумной нагрузки. Вы не должны использовать литой уретан для изготовления своих деталей, если вам нужны невероятно точные компоненты.
С другой стороны, металлические пресс-формы для литья под давлением предлагают меньшую вариацию окончательных измеренных размеров, поскольку они не могут так сильно перемещаться. Однако расплавленный пластик сжимается при охлаждении, что вызывает незначительные отклонения в окончательных измеренных размерах детали. Вам нужно будет установить допуски на пресс-формы, которые отражают это.
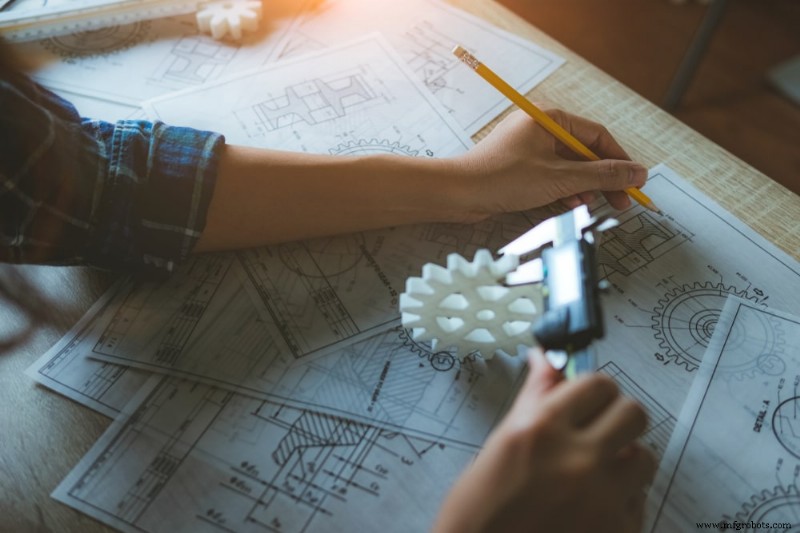
Заниженный допуск может быть более доступным, но он может повлиять на удобство использования, а чрезмерный допуск обходится дороже и требует больше времени. Потратив время на поиск идеального баланса между ними, вы можете быть уверены, что ваши детали надежны, функциональны и совместимы с другими частями, как предполагалось. Учитывайте функцию вашей детали, набор допусков, а также процессы производства и сборки. Если выбранный вами метод производства не соответствует вашим требованиям к допускам, вам может потребоваться использовать другую технологию производства. Вы также можете перепроектировать свою деталь, чтобы она работала с небольшими допусками.
Толщина стенки
Поддержание одинаковой толщины стенок важно, потому что это повышает согласованность между деталями, улучшает распределение напряжений и снижает затраты. Непостоянная или неравномерная толщина стенки может привести к короблению, утяжкам, усадке, недоливу или пустотам в деталях, изготовленных методом литья под давлением.
Идеальная толщина стенки детали зависит от ее размера, геометрии, конструктивных и эстетических требований. Для достижения наилучших результатов мы рекомендуем, чтобы толщина стенок деталей, изготовленных методом литья под давлением, составляла 1–4 мм. При создании деталей из уретанового литья можно иметь стенки разной толщины, хотя во время отверждения может возникнуть некоторая усадка или деформация. Для обоих процессов лучше всего поддерживать толщину стенки менее 5 мм.
Любые выступы или углубления, препятствующие извлечению детали из цельной пресс-формы без повреждений, считаются поднутрениями. В некоторых случаях утопленные поверхности, канавки и выступы могут затруднить процесс извлечения из формы и повредить деталь. В других случаях эти функции не причинят никакого вреда. Это зависит от того, как вы спроектировали и сориентировали эти функции и ваш компонент.
Подрезы
Влияние подрезов также зависит от вашего производственного метода. Благодаря гибкости, которую предлагает силикон для литья уретана, вы можете просто сгибать и растягивать инструмент, чтобы высвободить деталь, если у вас есть подрез. Этого нельзя сказать о металлических инструментах, используемых при литье под давлением, которые гораздо менее гибки. Вашему производителю может потребоваться добавить действия, создать отверстие или прорезь в вашей пресс-форме или перепроектировать вашу пресс-форму с элементами, параллельными оси, где пресс-форма отделяется, чтобы гарантировать, что ваша деталь может быть извлечена. Это приводит к более сложному и дорогому инструментарию.

Дизайн для производства с Fast Radius
Независимо от того, выбираете ли вы литье из уретана или литье под давлением, интеграция DFM в процесс проектирования снизит стоимость детали и сэкономит время. Принимая во внимание метод производства, допуски, толщину стенок и поднутрения при проектировании, вы можете свести к минимуму несоосность деталей и оптимизировать производственный процесс.
Независимо от того, какой производственный процесс вы выберете, Fast Radius может помочь вам спроектировать технологичность, чтобы вы были довольны качеством и стоимостью конечного продукта. Наша команда экспертов может посоветовать вам соответствующие допуски и толщину стенки или помочь вам определить, какой обходной путь поднутрения лучше всего подходит для вашей конструкции. Свяжитесь с нами сегодня, чтобы начать работу.
Промышленные технологии
- Руководство по литью малых объемов
- Что такое реакционное литье под давлением
- Литье против литья под давлением
- Термоформование против реакционного литья под давлением (RIM)
- Литье под давлением против реактивного литья под давлением (RIM)
- Литье под давлением против реакционного литья под давлением
- Литье под давлением против литья под давлением
- Когда вакуумное литье более подходит, чем литье под давлением?
- Дизайн ворот для литья под давлением:полное руководство по производству пластмасс
- Руководство по точному литью