Продвижение крыла, наполненного OOA
Поскольку аэрокосмическая отрасль ожидает выхода из пандемии COVID-19, предыдущий толчок к высокопроизводительному производству превратился в безотлагательную кампанию по снижению экологических угроз для планеты и людей. Эти усилия включают ограничения на выбросы парниковых газов (ПГ), использование энергии и воды и создание отходов, которые не могут быть переработаны. Хотя эти инициативы были действующими до COVID, в настоящее время они усиливаются, так как производство композитных конструкций требует гораздо более низких затрат. Панъевропейская авиационная программа Clean Sky 2 профинансировала исследования и разработки во всех этих областях и значительно продвинула ряд технологий армированных волокном композитов.
В седьмой конкурс предложений Clean Sky 2 (CFP07, октябрь 2017 г.) включен запрос Airbus Defense and Space (Airbus DS, Кадис, Испания) на инновационную и гибкую пилотную установку для производства высокоинтегрированного летающего демонстратора с крылом с крылом с использованием автоматизированного волокна. размещение (AFP) и инфузия жидкой смолы.
Были и другие демонстраторы боксов крыла, наполненные смолой и / или вне автоклава (OOA), в том числе "смешанный" бокс крыла OOA, представленный GKN Aerospace (Реддич, Великобритания) в 2013 году; крыло Airbus A220, произведенное Spirit AeroSystems Belfast в Северной Ирландии с использованием инфузии смолы в автоклаве; и крыло OOA производства «АэроКомпозит» (Москва, Россия) для МС-21 лайнер. Тем не менее, все они собрали отдельные композитные обшивки и лонжероны, усиленные стрингерами, с механическими креплениями (см. «Путь к крыльям OOA с минимальным количеством креплений»).
Корпус крыла, запрошенный Airbus DS в Clean Sky 2, должен был сделать шаг вперед за счет интеграции усиленной нижней обшивки с усиленными передним и задним лонжеронами, что позволило создать более полный модуль без крепежные детали должны быть отправлены для сборки с остальными компонентами крыла.
В этом кессоне крыла также будут использоваться узкие (шириной 0,25 или 0,5 дюйма) сухие ленты из углеродного волокна и высокотемпературные (180 ° C T g ) отверждающие смолы, но с энергосберегающими недорогими системами нагрева и цифровым управлением и моделированием на основе датчиков для прогнозирования и управления обработкой, сокращения циклов проб и ошибок во время разработки и обеспечения быстрого обучения производственного персонала. Эта оцифровка будет развиваться и включать мобильное приложение (приложение) с дополненной реальностью, которое также предоставляет руководства по эксплуатации и техническому обслуживанию, определение последовательности процессов, безбумажный процесс и отслеживание деталей и проекцию моделей CATIA на деталь, чтобы помочь в точном размещении заготовок ребер жесткости и инструментальных вставок. и уплотнительные плиты из армированного углеродным волокном полимера (CFRP)
Этот проект, возможно, наиболее сложный, требовал, чтобы все инструменты и производственное оборудование были портативными и гибкими, простыми для развертывания на любом производственном участке и адаптируемыми для других конструкций и обновлений деталей по мере появления более совершенных технологий управления технологическими процессами, нагрева и композитов 4.0.
Как пояснил руководитель темы Луис Рубио, руководитель отдела разработки композитных материалов - технологий и процессов в Airbus DS, «Конечная цель проекта - продемонстрировать, что альтернативная технология (препрег и автоклав) с более низкими затратами, сокращенным временем выполнения и воздействие на окружающую среду позволяет достичь аналогичных проектных допусков и уровней качества ».
MTorres (Torres de Elorz, Испания) ответил, подав заявку без партнеров. «У нас были все внутренние возможности:AFP, инфузия, сухие ленточные материалы и автоматизация», - объясняет Себастьян Диас, старший менеджер по прикладным технологиям композитов в MTorres. Компания была награждена проектом Innovative Infusion Airframe Manufacturing System (IIAMS), финансируемым в рамках программы Европейского Союза Horizon 2020 в рамках грантового соглашения № 820845, и начала работу в октябре 2018 года.
Демонстрация коробки наружного крыла
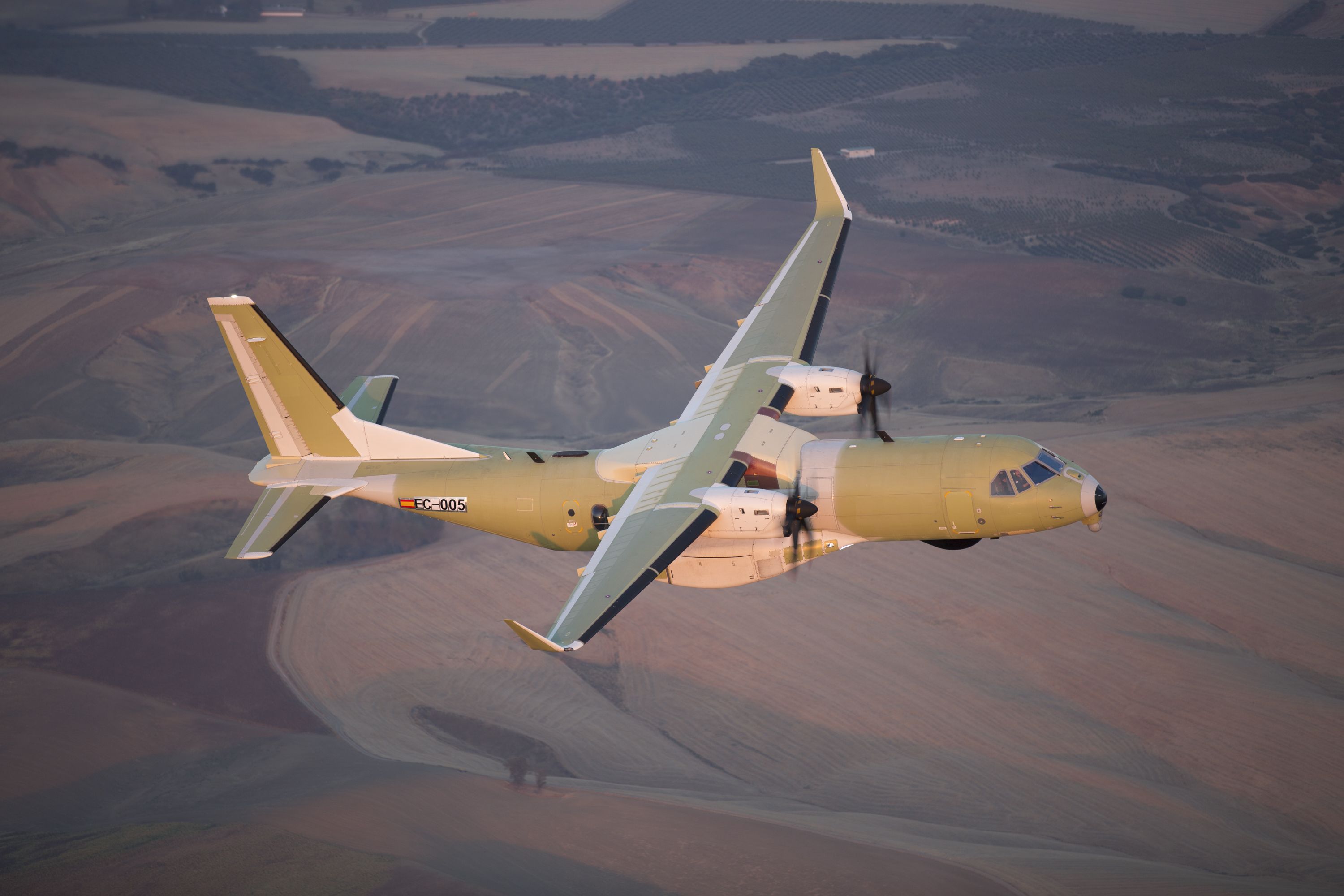
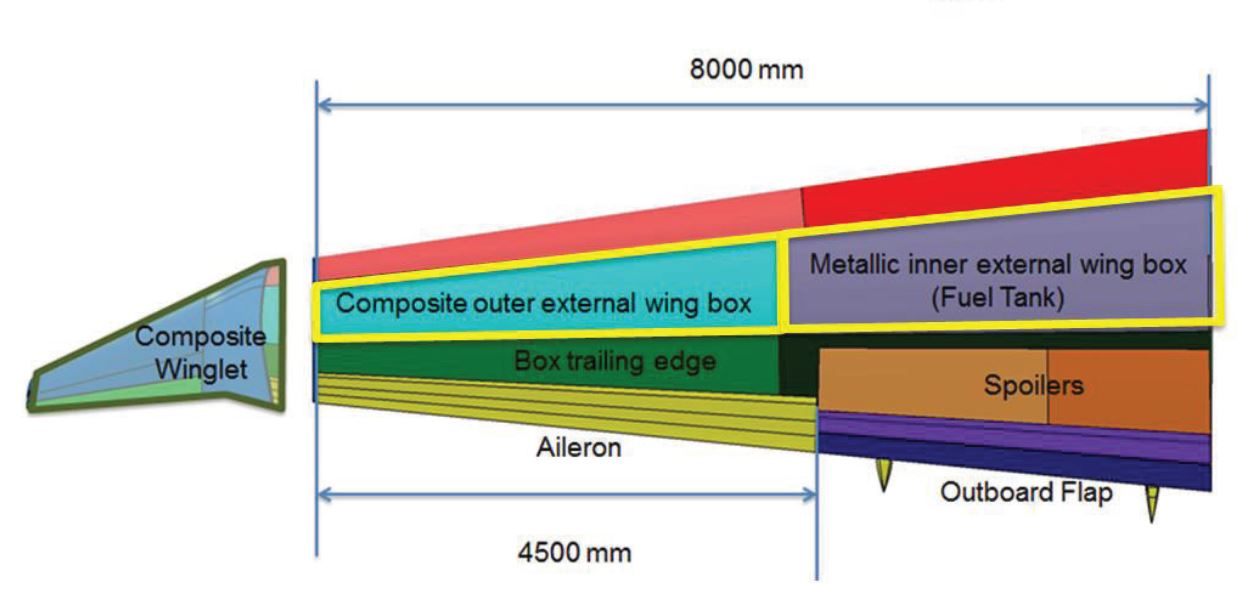
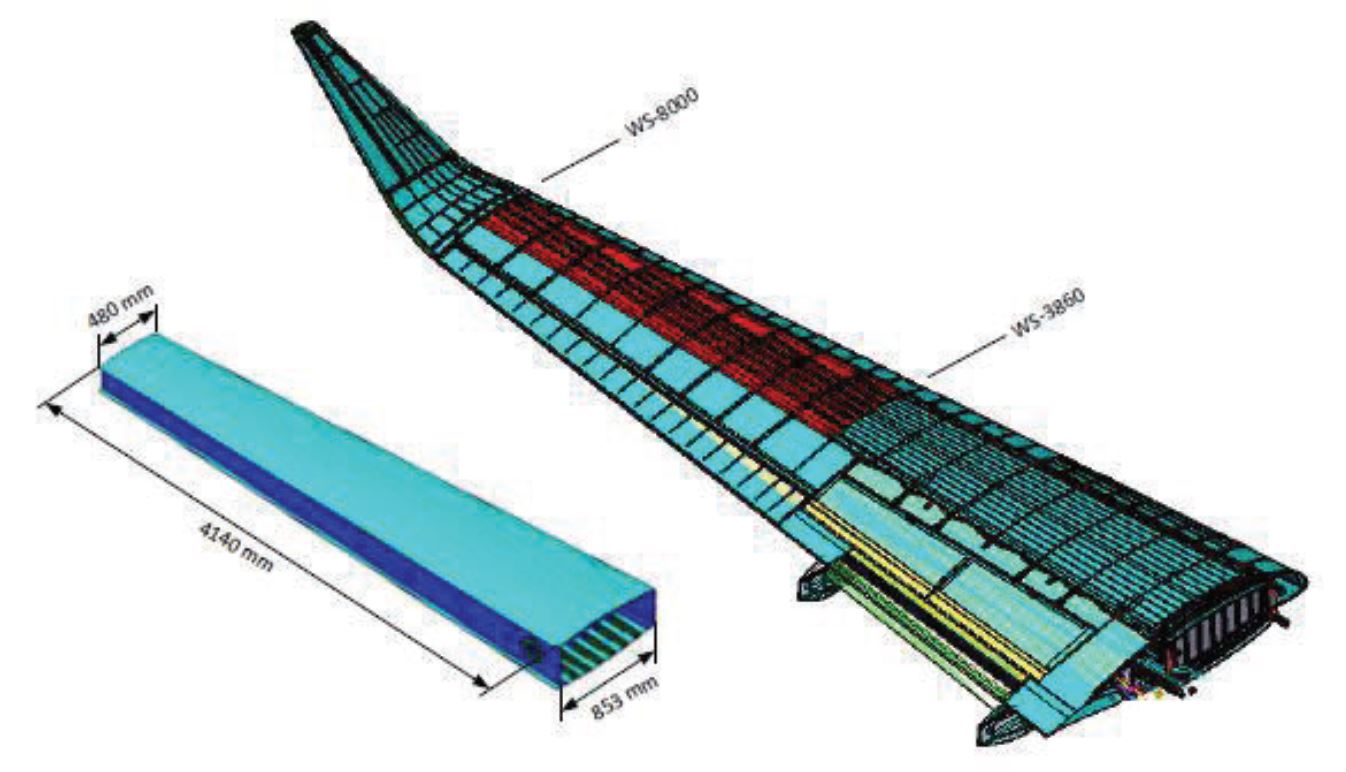
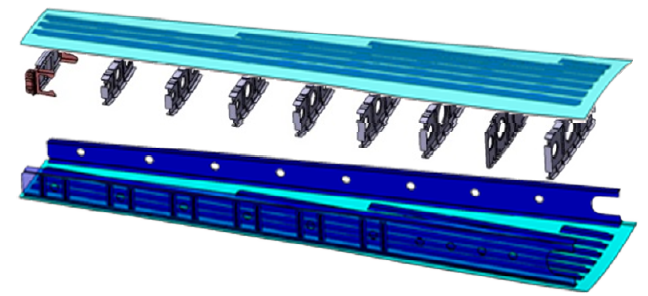
Демонстрационный образец, выбранный Airbus DS, представлял собой кессон внешнего крыла, созданный на базе его военно-транспортного самолета с двумя турбовинтовыми двигателями C-295 (рис. 1), произведенного в Сан-Пабло, Севилья, Испания. Этот композитный подвесной двигатель длиной 4,14 метра соединяется с внутренней металлической торсионная коробка. Составной кессон крыла также прикрепляется к крылышку, передней и задней кромке.
«Мы должны были изготовить два демонстратора длиной 4 метра, правое и левое крыло, которые будут установлены для летных испытаний», - говорит Диас. «Производство должно было быть одноразовым, без вторичного склеивания. Мы сделали только «U», состоящую из нижней обшивки с шестью интегрированными стрингерами и лонжеронами с каждой стороны. Обшивка, стрингеры и лонжероны различаются по толщине. J-образную форму лонжеронов и их элементы жесткости было довольно сложно изготовить. Мы также столкнулись с проблемой сохранения жестких допусков и точной геометрии в этом производственном процессе. Эта точность имеет решающее значение, особенно в основании для сборки к внутреннему кессону крыла, а затем и к крылышку ».
Дизайн инновационного промышленного производства был разработан в MTorres, в то время как Airbus DS предоставила спецификации конструкции деталей. «Мы легко работали вместе, чтобы разработать лучший производственный процесс, убедившись, что этот дизайн может быть произведен с помощью нашего процесса, и наоборот», - говорит Диас.
Автоматизированный центр термоинфузии (ACTI)
Согласно спецификации Airbus DS, все инструменты и производственное оборудование, используемые для производства кессона крыла, должны быть переносными, с возможностью транспортировки на другие объекты на стандартных транспортных средствах и быстрой установкой без специальных мер. Это привело к разработке автоматизированного центра термообработки (ACTI), который выполняет горячее формование стрингеров и лонжеронов; настой стрингеров, лонжеронов и обшивки; и циклы лечения. Формование горячим драпированием (HDF) - разработанное как удаление набухания с подогревом в аэрокосмических конструкциях и предварительное формование с подогревом за пределами авиакосмической отрасли - удаляет пустоты в укладках и преобразует 2D-заготовки для стрингеров и лонжеронов в профилированные преформы (см. «Формование горячего драпирования»).
ACTI имеет полезную внутреннюю площадь примерно 5,5 x 2,2 метра и похож на традиционную систему HDF, со стальной рамой и верхней половиной, которая поднимается и опускается с помощью электроники, в комплекте с блокировкой и другими устройствами безопасности. Инструмент для отверждения и несколько инструментов для формирования горячего драпирования расположены внутри ACTI. «Никакого давления не применяется, только вакуум», - отмечает Диас. «ACTI использует нагретый воздух с воздушным потоком, который обеспечивает быструю теплопередачу как в процессах горячего формования салфеток, так и в процессах инфузии».
Он также отмечает, что система самовыравнивающаяся. «Жесткость конструкции ACTI (и инструмента для отверждения) была разработана с учетом допусков при рабочих нагрузках в условиях простой опоры только на двух опорных секциях», - поясняет Диаз. «Это означает, что точность размеров сохраняется при лежании на полу без необходимости дальнейшего выравнивания или другой геометрической настройки. ACTI также отличается низким энергопотреблением и низкими производственными затратами ».
Последнее в значительной степени связано с заменой сборки нескольких отвержденных деталей сборкой нескольких преформ, которые затем вливаются и отверждаются в единую интегрированную структуру. «Инструмент для отверждения - это также инструмент для сборки», - говорит Диас. «Все элементы представляют собой сухие преформы, собранные в инструмент для отверждения, а затем залитые вместе за один проход». Никакого сборочного приспособления не требуется, а строгие допуски достигаются за счет инновационных элементов в инструментах.
Другой ключевой аспект этого подхода - исключить разрушающие и неразрушающие испытания (NDT), вместо этого полагаясь на данные процесса, собранные на различных этапах производства, для проверки качества процесса и отметки параметров, не соответствующих спецификациям. Датчики, используемые с ACTI, собирают температуру, вакуум, поток смолы и степень отверждения. «Контролируются как температура воздуха, так и температура деталей», - говорит Диас. «Инструмент имеет встроенные термопары, которые отслеживают температуру форм и поверхностей деталей». Все данные записываются, анализируются и используются для печати графиков и помогают принимать производственные решения.
«Как в IIAMS, так и в будущих проектах данные помогают улучшить настройку процесса на ранних этапах», - объясняет Диаз. Поток смолы и состояние отверждения контролируются с помощью диэлектрических датчиков Netzsch (Selb, Германия), устанавливаемых непосредственно в инструменты для отверждения углепластика. «Нам были нужны бесконтактные датчики для кожи, потому что нет прямого контакта между смолой и плесенью», - говорит Диас. «Датчики отслеживают изменение диэлектрического поля по мере того, как смола поступает, а затем становится твердой во время отверждения. Мы использовали эти данные, чтобы сократить цикл лечения ».
Позже в проекте датчики и ACTI были объединены с человеко-машинным интерфейсом (HMI), разработанным MTorres, который позволяет полностью контролировать процесс с компьютера, включая вакуум и температуру, а также поток смолы через подающий клапан. Согласно Airbus DS, цель состоит в том, чтобы продвигать массовое производство интегрированных композитных первичных структур, делая процесс более рациональным и интеллектуальным.
Легкие инструменты и портативность
Компания MTorres изготовила два набора пресс-форм - одну для правого крыла и одну для левого крыла. «Детали с идентичной геометрией, такие как ребра жесткости, имели только один комплект», - отмечает Диас. «По возможности предоставлялись и другие инструменты».
Один цельный инструмент для отверждения использовался для формирования трехмерной формы оболочки, на которой были расположены все остальные преформы. По словам Диаса, правая и левая версии этого инструмента длиной примерно 4,5 метра были изготовлены из углепластика. «Это упрощает соблюдение допусков, потому что мы разработали инструмент с той же компоновкой и обработкой, что и детали, поэтому CTE очень близок к CTE конечной детали. Эти инструменты для вулканизации углепластика также легкие, примерно 200 кг, и поэтому их можно перемещать с помощью небольшого электрического вилочного погрузчика. Это было бы невозможно, если бы мы использовали металл для инструмента длиной 4,5 метра ».
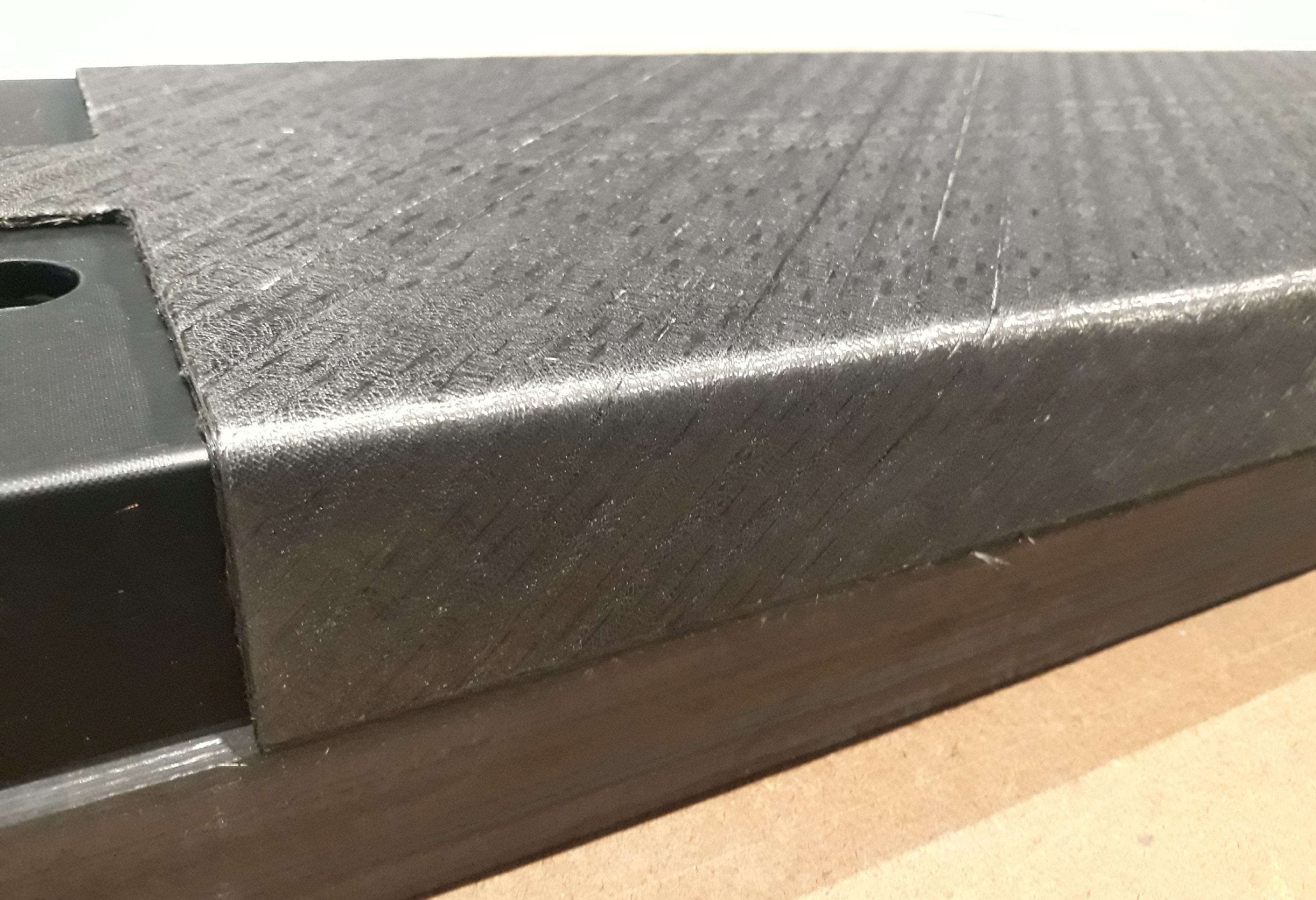
Остальной инструмент - насадки, позиционеры и инструменты HDF - легко обрабатывался вручную. Для HDF стрингеров, лонжеронов и заготовок ребер жесткости использовались инструменты с охватываемой резьбой (IML), также изготовленные из углепластика. Во время использования их устанавливали на алюминиевый стол и устанавливали внутри ACTI.
AFP с использованием новой ленты из сухого волокна
Все конструктивные элементы кессона крыла - обшивка, стрингеры, лонжероны, ребра жесткости лонжерона - были изготовлены по технологии MTorres AFP для лент из сухого волокна. «В объявлении говорилось об использовании быстрых и дешевых материалов», - говорит Диас. «Но коммерчески доступные ленты из сухого волокна, особенно у крупных поставщиков, было не так просто купить, и у нас был опыт, чтобы изготавливать наш собственный материал (см.« Новая сухая лента для жидких формованных композитов »). Итак, мы использовали нашу сухую ленту из углеродного волокна шириной 0,5 дюйма и плотностью 300 г / м2, изготовленную из высокопрочного (HS) волокна 50K компании Mitsubishi Rayon (Токио, Япония). Наша лента была разработана для облегчения и хорошей работы во время инфузии, а также во время укладки с использованием наших головок AFP. Мы знаем все параметры укладки AFP, горячего формования драпировки и инфузии смолы, и, если нам нужно было внести какие-либо небольшие изменения, мы могли бы это сделать, потому что у нас была линия для изготовления ленты ».
Компания MTorres также проверила процесс производства кессона крыла с лентой плотностью 200 г / м2 от Hexcel (Les Avenières, Франция), изготовленной из волокна с промежуточным модулем упругости (IM). «Хотя наш процесс может хорошо работать с обоими типами лент, - говорит Диас, - на этапе разработки было проще и дешевле уложить наш материал по сравнению с имеющимся в продаже материалом - ширина и жесткость были спроектированы таким образом, чтобы его поведение от катушки к столу были гладкими и быстрыми. Он также был легко доступен ».

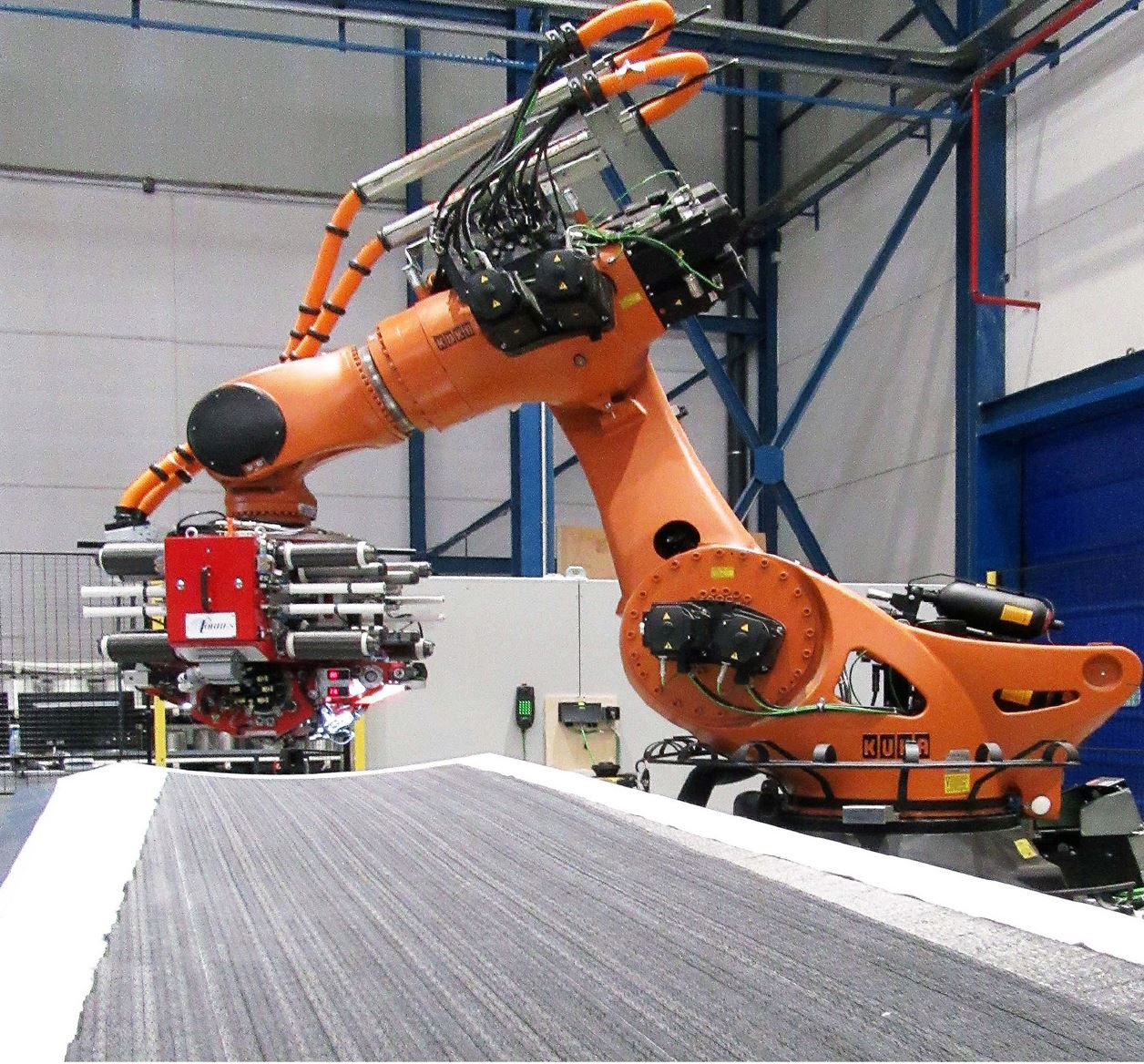
Шаг 1. AFP использовался для сборки обшивки кессона крыла (показано здесь), а также 2D-заготовок для стрингеров, лонжеронов и ребер жесткости лонжерона. Фото кредит, все шаги: Проект IIAMS, Airbus Defense and Space, MTorres.
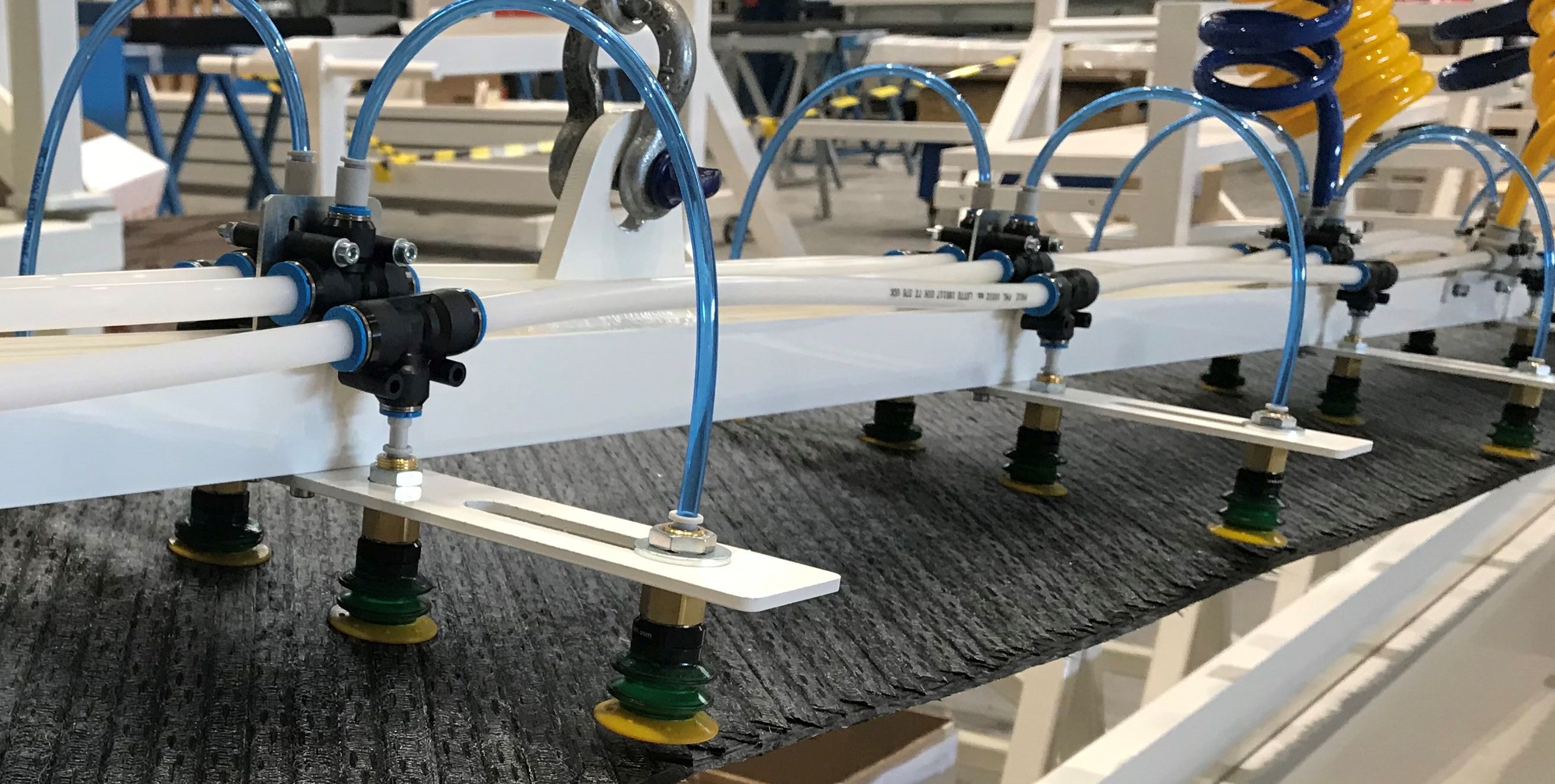
Шаг 2. Заготовки плоской ленты перемещались со стола для раскладки на инструменты для горячего формования драпировки.
Он отмечает, что для AFP использовались две стратегии:одна для нижней обшивки, а другая для стрингеров, лонжеронов и ребер жесткости. Кожа (толщиной 3-6 миллиметров) была наложена на окончательную трехмерную форму поверх инструмента для отверждения (шаг 1) с помощью полупроницаемая мембрана - запатентована Airbus для инфузии с использованием вакуумного процесса (VAP). Стрингеры, лонжероны и ребра жесткости были уложены плоскими заготовками (2D) на вакуумный стол, а затем перемещены на инструменты HDF для достижения их окончательной трехмерной формы (шаг 2).
Предварительное формование с подогревом
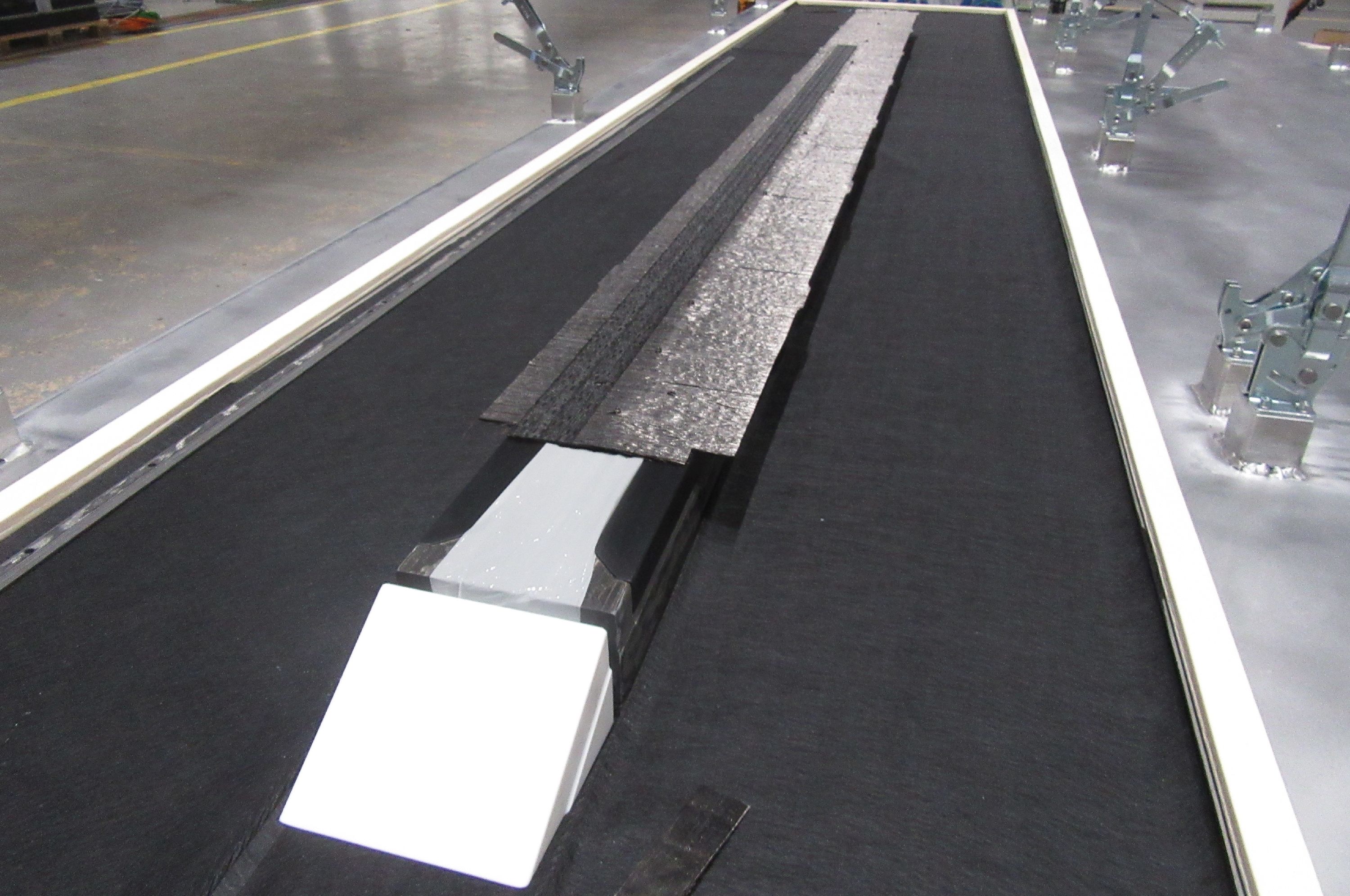
Шаг 3. Заготовка для стрингера помещается на верхнюю часть HDF-инструмента с наружной резьбой.
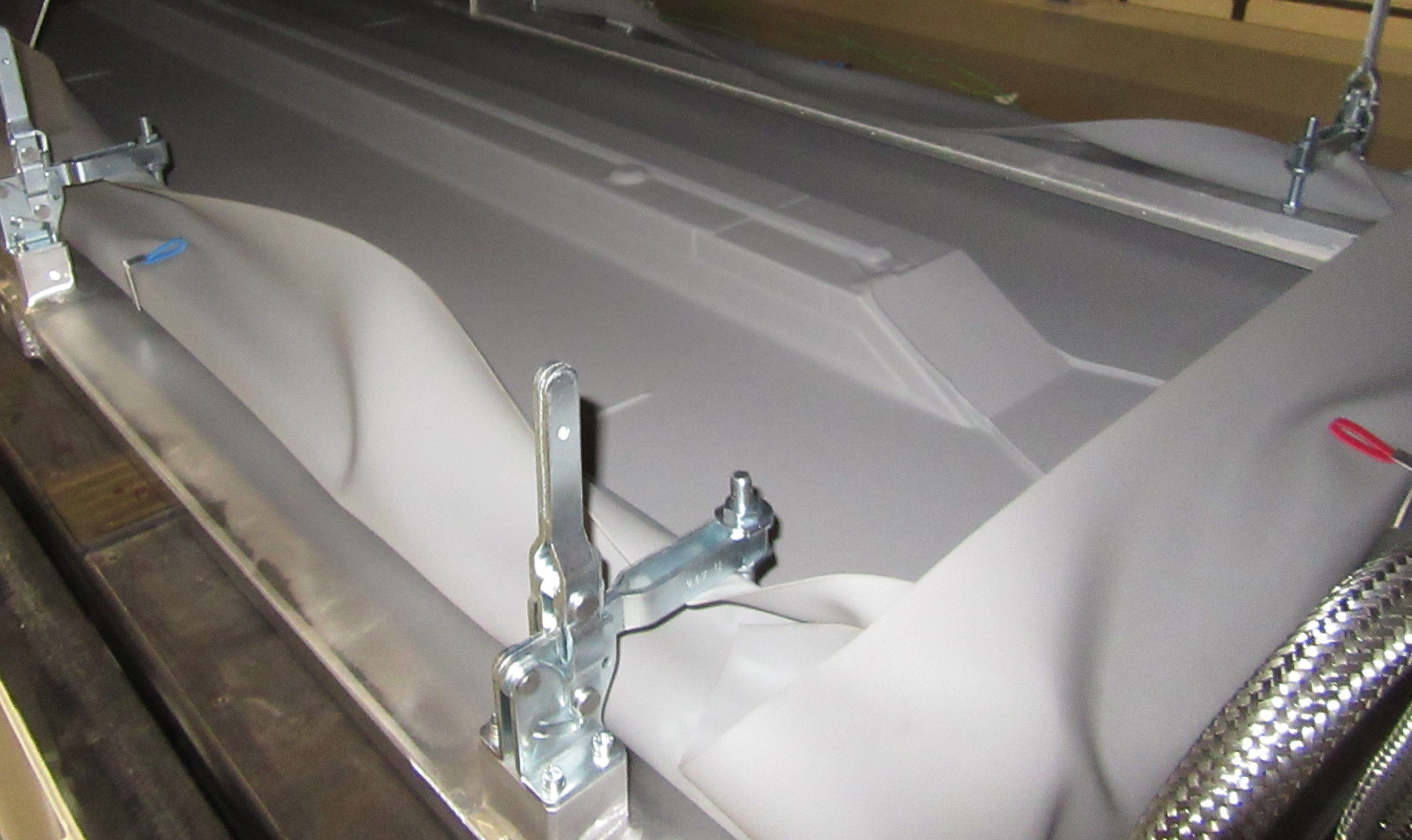
«Мы переместили плоские заготовки для стрингеров, лонжеронов и ребер жесткости со стола укладки на станцию горячей штамповки, используя портал с вакуумными захватами», - объясняет Диас. «Автоматическая система может перемещать заготовки в плоском состоянии и размещать их на инструментах для формовки охватываемых деталей [Шаг 3], не создавая складок». Формовочные инструменты были установлены на алюминиевый формовочный стол, который помещался в ACTI. Силиконовый вакуумный мешок многоразового использования (Mosites Rubber Co., Форт-Уэрт, Техас, США) помещали поверх заготовок, которые затем нагревали в ACTI до 130 ° C и формировали с использованием вакуумного давления (этап 4). «Вакуум плавно подавался по заранее заданному нарастанию с помощью регулирующего клапана при достижении заданного значения температуры», - говорит Диас.
Он отмечает, что сухие ленты легче формовать / горячее драпировать, «потому что связь между слоями мягче, чем в препрегах. Несмотря на то, что это сухой материал, он является HDF / удаление массы с подогревом, при котором полученная преформа сохраняет форму благодаря связующим, включенным в ленты ».
Для стрингеров и ребер жесткости лонжеронов заготовки были сформированы в две L, которые затем были помещены спиной к спине на инструменте для отверждения, чтобы сформировать Т-образные стрингеры / ребра жесткости. Каждый из шести стрингеров обшивки отличается и требует заготовок разной формы для создания преформ. Каждая из 24 ребер жесткости лонжерона также имеет разную длину.
Передний и задний J-образные лонжероны состоят из одной заготовки, имеющей форму буквы С, которая обращена внутрь кессона крыла, и другой заготовки, имеющей форму буквы Z, обращенной наружу - эти две заготовки расположены спиной к спине. Лонжероны также имеют опоры синусоидальной формы на внешней стороне кессона крыла (стрелка на шаге 7). «Мы вырезали форму для опор лонжерона на плоском столе для укладки перед тем, как переместить заготовку на станцию формования», - говорит Диас. «После этого на этом участке нельзя было ничего обрезать или фрезеровать. Заготовки устанавливались прямо на инструмент для штамповки охватываемой детали, при этом ножки лонжерона располагались с левой стороны инструмента, а верхний фланец - с правой стороны ».
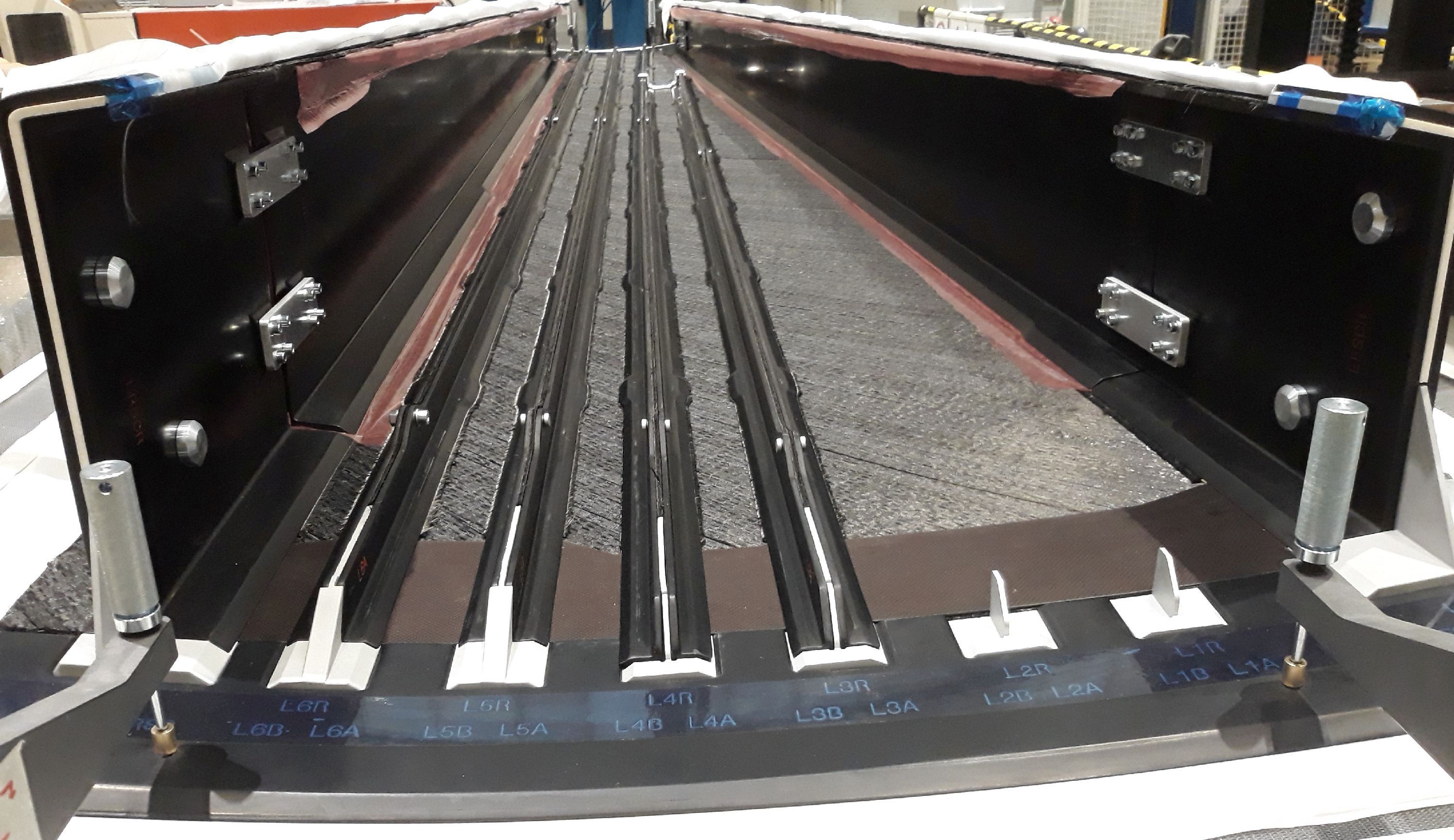
Рис. 3. Точное размещение преформ. Заготовки для J-образных лонжеронов и стрингеров устанавливались с помощью сдвоенных металлических цилиндров (видно слева и справа), белых позиционеров и уплотнителя из углепластика с вырезами для стрингеров / позиционеров. Фото: Проект IIAMS, Airbus Defense and Space, MTorres.
Одноразовая инфузия
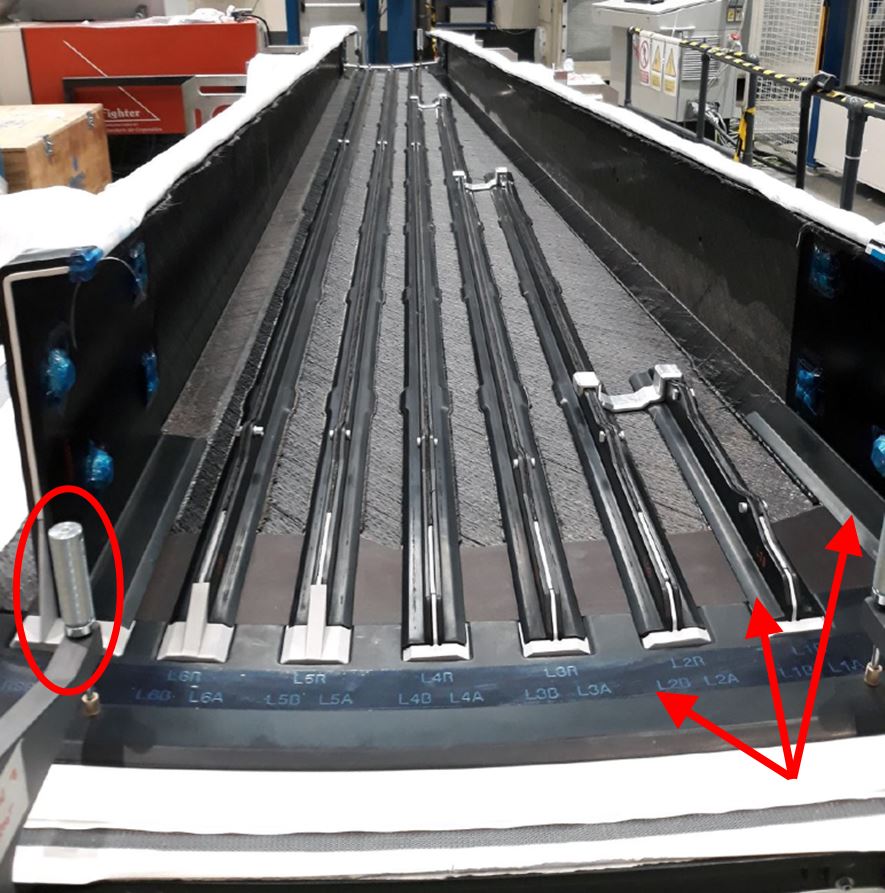
Шаг 5. Заготовки стрингера и лонжерона помещались на нижнюю обшивку с помощью цилиндрических ( обведенных ) и белые элементы позиционирования. Черные уплотнения из углепластика ( стрелки ) также использовались для позиционирования стрингеров и размещены поверх стрингеров и J-образных лонжеронов.
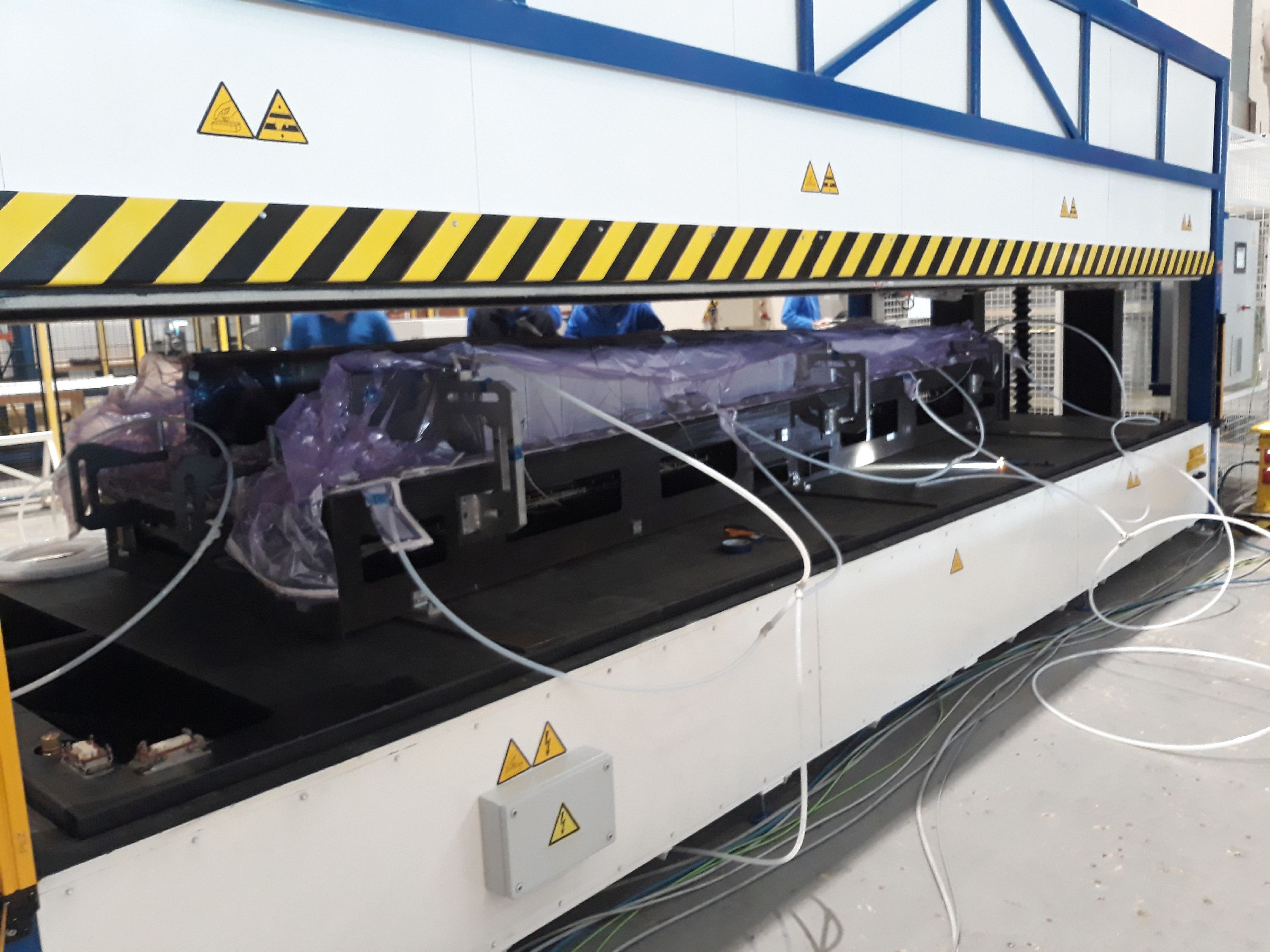
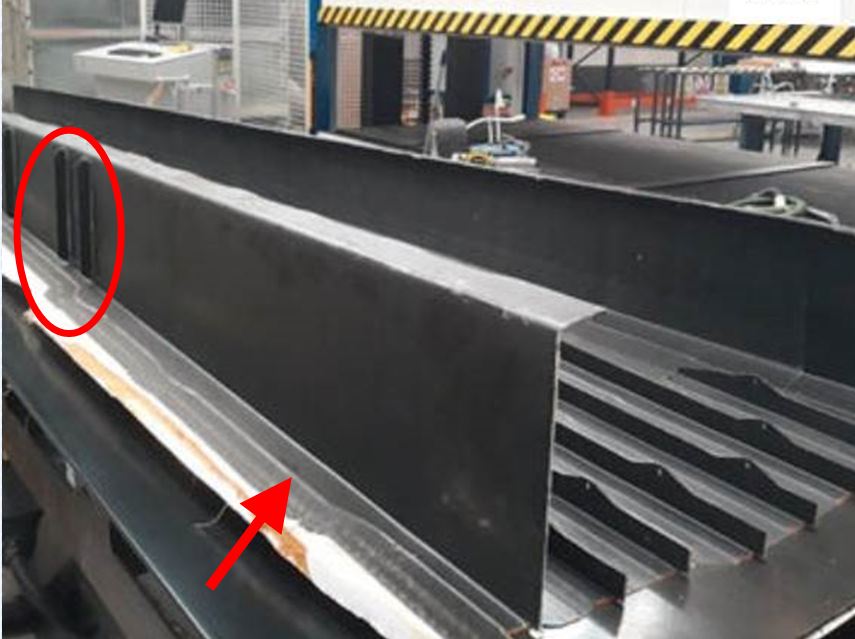
Шаг 7. Первоначальный демонстрационный образец, завершенный в MTorres, показывает J-образный лонжерон с двумя ребрами жесткости ( обведен ) и его синусоидальные ножки ( стрелка ).
Следующим шагом было размещение заготовок стрингера, лонжерона и ребра жесткости лонжерона на уже уложенную обшивку нижней части крыла (шаг 5). «Мы индексировали каждую преформу, когда помещали ее на кожу и закрепляли инструмент», - говорит Диас. Цилиндры, которые действуют как элементы позиционирования, можно увидеть на конце лонжерона слева на этапе 5 и в конце обоих лонжеронов на рис. 3. На этих изображениях также показаны белые устройства позиционирования для стрингеров и J-образных лонжеронов. В окончательной сборке преформы было 13 таких позиционеров, и каждый был другим.
Уплотнительные пластины также были ключевой частью системы расположения и размещения преформ. Они служили традиционной цели поддержания равномерного давления и температуры во всех областях сложной конфигурации и / или геометрии, но также были бы ключевыми для инфузии, как обсуждается ниже. Черная уплотнительная пластина из углепластика с вырезами для преформ стрингеров видна на концах стрингеров и лонжеронов на шаге 5 и на рис. 3.
«Расположение преформ стрингера зависит от расположения этого уплотнения», - объясняет Диас. «Цифровая технология, которую мы разработали для мониторинга и управления производственным процессом, включала приложение дополненной реальности, которое проецировало модели CATIA на укладку. Это использовалось, чтобы помочь направить размещение пластин герметика, позиционирующих элементов, а затем преформ. Он также показал следующие шаги, которые необходимо выполнить. Приложение позволяет автономно работать на планшетных компьютерах, чтобы у всех сотрудников был легкий доступ ко всей информации ».
Последний набор черных уплотнительных пластин из углепластика был затем помещен поверх L-образных преформ для Т-образных стрингеров, а также вдоль внутренней и внешней стороны каждого J-образного лонжерона, проходя вверх на фланец и вниз на основание на внешней стороне Корпус крыла, как показано на шаге 5 и на рис. 3. «В лонжеронах также используется своего рода герметизирующая пластина на внутренней стороне на концах, чтобы обеспечить повышенную точность в местах соединения», - говорит Диас. «Все эти уплотнительные пластины использовались во время процесса HDF и оставались прикрепленными к преформам во время укладки».
Завершенная сборка сухой преформы с герметизирующими пластинами затем была покрыта отрывным слоем и пленкой для вакуумного мешка. Затем весь комплект обшивки, стрингеров и лонжеронов был помещен в ACTI, и инструмент был нагрет до 120 ° C. Эпоксидную смолу Hexcel RTM6 нагревали до 70 ° C и дегазировали перед инфузией через единственное место подачи смолы. «ACTI был подготовлен для подачи смолы из четырех мест, - отмечает Диаз, - но после обширного моделирования и испытаний мы решили, что проще и дешевле иметь одно впускное отверстие для смолы».
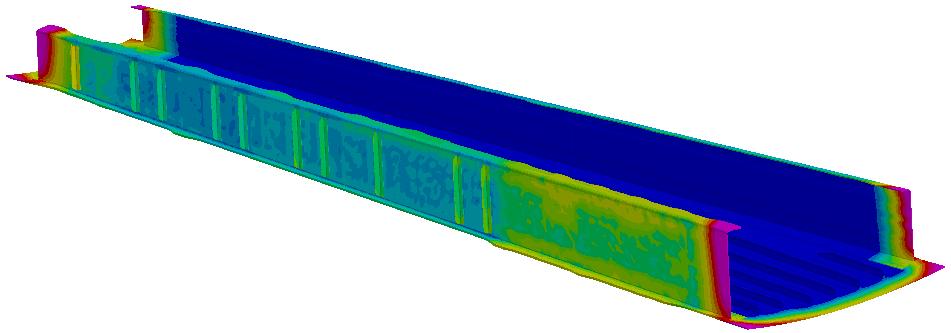
Даже с одним входом процесс инфузии был очень сложным и включал три разных режима. «Сначала мы выполнили моделирование потока с помощью программного обеспечения PAM-RTM [ESI Group, Париж, Франция]», - говорит Диаз. «Для полного смачивания требовалось такое сложное сочетание фронтов потока и параметров. Например, в центре кессона крыла смола текла быстрее, но нам было сложно намочить все ребра жесткости ».
VAP с полупроницаемой мембраной хорошо работал с нижней обшивкой, но ее заменили на высокотемпературную проточную сетку вдоль стрингеров и на внутренней стороне лонжеронов. «Углы были наиболее сложными для смачивания участками, - отмечает Диас, - но они также были наиболее важными для удержания допусков при сборке, а также по краям». Это можно увидеть в красных областях моделирования потока на рис. 4. «В этих областях был разработан индивидуальный подход для достижения требуемых точных размеров», - поясняет он. Мы также использовали вакуумные порты по периметру и поверх лонжеронов ».
Вливание было относительно быстрым, как и было предсказано при моделировании, с последующим двухчасовым отверждением при 180 ° C с использованием только горячего воздуха, а не нагреваемых инструментов. После демонтажа каждый демонстратор кессона крыла был затем проверен с помощью ультразвукового контроля (УЗ). Это было сделано в рамках результатов проекта IIAMS для анализа качества демонстраторов. Однако промышленное применение этого процесса приведет к сокращению традиционного неразрушающего контроля в пользу цифровых датчиков и более быстрых встроенных средств контроля, таких как системы технического зрения.
По словам Диаса, хотя цикл инфузионного отверждения был аналогичен циклу отвержденного в автоклаве препрега с крыльями, общее время цикла должно быть меньше. «Впоследствии мы устранили большую часть сборки, и нам также не нужно использовать какие-либо прокладки, подобные препрегу, но наше качество осталось прежним. Например, для соединения последнего слоя обшивки и первого слоя стрингера не требуется клеящая пленка в середине для улучшения механических свойств и учета допусков ». Это, очевидно, более эффективно, но он отмечает, что скорость производства деталей изначально не была движущим фактором. «Этот метод конкурирует не с производством отдельных деталей, а с законченной сборкой кессона крыла».
Полные демонстраторы, путь к сертификации
«У нас было всего 18 месяцев, чтобы завершить этот проект, который включал в себя разработку процесса и инструментов, а также производство инструментов и демонстраторов», - говорит Диас. «К 14 месяцу у нас был первый демонстратор, готовый для демонстрации в JEC в конце февраля 2020 года [шаг 3], но затем JEC был отменен из-за пандемии. Хотя проект завершился в конце сентября 2020 года, если вычесть месяцы, в течение которых мы не могли работать из-за COVID-19, мы фактически завершили его в месяц 16. Мы смогли выдержать этот очень плотный график благодаря нашим внутренним конструкторским возможностям и возможностям. для изготовления прототипов оснастки на наших фрезерных станках AFP и ЧПУ ».
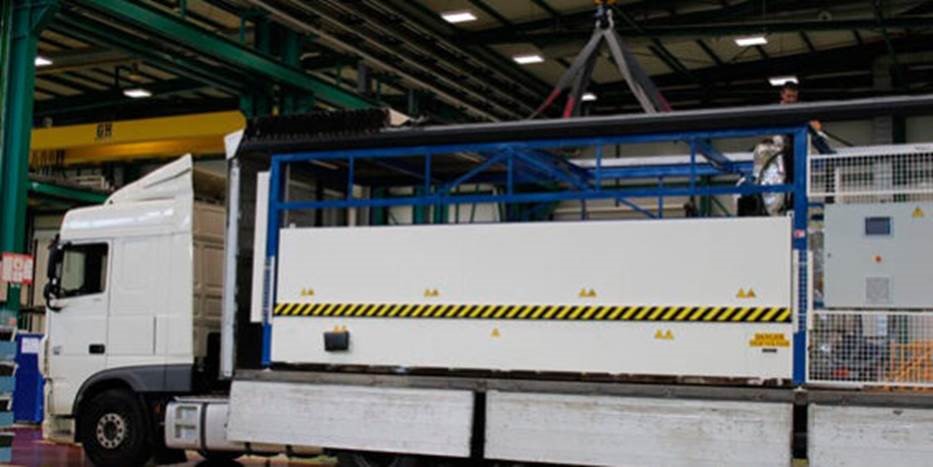
Шаг 8. Оборудование для формования / отверждения ACTI и инструменты кессона крыла были подняты на стандартный движущийся грузовик и перевезены в Airbus DS в Кадисе, Испания.
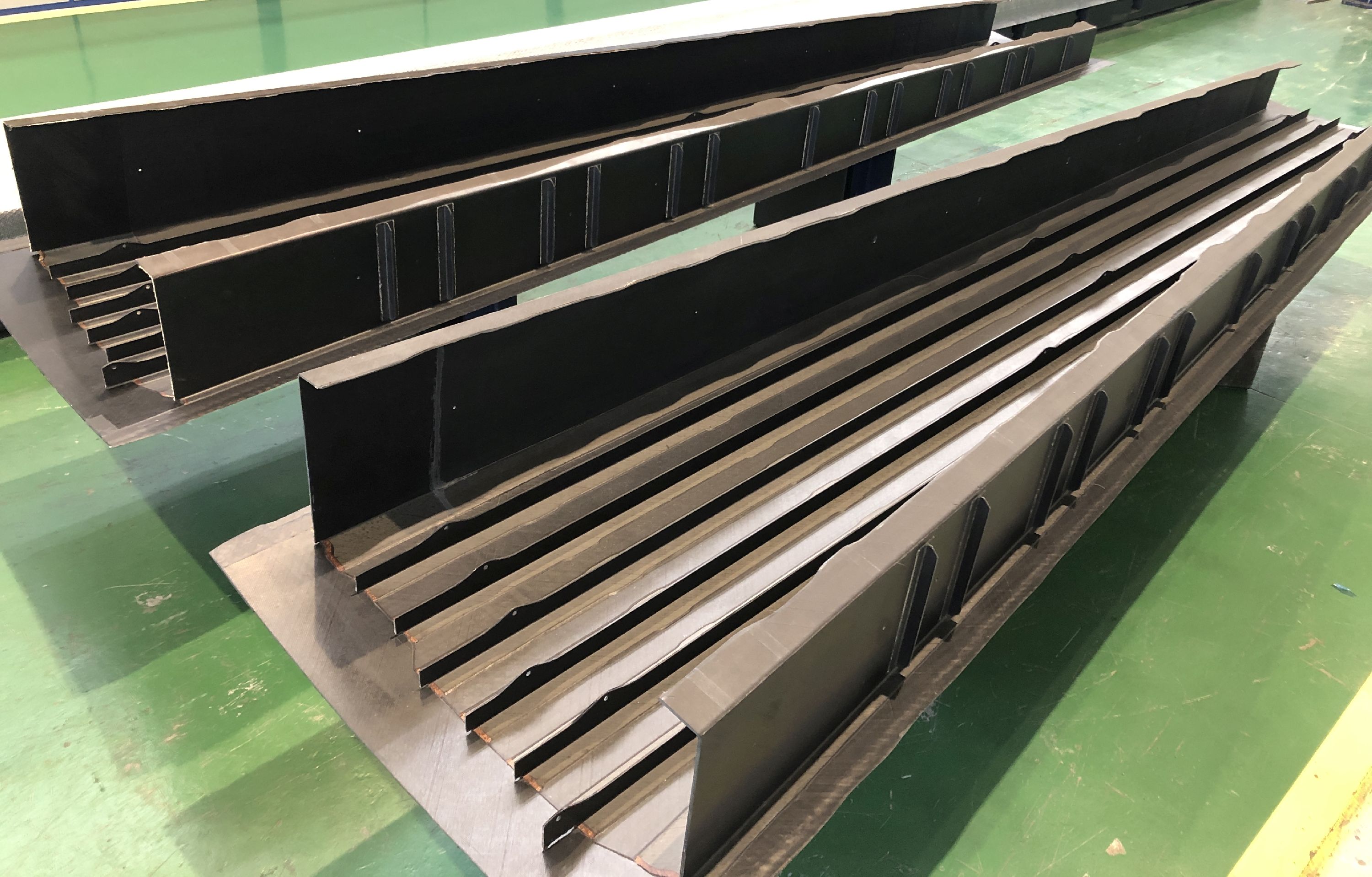
В MTorres был изготовлен упрощенный демонстрационный образец длиной 1 метр для проверки всех параметров процесса. Тогда был изготовлен первый полноразмерный демонстратор. Инструменты и производственное оборудование были затем переведены в Airbus DS в Кадисе (этап 8), где был изготовлен последний демонстрационный образец. Это также было частью результатов проекта, доказывающих, что оборудование можно легко транспортировать и устанавливать в нескольких местах.
Как поясняется во врезке «Дорожная карта крыла IIAMS до сертификации», Airbus DS сыграл ключевую роль в программе Clean Sky, продолжив свое развитие от соруководителя интегрированного демонстратора технологий (ITD) Green Regional Aircraft (GRA) в Clean Sky, соруководителю ITD AIRFRAME, а также руководителю испытательного стенда 2 (FTB # 2) на РЕГИОНАЛЬНОЙ интегрированной платформе демонстратора самолетов (IADP) в Clean Sky 2. FTB # 2 будет включать другие композиты и планер разработки, в том числе в кабине и других компонентах крыла.
Фактически, все проекты по подготовке FTB # 2 являются частью более широкой долгосрочной стратегии Airbus. Цель состоит в том, чтобы разработать будущий турбовинтовой планер, который будет легче и эффективнее, а производственные процессы будут дешевле и потребляют меньше энергии, производят жидкости и вспомогательные материалы, но при этом производят меньше лома и обеспечивают повышенную пригодность для вторичной переработки.
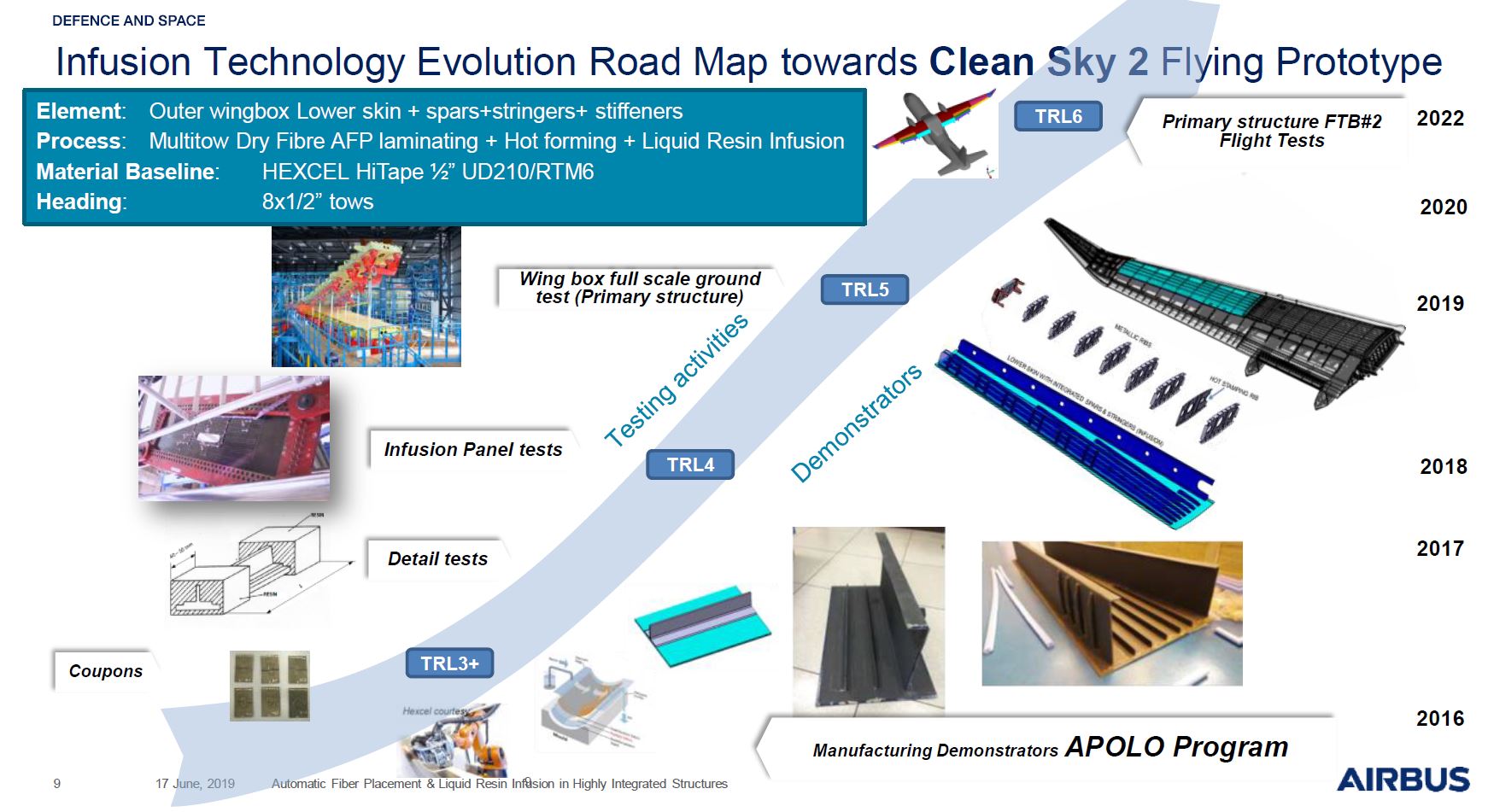
«Шаг за шагом мы [Airbus DS] проходим всю пирамиду испытаний конструкции планера от купонов до полномасштабных структурных испытаний внешнего крыла», - объясняет А.Е. Хименес Гахете в сентябрьском выпуске журнала Materiales Compuestos статья под названием «Высокоинтегрированная секция кессона крыла Airbus Defense and Space, изготовленная путем размещения сухого волокна и вливания жидкой смолы». Испытания характеристик материалов, матрица испытаний деталей конструкции и испытания подкомпонентов для конструктивных допустимых значений были завершены с положительными результатами. Компания MTorres оказала помощь в проведении этих испытаний, включая купоны на производственные испытания и детали, а также демонстрации для проверки процесса изготовления кессона крыла и деталей конструкции. По словам Гахете, остаются только заключительные полномасштабные статические и функциональные испытания внешнего крыла, чтобы получить квалификацию FTB # 2 для полета.
«Однократная инфузия уменьшает суставы, снижает вес и увеличивает прочность», - говорит Диас. «Новая сухая лента, разработанная MTorres, дала отличные результаты как при обработке (AFP, горячее формование и наплавление), так и в отношении структурных свойств детали». Он отмечает, что исторически существовало сомнение в том, что композиты, наполненные смолой, могут соответствовать тем же структурным характеристикам и допускам, что и препрег, отверждаемый автоклавом.
«Достижение таких же допусков при однократном процессе с использованием мягких [неметаллических] инструментов было нашей самой большой проблемой», - признает он. «Но мы доказали, что эта технология работает и может производить большие основные конструкции, необходимые для будущих самолетов. Наш следующий шаг - продолжать продвигать цифровые технологии и переносить производственную систему ».
Смола
- Пигментные порошки придали яркости индустрии пластмасс
- BLB Industries МАЛЕНЬКАЯ КОРОБКА
- Airbus представляет завод будущего
- Посещаете конференцию по периферийной цепочке поставок? Вот как управление цепочкой поставок продвигается
- Развитие современных пластмасс
- История винта
- Vespel®:аэрокосмический материал
- Что такое круговая экономика?
- Продвижение технологий в новом сценарии работы
- Лучший выбор:токарный станок с ЧПУ Box Way