Оцените, не сломайте — испытание на твердость и литейный цех
Важный шаг в оценке металлических деталей с использованием неразрушающего подхода
Испытание на твердость — это проверка качества, используемая на литейных заводах для измерения свойств литых металлов и их пригодности для различных применений. Его популярность обусловлена неразрушающим характером испытания и его связью с другими механическими свойствами. Литейщики делают вывод о растягивающем напряжении материала на основе результатов теста на твердость.
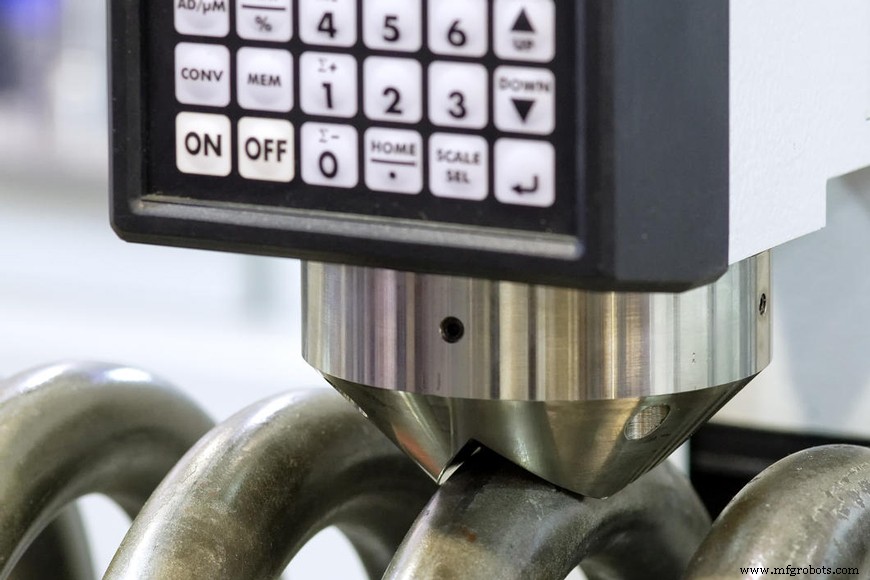
Свойства литых металлов различаются в зависимости от состава металла, условий процесса и термической обработки. Важно сертифицировать изделия из литого металла как пригодные для желаемого конечного применения. Для пользователей литых металлов важны четыре основные категории свойств:
- Сила
- Влияние
- Твердость
- Коррозионная стойкость
Литейные заводы иногда отливают пробный образец вместе с отливкой изделия. Предполагается, что результаты проверки качества на контрольном образце также верны для литого изделия. Некоторые испытания, такие как растяжение и удар, разрушают образец в процессе. Однако неразрушающие испытания (НК) не разрушают образец металла для получения результата. Преимущество неразрушающего контроля заключается в том, что испытания можно проводить на самом литом металлическом изделии, а не на образце.
Преимущества испытаний на твердость:
- Возможность проверки термообработки детали в операциях термообработки и анализа глубины корпуса
- Возможность определить, обладает ли материал необходимыми свойствами для предполагаемого использования.
- Альтернатива неразрушающему контролю для эффективной оценки и выпуска материалов или компонентов для целевых приложений
- Низкая стоимость и высокая производительность
Что такое испытание на твердость?
Термин твердость , как правило, подразумевает устойчивость к деформации. Для металлов свойство является мерой их сопротивления постоянной, или пластической, деформации. Существует несколько различных тестов для измерения твердости металлов и литых металлов.
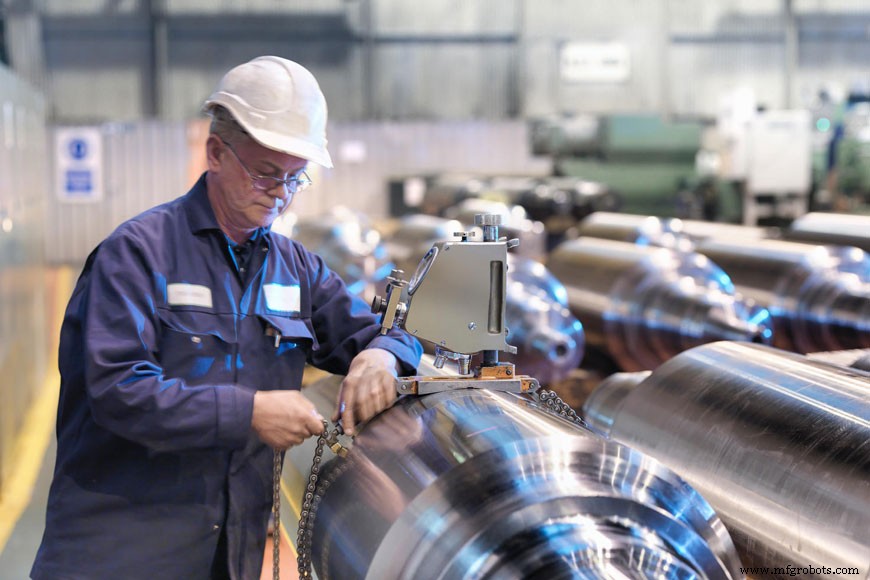
Тест по Бринеллю
В тесте на твердость по Бринеллю используется метод ASTM E10 — Стандартный метод определения твердости металлических материалов по Бринеллю. Американское общество испытаний и измерений (ASTM) является хранителем этого стандарта. Это тест на вдавливание макросов, при котором для измерения используется высокая нагрузка. Литые металлы требуют испытаний на макротвердость из-за грубой структуры зерна и потенциальной неоднородности материала.
Чтобы получить число твердости по Бринеллю (BHN), карбидный шарик фиксированного диаметра вдавливается в металл при фиксированном давлении в течение заданного времени. После снятия нагрузки оператор измеряет диаметр оставшейся вмятины и преобразует его в BHN по следующей формуле:
\(BHN={2PoverπD(D-sqrt{D^2-d^2})}\) П =приложенная сила (кгс)
D =диаметр индентора (мм)
d =диаметр вдавливания (мм)
В Соединенных Штатах испытательные нагрузки для стали и железа обычно устанавливаются не более 3000 кгс с 10-миллиметровым шаром. Алюминий использует меньшую испытательную нагрузку 500 кгс, а иногда и меньший индентор 5 мм. Типичный BHN колеблется от 50 до 750 для металлов. В приведенной ниже таблице «Твердость по Бринеллю» Engineering Toolbox перечислены несколько примеров BHN:
Материал
Число твердости по Бринеллю
Мягкая латунь
60
Мягкая сталь
130
Отожженная долотообразная сталь
235
Белый чугун
415
Азотированная поверхность
750
Подготовка поверхности металла для испытания на твердость по Бринеллю очень важна. Зубчатая поверхность или другие дефекты повлияют на результат. При подготовке к тесту рекомендуется отшлифовать металлическую поверхность, чтобы свести к минимуму вариабельность результатов.
Истоки теста на твердость по Бринеллю восходят к 1900 году. В первые годы испытаний на результаты сильно влияла точка зрения оператора. Разные операторы будут получать разные результаты, что приведет к большой изменчивости измерений. Однако с внедрением электронного измерительного оборудования уровень согласованности значительно улучшился.
Испытание на твердость по Роквеллу
В тесте на твердость по Роквеллу используется метод ASTM E18 — Стандартные методы определения твердости металлических материалов по Роквеллу. Тест Роквелла состоит из двух этапов. Оборудование прикладывает к образцу предварительное испытательное усилие с помощью алмазного или шарикового индентора. Целью этого этапа является пробитие поверхности металла и снижение влияния отделки поверхности на конечный результат. В этой точке оператор измеряет базовую глубину отпечатка. После удерживания предварительной нагрузки в течение заданного времени применяется основная нагрузка. Опять же, усилие удерживается в течение заданного времени, прежде чем снова уменьшить его до усилия предварительного натяга. По истечении времени оператор измеряет глубину отпечатка. Число твердости по Роквеллу основано на разнице между исходным и окончательным измерениями глубины.
Для точности теста Роквелла важно, чтобы ось теста находилась в пределах двух градусов от перпендикуляра. К тесту прилагается шкала твердости Роквелла.
\(RHN={N-(h/S)}\) Н =константа
S =единица измерения
ч =глубина отступа
Испытание на твердость по методу Лееба
В тесте Leeb используется ASTM A956 — Стандартный метод испытаний стальных изделий на твердость Leeb. Тест Лееба — это мера отскока объекта от тестового образца. Твердость металлов влияет на энергию отскока:более твердые материалы дают больший отскок, а более мягкие материалы гасят энергию отскока. Скорость объекта до и после удара об образец формирует основу для значения отскока. Испытательное оборудование Leeb содержит катушку, которая измеряет индуцированное напряжение магнитного шарика, используемого для испытания на отскок. Это индуцированное напряжение напрямую связано со скоростью шарика, движущегося через катушку испытательного оборудования. Значение твердости Leeb рассчитывается по следующей формуле:
\(LHN={Отскок;Скорость над ударом;Скорость}x1000\)Преимущества метода Либа заключаются в том, что отпечаток, оставленный на образце для испытаний, намного меньше, чем при использовании других методов. Он также портативный, простой в использовании и более быстрый, чем твердомеры по Бринеллю и Роквеллу. Недостатком является то, что он может давать разные результаты, если поверхность образца неровная. Толщина образца и содержание углерода также могут повлиять на результат.
Преобразование числа твердости
ASTM E140-12be1 дает стандартные таблицы преобразования твердости для металлов для преобразования одного метода определения твердости в другой. Важно отметить, что эти преобразования являются приблизительными и зависят от таких факторов, как состав материала, микроструктура и термическая обработка. Хотя таблицы основаны на большом количестве тестов с использованием различных методов, результат преобразования можно рассматривать только как оценку сопоставимых значений.
Количество твердости и термообработка
Литые металлы подвергаются термообработке для изменения их свойств. Термическая обработка заключается в повышении температуры материала до заданного значения. Затем его охлаждают с определенной скоростью в зависимости от желаемых свойств продукта. Конечная температура цикла нагрева и скорость охлаждения напрямую влияют на микроструктуру металла.
Тонкие микроструктуры перлита и феррита, вызванные более высокой скоростью охлаждения, имеют большее значение твердости. Если металл подвергается закалке, быстрое охлаждение приводит к образованию мартенситной микроструктуры, обладающей наибольшей твердостью. Из-за прямой зависимости между микроструктурой и твердостью испытание на твердость является быстрым индикатором того, была ли термообработка успешной или нет.
Количество твердости и свойства литого металла
Таблицы показывают, как прочность на растяжение коррелирует с твердостью для конкретных материалов. Это полезная корреляция, поскольку измерение растягивающего напряжения является разрушительным процессом, в то время как испытания на твердость не являются разрушающими. Однако существуют ограничения на преобразование твердости в прочность на растяжение, и эти таблицы являются приблизительными.
Связь между числом твердости по Бринеллю и растягивающим напряжением:
\(TS(MPa)=begin{cases}3,55 cdot HB(HB le 175 )[2ex]3,38 cdot HB(HB>175 )end{cases}\)\(TS(psi)=begin{cases}515 cdot HB (HB le 175 )[2ex]490 cdot HB(HB>175 )end{case}\)ХБ =твердость материала по Бринеллю (измерена стандартным индентором и нагрузкой 3000 кгс)
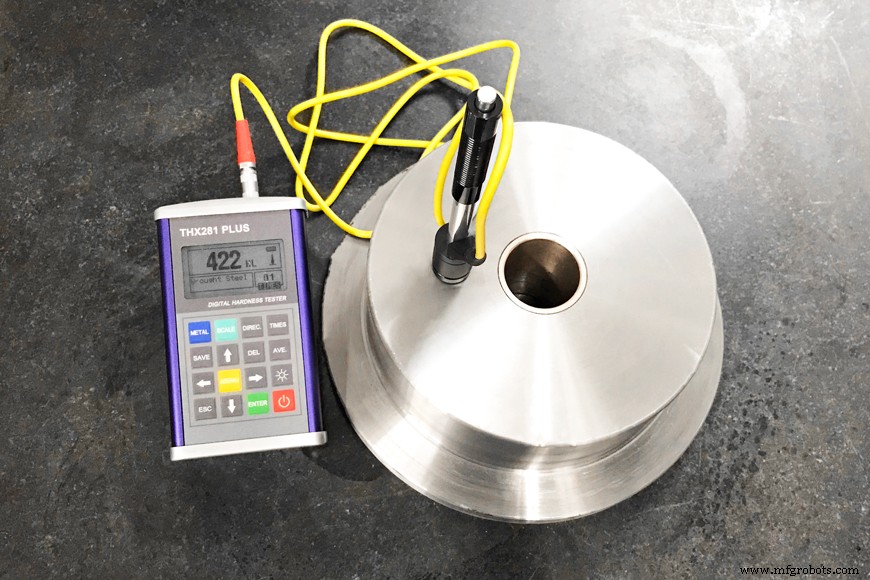
Отливки и сортировка
Многие факторы влияют на маркировку стального литья. Состав продукта, химические и механические свойства, а также процессы термообработки — все это играет роль в сертификации каждого литого продукта в соответствии с применимым стандартом ASTM.
ASTM устанавливает стандартные спецификации для различных марок металлических изделий. Важно понимать эти марки и их свойства, чтобы выбрать правильную марку для каждого применения. ASTM A27 – это стандарт, который распространяется на отливки из углеродистой стали общего назначения.
Испытания на твердость в литейных цехах
Разработка теста на твердость упростила для литейных заводов оценку свойств своей продукции на основе одного простого теста. Он неразрушающий, что означает, что его можно проводить на готовых изделиях, не вызывая повреждений. Это быстрый процесс, позволяющий литейщикам быстро получать информацию о продуктах, покидающих производственную линию. Корреляция между числом твердости и пределом прочности при растяжении является полезным ориентиром для первоначальной оценки класса продукта. Литейные заводы проходят полный набор сертификационных испытаний перед выпуском продуктов клиентам.
Измерение твердости также помогает литейным предприятиям проверять свои процессы термообработки. Результаты показывают, изменилась ли микроструктура материала, как ожидалось. Измерение твердости — важнейший компонент контроля качества и настройки технологических процессов на литейных заводах.
Производственный процесс
- В чем разница между AU и OEE?
- Разница между автоматизацией роботизированных процессов и автоматизацией тестирования
- Срок службы башенных кранов (и почему важны регулярные испытания)
- Испытания под нагрузкой и требования к мостовым кранам и подъемникам
- Будущее тестирования:автоматизация и коллаборативные роботы
- 16 Раздел 2:Определение твердости
- Функциональность и усовершенствование подшипника
- Фрезерный шпиндель и замечательные приложения
- Токарный центр и соответствующая обработка
- Основы снятия фаски и удаления заусенцев