Что такое формирование? Типы процесса формовки [Примечания и PDF]
Формование является одним из важных методов производства в современном машиностроении. Почти многие предметы, которые используются в нашей повседневной жизни, изготавливаются методами или процессами формовки.
Вот некоторые примеры:шарик, используемый в шариковой ручке, гидравлические и пневматические клапаны, контейнеры для зубной пасты, емкости для приготовления пищи, цепи, лопасти вентилятора. и т. д.
Формовка металлов широко используется во всем мире благодаря своим положительным преимуществам, таким как экономичность, улучшенные механические свойства, высокая прочность, повышенная производительность и улучшенная экономия материалов.
Формовка нашла применение во многих областях, таких как аэрокосмическая, автомобильная и оборонная промышленность.
В типичном автомобиле используются такие детали, как колесные диски, кузов, шасси, клапаны, изготовленные методом штамповки.
В этой статье мы изучим что такое формование и какие существуют типы процессов формования. ? в деталях. А дальше мы также увидим преимущества, недостатки и области применения. .
История процесса формирования
Обнаружение медного кулона в северном Ираке около 8700 г. до н.э. считается первой известной промышленной добычей и обработкой металлов. Добыча меди была зарегистрирована в Северной и Южной Америке еще в 4000–5000 годах до н. э. на озере Мичиган.
Со временем металлы становились все более важными для их отдельных цивилизаций, становясь необходимыми для строительных работ, а металлообработка стала важным компонентом общества.
Искусство работы с металлом в настоящее время охватывает широкий круг профессий и отраслей.
Формовка и обработка металлов – это специальность для многих людей. С древних времен технологии претерпели значительные изменения, и в настоящее время большую часть формообразования металлов выполняют машины.
Например, профилирование осуществляется с использованием высококачественного профилегибочного оборудования. Профилирование – это метод сгибания непрерывной полосы металла в определенную форму.
Профилегибочная машина состоит из ряда валков, которые непрерывно изгибают металл в заданную форму. Каждая пара валков изгибает лишь небольшую часть металла, также известную как пряди. Металл прокатывается до тех пор, пока он не будет соответствовать требованиям.
Эволюцию металлообработки можно увидеть в искусстве изготовления валков. Использование профилегибочного станка и другого профилегибочного оборудования является примером того, как металлообрабатывающая промышленность развивалась с течением времени.
Что такое процесс формирования?
Формование металла – это процесс изготовления компонентов желаемой формы путем пластической деформации материала путем приложения силы сжатия, изгиба или сдвига, силы растяжения или комбинации всех этих сил без добавления или удаления материала.сильный>
Типы процесса формирования
Процесс формования был разделен на две группы; Объемное формование и формование листового металла .
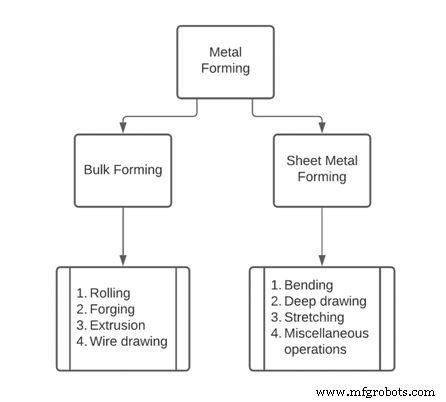
Далее подробная классификация процесса формовки, как вы можете видеть на макете выше.
Теперь мы подробно познакомимся со всеми типами.
#1. Массовое формирование
Формование в массе – это метод производства материалов, больших объемов продуктов, площадь поверхности которых меньше объемного отношения. .
Здесь, чтобы выполнить механическую обработку, обрабатываются силы растяжения, силы сжатия, силы сдвига или их комбинация.
Осуществляется на станке, который имеет набор инструментов и штампов. Использование инструмента и самого штампа дает нам понять, что штамп имеет ту же форму, что и продукт, который нужно произвести, и инструмент прижимается к штампу, чтобы создать форму на материале.
Массовое формование включает в себя процессы, называемые прокаткой, ковкой, экструзией и волочением, в качестве рабочих процессов.
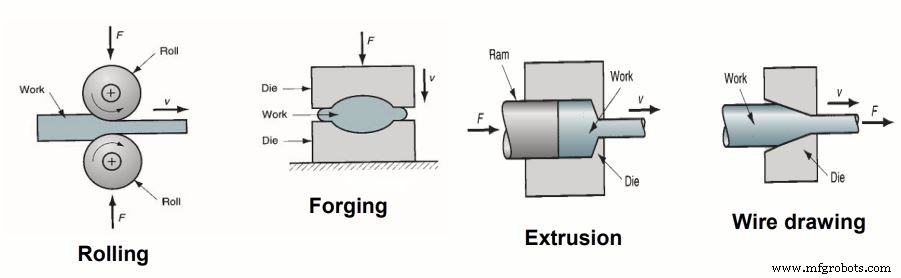
1.1 Роллинг
Прокатка является типичным процессом формования, используемым для производства полуфабрикатов, таких как стержни, листы и пластины, а также готовых изделий, таких как уголки, U-образные профили и профили. Прокатку можно производить как в горячем, так и в холодном виде.
В этом процессе заготовка в виде сляба сжимается между двумя валками, которые вращаются в противоположном направлении, уменьшая таким образом толщину заготовки и придавая ей новую форму. Вращающиеся ролики вытягивают плиту в пространство и сжимают ее. Конечным продуктом является уменьшенный размер заготовки.
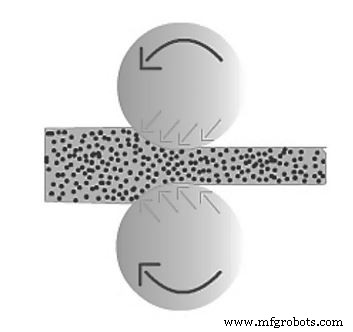
Со временем появилось множество прокатных станов для производства изделий различной формы. Каждый из них описан ниже.
1.2 Двухвалковый прокатный стан
Двухвалковый прокатный стан состоит из трех отдельных клетей с двумя горизонтальными валками, установленными друг над другом.

В мельницах этого типа можно регулировать один или оба ролика. Металл пропускают между двумя роликами, которые во время работы вращаются с одинаковой скоростью, но в разных направлениях.
1.3 Трехвалковый прокатный стан
В случае трехвалкового прокатного стана имеется три валка, один над другим. Два рулона будут использоваться одновременно для одного прохода. В этом случае направление вращения не изменится.
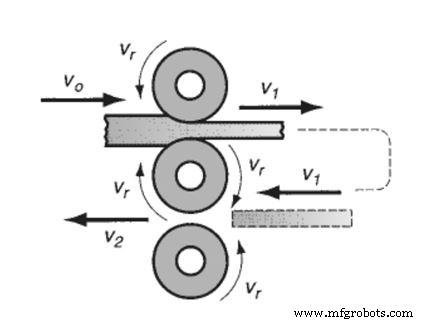
Лист будет перемещен на два нижних вала для дальнейшего обжатия после того, как два верхних вала будут использованы для первого обжатия. Этот цикл повторяется до тех пор, пока не будет достигнуто желаемое уменьшение.
1.4 Четырехвалковый прокатный стан
Четырехвалковый прокатный стан состоит из двух небольших валков, используемых для уменьшения толщины, и двух больших опорных валков, используемых для поддержки малых валков.
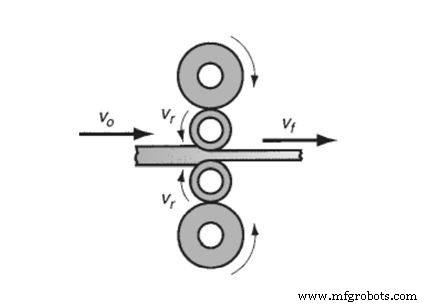
Поскольку площадь контакта с листом рулона с короткими роликами уменьшается, требуемое усилие прокатки снижается.
Большие опорные ролики необходимы для уменьшения упругого прогиба маленьких роликов, когда лист проходит между ними.
1,5 Cluster Mill
Кластерная мельница состоит из двух рабочих валков и четырех или более опорных валков.
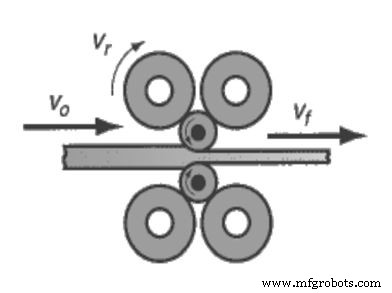
Количество необходимых опорных или опорных валков определяется количеством опор, необходимых для рабочих валков (малого диаметра). Кластерные станы обычно используются в операциях холодной прокатки.
1.6 Прокрутка кольца
Прокатка колец – это метод формирования, при котором толстостенный кольцевой компонент меньшего диаметра прокатывается в тонкостенное кольцо большего диаметра.

По мере сжатия толстостенного кольца деформированный материал удлиняется, что приводит к увеличению диаметра кольца.
1.7 Форжинг
Ковка — это метод объемного формования, при котором к заготовке или заготовке прикладывают силы сжатия и растяжения для превращения ее в конечный продукт с использованием пары инструментов, называемых штампом и пуансоном.
Для ковки могут использоваться открытые или закрытые штампы. В большинстве случаев ковка в открытых штампах используется для придания сырью формы, подходящей для последующего формования или механической обработки.
В этом процессе заготовка сжимается между двумя штампами. Матрицы содержат фигурный контур, который должен быть создан на конечном изделии. При сжатии заготовки между парой штампов заготовке придается форма, в результате чего получается конечный продукт.
1.7.1 Ковка в открытых штампах
Для таких операций, как вытяжка, утонение и т. д., открытые штамповки выполняются с помощью двух штампов с плоской поверхностью.
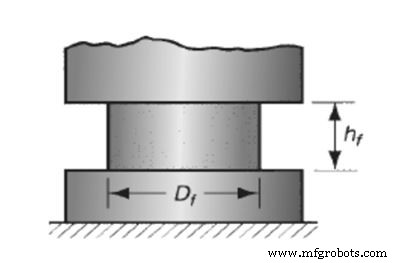
Ковка в открытых штампах является жизненно важной технологией в различных отраслях промышленности.
Он позволяет выполнять черновую и чистовую обработку металлов, особенно стали и стальных сплавов. Для этого требуется матрица с открытыми сторонами, которая позволяет заготовке свободно перемещаться в боковом направлении при ударе. Эта конструкция также позволяет ковать очень большие заготовки.
1.7.2 Ковка в закрытых штампах
Ковка в закрытых штампах осуществляется путем сжатия заготовки сырья в полость, образующуюся между двумя фигурными штампами.
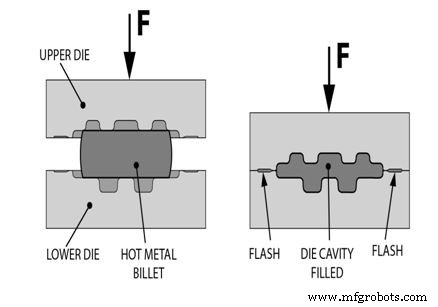
Форма полости штампа достигается формованием изделий. Закрытая штамповка используется для изготовления деталей клапанов, деталей насосов, крошечных шестерен, шатунов, гаечных ключей и других изделий.
1.7.3 Создание монет
Процесс чеканки представляет собой приложение сжимающего напряжения к поверхности сырья, чтобы придать уникальные формы штампу для тиснения.
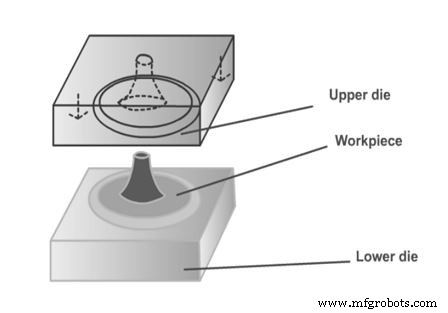
Примерами являются печатные металлические монеты и медальоны.
1.7.4 Штамповка
При штамповке штампами поверхности штампов имеют форму, которая передается заготовке во время сжатия, что значительно ограничивает течение металла. Дополнительный искаженный материал за пределами отпечатка штампа называется вспышкой. Это будет удалено позже.
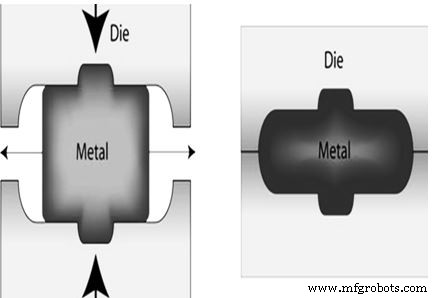
Ковка в штампах не позволяет производить изделия с жесткими допусками.
Для достижения требуемой точности обычно требуется механическая обработка.
В процессе ковки создается основная форма изделия, а дальнейшая обработка выполняется на тех частях детали, которые требуют точной обработки, таких как отверстия и резьба.
1.7.5 Ковка без Flash
В технике безпламенной ковки заготовка полностью ограничена матрицей при безпламенной ковке, и облоя не образуется. Количество используемой начальной заготовки должно точно регулироваться, чтобы оно соответствовало объему полости штампа.
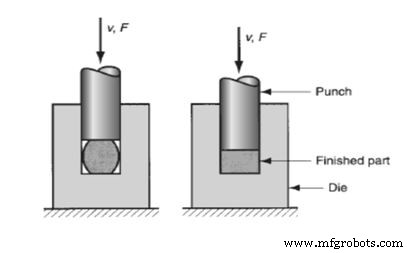
Этот метод ковки без оплавления подходит для изготовления деталей базовой и симметричной геометрии, а также рабочих материалов, таких как алюминий, магний и их сплавы, в зависимости от требований.
1.7.6 Прокатная ковка
Роликовая ковка — это метод формирования, который используется для уменьшения поперечного сечения цилиндрического или прямоугольного стержня путем пропускания его через набор противоположных роликов с соответствующими канавками в зависимости от желаемой формы готового изделия. Хотя он также сочетает в себе прокатку и ковку, он относится к категории операций ковки.
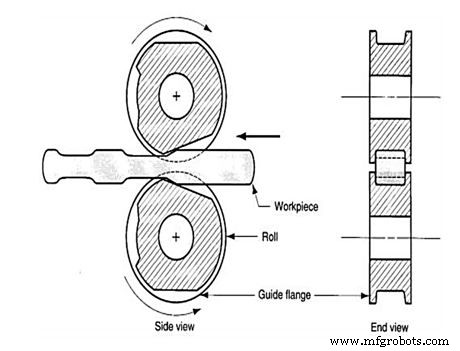
При этом ролики частично раскручиваются в зависимости от степени деформации. Кованые изделия часто прочнее и имеют необходимую структуру зерна по сравнению с механической обработкой того же изделия.
1.7.7 Орбитальная ковка
В орбитальной ковке форма придается материалу с помощью конусообразной верхней матрицы, которая синхронно прокатывается и вдвигается в работу. Нижний штамп используется для поддержки работы.
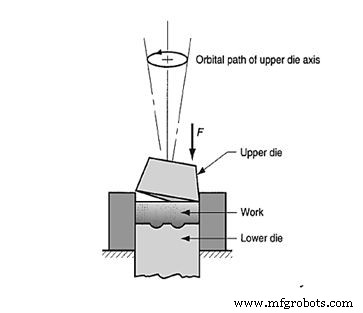
Из-за наклонной оси конуса только небольшая часть поверхности заготовки сжимается в любой точке процесса формования.
Область сжатия вращается по мере вращения верхней матрицы. Существует значительное снижение требуемой нагрузки пресса, вызванное контактом с частичной деформацией на любом этапе формования.
1.7.8 Изотермическая ковка
Изотермическая ковка — это метод горячей ковки, при котором изделие выдерживается при высокой температуре в процессе формовки. Кузнечные штампы также поддерживаются при такой же высокой температуре. Благодаря устранению холода заготовки, соприкасающейся с холодными поверхностями штампа, металл течет легче, а требуемое усилие снижается.
Этот метод более дорогостоящий, чем традиционная ковка, и обычно используется для трудно поддающихся ковке металлов, таких как титан, суперсплавы и сложные формы компонентов. Во избежание быстрого окисления материала штампа операцию проводят в вакууме или инертной среде.
1.8 Экструзия
Экструзия — это процедура объемного формования, при которой рабочий металл продавливается или сжимается через отверстие матрицы для получения желаемой формы поперечного сечения.
Экструзия обычно делится на два способа работы. Один как прямое или прямое выдавливание, а другой как непрямое или обратное выдавливание.
1.8.1 Прямое или прямое выдавливание
При прямом прессовании в контейнер сначала загружают металлическую заготовку. Контейнер имеет выемку фигурного контура. Затем с помощью ползуна проталкивают металлическую заготовку через отверстие матрицы для изготовления изделия.
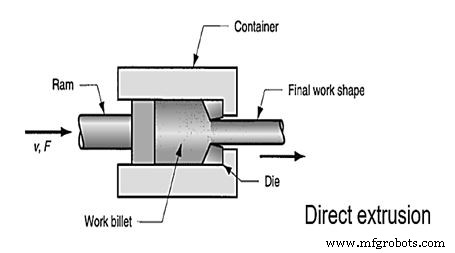
К экструдированным продуктам относятся трубы, банки, чашки, небольшие шестерни, валы и т. д.
Некоторая часть заготовки всегда остается в конце каждого прессования и называется торцом.
1.8.2 Непрямое или обратное выдавливание
Вместо того, чтобы монтироваться на контейнере, матрица монтируется на плунжере. Металл проходит через отверстие матрицы на стороне ползуна в направлении, противоположном движению ползуна, поскольку он сжимается ползунком.
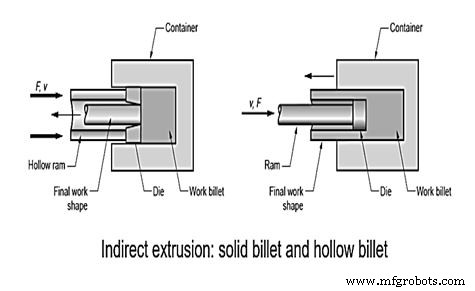
В месте контакта отсутствует трение, так как между заготовкой и контейнером нет относительного движения, следовательно, сила ползуна меньше, чем при прямом прессовании.
1.9 Волочение проволоки:
Процесс волочения проволоки используется для изготовления проволоки малого диаметра из стержней путем уменьшения их диаметра и растяжения по длине за счет растягивающей силы.
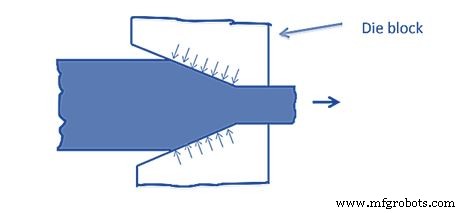
Волочение проволоки используется для изготовления музыкальных струн. Чертеж трубы можно использовать для создания бесшовных труб.
В этом процессе стержень или стержень протягивают через отверстие матрицы, чтобы сформировать проволоку нужной толщины, уменьшая площадь их поперечного сечения.
2. Ударное выдавливание
Ударное прессование всегда осуществляется в холодном виде. Обратная ударная экструзия позволяет получать очень тонкие стенки. Например, производство тюбиков для зубной пасты или батарейных отсеков.
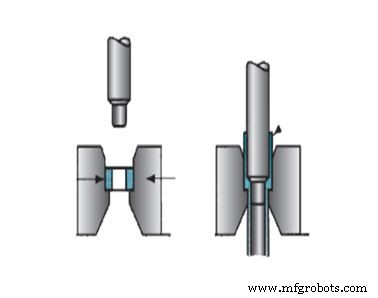
Это делается на более высоких скоростях и с более короткими ударами. Ударное давление, а не давление, используется для выдавливания заготовки через головку. Однако воздействие может быть достигнуто путем прямого или обратного выдавливания или их комбинации.
2.1 Гидростатическая экструзия
В методе гидростатической экструзии заготовка окружена жидкостью внутри контейнера во время процесса, и жидкость подвергается давлению за счет поступательного движения плунжера. Из-за жидкости трение внутри контейнера отсутствует, а трение в отверстии штампа минимально. При работе при высоких температурах необходимо использовать специальные жидкости и методы.
Пластичность материала повышается, когда на него действует гидростатическое давление и отсутствует трение. В результате этот подход можно использовать для металлов, которые слишком хрупкие для традиционных процедур экструзии.
Этот метод используется для пластичных металлов с возможным большим коэффициентом обжатия.
#2. Формование листового металла
Формование листового металла включает в себя приложение усилий растяжения и сдвига для изготовления листов, пластин и полос до желаемой возможной формы с использованием набора инструментов. Пуансон и матрица используются в качестве инструментов в процессе изготовления.
Формовка листового металла связана с операциями; Гибка, волочение, резка, вырубка и штамповка для производства материалов.
В методе формования листа используются методы деформации пластикового листа, такие как глубокая вытяжка, резка, сгибание, подгибка, отбортовка, скручивание, формование/растяжение, штамповка.
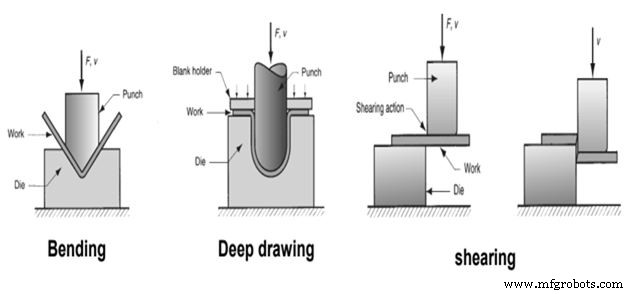
2.1 Глубокое рисование:
Глубокая вытяжка – это процесс обработки листового металла, при котором листовой металл запрессовывается в чашу полой формы под действием сил растяжения и сжатия без изменения его толщины.
В этом процессе лист помещается над отверстием штампа и вдавливается в него с помощью пуансона. Держатель заготовок используется для плоской фиксации листа на поверхности штампа.
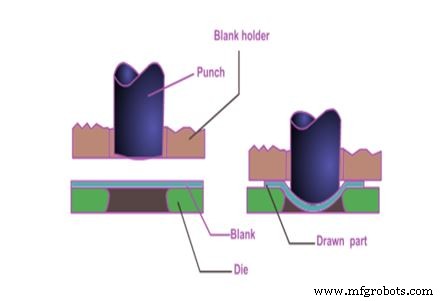
Во многих случаях изменение, необходимое для создания этой детали, будет значительным (коэффициент вытягивания очень высок). В таких случаях полное формирование детали требует более чем одного этапа глубокой вытяжки.
Любые дополнительные шаги рисования, необходимые для завершения операции рисования, называются перерисовкой.
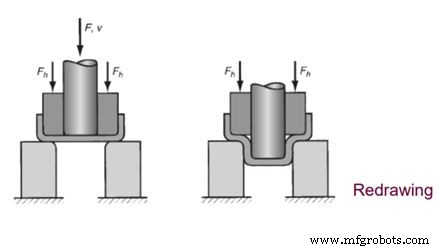
2.2 Гибка листа:
Изгиб листа определяется как деформация металла вокруг прямой оси. Металл на внутренней кромке нейтральной плоскости сжимается, а металл на внешних кромках нейтральной плоскости растягивается во время операции гибки. Толщина листового металла не меняется в результате изгиба.
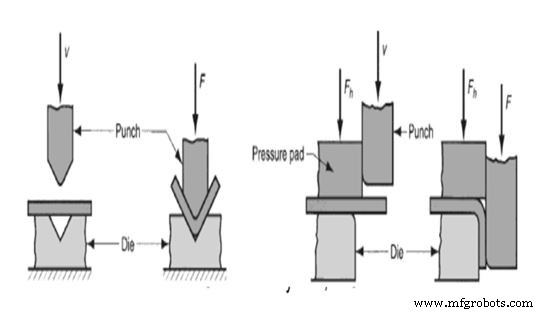
2.3 Растяжка или растяжка:
Формование растяжением – это процесс формовки листового металла, при котором листовой металл намеренно одновременно растягивается и изгибается, чтобы изменить свою форму.
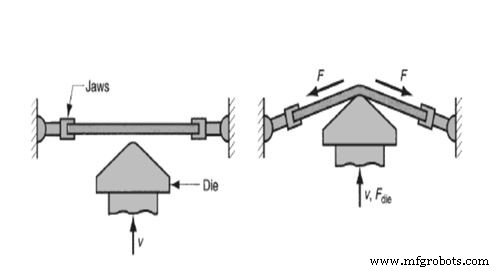
Лист удерживается с обоих концов зажимами или натяжными валиками, а затем растягивается с помощью пуансона, в результате чего лист подвергается напряжению, превышающему его предел текучести, и придается желаемая форма.
При снятии напряжения металл пластически деформируется. Комбинированное воздействие растяжения и изгиба приводит к тому, что деталь имеет меньшую упругую отдачу.
Видеолекция о процессе формовки металла:
Применения процесса формовки металла:
Техника обработки металлов давлением используется для производства бесшовных труб, стержней и турбинных колец. Он также используется для создания печей для обжига цемента.
Этот процесс формовки можно использовать для создания подшипников, пластин, стальных листов и множества компонентов для автомобиля.
Этот метод также используется для изготовления компонентов ракет и самолетов, а также для изготовления петель, болтов и гвоздей.
Преимущества процесса формовки металла:
Следующие преимущества процессов формовки следующим образом:
- Изделия повышенной прочности.
- Очень меньше потерь материала.
- Можно изготовить более мелкие компоненты с высокой прочностью.
- Производимые изделия имеют точные размеры.
- Равномерная скорость формования.
- Отличная отделка поверхности.
- Меньшее время обработки по сравнению с традиционным методом удаления металла.
- Улучшенные механические свойства.
Недостатки процесса формовки металла:
Следующие недостатки процессов формовки следующим образом:
- Потребность в силе высока.
- Требуется высокое механическое усилие.
- Деформационное упрочнение рабочего материала является пределом объема формовки.
- Хрупкий материал не может быть изготовлен в этом процессе.
- Также иногда используется процесс термообработки при формовке металлов.
Промышленные технологии
- Из чего формируются резиновые прокладки в металлообработке?
- Что такое процесс изготовления листового металла?
- Что такое штамповка? - Типы, операции и применение
- Что такое кастинг? - Определение| Виды литья
- Что такое протяжка? - Процесс, работа и типы
- Что такое ковка? - определение, процесс и типы
- Что такое металлизация? - Определение, типы и преимущества
- Что такое литье металлов? - определение, типы и процесс
- Процесс формирования листового металла
- Какие существуют 4 типа производственного процесса?