Обратный инжиниринг в стоматологической промышленности
Возможно, вы слышали, что стоматологическая промышленность является одним из крупнейших пользователей 3D-печати в мире. Массовая настройка элайнеров и других стоматологических инструментов сделала внедрение этой технологии огромной финансовой выгодой. У моего дантиста, который также является моим отцом, был другой запрос на 3D-печать. Компонент зажима, который удерживает небольшой рабочий стол, вышел из строя, разбив его пополам. В качестве временного решения его сотрудники снова склеили зажим. Мой отец обратился ко мне, чтобы узнать, могу ли я напечатать компонент, поскольку производитель больше не производит эту часть.
Обратное проектирование компонента зажима
Я передал деталь нашей команде SolidWorks, чтобы они могли перепроектировать ее и провести быстрый анализ напряжений, чтобы увидеть, не повлияют ли небольшие изменения в конструкцию на функциональность детали. Фред, один из наших инженеров службы поддержки, пришел к выводу, что наш стандартный материал из АБС-пластика справится с этой задачей даже с редким напечатанным заполнением.
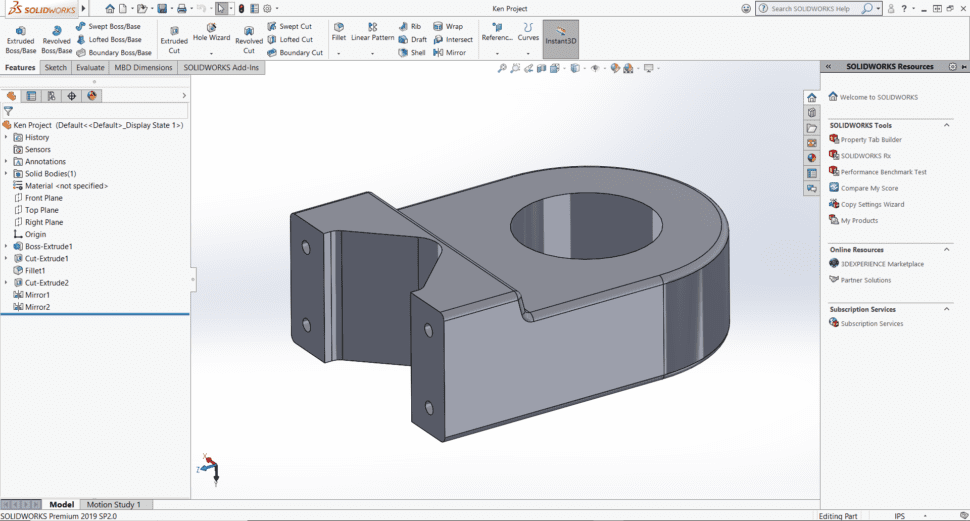
Установка для 3D-печати компонентов стоматологического зажима
Я перенес файл в GrabCAD, чтобы настроить его для печати, когда модель SOLIDWORKS будет завершена. Я смог использовать некоторые из замечательных новых функций в «Расширенном режиме FDM», чтобы изменить деталь. Сначала я использовал функцию «Применить вставку», чтобы изменить четыре отверстия в основании детали, чтобы они подходили к вставкам № 10–24 с длинной термофиксацией. Программа автоматически изменяет диаметры отверстий до подходящего размера и добавляет дополнительные контуры к области вокруг них, чтобы обеспечить правильную подгонку.
Затем я использовал функцию «Избегать швов», чтобы сместить печатный шов с сопрягаемых поверхностей и с поверхностей, которые соприкасались со стулом. Зеленые поверхности ниже показывают изменения.
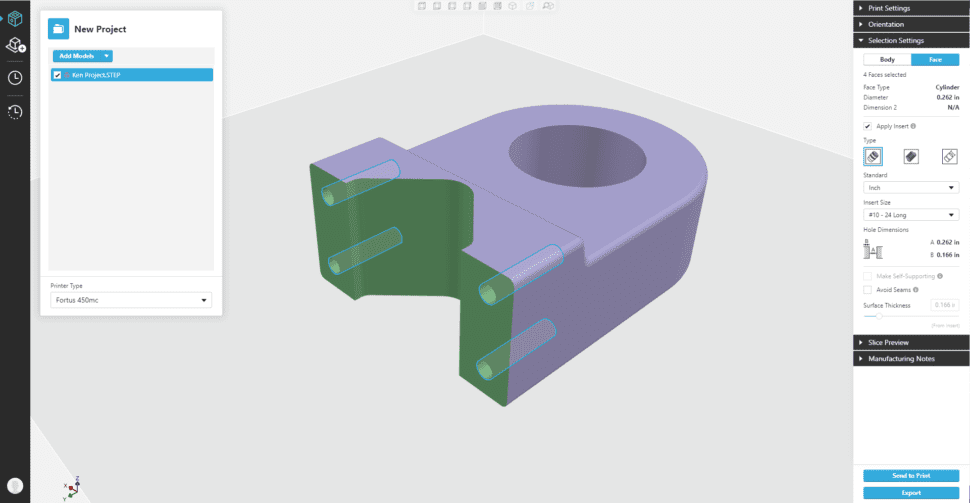
Я отправил задание на наш Fortus 450mc, когда был доволен своими настройками. Используя разреженный образец заполнения и высоту слоя 0,013 дюйма, деталь была завершена менее чем за 3,5 часа. Когда печать закончилась, я вылила ее в бак для стирки. Чтобы полностью удалить растворимую подложку из отверстий для вставки, потребовалось всего 4 часа.
Следующим шагом стала установка вкладышей для термоустановок. Паяльника для нагрева деталей у нас не было. Мы закончили тем, что использовали небольшую паяльную лампу, чтобы металлические вставки были достаточно горячими, чтобы они встали на место. Я бы не рекомендовал использовать этот метод, поскольку равномерное нагревание деталей было довольно непредсказуемым.
Окончательные результаты
С готовой деталью в руках я зашел в офис отца, чтобы помочь установить новую. Он хорошо подходил и мог удерживать стол и инструменты плюс небольшой дополнительный вес. Радиус новой детали можно было бы немного увеличить для лучшей подгонки.
Я также обнаружил, что на существующей половине зажима был небольшой резиновый лист, который не давал части соскользнуть вниз по штанге. Вторая резиновая деталь должна была быть потеряна, когда сломался оригинал. Деталь в настоящее время выполняет свою работу. Во всяком случае, это можно было бы немедленно улучшить, это добавило бы большего трения между деталью и шестом. Мой отец был доволен результатом, и я с нетерпением жду возможности улучшить эту часть в будущем.
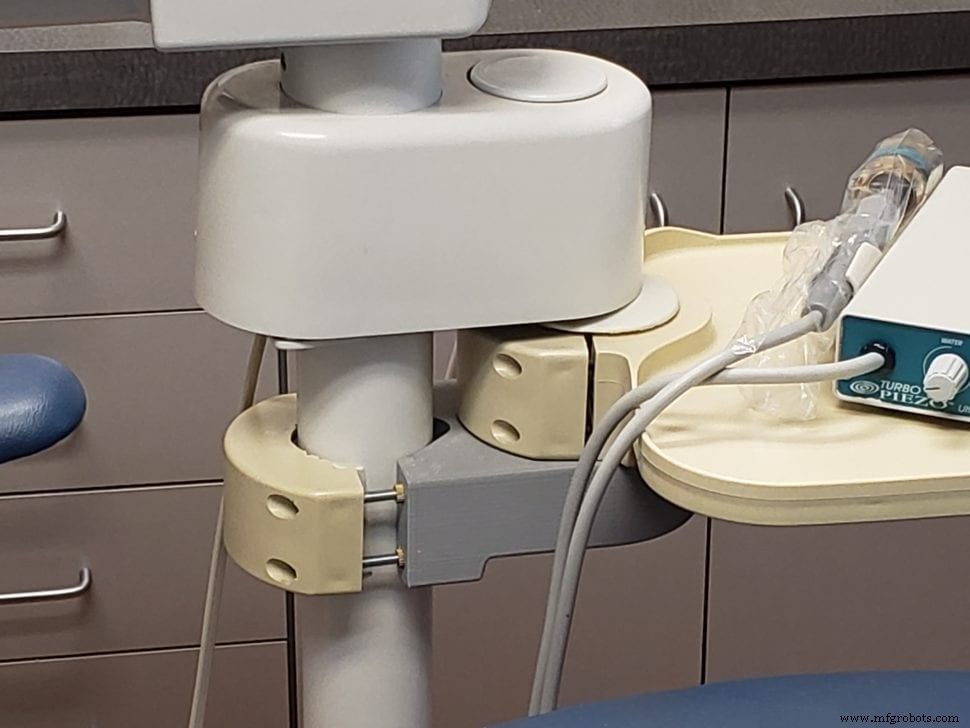
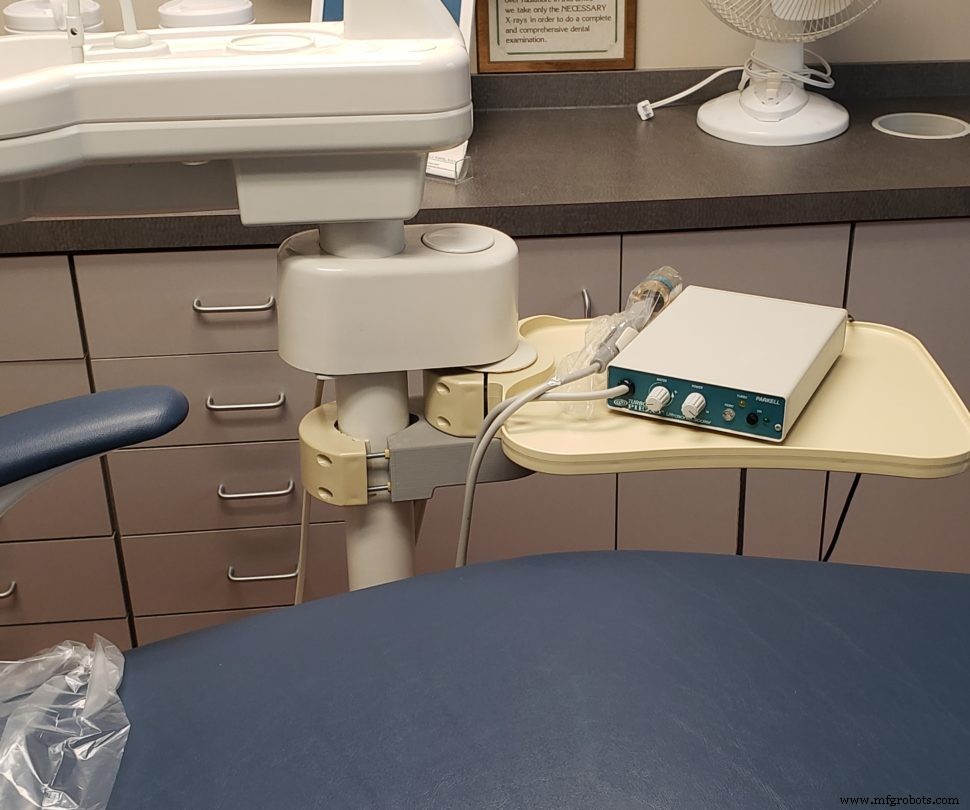
Теги:3D-печать, Запасные части, Обратный инжиниринг
3D печать
- Часть недели - составное приспособление для натяжения колес от Carl Calabria
- Прослеживание истории полимерных материалов:Часть 1
- Отслеживание истории полимерных материалов, часть 4
- Прослеживание истории полимерных материалов:Часть 6
- Прослеживание истории полимерных материалов:часть 7
- Прослеживание истории полимерных материалов:часть 9
- Прослеживание истории полимерных материалов:часть 10
- Прослеживание истории полимерных материалов:часть 11
- Повышение квалификации и лидерство в технической индустрии как женщина 40 лет
- Производство 101:стать частью аэрокосмической отрасли