Разработка RAPM с помощью PtFS
Этот блог представляет собой онлайн-сайдбар для майской 2020 года статьи «Революция парадигмы стоимости композитов, часть 2:формование», в которой обсуждается программа высокопроизводительного производства RApid (RAPM, произносится как «wrap-em»), проводимая компанией Boeing Co. (Чикаго, Иллинойс, США), «формирующая» часть программы DARPA Tailorable Feedstock and Forming (TFF), позволяющая быстро, недорого и быстро производить небольшие композитные детали сложной формы.
Все три направления материалов и процессов в программе RAPM - инфузия смолы, термореактивный препрег и формование из термопласта - включали испытания с использованием системы управления пиксельным нагревом от производства до функциональных спецификаций (PtFS) и инструментальной системы, поставляемой Surface Generation и расположенной в Boeing R&T в г. Сент-Луис (см. Таблицу ниже).
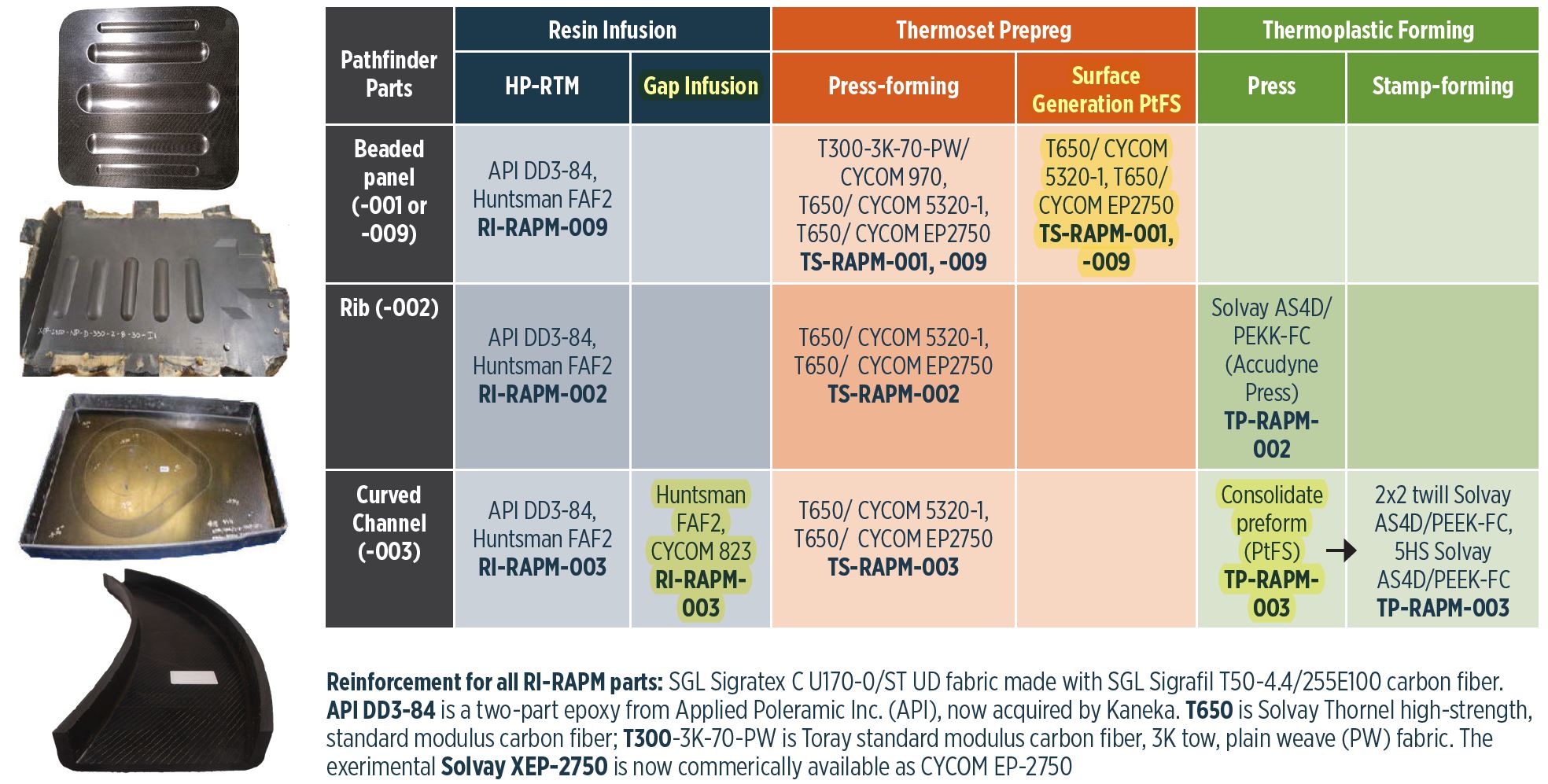
Обратите внимание, что PtFS была коммерциализирована в течение многих лет. Этот блог посвящен разработке процессов RAPM с использованием системы PtFS. Ссылки для этого блога включают:
- 2019 SAMPE (20-23 мая, Шарлотт, Северная Каролина) технический доклад и слайд-презентация, «Разработка масштабируемых архитектур динамического управления для рабочих ячеек для производства гибких композитов», Стивен М. Шевчук 1 , Бен Хэлфорд 2 , Майкл П. Мэтлак 1 , Эндрю Шарп 2 и Пит Мэсси 2 . 1 Компания "Боинг", Сент-Луис, Миссури, США 2 Surface Generation Ltd. (Ратленд, Великобритания).
- Технический доклад SAMPE, 2020 г., «Формование сложных термореактивных ламинатов», Трэвис Р. Адамс, Тимоти Дж. Лучини, Джаред Б. Хьюз, Стивен М. Шевчук, Адам Мартинес и Гейл Хан, The Boeing Company.>
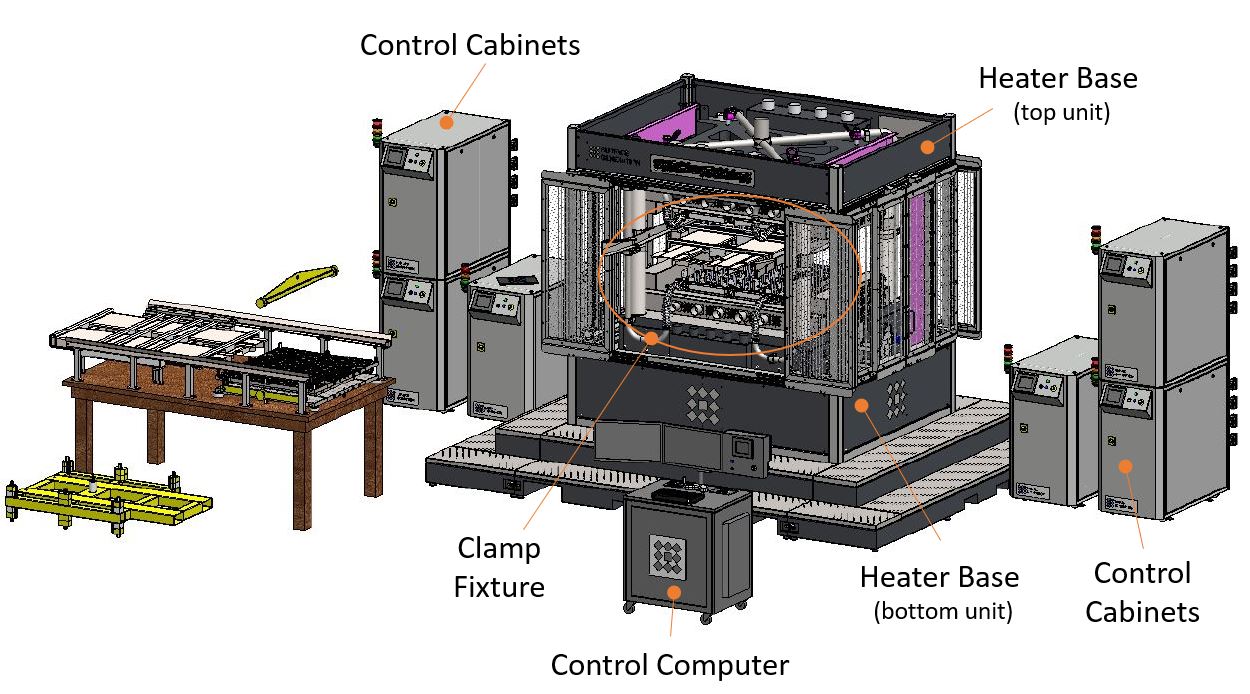
Компоненты системы PtFS
Система PtFS является модульной и может быть полностью автономной или использовать части существующей инфраструктуры. Для давления уплотнения / уплотнения в системе можно использовать существующий гидравлический пресс или зажимное приспособление для инструмента с гидравлическим приводом. Ячейка PtFS компании Boeing St. Louis оснащена последней, 150-тонной зажимной арматурой . разработан Surface Generation. Эта формовочная ячейка вмещает детали размером 750 на 750 на 100 миллиметров.
Ячейка PtFS Boeing St. Louis включает управление положением и давлением. «Программное обеспечение Orchestrator компании Surface Generation используется для управления рабочей ячейкой CF-OaO-RAPM PtFS», - отмечает технический сотрудник Boeing и руководитель программы RAPM Гейл Хан. «Каждый инструмент калибруется в системе посредством настройки рабочего объема и давления. Калибровка давления проводится для настройки гидравлики на ожидаемое давление, которое будет испытывать инструмент во время обработки. Калибровка разделения и смещения инструмента выполняется для установки открытого / закрытого положения инструмента, а также областей медленного / быстрого закрытия, которые защищают поверхность инструмента во время ручного и автоматического управления ». «Позиционные измерения выполняются с помощью четырех струнных потенциометров», - объясняет инженер Boeing по композитным материалам и исследователь RAPM Стивен Шевчук. «Каждый из них расположен на направляющей стойке зажимного приспособления для измерения положения плиты, а также для обеспечения безопасного метода определения стеллажа плиты во время работы. Регулятор давления укомплектован одним встроенным датчиком давления, обеспечивающим управление с обратной связью гидравлическому насосу зажимного приспособления ».
Выше и ниже зажимного приспособления находятся верхний и нижний базовые блоки нагревателя . . Они содержат все компоненты нагрева / охлаждения и работают в зависимости от выходных сигналов шкафов управления . (три шкафа на каждую подставку обогревателя в установке Boeing). Торцы инструментов разработаны для каждого основания нагревателя и устанавливаются с помощью направляющей и системы загрузки.
Каждая поверхность инструмента нагревается и охлаждается с помощью сжатого воздуха, направляемого на нижнюю сторону каждой поверхности инструмента и распределяемого через диффузор. Каждый набор подходящих металлических поверхностей инструмента разделены на 180 индивидуально управляемых каналов нагревателя - 90 для верхней поверхности инструмента и 90 для нижней. Каналы нагревателя расположены на расстоянии 10,0 сантиметров друг от друга по сетке на каждой поверхности инструмента. Каждый канал имеет нагреватель, двухступенчатый источник сжатого воздуха и две термопары обратной связи . которые подпружинены для обеспечения плотного контакта с тыльной стороной торца инструмента. Для нагрева торцевых поверхностей инструмента RAPM использовался 1 кубический фут сжатого воздуха в минуту на канал нагревателя, а для охлаждения использовался 3 кубических фута в минуту.
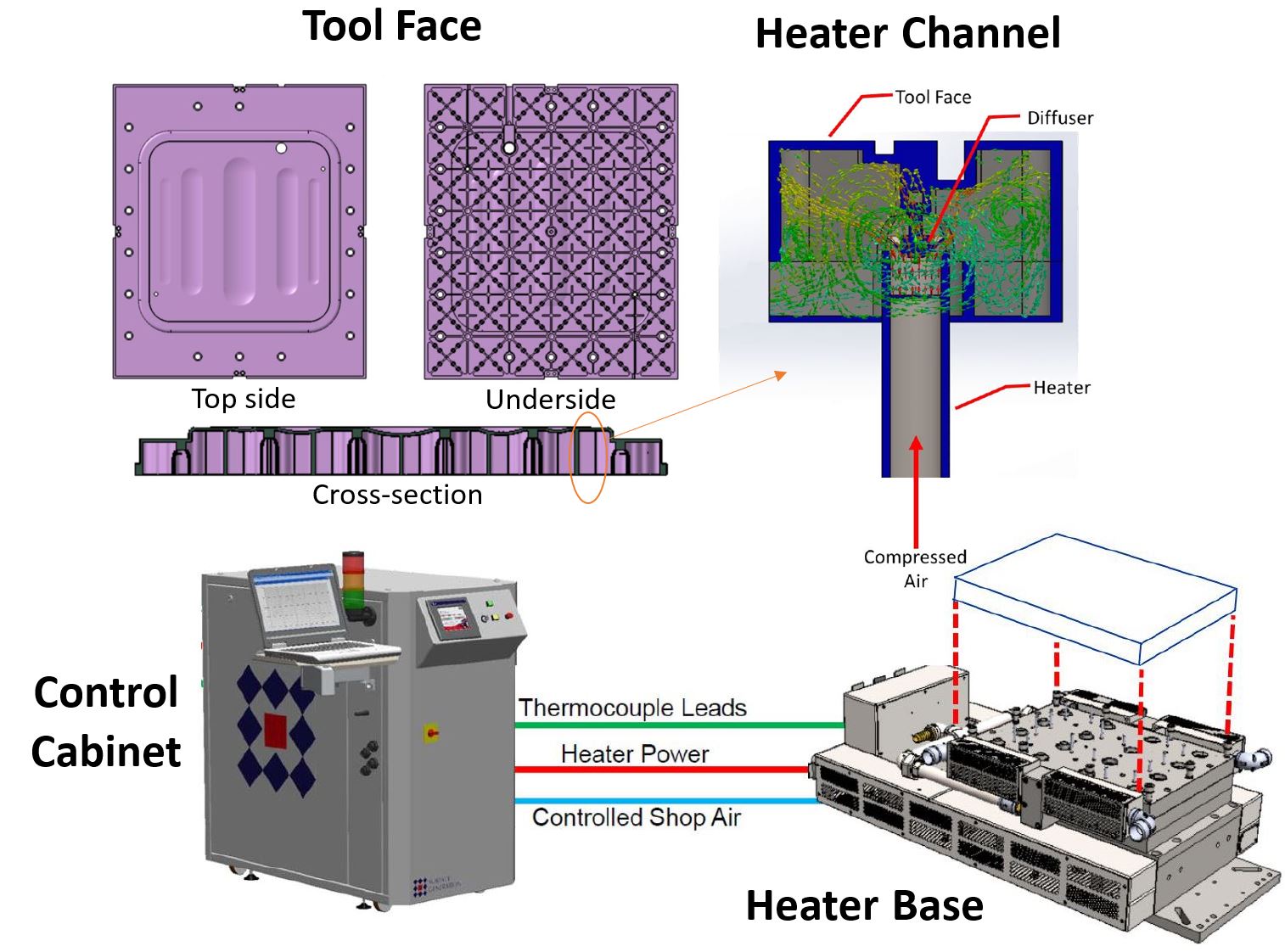
Грани инструмента
Торцы инструментов в RAPM были обработаны из инструментальной стали до толщины ≈3 миллиметра. Нижняя поверхность инструмента для TS-RAPM-001-201 показана вверху слева на рисунке выше. Верхняя часть торца инструмента выглядит как стандартный инструмент для штамповки, но на нижней стороне видны каналы нагрева.
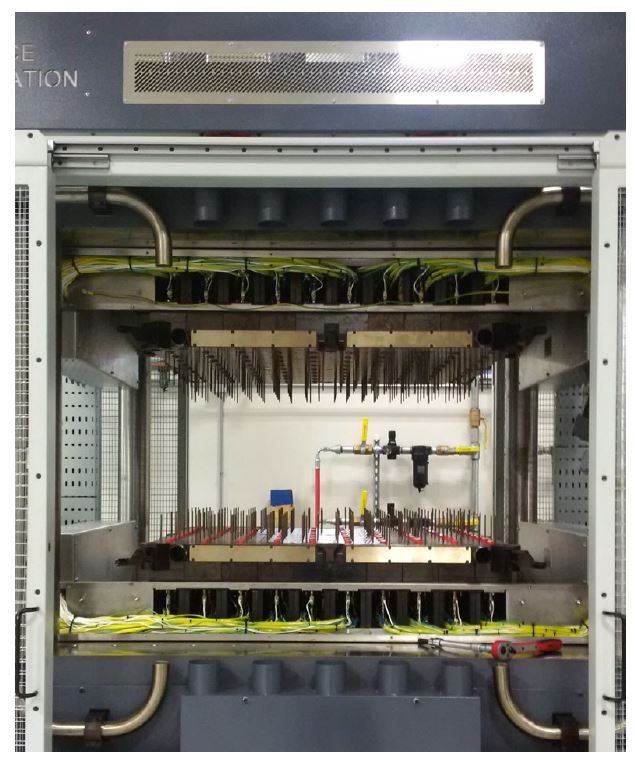
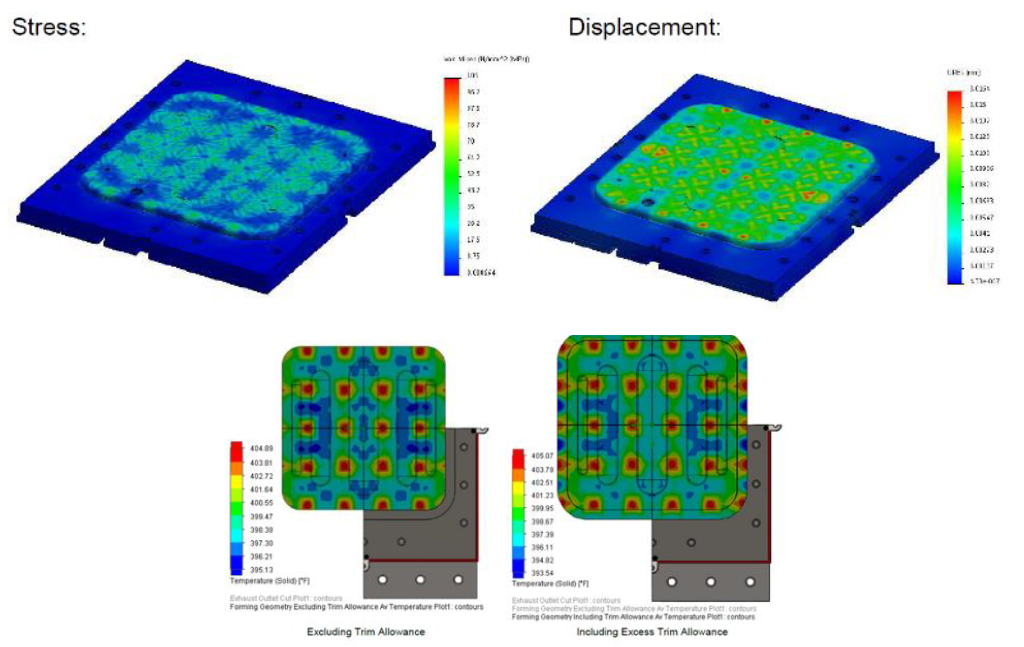
Грани инструмента приемлемой геометрии можно заменить другими торцами инструмента, предназначенными для того же основания нагревателя. Для инструмента потребуются те же размеры канала нагревателя, примерное размещение термопары и глубина, которая будет находиться в пределах хода подпружиненной термопары.
Система загрузки рельсов, используемая для изменения торца инструмента, выравнивает все 180 подпружиненных термопар обратной связи в втулки на задней стороне торца инструмента. Штифты выравнивают поверхность инструмента и позволяют производить загрузку инструмента без точного управления вилочным погрузчиком. Смена инструмента может быть завершена за 2-4 часа с двумя операторами, включая разборку и повторную сборку лицевой панели инструмента в рамку для изображения.
Обрабатывается как можно больше материала, чтобы уменьшить тепловую массу и улучшить скорость нагрева и охлаждения. По этой причине каждая поверхность инструмента, используемая в RAPM, требовала структурного анализа методом конечных элементов (FEA), чтобы определить, может ли поверхность инструмента выдержать температуру и давление обработки. Торцы инструмента были оптимизированы с использованием линейного и нелинейного FEA, а также термического анализа вычислительной гидродинамики (CFD) в установившемся и переходном режиме. Последнее помогло обеспечить равномерный нагрев инструмента. И толщина инструмента, и воздухораспределители в каждом канале нагревателя были изменены для улучшения однородности температуры. Итерационный цикл между FEA и CFD позволил настроить геометрию, чтобы помочь поддерживать желаемую температуру торца инструмента при соблюдении требуемых факторов безопасности для опоры торца инструмента.
Зоны нагрева и контроль температуры
Каналы нагревателя обычно группируются в зоны, причем количество каналов нагревателя на зону указывается для каждой детали. Каждая зона имеет связанный с ней профиль нагрева, и допуски могут быть установлены внутри и между зонами по мере необходимости. Это позволяет всем нагревателям в каждой зоне нагревать, охлаждать или поддерживать температуру в соответствии с предписанным профилем нагрева за счет динамического изменения уровней мощности нагревателя и расхода сжатого воздуха.
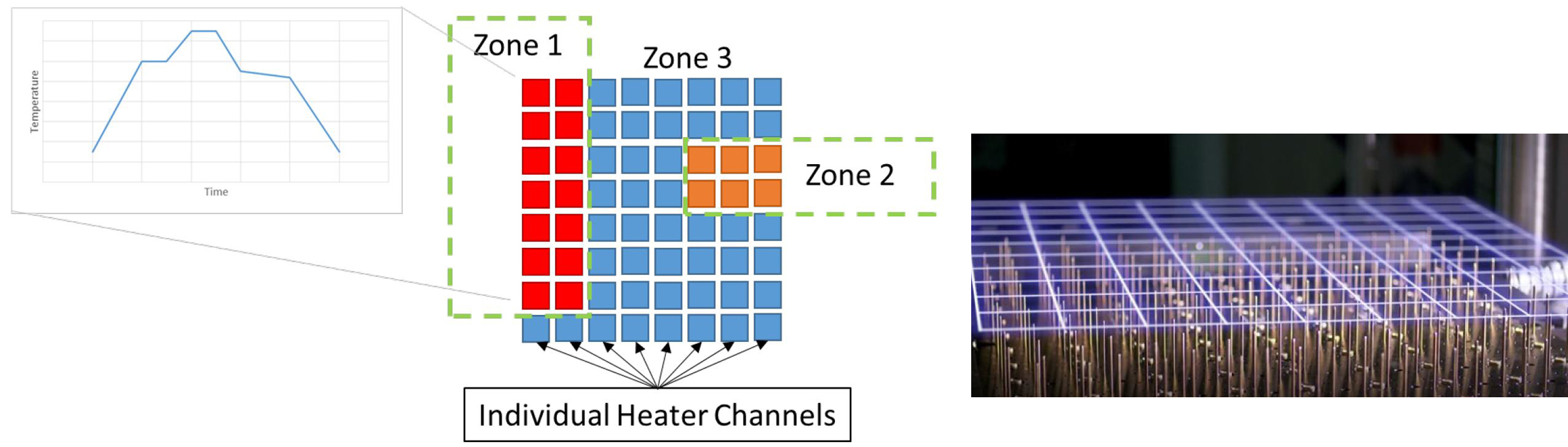
Хотя программное обеспечение для управления оборудованием PtFS имеет как аналоговые, так и цифровые стратегии нагрева, которые можно адаптировать к различным сценариям нагрева, ячейка RAPM использует аналоговое управление. Это требует автонастройки системы для определения уровней мощности нагревателя при заданных температурах. Уровни мощности для каждого нагревателя устанавливаются таким образом, чтобы предотвратить превышение или снижение во время линейных изменений нагрева / охлаждения и поддержание заданных значений температуры. Автоматическая настройка автоматически определяет постоянные значения для модифицированного метода управления пропорционально-интегральной производной для каждого канала нагревателя при каждой заданной температуре. После завершения автонастройки можно записать профили нагрева для каждой зоны. Все термические профили были проверены, чтобы убедиться, что композитная деталь подвергалась воздействию температур в пределах ± 5,5 ° C (± 10 ° F) от желаемой уставки.
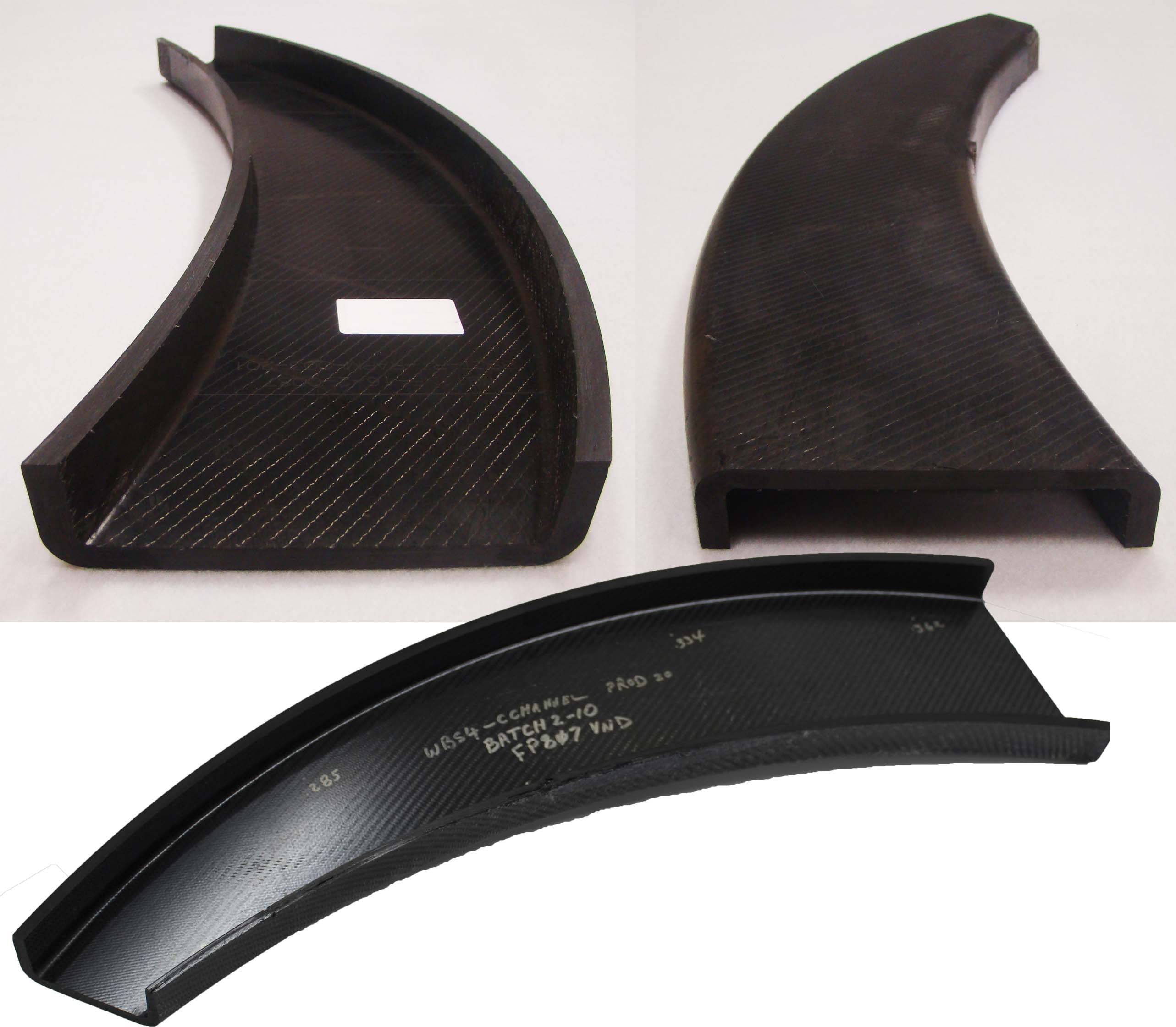
Ячейка Boeing PtFS имеет максимальную температуру 440 ° C. Первоначально, когда Boeing обрабатывал несколько высокотемпературных циклов в день, существовали опасения, что некоторые компоненты могут быть повреждены из-за отсутствия охлаждения между циклами обработки. Однако в сентябре-октябре 2019 года система охлаждения была модернизирована, включая дополнительную мощность вентилятора для отвода тепла. Благодаря этому улучшенному охлаждению ячейка может непрерывно работать при 440 ° C.
При использовании большого объема сжатого воздуха при температуре окружающей среды в качестве метода охлаждения охлаждение торца инструмента происходило быстро около верхнего предела температурного диапазона, но значительно замедлялось при достижении 60 ° C (140 ° F). Во время нагрева до температур термопласта (> 350 ° C) температура поверхности инструмента нарастала со средней скоростью 41 ° C / мин (74 ° F / мин). Во время охлаждения того же цикла максимальная средняя скорость охлаждения составляла 36 ° C / мин (65 ° F / мин). Использование сжатого воздуха для охлаждения обеспечивало более непрерывную рампу охлаждения и в сочетании с активным управлением температурой (то есть нагревом по мере необходимости), температура оставалась довольно линейной во время охлаждения.
Изотермическая штамповка TS препрега
Первые испытания детали с использованием рабочей ячейки PtFS были для панелей крышки доступа TS-RAPM-001, изготовленных из термореактивного препрега прессованием (штамповка). Инструмент для этой детали занимает 112 из 180 каналов в рабочей ячейке RAPM PtFS. Это включает 56 каналов на верхней поверхности инструмента и 56 каналов на нижней поверхности инструмента. Фактическая часть, однако, не покрывает весь инструмент - а покрывает только 30 из этих 56 каналов для каждой поверхности инструмента, верхней и нижней. На рисунке ниже показано размещение 78 термопар (ТС), используемых для деталей RAPM-001 - 39 для верхней поверхности и 39 для нижней поверхности с одинаковым размещением для обеих. Количество ТС включает по одной на ячейку (канал нагревателя) плюс дополнительные ТС в горячих и холодных областях, определенных в термическом анализе CFD.
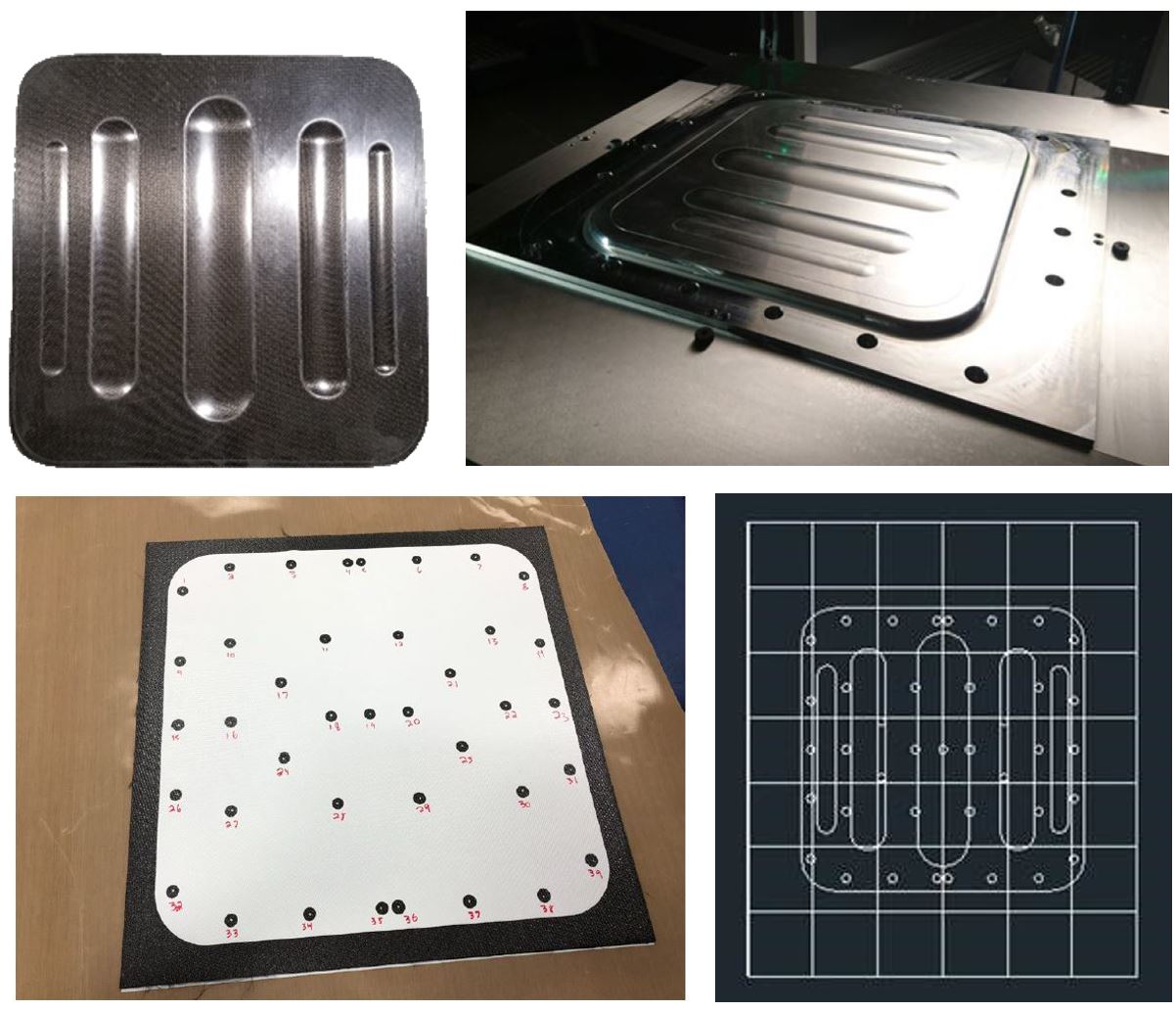
Пустая поверхность инструмента была испытана на однородность температуры, а затем испытание было повторено после заделки термопар в середине 16-слойного тканого / эпоксидного ламината из углеродного волокна. После добавления композитного материала распределение температуры торца инструмента становится более жестким, поскольку композит действует как путь теплопередачи. Кроме того, однородность температуры внутри многослойного композитного материала была более жесткой, чем показания на торце инструмента. Одиночный TC в прогоне 1 (см. Рисунки ниже, вверху диаграммы справа) колебания, превышающие заданный диапазон температур, были около края детали и предположительно были вызваны колебаниями температуры соседних ячеек за пределами линии обрезки детали.
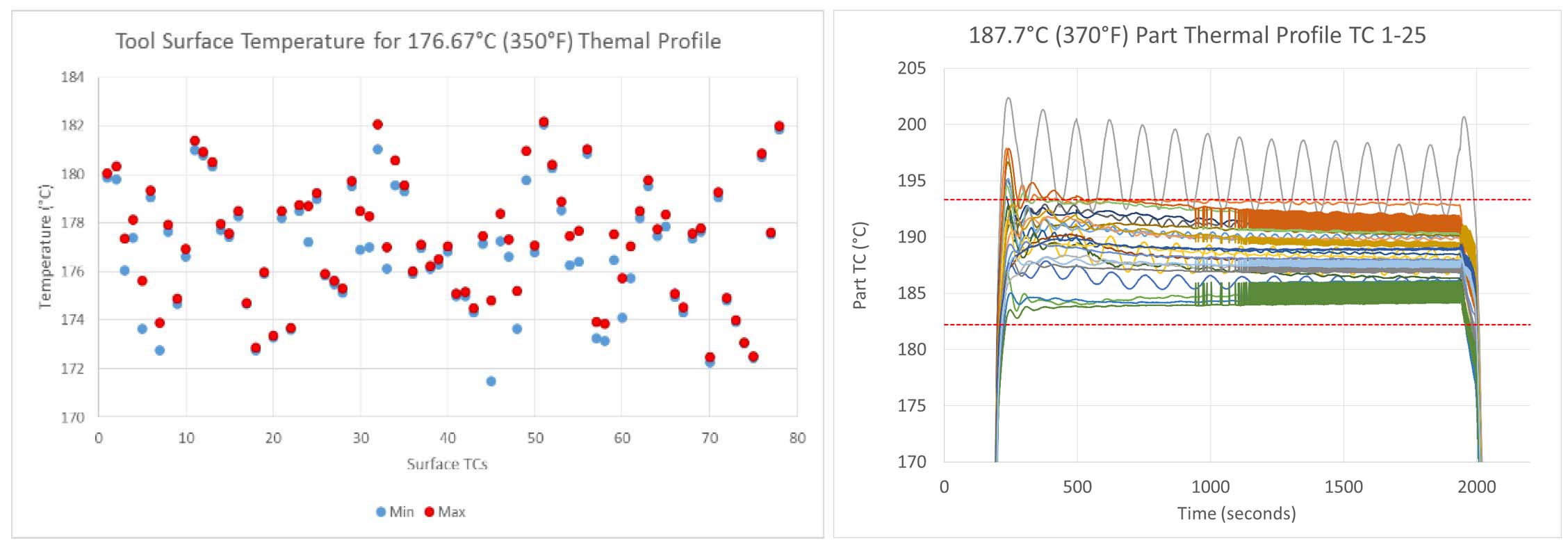
Изотермическое прессование во время обработки удерживало инструмент при 176,7 ° C (350 ° F) в пределах допуска ± 5,5 ° C (± 10 ° F). Для TS-RAPM-001 была соблюдена следующая последовательность:
- Система нагревается до 187,7 ° C в приложении. 8 минут
- Составная заготовка загружена в горячий инструмент
- Инструмент закрывается в 12:09 (например).
- Время отверждения инструмента до гелеобразования - 30 минут.
- Первая ступень давления:начальный быстрый нагрев заготовки при минимальном выдавливании смолы.
- Вторая ступень давления:увеличьте давление до 300 фунтов на квадратный дюйм, чтобы обеспечить хорошее уплотнение и предотвратить рост пустот.
- Удалите «зеленый» композит с горячего инструмента для последующего отверждения.
Этот процесс действительно позволил получить высококачественные детали и продемонстрировать детали с меньшим временем цикла, чем существующие в настоящее время процессы изготовления композитных материалов. Более высокая температура процесса может привести к гелеобразованию композита еще быстрее, но также может вызвать деградацию материала и риск экзотермии. Это вызывало беспокойство, потому что в инструментах PtFS не используется традиционная большая тепловая масса для поглощения экзотерма, а вместо этого используется активное охлаждение тыльной стороны инструментов с низкой тепловой массой для рассеивания экзотерма.
Ячейку PtFS также использовали для изготовления «волновых» частей для испытания TS-RAPM-012. Используя предыдущие испытания разработки, было определено, что отверждение этих деталей возможно с использованием 30-минутного изотермического цикла при 177 ° C с последующим 2-часовым дополнительным отверждением при той же температуре. Однако отличия от предыдущих испытаний заключались в более агрессивной геометрии и квазиизотропном наложении эпоксидной смолы CYCOM 5320-1 - стандартной для деталей авиакосмической отрасли вне автоклавов - в сочетании с сатиновым и однонаправленным слоем углеродного волокна с 8 ремнями и внешним слоем. из стеклоткани Style 108 с одной стороны. Контроллер RAPM PtFS был запрограммирован на приложение минимального давления на ламинат до достижения надлежащей вязкости. После этого начального шага было приложено последнее давление, чтобы закончить отверждение. Одно испытание было подвергнуто последующему отверждению в печи, тогда как остальные были подвергнуты пост-отверждению в зажимном приспособлении PtFS, чтобы сократить время между испытаниями. Было произведено множество высококачественных деталей.
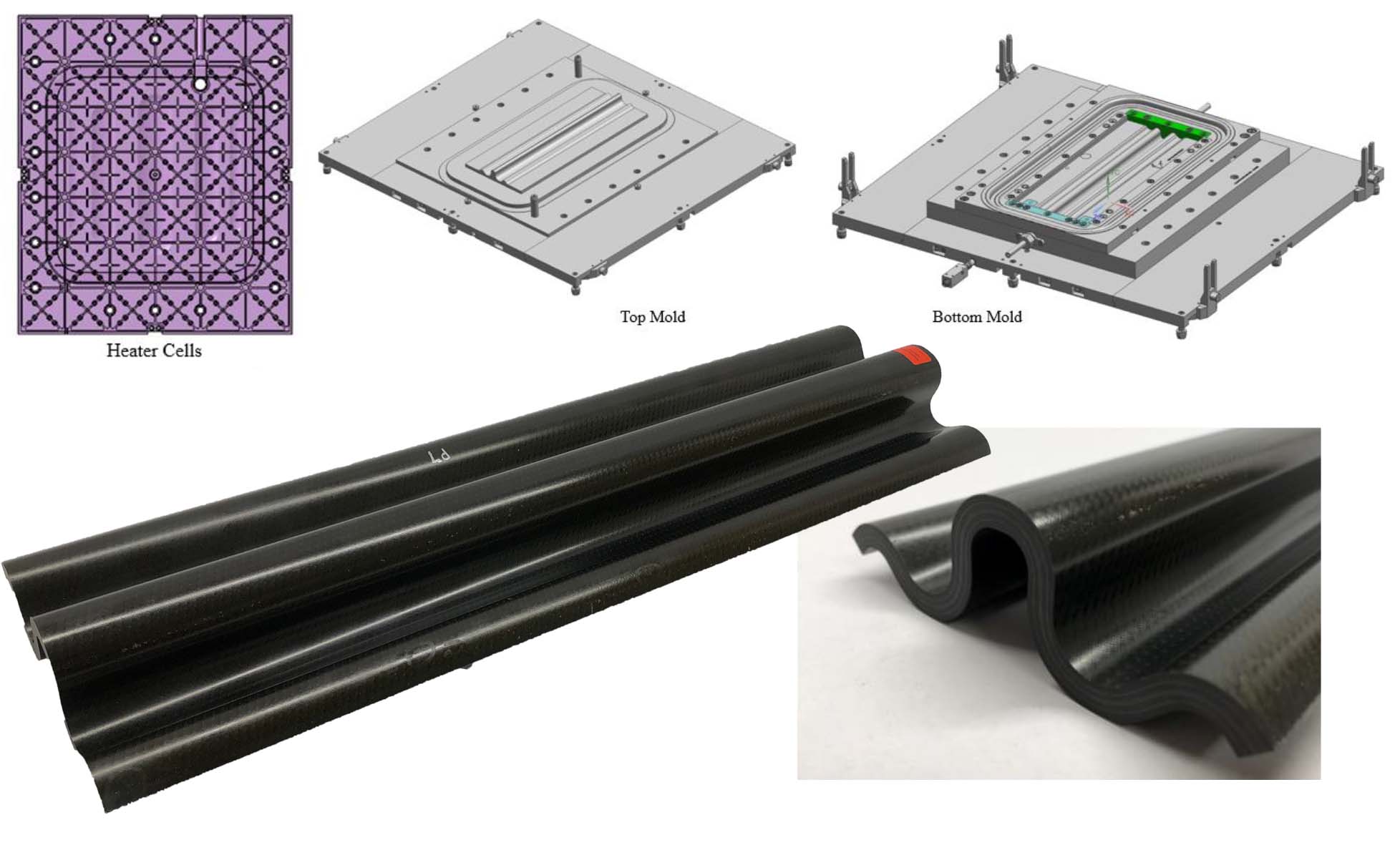
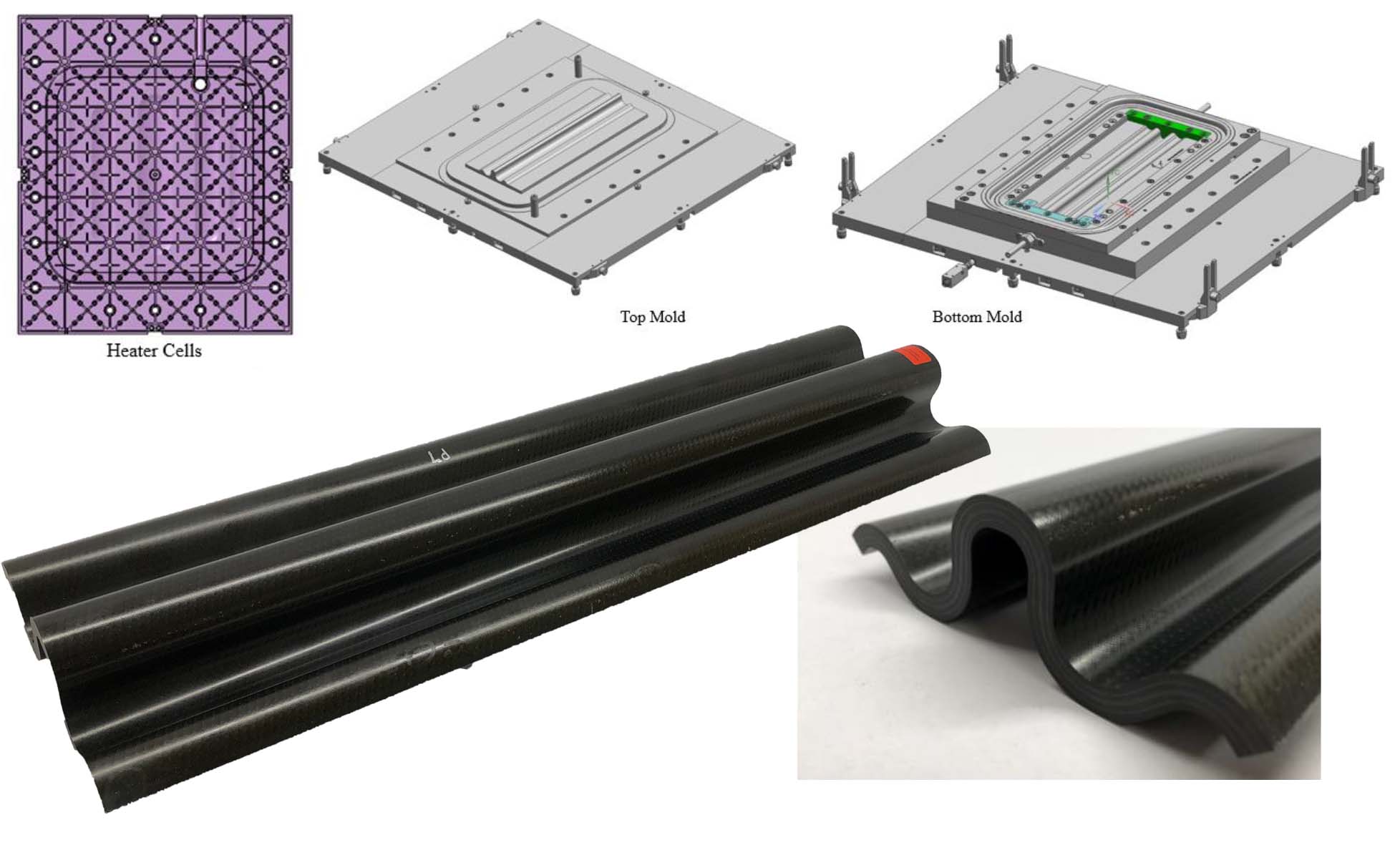
Динамические температурные циклы для настаивания смолы
Испытания части для инфузии смолы с использованием рабочей ячейки PtFS начались с изогнутой части с С-каналом RI-RAPM-003. Первоначально были испытаны три различные системы эпоксидных смол:
- Solvay CYCOM 823, настаивается при 80 °, а затем выдерживается до 125 ° C.
- Huntsman FAF2 (система быстрого отверждения) настаивается при 100 ° C с выдержкой 150 ° C.
- Applied Poleramic (теперь приобретенный Kaneka) API DD3-84 (также система быстрого отверждения) настаивается при 60 ° C с температурой выдержки 160 ° C.
Заготовку из не изогнутой ткани заваривали, нагревали со скоростью 2 ° С / мин до заданной температуры выдержки и затем выдерживали в течение 60 минут перед охлаждением. Для быстроотверждаемых смол по мере развития экзотермической реакции PtFS автоматически применяет активное охлаждение к определенным участкам инструмента для поддержания заданной температуры детали.
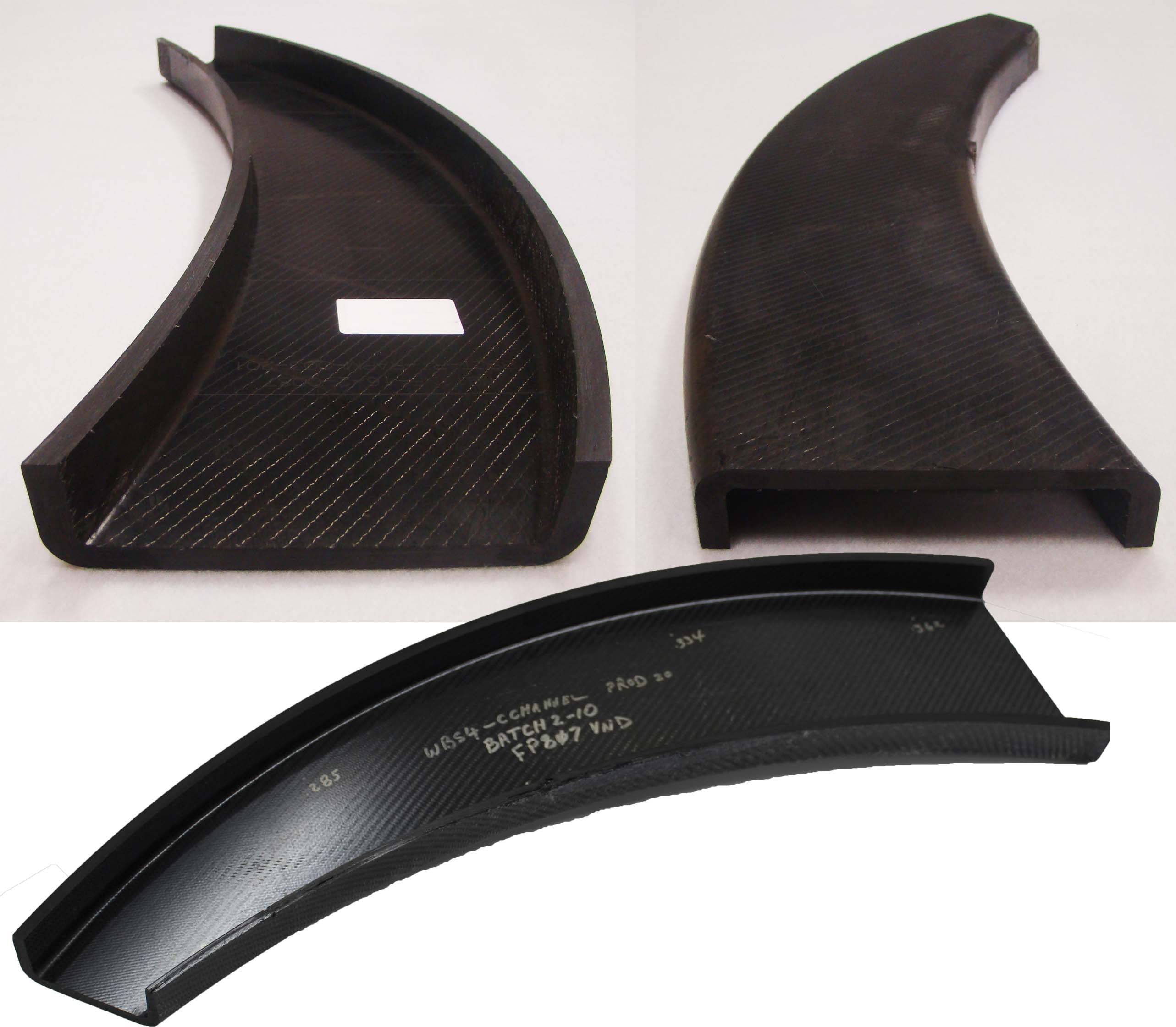
Оборудование PtFS также могло обеспечивать позиционное управление для поддержки метода инфузии зазоров для деталей RI-RAPM-003. В этом методе инструмент был закрыт до начальной высоты вакуумной прокладки, что позволяло инструменту оставаться открытым на 1,3 миллиметра во время инфузии. После завершения инфузии инструмент закрывали оставшееся расстояние, чтобы ввести смолу в преформу в z-направлении. Детали были успешно изготовлены с использованием этого процесса.
Динамический контроль температуры для термопластической штамповки
На оборудовании PtFS также был изготовлен изогнутый С-образный канал РАПМ-003 в термопластичных композитах. В частности, он использовался для консолидации сложной преформы, размер которой составлял от 32 до 24 слоев по длине детали, в плоскую заготовку с коническим поперечным сечением. Затем объединенные заготовки были отправлены в ATC Manufacturing (Пост-Фоллс, Айдахо, США), где на последней детали была нанесена штамповка с вертикальными фланцами.
Материалом для изогнутого С-образного канала TP-RAPM-003 была саржа из углеродного волокна 2x2, покрытая порошковой краской полиэфирэфиркетоном (PEEK). Рабочая ячейка PtFS использовалась для сверхпластической формовки магниевого баллона AZ31 над термопластичной загрузкой, нагрева баллона и загрузки до температуры процесса PEEK 400 ° C в прибл. 55 минут.
При этой температуре формования к баллону подавали газообразный аргон, который оказывал давление консолидации на термопластичный композиционный материал. Затем элемент охладил баллон и зарядился до температуры ниже температуры кристаллизации PEEK за 30 минут, общее время цикла - 3 часа.
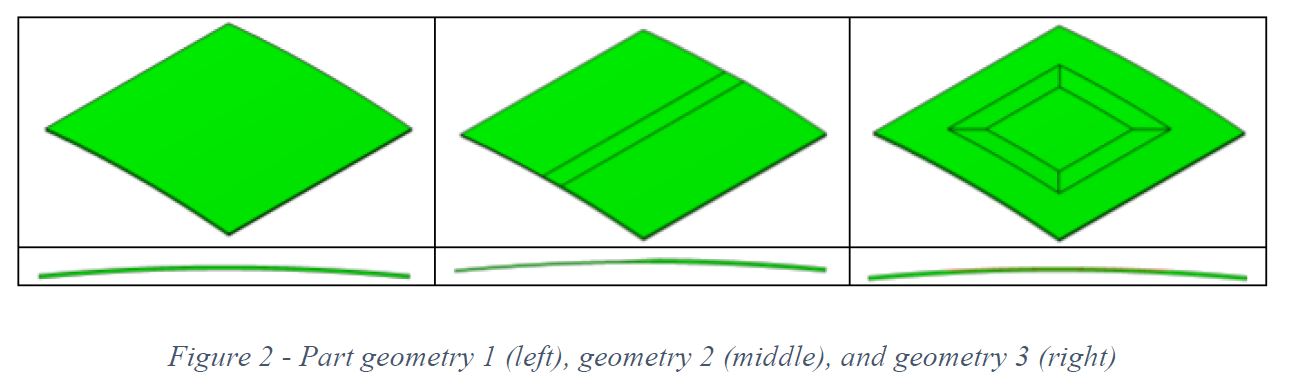
На слайде 11 выше показано изменение приложенного давления во время сверхпластического формования эластичного баллона и уплотнения термопласта, которое увеличивается с 20 фунтов на квадратный дюйм до 140 фунтов на квадратный дюйм после того, как баллон достигает температуры сверхпластического формования, которая поддерживается за счет охлаждения. Преформы были успешно консолидированы и отправлены в ATC Manufacturing, где на детали были нанесены штамповки для этой чрезвычайно сложной геометрии.
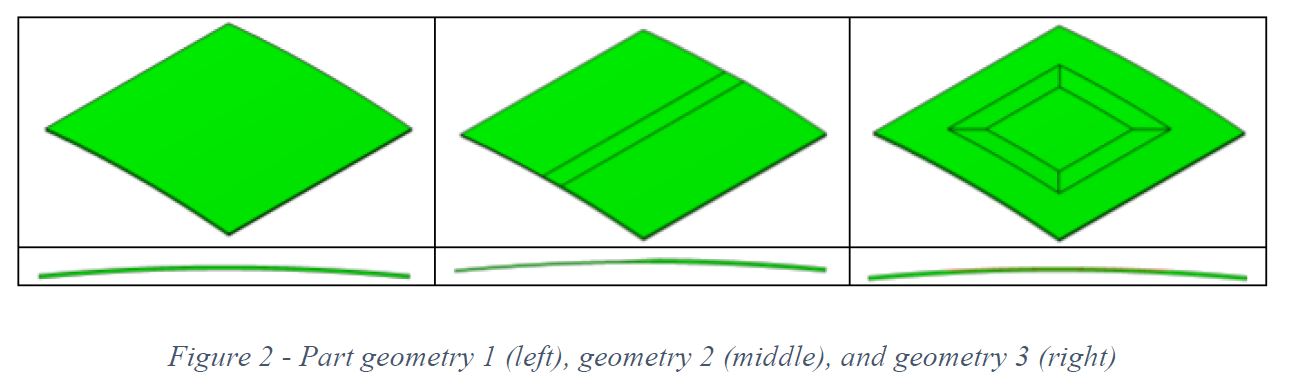
Ячейка PtFS также использовалась для пошаговой штамповки деталей панелей TP-RAPM-017, сделанных из сбалансированной и симметричной укладки однонаправленной (UD) ленты из углеродного волокна / полиэфиркетонекетона (PEKK), при изучении различных вариантов а особенности детали влияют на формирование мочевого пузыря. Панели TP-RAPM-017 имели размеры 40,6 на 40,6 сантиметра с плавным контуром, достигающим 1,3 сантиметра в высоту. Были оценены три различные геометрические формы деталей - плоская (без перепада слоев), одностороннее падение слоя и рамка для изображения - с 32 слоями в толстых областях, 16 слоями в тонких областях и соотношением падения слоев 20:1 между ними. Продолжительность цикла обработки составляла 1,5 часа для всех геометрических форм.
Грани инструмента были изготовлены из инвара 42, чтобы наилучшим образом соответствовать тепловому расширению ленты из термопластичного композита UD. Комплекты слоев ленты UD были вырезаны и собраны в комплекты, сварились вместе ультразвуковой сваркой и помещены в инструмент для вулканизации, где они были нагреты до 385 ± 15 ° C. Были испытаны различные циклы давления, а затем деталь была охлаждена до температуры ниже 220 ° C, после чего давление было сброшено, и деталь была извлечена из формы.
Один пример цикла давления для геометрии 1 составлял 20 фунтов на квадратный дюйм при комнатной температуре, подъем до 140 фунтов на квадратный дюйм после того, как запаздывающая термопара достигла температуры расплава 310 ° C, а затем охлаждение со скоростью 10 ° C / мин под давлением до тех пор, пока термопара детали не измеряла ниже 220 ° C. . Были испытаны начальные давления 20 фунтов на квадратный дюйм, 30 фунтов на квадратный дюйм, 50 фунтов на квадратный дюйм и 70 фунтов на квадратный дюйм. График давления также варьировался от 10 фунтов на квадратный дюйм в минуту до 10 фунтов на квадратный дюйм за 15 секунд, вплоть до максимального давления в 140 фунтов на квадратный дюйм.
Одним из примечательных результатов было то, что все панели показали плохие результаты C-сканирования, когда слои были сварены прихваточным сварным швом. Таким образом, для достижения наилучших результатов такие прихваточные швы должны располагаться за пределами линии обрезки сетки детали. Были изготовлены приемлемые детали, но некоторые детали показали плохое уплотнение по краям слоев. Это было исправлено увеличением начального давления уплотнения до 30 фунтов на квадратный дюйм перед нагревом. Однако это увеличение давления привело к некоторой шероховатости / матовости поверхности детали со стороны баллона. Кроме того, на некоторых панелях с геометрией 2, изготовленных с использованием начального давления уплотнения 50 и 70 фунтов на квадратный дюйм, наблюдались складки в центре деталей. Считалось, что такое более высокое давление могло препятствовать скольжению слоев друг относительно друга во время обработки, таким образом удерживая складки на деталях.
Другой опробованный вариант заключался в замене газообразного аргона на более дешевый газообразный азот для создания давления в баллоне, но это также снизило качество деталей, включая шероховатость поверхности / матовое покрытие, что привело к более высоким уровням затухания в результатах C-сканирования, даже несмотря на то, что пористость не была обнаружена на перекрестных изображениях. разделы.
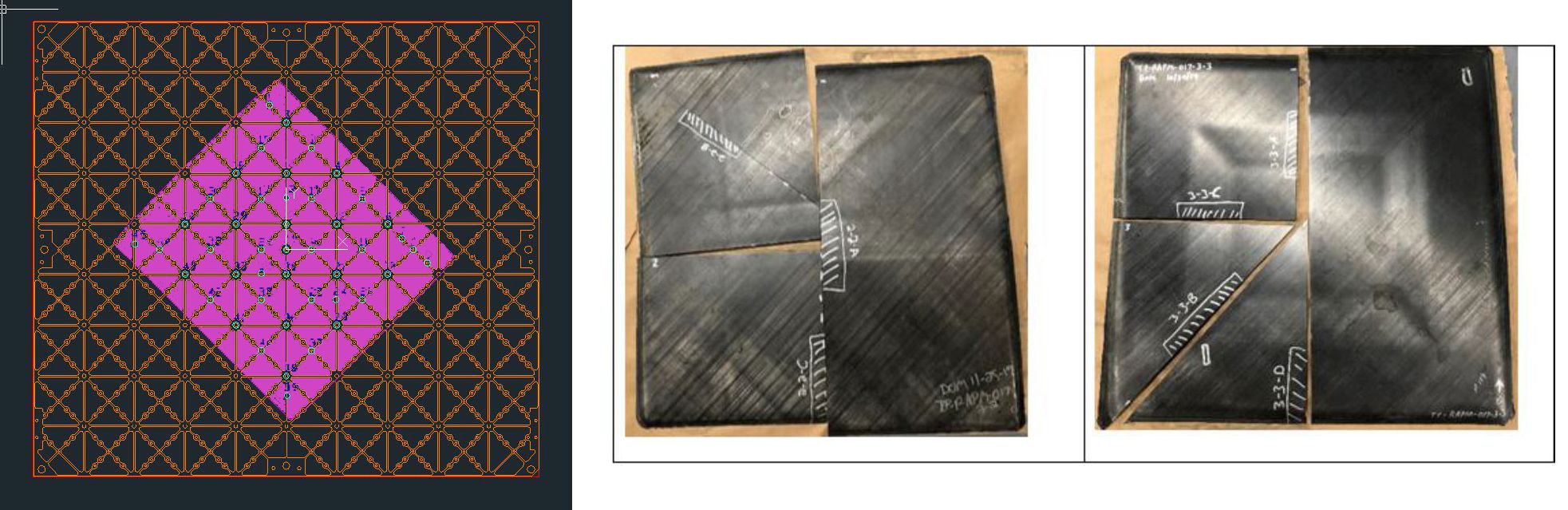
Плюсы и минусы PtFS в RAPM
Рабочая ячейка PtFS продемонстрировала быстрый нагрев (<10 минут для отверждения эпоксидной смолы при ≈180 ° C). В сочетании с автоматической сменой инструмента это может обеспечить быструю замену деталей и снизить стоимость композитных деталей при небольших производственных циклах. PtFS также хорошо подходит для высокотемпературных динамических прогонов (в отличие от циклов изотермической части).
Возможности ячейки PtFS компании Boeing St. Louis были значительно увеличены во время программы RAPM благодаря улучшенным обновлениям программного обеспечения для улучшения тепловой однородности и управления зажимными приспособлениями, улучшенной охлаждающей способности и управления термопарами, а также автоматизированной системы управления давлением пресс-клавов. Дальнейшее увеличение возможностей может быть возможным за счет использования огромного количества данных, генерируемых и записываемых системой каждую секунду, включая уставку каждого канала нагревателя, рычаг мощности нагревателя, уровень сжатого воздуха и т. Д. Применение машинного обучения к этим данным может обеспечить качество детали и улучшения процесса. Дальнейшие усовершенствования программного обеспечения также могут позволить с помощью этих данных выявлять аномалии обработки, такие как потребляемая чрезмерная энергия и низкая чувствительность определенных местоположений инструментов.
«PtFS обеспечивает множество настроек, как следует из названия:от производства до функциональной спецификации, - говорит Хан, - но такая настройка может потребовать затрат времени на создание и« настройку »системы для новой конфигурации инструмента / детали». Большинство обработанных металлических поверхностей инструмента для RAPM были произведены компанией Surface Generation в Великобритании, однако Boeing и Surface Generation «обучили» проектировщика инструментов из США и производителя инструментов США, чтобы продемонстрировать, что проектирование лицевых поверхностей пресс-формы можно проводить в США. из источников, отличных от Surface Generation. Эта лицевая панель инструмента CMD-TP-RAPM-008-503 успешно использовалась для изготовления панелей доступа для коротких волокон TP-RAPM-008-203.
«Хотя некоторая форма контроля температуры в инструменте и / или детали помогает при формовании всех композитных деталей, - объясняет Хан, - на самом деле требуется контроль температуры в критических областях и в определенные моменты времени, и это зависит от детали и процесса. Таким образом, ключевым моментом является понимание контроля температуры, фактически необходимого для изготовления данной детали. 180 зон в PtFS полезны, но также дороги, потому что каждая требует обработанного канала в инструменте. Если детали нужны только внешняя и внутренняя зоны или определенная зона по геометрии триггерной точки, то другое решение может быть более доступным. Тем не менее, это вызывает дебаты о том, как лучше всего разработать ячейку для производства деталей из композитных материалов, гибкую для различных типов процессов и деталей ».
Boeing и DARPA продолжат добавлять информацию к этим дебатам, поскольку они завершат программу RAPM в 2020 году и опубликуют дальнейшие результаты.
Смола
- Проблемы при разработке новых продуктов
- Арифметика с научной записью
- Вопросы и ответы с архитектором решений Индустрии 4.0
- Boeing сотрудничает с Microsoft по развитию авиационной аналитики
- Развитие современных пластмасс
- Solvay сотрудничает с Boeing в создании защитных экранов от коронавируса
- SABIC и NUDEC запускают возобновляемый ПК
- Композитные материалы для 3D-печати с непрерывным волокном
- Запуск проектов с нуля с помощью аутсорсинга
- Boeing подтверждает соглашение с Siemens Mentor Graphics