Большие композитные покрытия защищают много воды
Хранение и доставка воды в Боготе, Колумбия, как и в любой другой большой городской местности, сложны. Проблема заключается не в обеспечении, поскольку в городе с населением около 9 миллионов человек ежегодно выпадает 32 дюйма (824 миллиметра) дождя, плюс река Богота протекает через город. Задача состоит в том, чтобы собрать эту воду, обработать ее и затем хранить, чтобы она оставалась пригодной для питья и была доступна по мере необходимости для жителей и предприятий. Для этого Empresa de Acueductos y Alcantarillados (Компания акведуков и канализации, EAAB, Богота) на протяжении многих лет построила серию из 59 резервуаров по всему городу для хранения очищенной воды и обеспечения снабжения клиентов.
Некоторые из этих резервуаров представляют собой настоящие резервуары - полностью закрытые для защиты воды от внешних элементов. Другие, многие из которых более старые, представляют собой массивные бетонные бассейны, защищенные от непогоды серией съемных крышек. Один такой резервуар под названием Casablanca, расположенный в районе Сьюдад-Боливар в южной части Боготы, обслуживает население около 3 миллионов человек. Касабланка, самый большой резервуар для хранения воды в сети EAAB и самый большой резервуар для хранения воды в Колумбии, имеет размеры 144 метра (472 фута) в длину, 110 метров (361 фут) в ширину и 9 метров в глубину и имеет емкость для хранения 143 000 кубических метров ( 38 миллионов галлонов воды. Резервуар делится пополам бетонной перегородкой, проходящей по его середине, так что вода хранится в двух равных частях.
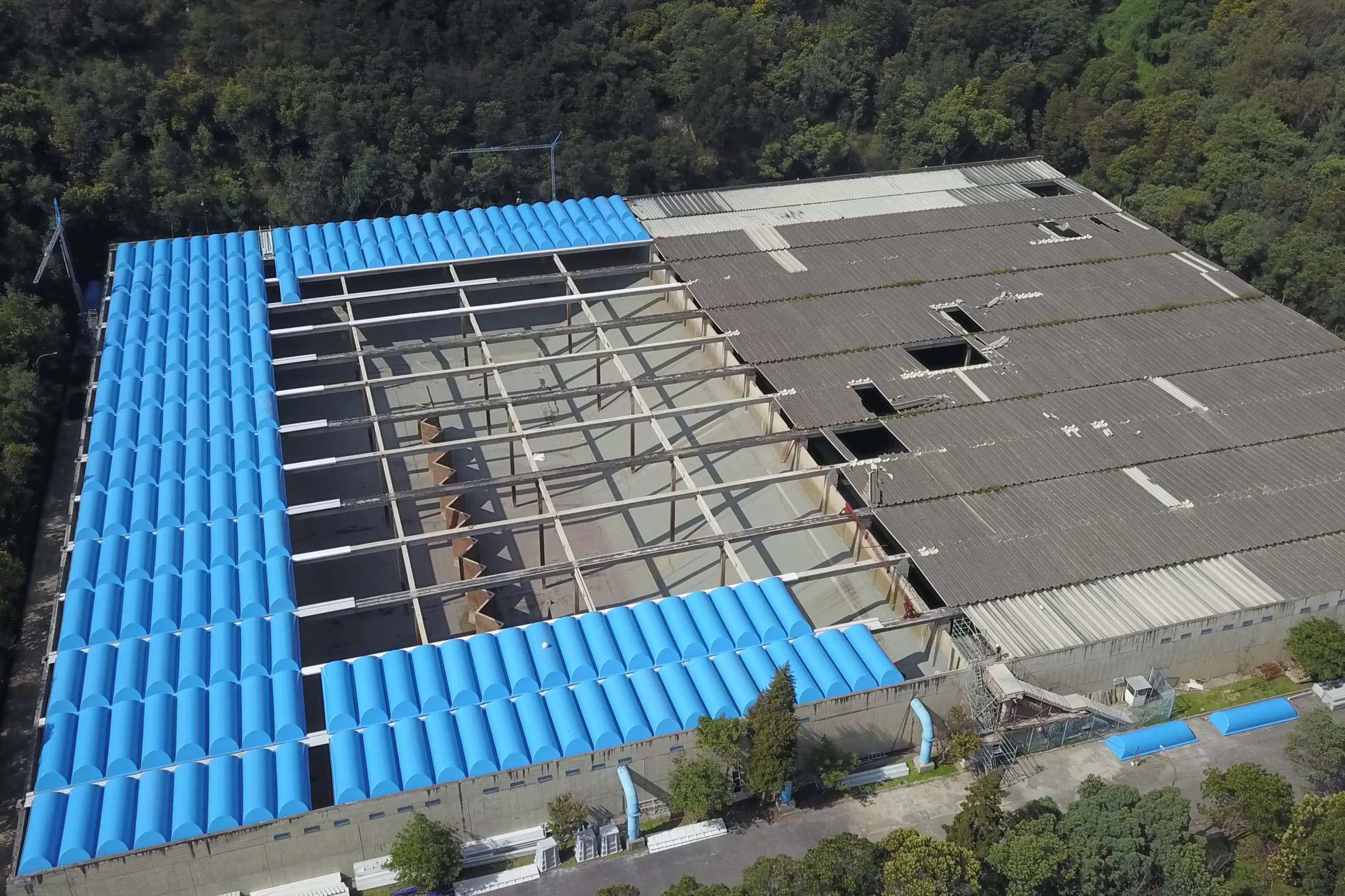
Удержать 66-летнюю Касабланку - непростая задача. В 2009 году было обнаружено, что трещины в бетонном полу резервуара пропускали 360 000 литров (95 000 галлонов) воды каждый час . . Ремонт бетона с покрытием из полимочевины снизил утечку до нуля. Однако у Касабланки все еще была проблема над бетоном. Вода в резервуаре была защищена серией крышек, которые состояли из смеси бетона и асбеста, что представляло значительную угрозу для качества воды и здоровья человека. Старые крышки также были подвержены поломкам и были дорогостоящими в обслуживании. EAAB необходимо было заменить старые крышки на более безопасную, легкую и долговечную альтернативу.
Большие обложки и много их
EAAB решила использовать композитные материалы для крышек, но сразу же столкнулась с проблемой масштабом проекта. Касабланку пересекает серия бетонных столбов, которые поддерживают сеть балок, на которые опираются покрытия. Эти балки расположены на расстоянии около 7,2 метра (23,6 фута) друг от друга, поэтому новые покрытия должны быть самонесущими и покрывать этот пролет, чтобы можно было использовать существующую инфраструктуру. EAAB предложила изготавливать такие крышки с помощью литья под давлением из легкой смолы (LRTM). Соревнование? Композитные конструкции такого размера, необходимые для этого приложения, никогда не производились с помощью LRTM в Колумбии. Многие производители просто не смогли взяться за проект.
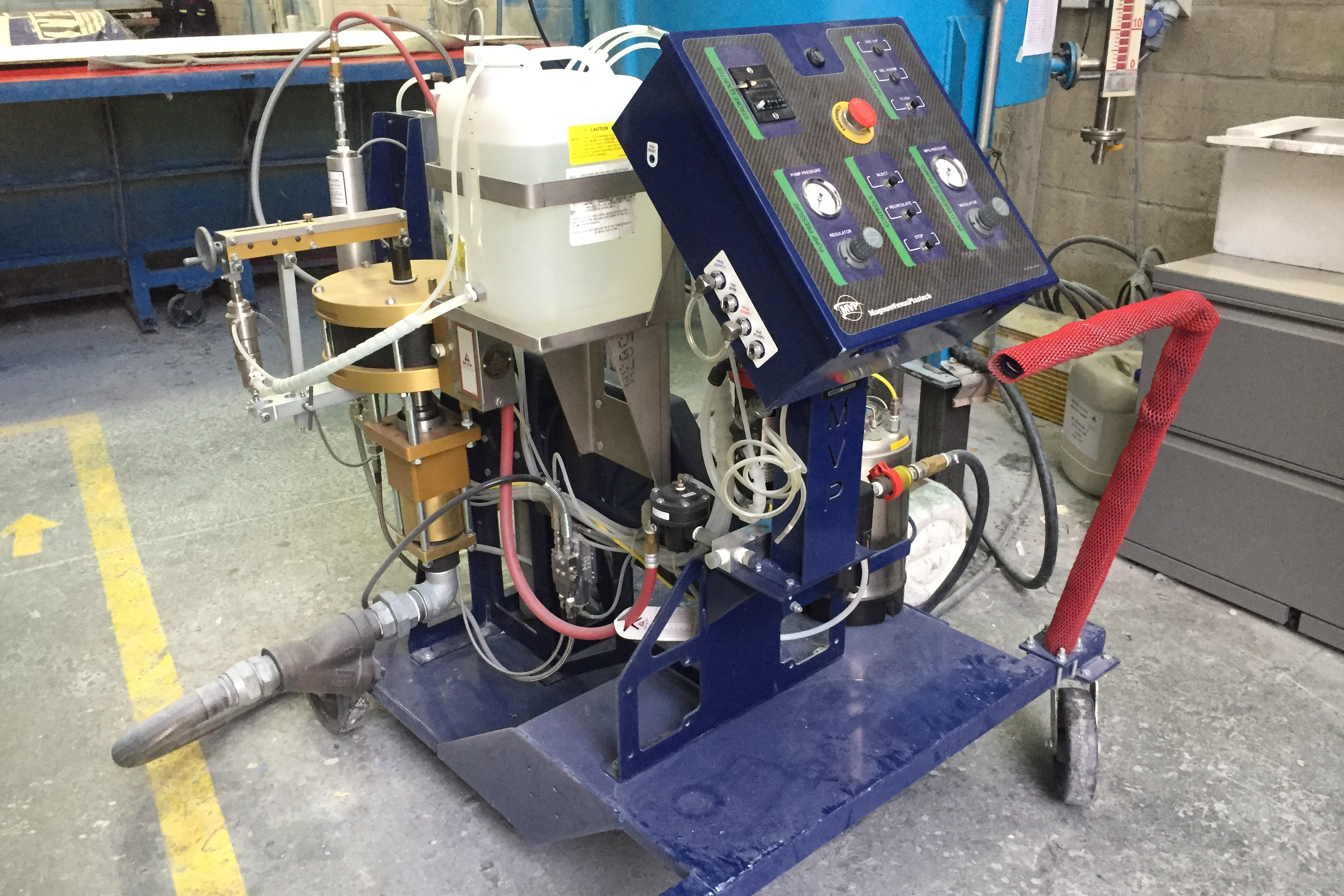
Исключение составляла компания Innovative Engineering Solutions, или Soling, производитель композитных материалов, расположенный в Ла-Эстрелья, Антиокия, Колумбия, к югу от Медельина. Компания Soling была основана в 2014 году Хавиаром Морено, который владеет и управляет несколькими компаниями по производству композитов в Колумбии и за ее пределами. Родриго Вергара, инженер-координатор Soling, говорит, что размер крышек не стал решающим для многих производителей. «Никто не сталкивался с этим в Колумбии из-за размера детали», - отмечает он. «Это самая большая композитная деталь, изготовленная в Колумбии». Для Морено, однако, размер обложек был интересной проблемой. «Для нашего владельца [Морено], - говорит Вергара, - это была мечта. «Невозможное» - это слово, которого он не понимает. Он сказал:«Мы сделаем это!» Я сказал:«Хорошо!»
Солинг предложил конкретное решение для проекта в Касабланке:серия 840 куполообразные прямоугольные композитные конструкции, каждая размером 7,6 метра в длину и 2,4 метра в ширину (24,9 x 7,9 футов). По словам Вергара, была выбрана конструкция полукруглого купола, потому что «геометрическая форма, которая имеет наибольшее механическое сопротивление, - это окружность. Это был главный фактор, гарантирующий, что покрытия будут самонесущими. С другой стороны, нам нужно было найти самый простой способ доставить их с производственной площадки до точки установки, которая находилась в 260 милях от нас ».
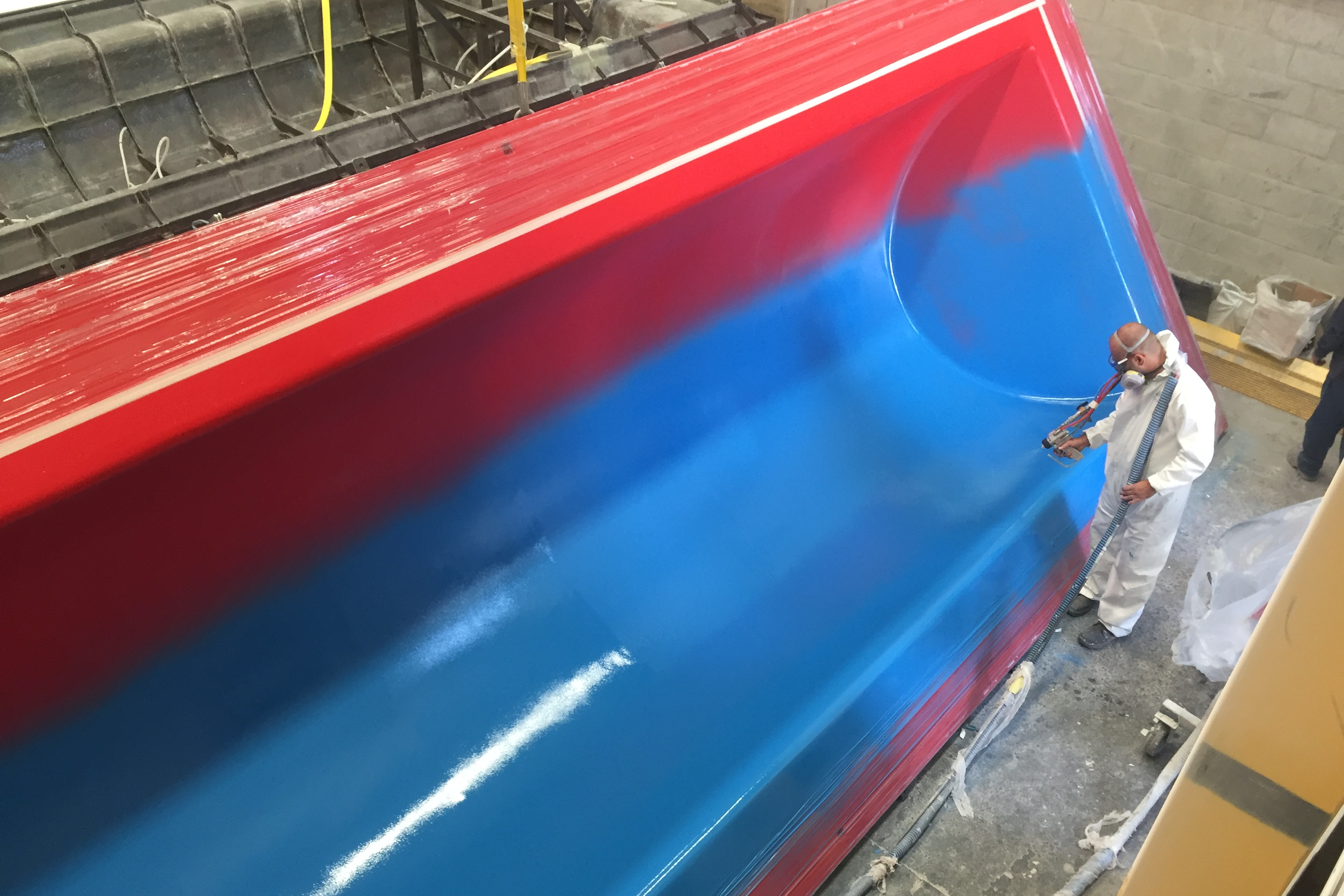
Покрытия будут изготавливаться с помощью LRTM с, в соответствии со спецификацией EAAB, синим гелевым покрытием на внешней поверхности и белым гелевым покрытием на внутренней поверхности. Покрытие, состоящее из стекловолокна и полиэфирной смолы, имеет площадь поверхности 28,5 квадратных метров (207 квадратных футов) и будет весить 320 килограммов (705 фунтов), из которых 208 килограммов составляют смола. Вергара и Солинг взялись за работу, имея в руках дизайн и готовые предоставить обложки.
Создание идеального прикрытия
Солинг, конечно же, взялся за проект Касабланки не без посторонней помощи. С компанией работала сеть поставок, в которую входили дистрибьютор, поставщик материалов и поставщик оборудования. Дистрибьютор Minepro SAS (Медельин, Колумбия) оказывал техническую поддержку и работал с поставщиком оборудования Magnum Venus Products (MVP, Ноксвилл, Теннесси, США), который поставлял насосы и вспомогательное оборудование для процесса LRTM. Поставщиками материалов являются компания Andercol (Медельин), которая предоставила матрицу из полиэфирной смолы, гелькоуты и техническую поддержку, и Jushi (город Тунсян, Китай), которая предоставила ткани из стекловолокна E.
Производство, естественно, начинается с оснастки. Вопрос был в том, сколько форм требуется для проекта. Вергара говорит, что для того, чтобы определить это, Soling сначала нужно было определить темпы производства, чтобы соответствовать требованиям EAAB. На это, в свою очередь, повлияли требования на рабочем месте. Чтобы избежать потенциального загрязнения водопровода во время установки новых крышек, EAAB согласилась опорожнить половину Касабланки, над которой были доставлены крышки, и опустить их на место. Уменьшение емкости резервуаров для воды в Касабланке наполовину создает проблемы, поэтому EAAB потребовалась доставка и установка в кратчайшие сроки.
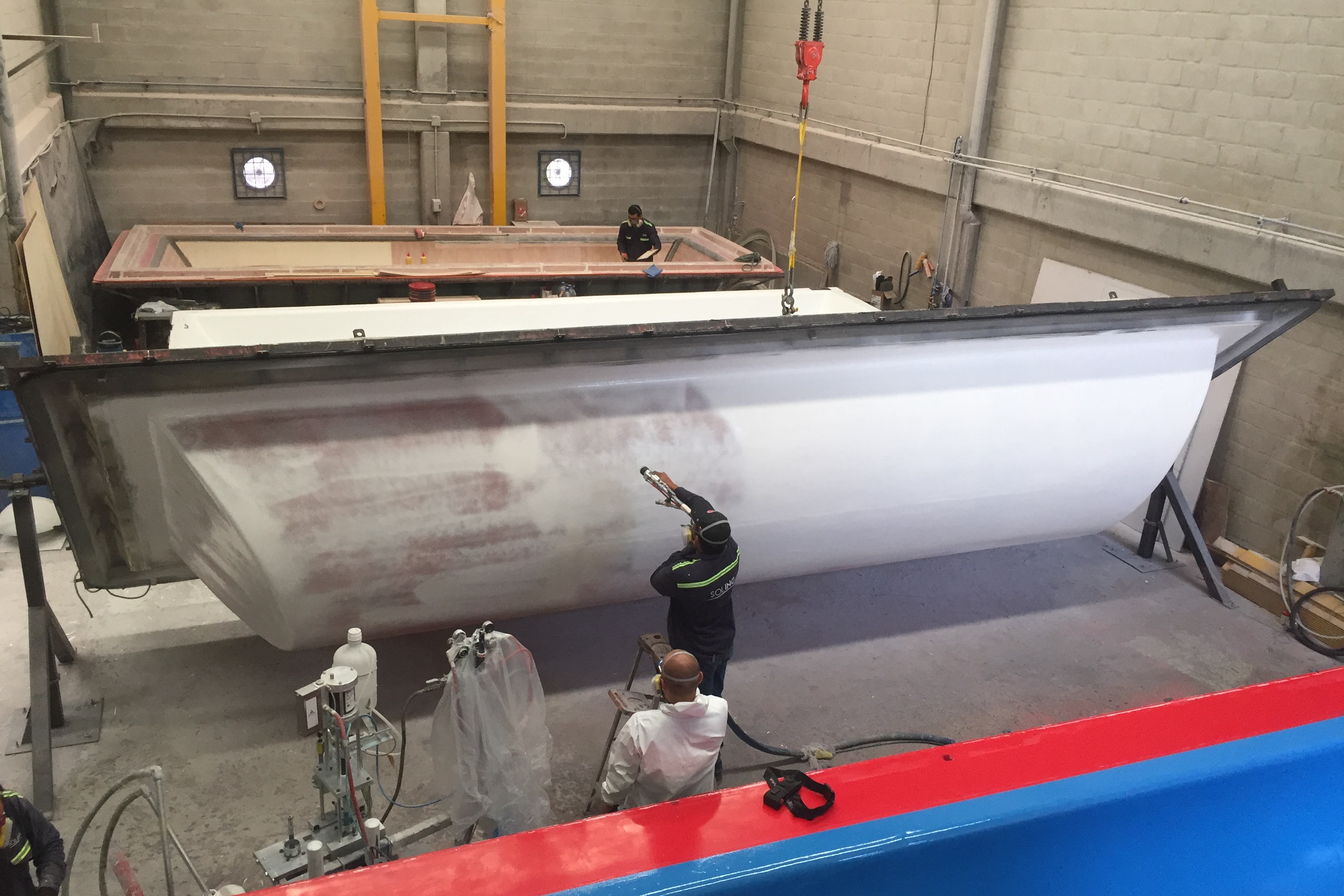
Солинг, работая с EAAB, объясняет Вергара, установил производственный график, согласно которому каждый день будет поставляться шесть обложек. На предприятии, работающем в три восьмичасовые смены в день, требовалось две пресс-формы, каждая из которых позволяла изготавливать одно покрытие за смену. Формы, по его словам, были изготовлены собственными силами и состояли из конструкции охватывающая и охватывающая часть из стекловолоконного композитного материала, поддерживаемого стальной опорной конструкцией.
Создав формы, Солинг затем начал работу по определению того, как, в частности, будут изготавливаться купола. Вергара говорит, что работая с Minepro и MVP, было решено, что каждая форма будет питаться двумя портами для впрыска смолы с одним вакуумным портом. Для впрыска смолы компания MVP рекомендовала использовать насосную установку для формовки большого объема смолы (RTM) Patriot Innovator, которая способна подавать большой объем смолы, необходимый для каждой крышки. MVP также предоставила клапаны Turbo Autosprue, а также универсальные муфты, уплотнения и принадлежности для пресс-форм.
Чтобы начать производство покрытия, говорит Вергара, на охватывающую половину формы был нанесен белый гелькоут, а на охватываемую половину формы - синий гелькоут. Как уже отмечалось, оба гелькоута были поставлены Andercol. Затем коврики и ткани из E-стекла, поставленные Jushi, вручную уложили в женскую половину формы. За этим следовало опускание с помощью крана охватываемой половины формы в охватывающую половину, при этом две половины были зажаты вместе. После снятия вакуума началось нагнетание смолы. Вергара говорит, что инъекция каждого покрытия была завершена примерно за 40 минут, после чего следовало отверждение при комнатной температуре. После демонтажа каждой крышки ее обрезали до окончательных размеров, а на поверхности фланца крышки прорезали каналы подачи дождевой воды.
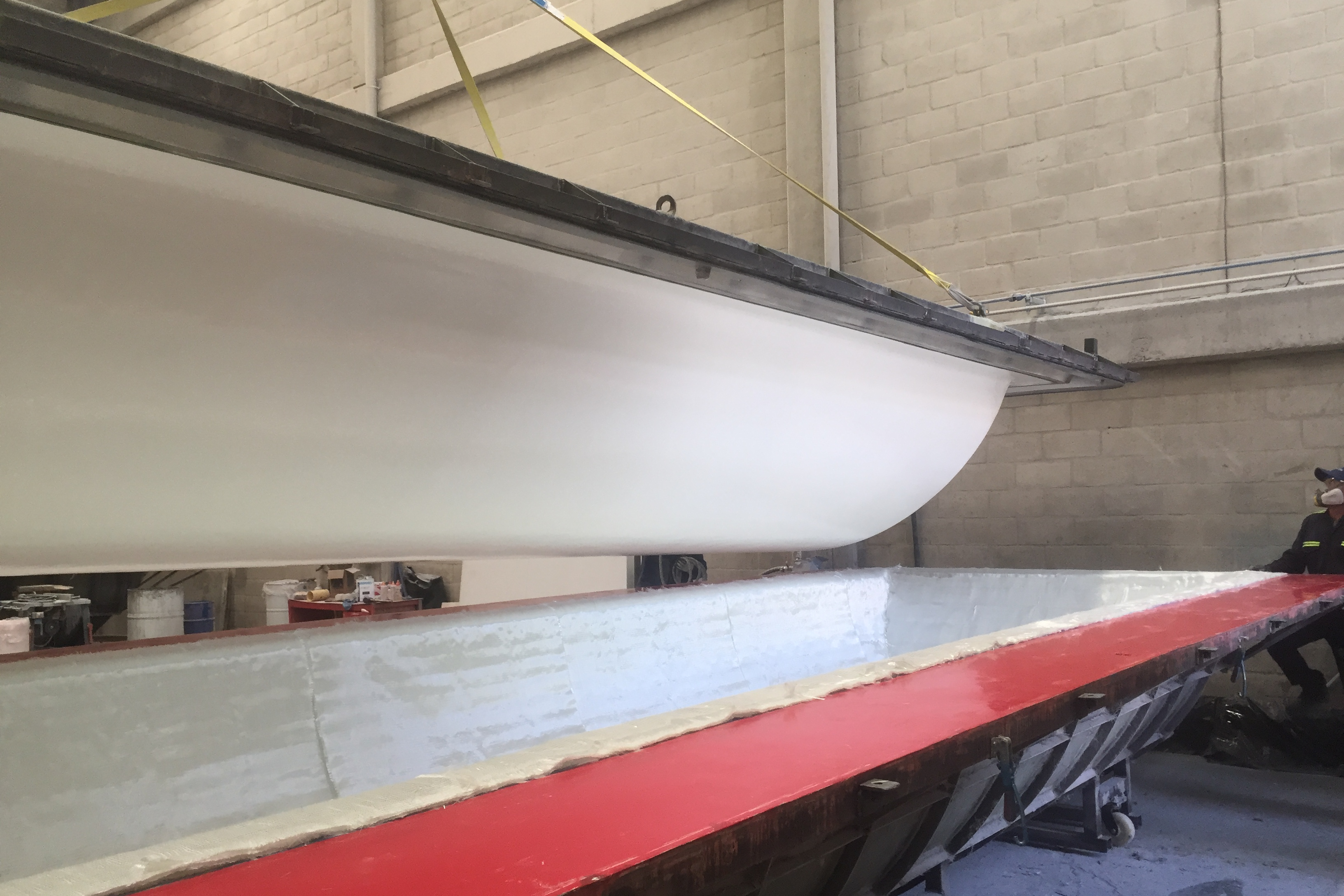
Вергара говорит, что огромные размеры крышек в сочетании со строгими требованиями к весу и размерам создают наибольшую проблему для их производства. Для определения местоположения порта впрыска и управления временем впрыска потребовалось много проб и ошибок, а также консультации с техническими экспертами. Однако в конце концов, по словам Вергара, Солинг остановился на процессе изготовления, который оказался очень воспроизводимым и надежным.
«Самой большой проблемой был вес элементов, которые мы собирались установить, потому что мы не могли превысить грузоподъемность существующей конструкции», - говорит Вергара. «Это требовало, чтобы все детали имели одинаковые характеристики как по геометрии, так и по весу. Единственный способ гарантировать эти условия - использовать процесс, гарантирующий повторяемость ».
Готовые покрытия были отправлены на расстояние 418 километров (260 миль) от завода Soling около Медельина до рабочей площадки в Касабланке в Боготе, а затем установлены с помощью крана, опущены на опорную конструкцию и размещены рабочими, стоящими на балках, на которые будут опираться покрытия. Хотя крышки механически не прикреплены к опорным конструкциям, Вергара говорит, что они также не предназначены для перемещения или снятия, если «не произошло чего-то очень серьезного».
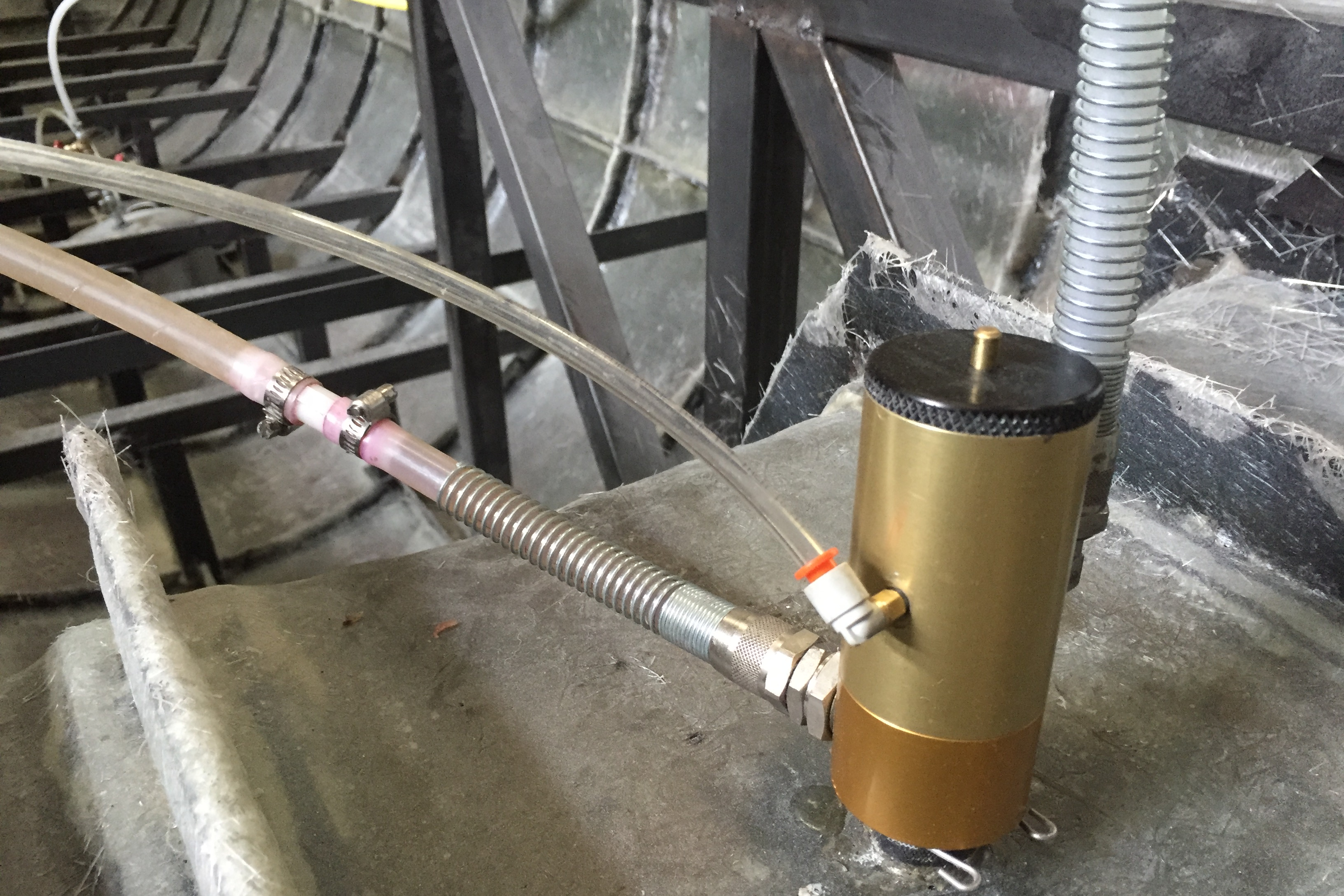
Soling приступила к проектированию крышек в начале 2019 года и приступила к изготовлению первых крышек в 2020 году. Пандемия коронавируса и случайные механические проблемы вызвали остановку и запуск производства, но Вергара говорит, что Soling завершила производство всех 840 покрытий за период 7- 8 месяцев, срок окончания - конец 2020 года. Ожидается, что новые покрытия прослужат значительно дольше и потребуют гораздо меньше обслуживания, чем те, которые они заменили.
По словам Вергара, проект в Касабланке продемонстрировал возможности Soling как производителя высококачественных, высокопроизводительных, больших композитных конструкций и открыл двери для других возможностей. «Этот проект был вызовом, в котором нам пришлось сломать парадигмы, которые говорили, что детали такого масштаба не могут быть изготовлены с использованием этого производственного метода, и тем не менее мы это сделали», - говорит он. «Что касается будущего Soling, кое-что предельно ясно:нет проекта, который мы бы не смогли выполнить».
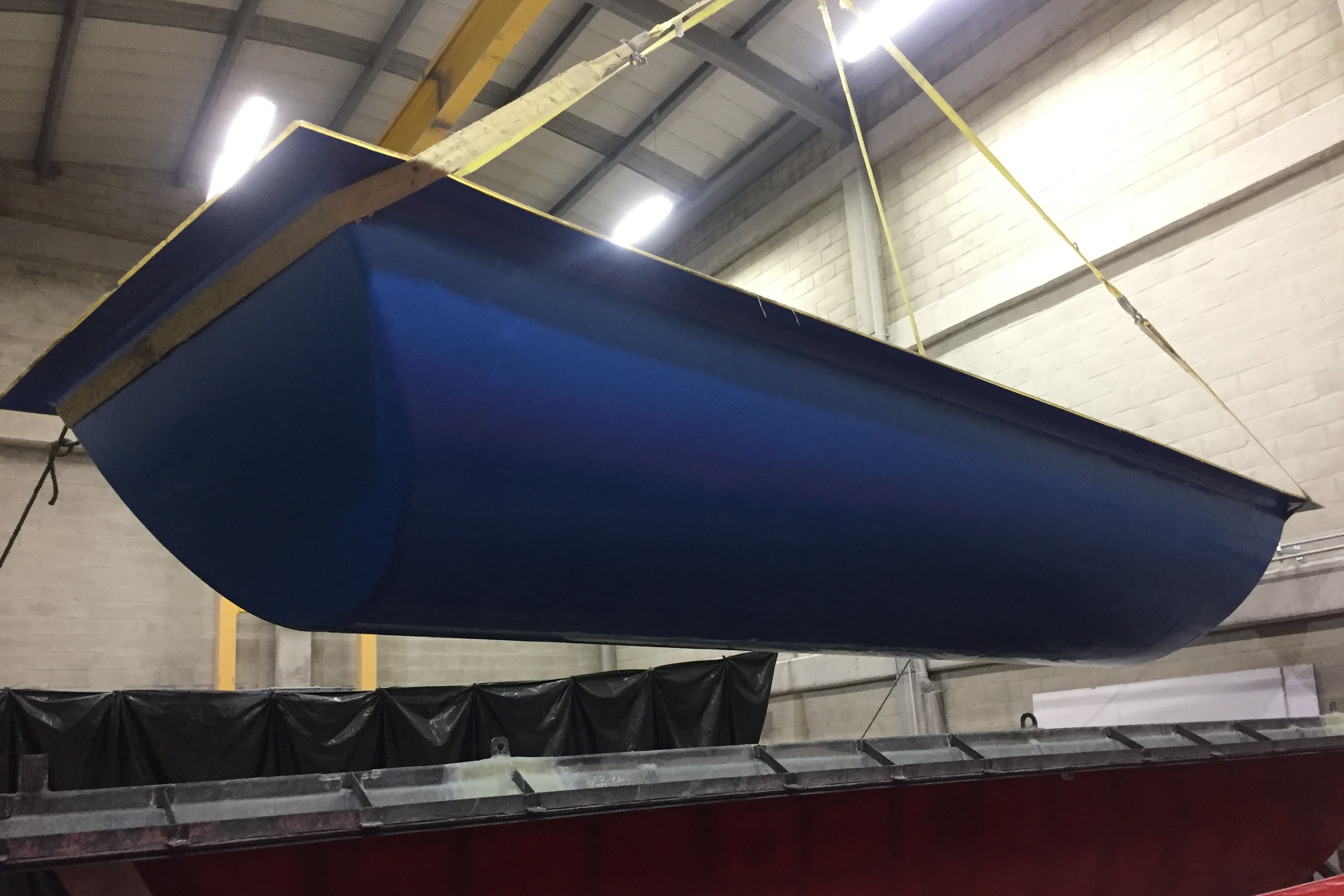
Смола