Термопластические композиты:структурный кронштейн бампера
Chevrolet Silverado от GM 2019 модельного года (MY) Пикапы имеют новое структурное применение для композитов в скрытом, но очень эффективном месте:слева и справа спереди за стальным бампером. Гибридный кронштейн из термопластичного композита / металла снижает массу, обеспечивает эквивалентные или лучшие характеристики в модальных, стрессовых, усталостных и краш-тестах в ограниченном пространстве упаковки, снижает риски коррозии и гарантии и позволяет значительно консолидировать детали. Все фотографии предоставлены General Motors Co.
Непросто быть инженером-конструктором OEM, работающим над программами полноразмерных пикапов. С одной стороны, вы хотите сделать эти автомобили максимально безопасными, многофункциональными и экономичными. С другой стороны, ваши клиенты, особенно в строительной и сельскохозяйственной отраслях, каждый день усердно работают над своими автомобилями и имеют определенные представления о том, что является прочным материалом, а что нет. Они знают сталь и доверяют ей. Композиты? Может, не так уж и много.
Как Крис Хео, ведущий инженер по разработке полноразмерных пикапов в General Motors Co. (GM, Детройт, штат Мичиган, США), и его команда начали работу над последним поколением Chevrolet Silverado пикапы, они обсудили, какие приложения они могли бы преобразовать из металла в композиты, чтобы уменьшить массу автомобиля.
В 2019 модельном году (MY) уже было принято решение сохранить стилизованные ударные планки бампера - штампованные стальные бамперы со стилизованными поверхностями и отделкой (хромирование или окраска в цвет кузова) - на передней и задней части автомобиля. . Из-за стилизованной формы и массы стальных корпусов для таких бамперов обычно требуется один или несколько кронштейнов стальной арматуры для соединения бампера с рамой автомобиля и соответствия требованиям GM по долговечности бампера, повреждаемости автомобиля, характеристикам при столкновении и требованиям к упаковке. В этом случае пара скоб обернута вокруг левого и правого углов бампера. Члены команды задавались вопросом, смогут ли они превратить эти тяжелые, сложные, состоящие из нескольких частей штампованные детали во что-то более легкое без ущерба для производительности или долговечности.
«Мы обсудили, как сохранить металлическую обшивку бампера, но преобразовать скрытые компоненты в легкие», - вспоминает Хео. «Мы знали, что это будет проблемой, потому что вам нужны прочные кронштейны, чтобы удерживать тяжелую деталь, например бампер, а бамперы и кронштейны должны служить в течение всего срока службы автомобиля. Кроме того, эти кронштейны являются ключевыми при выполнении жестких краш-тестов со смещением барьеров, и даже в случае металлов - эти испытания сложно пройти ».
Сначала попробую
Не испугавшись этой проблемы, команда GM приступила к работе и вскоре привлекла к сотрудничеству специального поставщика бампера для автомобиля, Flex-N-Gate Corp. (FNG, Урбана, Иллинойс, США). Первоначально, поскольку внешний вид автомобиля все еще находился на доработке, объединенная команда провела год, исследуя варианты в отрасли и обсуждая подходы, которые могут сработать. «Мы ждали подходящего времени, потому что, в зависимости от окончательного стиля, это могло изменить дизайн, который мы использовали, и подход, который мы выбрали», - объясняет Хео.
«Мы знали, что другая компания преобразовала очень маленький кронштейн - тот, который не был конструктивным - в композитный на одном из бамперов грузовиков, так что это дало нам место для начала», - добавляет Стив Перукка, менеджер группы инженеров FNG - R&D Plastics. / металлы. У FNG уже был большой опыт преобразования конструкционных металлических деталей в термопластичные композиты на легковых автомобилях, и это придало команде уверенности двигаться вперед.
Рекомендации по дизайну
По мере того, как внешний вид пикапа был утвержден, объединенная команда начала свою собственную работу по дизайну кронштейнов со списком пожеланий и потребностей. Кронштейны для эталонов были штампованы из высокопрочной / низколегированной (HSLA) стали, выбранной из-за ее более высоких механических свойств и улучшенной коррозионной стойкости по сравнению с углеродистой сталью. Кронштейны имели номинальную толщину 3 миллиметра и весили 4,362 кг каждая. Во-первых, композитные кронштейны должны были уместиться примерно в том же пространстве упаковки, которое было ограничено за бампером. Таким образом, требовался материал с достаточной прочностью, чтобы толщина детали не увеличивалась значительно.
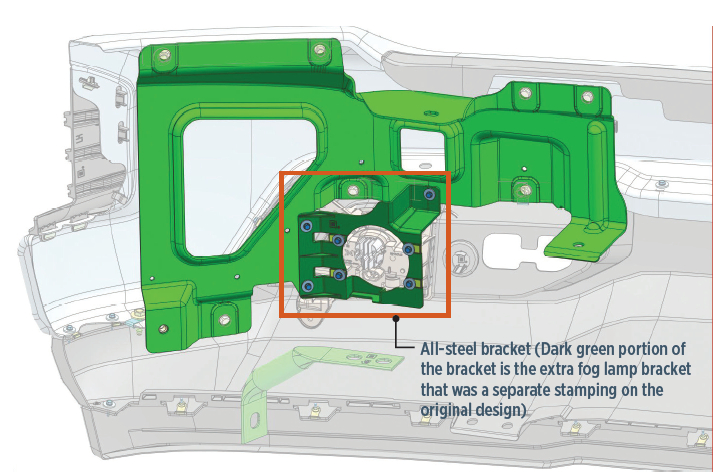
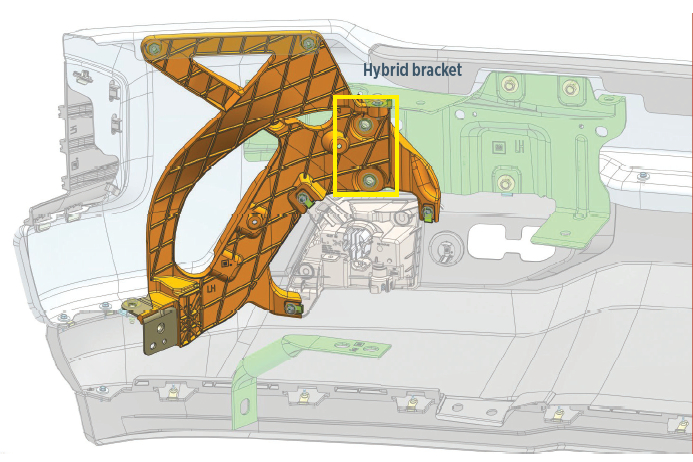
Во-вторых, передние бамперы обычно огибают передние углы автомобиля, чтобы добиться стиля, которого требует дизайн-студия. Однако, поскольку они удерживаются на раме жесткими стальными скобами, во время столкновений на высокой скорости бампер может врезаться внутрь колеса, что отрицательно повлияет на ориентацию колеса и заблокирует рулевое управление. Чтобы защитить колесо на стороне удара как можно дольше, желательно, чтобы кронштейны бампера отламывались во время удара. С другой стороны, чтобы избежать проблем с гарантией, бампер должен оставаться прикрепленным при нормальном использовании в течение всего срока службы автомобиля. Следовательно, команде нужно было определить, как сбалансировать эти конкурирующие потребности.
Еще одна проблема, которую команда хотела решить, заключалась в том, что из-за ограничений, связанных с формуемостью стали, контрольные кронштейны не могли иметь форму, позволяющую удерживать противотуманные фары автомобиля, что потребовало использования еще одной пары кронштейнов из тяжелого металла. Если это было возможно, команда хотела объединить опору противотуманных фар в композитный кронштейн.
Кроме того, было важно избегать защемления жгута проводов при его прохождении через кронштейн, чтобы жгуты и провода не натирались и не ломались, что могло бы привести к короткому замыканию таких важных элементов, как фары и вентиляторы. Чтобы избежать этого, сделав отверстие в металлических скобах, через которое могли бы проходить провода, пришлось использовать дополнительную операцию перфорации, что увеличивало затраты на инструменты из-за ограничений свободы конструкции. Поэтому было желательно попытаться решить эту проблему в составной скобке. Конечно, также было важно избежать внесения изменений в сборку автомобиля для использования композитных кронштейнов. И, как это часто бывает в автомобильной промышленности, композитные кронштейны в идеале были бы легче и дешевле металлических эталонов. Еще одна проблема заключалась в том, могут ли доступные в настоящее время модели CAE точно предсказать многоцикловую усталость / долговечность прерывистого армированного волокном термопласта.
Гибридный подход
Со своим списком желаний команда занялась делом. Первым решением был выбор материала, который будет использоваться, а именно материала, с которым у FNG уже был опыт работы и одобрения GM. Они выбрали черный 40% -ный волокнистый полипропилен (LFT-PP) из длинного стекловолокна (LFT-PP) от Lotte Chemical (Сеул, Южная Корея) под названием Supran PP1340 GMW15890P. Поскольку кронштейны не подвергаются воздействию солнечного света и находятся на достаточном удалении от тепла двигателя, прочный олефиновый полимер будет обеспечивать адекватные тепловые характеристики. Марка с высокой текучестью, пригодная для литья под давлением, имела индекс текучести расплава (MFI) 40, что обеспечивало хорошее заполнение сложной геометрии без необходимости добавления дополнительных затворов; дополнительные ворота создают линии сгиба, которые более слабые, чем окружающий материал, и их следует избегать в конструктивных элементах, особенно в тех, которые должны пройти краш-тесты.
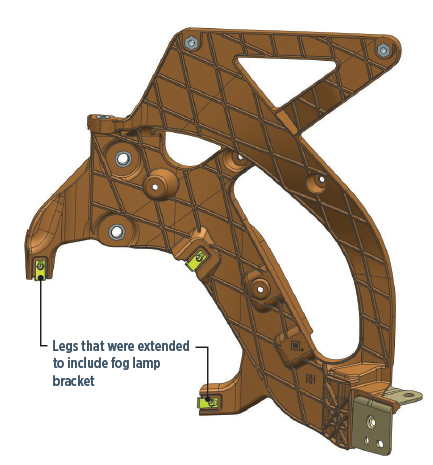
Чтобы уравновесить конкурирующие потребности в долговечности и высокой ударопрочности, команда применила гибридный подход и разделила кронштейн. Часть, соединяющая бампер с рамой, останется из стали HSLA, а внешняя часть будет преобразована в композит. Такой подход обеспечит большую свободу при проектировании для объединения деталей, уменьшения массы и включения противотуманных фар, но композитная часть будет спроектирована так, чтобы отрываться при высокоскоростном боковом столкновении, чтобы обеспечить продольную ориентацию колес как можно дольше. помогают поддерживать способность рулевого управления. Чтобы удовлетворить все требования GM, на композитную сторону кронштейна были добавлены несколько металлических вставок, а также три втулки, которые позволяют регулировать во время сборки. Дизайнеры обнаружили, что материал без проблем позволяет удлинить ножку кронштейна (изогнутые концевые детали, показанные в комбинированном / коричневом дизайне CAE), чтобы охватить противотуманную фару, что устраняет необходимость в отдельном кронштейне в этом месте (рис. 1).
По мере того, как проект продолжался, и физические части производились и тестировались, команда была рада узнать, что их модели CAE были достаточно точными. «Первоначально мы задавались вопросом, сможем ли мы правильно смоделировать деталь, учитывая, что мы пытались предсказать многоцикловую усталость с точки зрения долговечности и высокой перегрузки при моделировании столкновений», - отмечает Хео. «Удивительно, но корреляция между прогнозируемыми и измеренными результатами испытаний шейкерной машины была близкой, даже в случае аварии». Окончательный дизайн кронштейна был завершен менее чем за шесть месяцев. Он имеет размер примерно 41 x 46 см, номинальную стенку 3 миллиметра и имеет ребра жесткости для более высоких механических характеристик.
Инструмент был произведен Integrity Tool &Mold Inc. (Олдкасл, Онтарио, Канада) и представлял собой хорошо вентилируемую пресс-форму 2 + 2 с двумя полостями на пластину и двумя прямыми спусками (холодные литники) с последовательным запиранием клапанов, из которых получается четыре детали. / цикл из-за большого объема сборки Silverado Платформа. Подразделение Ventra Evart компании FNG является формовщиком. Цикл от кнопки к кнопке составляет 60 секунд.
Значительные достижения
При первом коммерческом использовании гибридный подход GM к конструктивному кронштейну бампера (рис. 2) принес множество преимуществ. Во-первых, он продемонстрировал эквивалентные или превосходные характеристики при модальных, стрессовых, усталостных и краш-тестах (см. Таблицу ниже).
Дизайн
10 Gx
20 Gx
1 st Частота режима (Гц)
Максимальное смещение (мм)
Максимальное напряжение (МПа)
Максимальное смещение (мм)
Максимальное напряжение (МПа)
Гибридный стальной / композитный кронштейн
2,00
213
3,97
381
31,7
Стальной кронштейн Benchmark
2.36
259
4,45
480
30,1
Гибридный композитный кронштейн с металлическими вставками не только уменьшил массу, но и его специальная геометрия улучшила как нагрузочные, так и модальные характеристики.
Во-вторых, свобода дизайна композитов позволила создать более агрессивный стиль при относительно небольшом пространстве корпуса. В-третьих, масса пары гибридных кронштейнов была уменьшена на 2,5 кг / автомобиль по сравнению с эталоном. А благодаря эффектам разложения массы более легкие углы бампера позволили уменьшить толщину кронштейна крепления бампера, а также других компонентов, поэтому общая масса системы переднего бампера была уменьшена на 7,3 кг по сравнению с предыдущей моделью 2016 года.
Кроме того, риск коррозии и гарантийные расходы были снижены, поскольку композитный кронштейн не ржавеет. Снижение массы приносит пользу потребителям, так как способствует экономии топлива или позволяет перевозить более тяжелую полезную нагрузку без превышения установленных законом пределов дорожной нагрузки.
В расчете на единицу стоимости гибридный кронштейн был стиркой из-за добавленной стоимости формы для литья под давлением. С точки зрения затрат на систему, экономия была достигнута за счет возможности замены дополнительных компонентов, хотя фактическую экономию трудно определить количественно. Кронштейн без проблем выпускается более трех лет.
Для следующего поколения Silverado , Команда Хео планирует и дальше использовать гибридные кронштейны на переднем бампере, но он уже призвал членов команды задуматься о том, как применить гибридный подход к кронштейнам заднего бампера. Это усложняется тем фактом, что задние бамперы содержат по углам вспомогательные элементы, позволяющие людям легко и безопасно забираться в / из пикапа. Кроме того, за стальной обшивкой размещено больше компонентов (например, датчики резервных предупреждений), что сокращает пространство упаковки.
«Мы продолжим использовать интеллектуальный инженерный подход, рассматривая проблемы, выясняя, как используются продукты и каковы их функциональные требования, а затем расширяем границы», - заключает Хео.
Смола
- Covestro увеличивает инвестиции в термопластические композиты
- Термопластические композиты в Oribi Composites:CW Trending, эпизод 4
- Устранение проблем термоформования термопластичных композитов
- Toray Advanced Composites расширяет возможности термопластичных композитов
- Teledyne CML Composites инвестирует в возможности обработки термопластов
- Cato Composites увеличивает производственные мощности по производству термопластичных композитов
- ACMA выпускает программу конференции Thermoplastic Composites Conference 2020
- Двери из термопласта впервые для автомобильных композитов
- Термопластические композиты:живописный вид
- Сварка термопластичных композитов