Прокаливаемость стали
Многие типы стали хорошо реагируют на метод термической обработки, известный как закалка. Одним из важнейших критериев при выборе материала заготовки является прокаливаемость. Прокаливаемость описывает, насколько глубоко металл может быть закален при закалке от высокой температуры, а также может называться глубиной закалки.
Сталь в микроскопическом масштабе:
Первый уровень классификации сталей на микроскопическом уровне — это их кристаллическая структура, способ расположения атомов в пространстве. Объемно-центрированные кубические (BCC) и гранецентрированные кубические (FCC) конфигурации являются примерами металлических кристаллических структур. Примеры кристаллических структур ОЦК и ГЦК можно увидеть ниже на рисунке 1. Имейте в виду, что изображения на рисунке 1 предназначены для отображения положения атомов и что расстояние между атомами преувеличено.
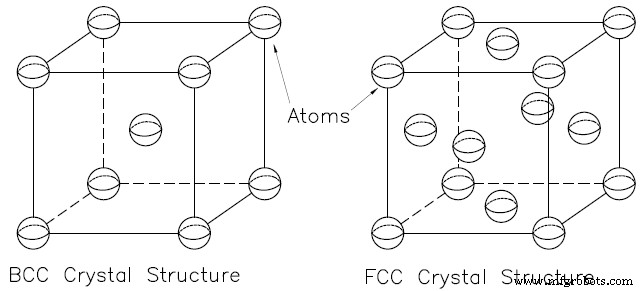
Следующий уровень классификации – фаза. Этап однородная часть материала, обладающая одинаковыми физическими и химическими свойствами. Сталь имеет 3 различных фазы:
- Аустенит:гранецентрированное кубическое железо; также сплавы железа и стали с кристаллической структурой ГЦК.
- Феррит:объемно-центрированные кубические сплавы железа и стали с кристаллической структурой ОЦК.
- Цементит:карбид железа (Fe3 В)
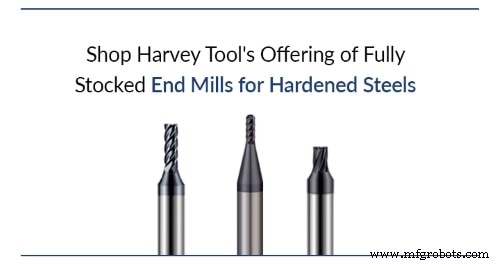
Последним уровнем классификации, обсуждаемым в этой статье, является микроструктура. Три фазы, показанные выше, могут быть объединены для формирования различных микроструктур стали. Примеры этих микроструктур и их общие механические свойства показаны ниже:
- Мартенсит:самая твердая и прочная микроструктура, но и самая хрупкая.
- Перлит:твердый, прочный и пластичный, но не особенно прочный.
- Бейнит:имеет желательное сочетание прочности и пластичности, тверже перлита, но не так твердо, как мартенсит.
Упрочнение в микроскопическом масштабе:
Прокаливаемость стали зависит от содержания углерода в материале, других легирующих элементов и размера зерна аустенита. Аустенит представляет собой гамма-фазное железо, и при высоких температурах его атомная структура претерпевает переход от ОЦК-конфигурации к ГЦК-конфигурации.
Высокая прокаливаемость относится к способности сплава производить высокий процент мартенсита по всей массе материала при закалке. Закаленные стали создаются путем быстрой закалки материала от высокой температуры. Это включает в себя быстрый переход от состояния 100% аустенита к высокому проценту мартенсита. Если сталь содержит более 0,15 % углерода, мартенсит принимает сильно напряженную объемно-центрированную кубическую форму и становится пересыщенным углеродом. Углерод эффективно закрывает большинство плоскостей скольжения внутри микроструктуры, создавая очень твердый и хрупкий материал. Если скорость закалки недостаточно высока, углерод будет диффундировать из аустенитной фазы. Затем сталь становится перлитом, бейнитом или, если ее достаточно долго держать в горячем состоянии, ферритом. Ни одна из только что указанных микроструктур не имеет такой же прочности, как мартенсит после отпуска, и обычно считается неблагоприятной для большинства применений.
Успешная термообработка стали зависит от трех факторов:
- Размер и форма образца
- Состав стали
- Способ тушения
1. Размер и форма образца
В процессе закалки тепло должно быть передано поверхности образца, прежде чем оно сможет рассеяться в закалочной среде. Следовательно, скорость охлаждения внутренней части образца зависит от отношения площади его поверхности к объему. Чем больше это отношение, тем быстрее будет охлаждаться образец и, следовательно, тем глубже будет эффект упрочнения. Например, 3-дюймовый цилиндрический стержень диаметром 1 дюйм будет иметь более высокую прокаливаемость, чем 3-дюймовый стержень диаметром 1,5 дюйма. Из-за этого эффекта детали с большим количеством углов и кромок лучше поддаются закалке, чем детали правильной и закругленной формы. На рис. 2 представлена примерная диаграмма трансформации время-температура (ТТТ) кривых охлаждения закаленного в масле стержня диаметром 95 мм. Поверхность превратится в 100% мартенсит, в то время как сердцевина будет содержать некоторое количество бейнита и, следовательно, будет иметь более низкую твердость.
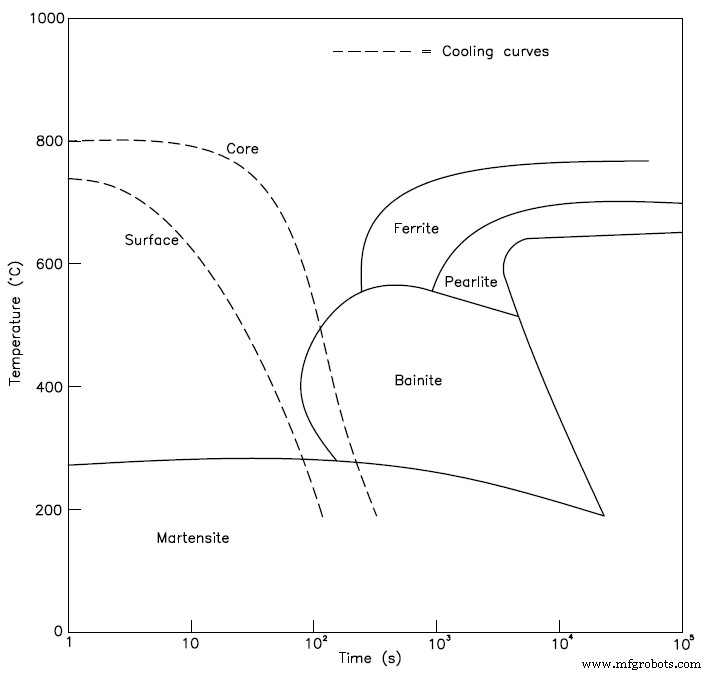
2. Состав стали
Важно помнить, что разные сплавы стали имеют разный химический состав. Отношение этих элементов к количеству железа в стали дает широкий спектр механических свойств. Увеличение содержания углерода делает сталь более твердой и прочной, но менее пластичной. Преобладающим легирующим элементом нержавеющих сталей является хром, который придает металлу высокую устойчивость к коррозии. Поскольку люди уже более тысячи лет изучают состав стали, количество комбинаций бесконечно.
Поскольку существует так много комбинаций, которые дают так много различных механических свойств, стандартные тесты используются, чтобы помочь классифицировать различные типы стали. Распространенным тестом на прокаливаемость является тест Джомини, показанный на рисунке 3 ниже. Во время этого испытания стандартный блок материала нагревают до тех пор, пока он не станет 100% аустенитным. Затем блок быстро перемещают в аппарат, где он охлаждается водой. Поверхность или область, соприкасающаяся с водой, немедленно охлаждается, и скорость охлаждения падает в зависимости от расстояния до поверхности. Затем на блок по длине образца натачивают плоскую поверхность. Вдоль этой плоскости измеряется твердость в различных точках. Затем эти данные наносятся на диаграмму прокаливаемости с твердостью по оси Y и расстоянием по оси X.
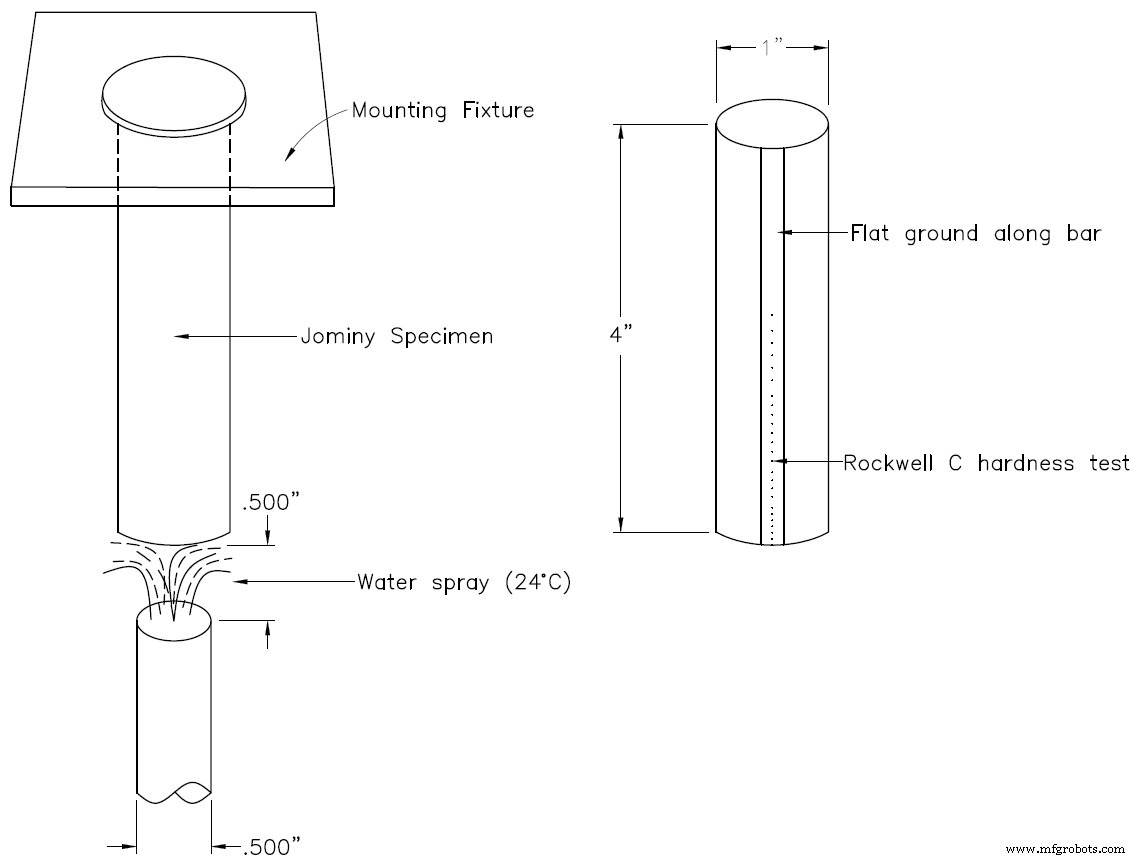
Кривые прокаливаемости построены по результатам испытаний Джомини. Примеры нескольких кривых сплава стали показаны на рис. 4. При уменьшении скорости охлаждения (более резкое падение твердости на коротком расстоянии) остается больше времени для диффузии углерода и образования большей доли более мягкого перлита. Это означает меньшее количество мартенсита и более низкую прокаливаемость. Материал, который сохраняет более высокие значения твердости на относительно больших расстояниях, считается хорошо упрочняемым. Кроме того, чем больше разница в твердости между двумя концами, тем ниже прокаливаемость. Для кривых прокаливаемости характерно, что по мере удаления от закаленного конца скорость охлаждения уменьшается. Сталь 1040 изначально имеет такую же твердость, как и 4140, и 4340, но очень быстро остывает по длине образца. Стали 4140 и 4340 остывают более постепенно и, следовательно, имеют более высокую прокаливаемость. 4340 имеет менее экстремальную степень охлаждения по сравнению с 4140 и, таким образом, имеет самую высокую прокаливаемость из трех.
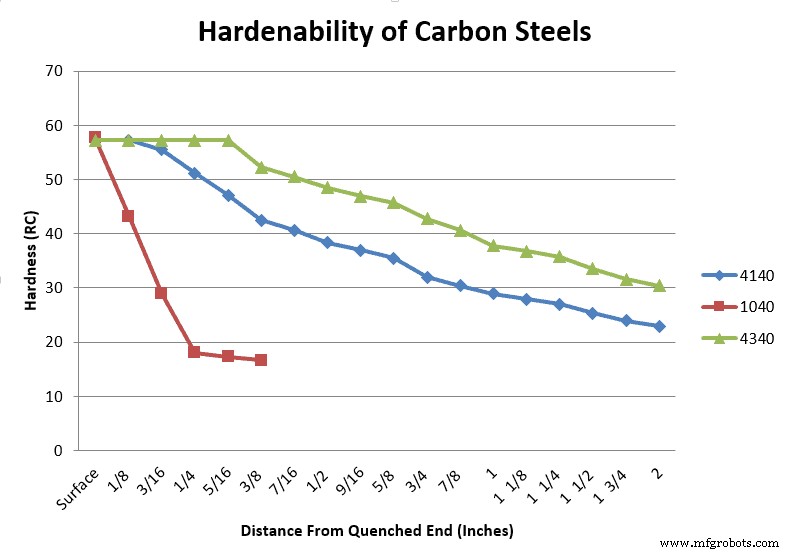
Кривые прокаливаемости зависят от содержания углерода. Более высокий процент углерода, присутствующего в стали, увеличивает ее твердость. Следует отметить, что все три сплава на рис. 4 содержат одинаковое количество углерода (0,40% С). Углерод — не единственный легирующий элемент, который может влиять на прокаливаемость. Различия в характеристиках прокаливаемости этих трех сталей можно объяснить с точки зрения их легирующих элементов. В таблице 1 ниже показано сравнение содержания легирующих элементов в каждой из сталей. 1040 представляет собой простую углеродистую сталь и, следовательно, имеет самую низкую прокаливаемость, поскольку в ней нет других элементов, кроме железа, которые блокируют выход атомов углерода из матрицы. Никель, добавленный в 4340, позволяет формировать немного большее количество мартенсита по сравнению с 4140, что придает ему самую высокую прокаливаемость из этих трех сплавов. Большинство металлических легирующих элементов замедляют образование перлита, феррита и бейнита, поэтому повышают прокаливаемость стали.
Таблица 1:показано содержание легирующих элементов в стали 4340, 4140 и 1040
Тип стали: | Никель (вес. %): | Молибден (вес. %): | Хром (мас.%): |
4340 | <тд>1,85%тд> <тд>0,25%тд> <тд>0,80%тд>|||
4140 | 0,00% | <тд>0,20%тд> <тд>1,00%тд>||
1040 | 0,00% | 0,00% | 0,00% |
В пределах одной группы материалов могут быть различия в прокаливаемости. При промышленном производстве стали всегда имеют место незначительные неизбежные колебания элементного состава и средней зернистости от одной партии к другой. В большинстве случаев прокаливаемость материала представлена максимальной и минимальной кривыми, установленными в качестве пределов.
Прокаливаемость также увеличивается с увеличением размера аустенитного зерна. Зерно – это отдельный кристалл в поликристаллическом металле. Подумайте о витражном окне (таком, как показано ниже), цветное стекло будет зернами, а припой, удерживающий его, будет границами зерен. Аустенит, феррит и цементит — это разные типы зерен, которые составляют разные микроструктуры стали. Именно на границах зерен образуются перлит и бейнит. Это вредно для процесса закалки, поскольку желаемой микроструктурой является мартенсит, а другие типы мешают его росту. Мартенсит образуется при быстром охлаждении аустенитных зерен, и процесс его превращения еще недостаточно изучен. С увеличением размера зерна становится больше аустенитных зерен и меньше границ зерен. Следовательно, меньше возможностей для образования микроструктур, таких как перлит и бейнит, и больше возможностей для образования мартенсита.
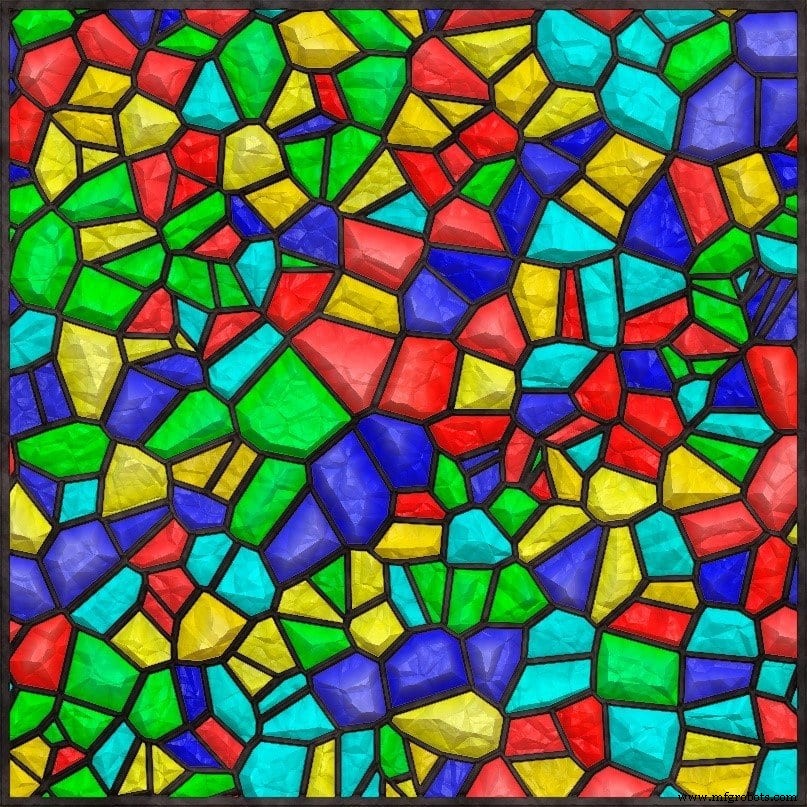
3. Способ закалки
Как указывалось ранее, тип закалки влияет на скорость охлаждения. Использование масла, воды, водных полимерных закалочных средств или воздуха приведет к различной твердости внутри заготовки. Это также сдвигает кривые прокаливаемости. Наиболее жесткая закалка производится водой, за ней следует масло, а затем воздух. Водные полимерные реагенты обеспечивают скорость охлаждения между водой и маслом и могут быть адаптированы к конкретным применениям путем изменения концентрации и температуры полимера. Степень перемешивания также влияет на скорость отвода тепла. Чем быстрее закалочная среда перемещается по образцу, тем выше эффективность закалки. Закалка в масле обычно используется, когда закалка в воде может быть слишком жесткой для определенного типа стали, поскольку она может растрескиваться или деформироваться при обработке.
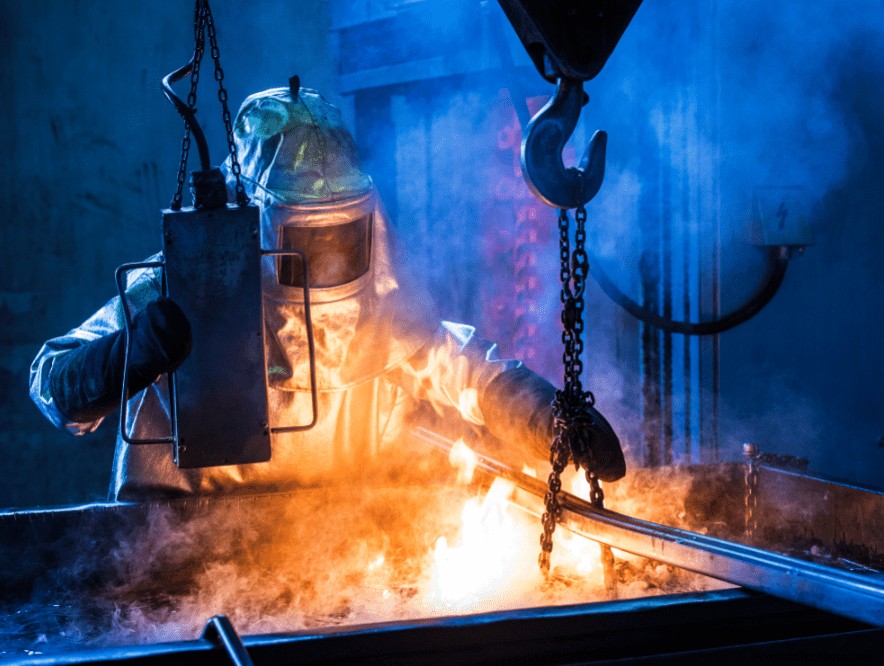
Обработка закаленных сталей
Тип фрезы, которая должна быть выбрана для обработки инструментов, выбранных для обработки заготовки после закалки, зависит от нескольких различных переменных. Не считая геометрических требований, характерных для применения, двумя наиболее важными переменными являются твердость материала и его прокаливаемость. В некоторых приложениях с относительно высокими напряжениями требуется, чтобы внутри заготовки было произведено не менее 80% мартенсита. Обычно для деталей с умеренным напряжением требуется только около 50% мартенсита по всей заготовке. При обработке закаленного металла с очень низкой прокаливаемостью цельный твердосплавный инструмент со стандартным покрытием может работать без проблем. Это связано с тем, что самая твердая часть заготовки ограничена ее поверхностью. При обработке стали с высокой прокаливаемостью рекомендуется использовать фрезу со специальной геометрией, предназначенной для конкретного применения. Высокая прокаливаемость приводит к тому, что заготовка становится твердой по всему объему. В каталоге Harvey Tool представлен ряд различных фрез для закаленной стали, в том числе сверла, концевые фрезы, фрезы для шпоночных пазов и граверы.
Покупка полностью укомплектованных концевых фрез Harvey Tool для обработки закаленных сталей
Закаленная сталь, сводка
Прокаливаемость – это мера глубины, на которую может быть упрочнен сплав железа путем образования мартенсита по всему его объему, от поверхности до сердцевины. Это важное свойство материала, которое необходимо учитывать при выборе стали, а также режущих инструментов для конкретного применения. Закалка любой стали зависит от размера и формы детали, молекулярного состава стали и типа используемого метода закалки.
Станок с ЧПУ