Достижение лучших результатов аддитивного производства в генеративном дизайне
Читать эту статью на немецком языке:Deutsch (немецкий)
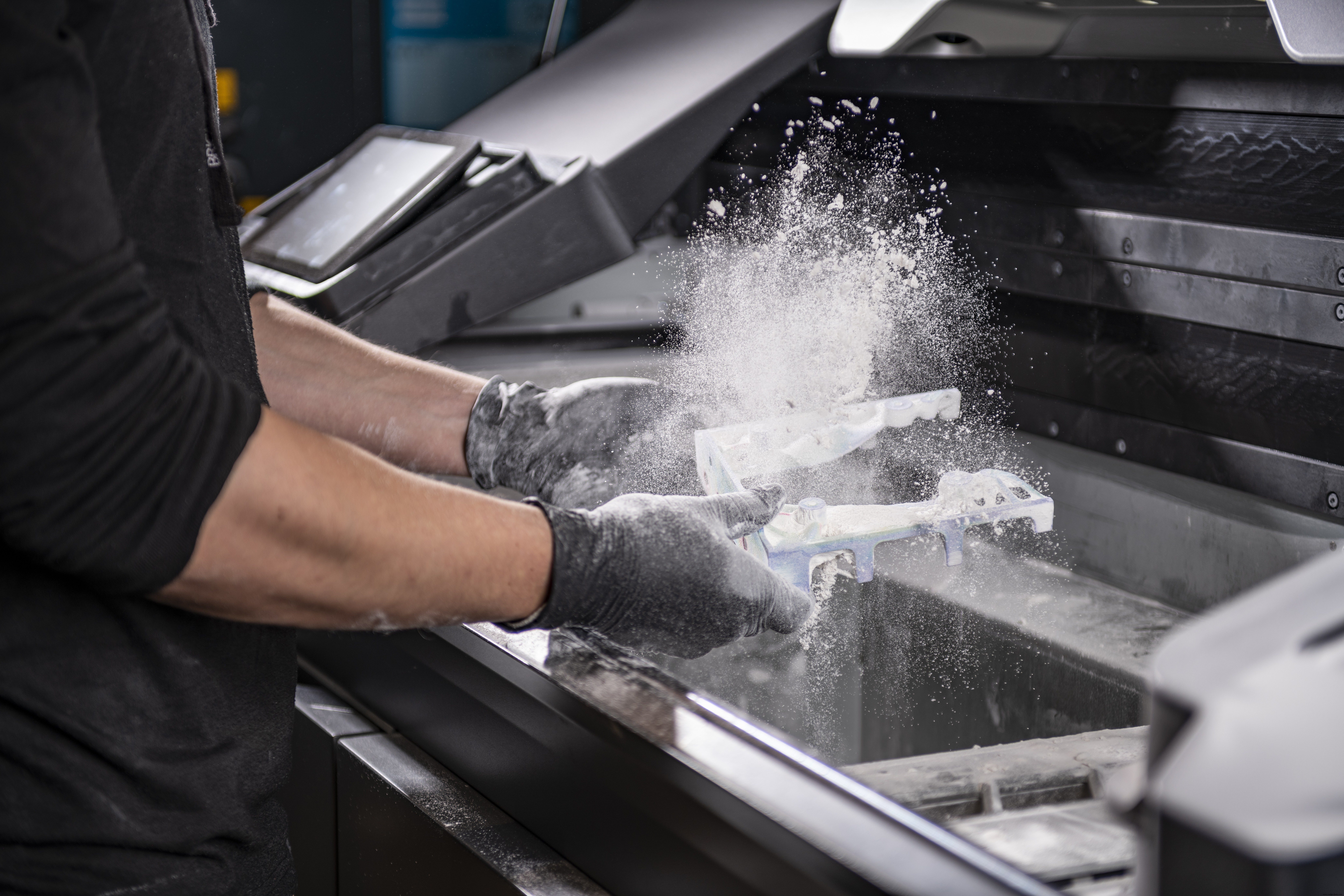
В рамках обновления Fusion 360 за декабрь 2020 г. мы доставили скрытый подарок как раз к праздникам:новый метод получения результатов аддитивного производства. Внутри мы называем этот проект Additive 2.0, и он является частью нашего предварительного просмотра экспериментальных генеративных решателей и функций. Этот новый метод должен иметь большое значение для улучшения качества формы и возможности печати результатов по сравнению с тем, что вы видели ранее в генеративном дизайне. Я знаю, что многие из нас с нетерпением ждали этого подарка, и я и моя команда хотели бы «развернуть» все, что мы доставили.
Использование нового алгоритма Additive 2.0
Во-первых, вы должны включить предварительный просмотр экспериментальных генеративных решателей и функций в настройках пользователя.
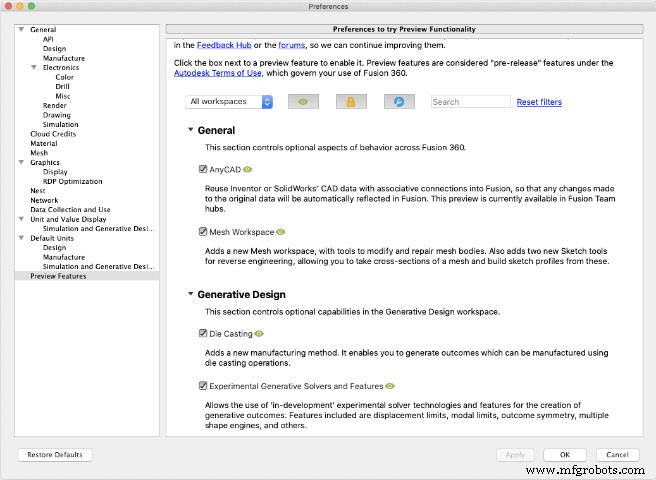
При включенном предварительном просмотре вам необходимо включить альтернативные результаты в настройках исследования. Оттуда просто настройте свое исследование, как обычно. Включите ограничение аддитивного производства в диалоговом окне «Производственные ограничения», выберите желаемую ориентацию печати, а об остальном позаботятся наши решатели.
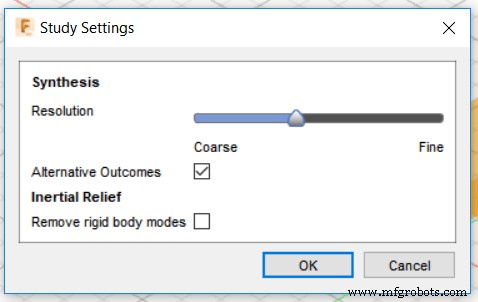
В режиме исследования для каждого набора аддитивных результатов (где набор соответствует заданному материалу и направлению) Additive 2.0 будет генерировать второй результат в каждом наборе. Совет:самый простой способ убедиться в этом — переключиться на представление свойств, выделить метод аддитивного производства и выбрать в раскрывающемся списке "Сортировать по" значение "Материал".
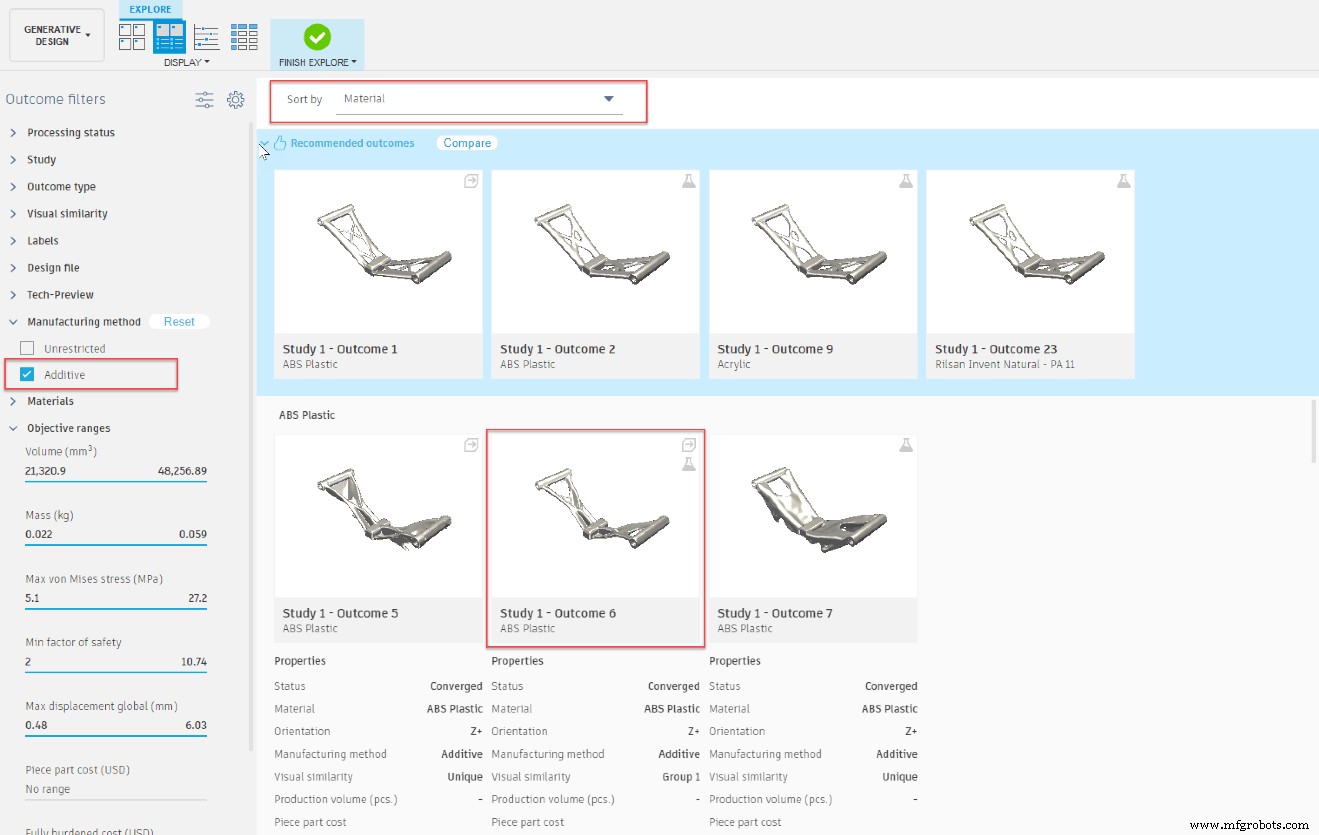
Чем Additive 2.0 лучше?
Наш первоначальный подход к созданию аддитивных результатов оставлял желать лучшего в отношении качества формы во многих сценариях (многие из вас говорили нам об этом, и мы прислушались!). Было обычным делом видеть результаты с ярко выраженными ступеньками и другими артефактами, когда мы пытались выполнить требования по нависанию и быть полностью самодостаточными. Благодаря нашему новому подходу наши решатели гораздо лучше справляются с выполнением требований по минимальной толщине, уравновешивают расчетную массу и минимизируют вспомогательный материал. Этот новый подход не принесет в жертву качество формы ради полной самоокупаемости.
Давайте рассмотрим пару примеров, демонстрирующих, как эти улучшения влияют на результаты, которые мы создаем.
Наш первый пример — это простая генеративная установка, показанная ниже (нагрузки и ограничения скрыты). Мы намерены изготовить эту деталь в ориентации, показанной на рис. 1 (ниже), заменив красное препятствие рабочей пластиной.
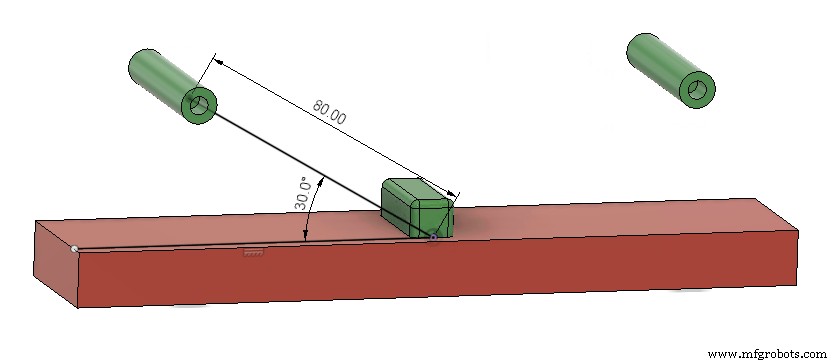
Эта установка дает неограниченный результат, как показано на Рисунке 2 (ниже), который трудно воспроизвести по разным причинам. Во-первых, большая площадь под геометрией детали требует опорных конструкций (выделенные красным цветом области во второй половине рисунка). Кроме того, тонкие элементы вблизи центра детали хрупкие и могут сломаться при удалении опоры. Хотя эту конструкцию можно изготовить с помощью аддитивных технологий, она далека от оптимизации.
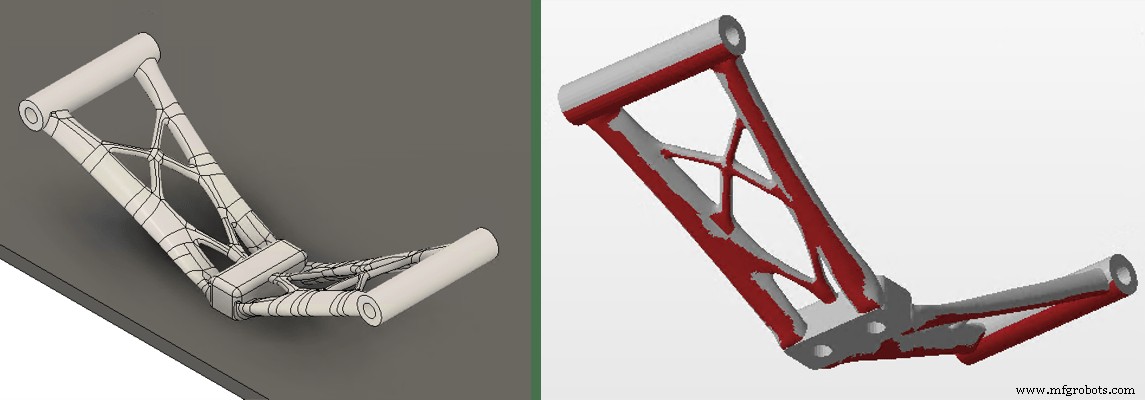
Когда мы начинаем рассматривать Additive 2.0 рядом с нашими существующими аддитивными ограничениями (Additive 1.0), различия становятся очевидными, как показано на рисунке 3 (ниже). В обоих случаях мы настроили дополнительное ограничение с углом выступа 45 градусов и минимальной толщиной 3 мм.
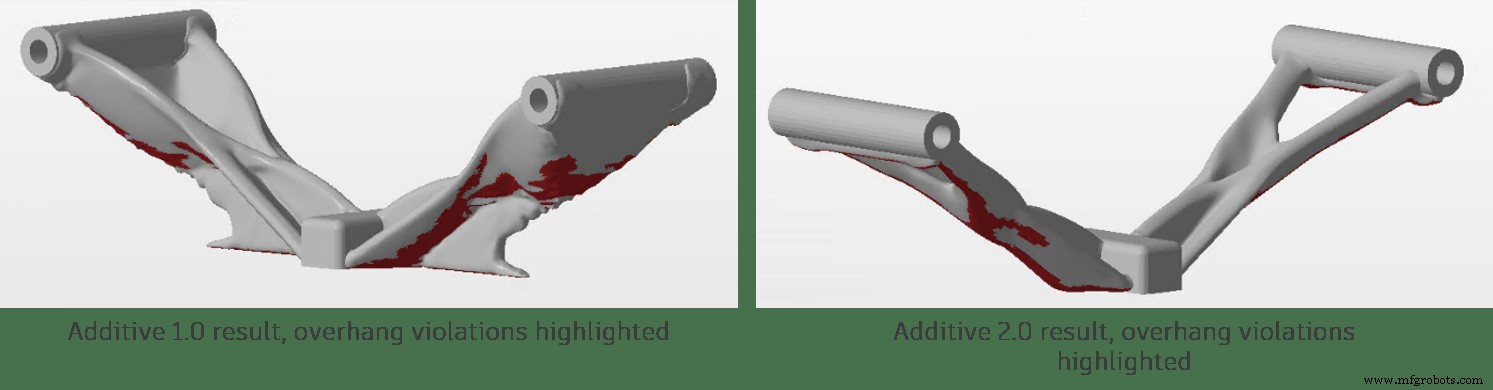
В обоих случаях количество требуемого вспомогательного материала уменьшается, но не устраняется. Однако результат Additive 1.0, который строит материал из рабочей пластины для поддержки всей конструкции, на 50% тяжелее, чем результат без ограничений. Он демонстрирует артефакты ступенчатости, которые обычно раздражали оригинальное решение для аддитивного производства. Additive 2.0 также значительно уменьшает количество требуемого вспомогательного материала, но делает это с более тонкими изменениями геометрии и увеличивает массу этой модели только на 11%. Оба аддитивных дизайна соответствуют минимальному размеру элемента 3 мм, но Additive 2.0 сохраняет структуру, гораздо более близкую к неограниченной, объединяя слишком тонкие решетчатые балки в более толстую органическую структуру. Новые результаты Additive 2.0 также устраняют большую часть плохого качества поверхности в исходном результате.
Теоретически новые ограничения Additive 2.0 уменьшат поддерживаемую площадь и устранят тонкие балки с минимальным увеличением общей массы детали. Но действительно ли эти конструкции более технологичны? Давайте пройдемся по процессу подготовки к печати и посмотрим.
Проверка процесса печати
Пример FFF
Рисунок 4 (ниже) сравнивает результаты для Additive 1.0 и Additive 2.0 с исходным неограниченным результатом. Каждый из этих результатов был пройден через общий рабочий процесс FFF с использованием дополнительного рабочего пространства Fusion 360. Модели были нарезаны и обработаны с помощью Fusion 360 перед печатью на настольном FFF-принтере. Каждая деталь подвергалась постобработке с использованием одних и тех же настроек печати, машины и одной и той же нити PLA. Результаты, показанные на рис. 3, ясно показывают улучшение между добавкой 2.0 и 1.0 со значительным снижением массы детали на 41,3%. Преимущество Additive 2.0 по сравнению с использованием неограниченных ограничений также подчеркивается сокращением требуемого вспомогательного материала на 47,8%.
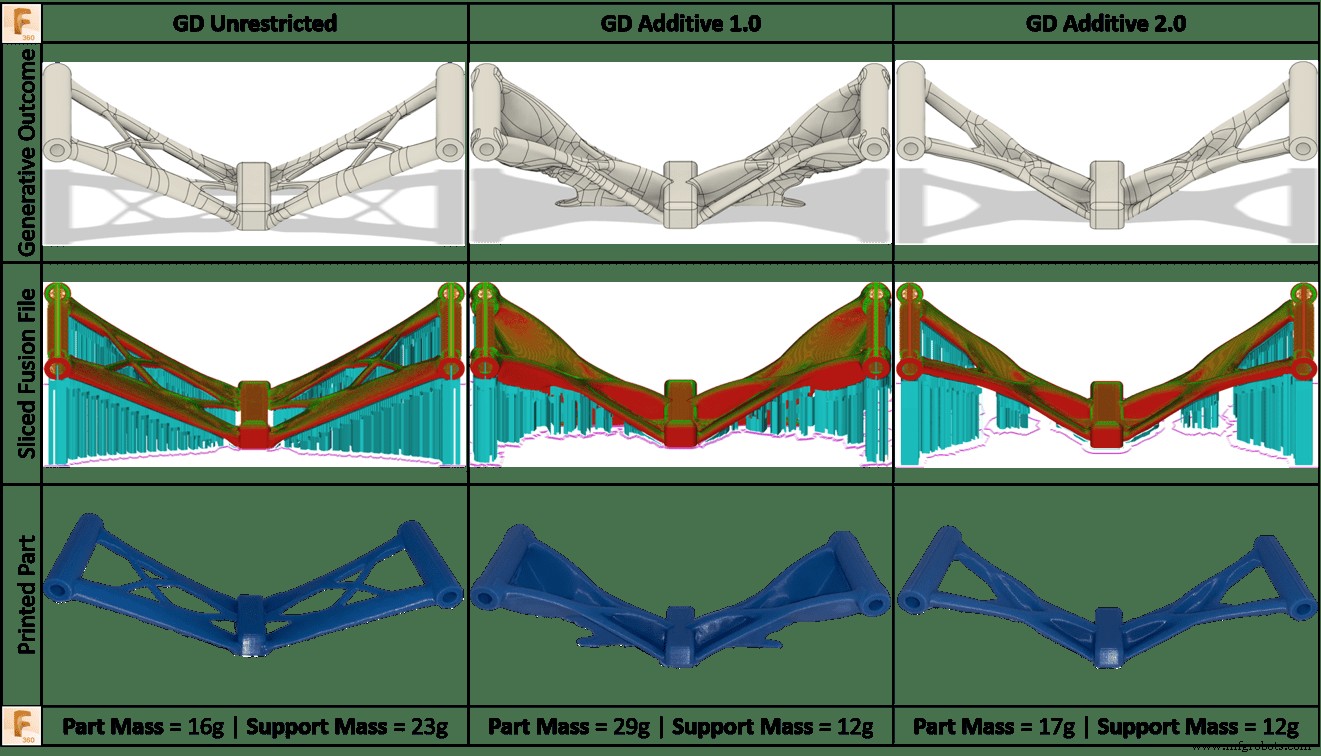
Пример SLA
На рис. 5 (ниже) результаты для Additive 1.0 и Additive 2.0 сравниваются с исходным неограниченным результатом, подготовленным для печати в процессе SLA. Каждый из этих результатов был получен через общий рабочий процесс SLA с использованием Netfabb. Подобно приведенным выше результатам, на рис. 5 четко показано улучшение по сравнению с добавкой 1.0 до 2.0. Этот процесс также требовался как для массы детали, так и для вспомогательного материала.
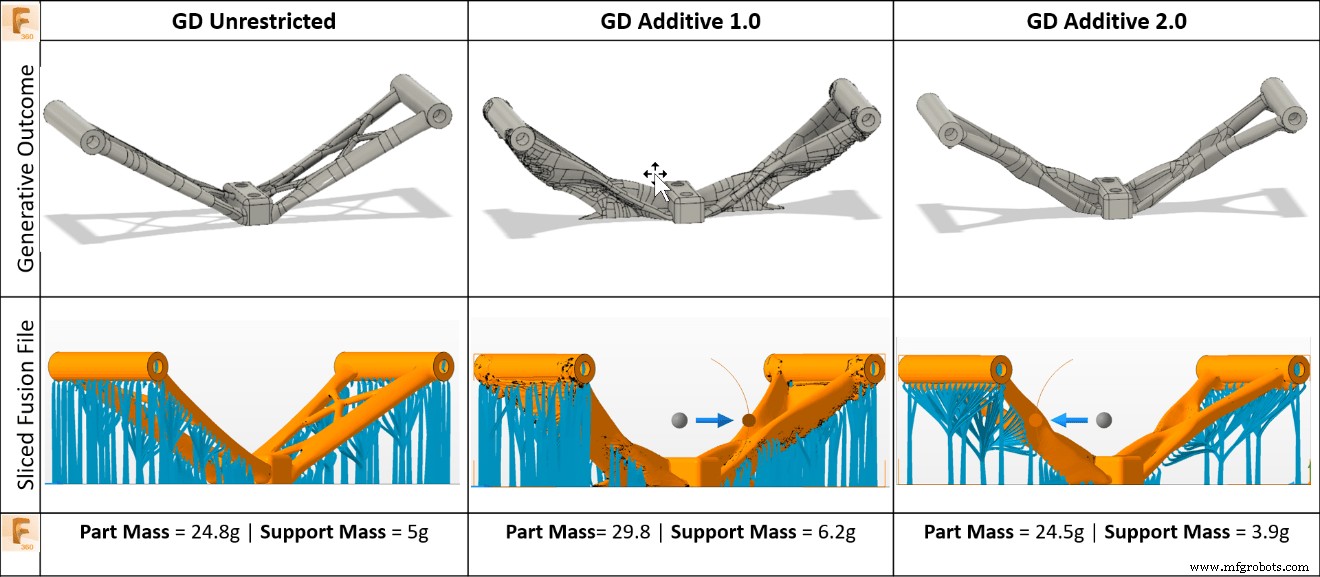
Пример УУЗР
Давайте рассмотрим другой, более реальный пример. Пример задачи «Тройной зажим мотоцикла» в учебных материалах по генеративному проектированию описывает проектирование конструктивного компонента, соединяющего трубы вилки с рулевым стержнем мотоцикла. В этом примере мы хотим аддитивно изготовить компонент из алюминия с помощью селективного лазерного плавления (SLM).
Перед запуском генеративного исследования мы выбрали направление сборки компонента. Высота сборки является основным источником затрат, поэтому мы избегали направления +X. Мы знаем по опыту, что нам нужно будет заполнить большинство больших отверстий материалом во время печати, а затем после обработки, чтобы получить нужный нам допуск. Как только отверстия заполнены, ориентация +Y будет иметь быстрое изменение площади поперечного сечения на верхней грани детали, что вызывает быстрое охлаждение большой поверхности и может вызвать проблемы со сборкой. В результате мы отказались от ориентации +Y и остановились на направлении построения +Z.
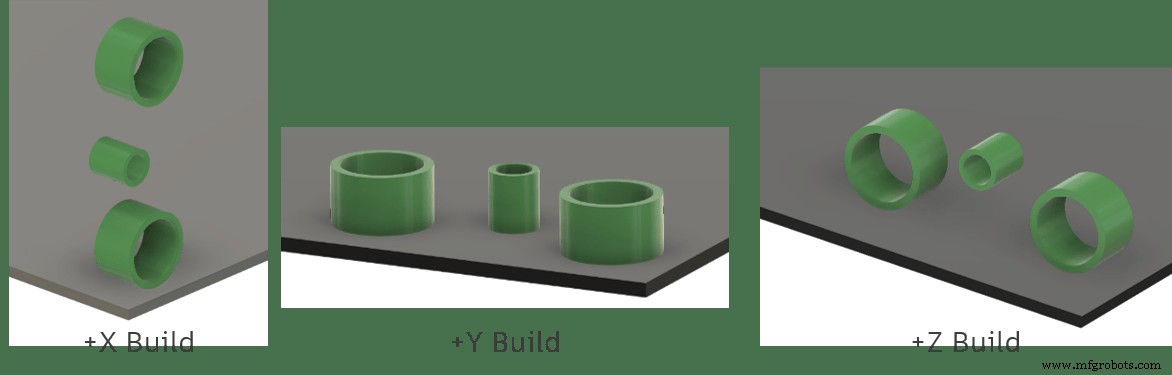
Мы выбрали минимальный размер элемента 0,25 дюйма (6,35 мм), чтобы гарантировать, что любые произведенные балки будут достаточно большими, чтобы противостоять силам, возникающим при удалении опоры. Угол выступа был установлен на 45°, что соответствует параметрам процесса SLM. Результат Additive 2.0 показан на изображении ниже.
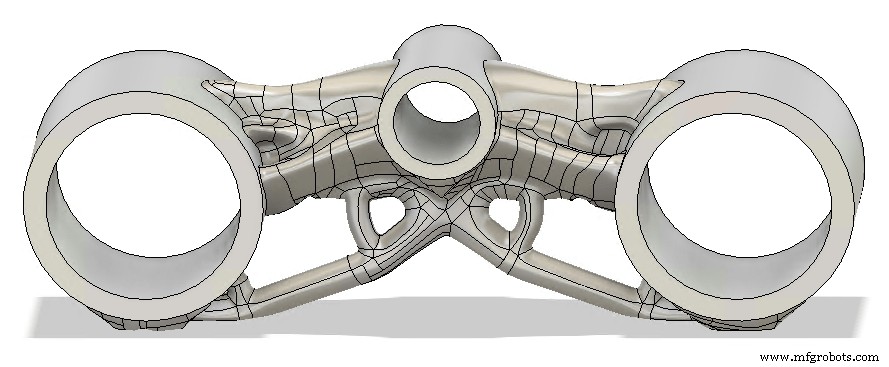
Обычно на этом этапе мы, скорее всего, вносим изменения в органическую форму и проверяем эффективность дизайна. На сегодня мы пропустим эти шаги и сразу перейдем к производственному рабочему пространству, чтобы подготовить его к печати.
Мы будем использовать Renishaw AM250 для изготовления конструкции, для которой требуется расширение Additive Build Fusion. Во-первых, нам нужно заполнить большие отверстия материалом, чтобы позже мы могли обработать их до допуска. Мы сделаем это в рабочей области «Производство», создав производственную модель, в которой мы нажимаем/тянем отверстия, чтобы они были меньшего диаметра.
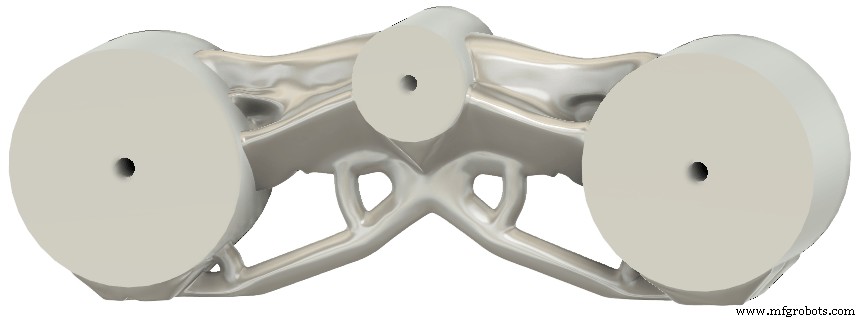
Теперь мы создадим новую настройку, выбрав станок Renishaw и нашу измененную геометрию. После небольшой работы с командой Move наша деталь позиционируется на платформе сборки.
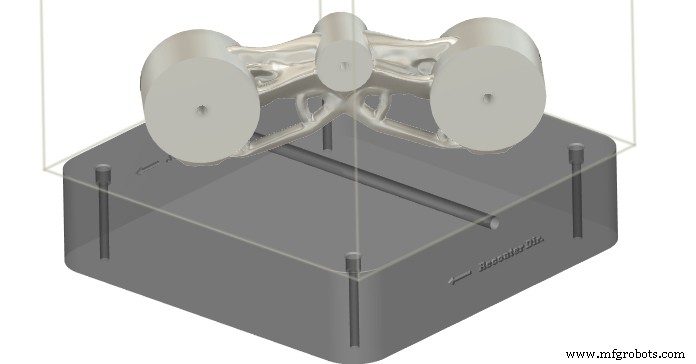
Теперь мы будем использовать команду Volume Support для создания вспомогательного материала.
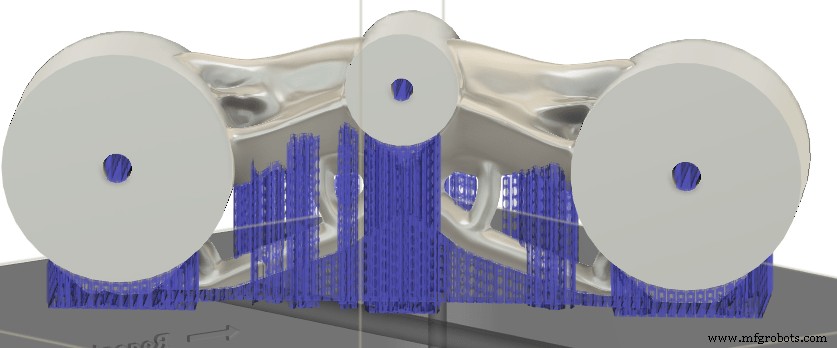
На данный момент мы готовы смоделировать печать, затем сгенерировать g-код и отправить его на машину.
Рисунок 7 (ниже) сравнивает конструкцию Additive 2.0 с неограниченными и существующими решениями для аддитивного производства, и мы видим ту же тенденцию, что и в предыдущем примере. Результаты Additive 1.0 тяжелее, требуют такой же поддержки, как и неограниченная часть, и имеют проблемы с качеством поверхности. Additive 2.0 улучшает качество формы, снижает потребность в вспомогательном материале и возвращает массу детали почти к одинаковому результату без ограничений.
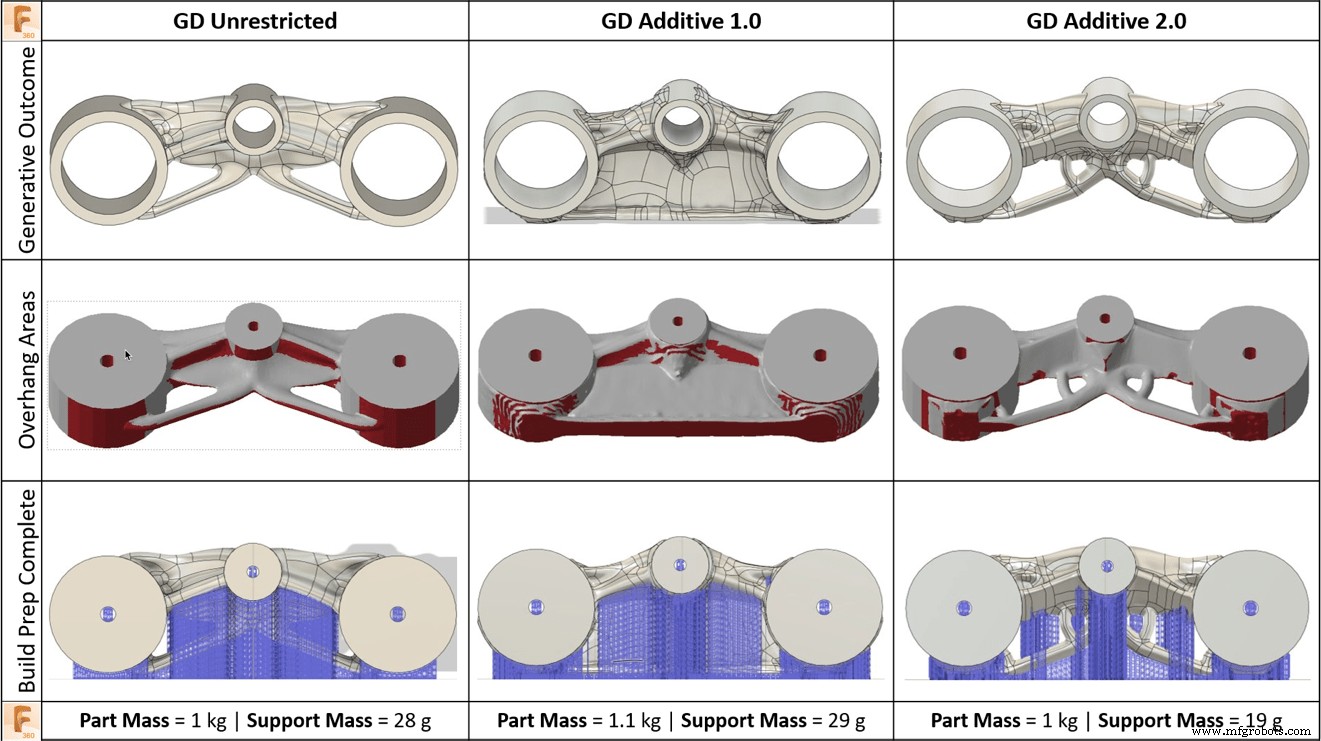
Попробуйте Additive 2.0 сами
Мы надеемся, что вы так же взволнованы этими улучшениями в аддитивном производстве, как и мы, чтобы внедрить их в продукт. Хотя изображения в этом блоге рассказывают замечательную историю, мы хотели предоставить вам модели, которые мы использовали для демонстрации улучшений, чтобы вы могли посмотреть сами. Эти модели готовы к запуску, откройте их и сгенерируйте доступные исследования.
Аддитивная установка натяжного стержня 2,0 В
Установка тройного зажима Additive 2.0 для мотоциклов
Если у вас есть какие-либо вопросы или комментарии о наших новых ограничениях аддитивного производства, свяжитесь с нами по адресу [email protected]. Кроме того, я хочу выразить большую благодарность замечательной команде экспертов, которые разрабатывали и проверяли это решение, а также Бену Вайсу, Адаму Дэю, Мэтту Остуйзену и Диви Кишору Тивари за помощь в написании этого сообщения в блоге. Желаю всем счастливого праздничного сезона и счастливого Нового года!

Промышленные технологии
- Аддитивное производство против субтрактивного производства
- Преимущества аддитивного производства
- 4 Перспективные тенденции автоматизации в аддитивном производстве
- Обзор рабочих процессов аддитивного производства
- Генеративный дизайн и 3D-печать:производство завтрашнего дня
- Дизайн для производства печатных плат
- Все вместе с добавками
- Аддитивное производство в электронике
- Как в полной мере использовать САПР в процессе аддитивного производства
- Аддитивное производство в аэрокосмической отрасли