5 способов, которыми 3D-печать дополняет традиционное производство
Предполагается, что 3D-печать заменит традиционные производственные технологии. Однако реальная сила технологии может заключаться не в конкуренции с традиционными методами производства, а в их дополнении и расширении.
Чтобы подтвердить это утверждение, ниже мы исследуем 5 ключевых способов поддержки традиционного производства с помощью 3D-печати.
1. 3D-печать более эффективных форм для литья под давлением
Литье под давлением включает в себя процесс плавления и впрыскивания пластика в специальный инструмент для формования, имеющий форму желаемого объекта. Когда пластик затвердевает, он принимает форму полости формы. Литье под давлением - лучший способ массового производства высокоточных и сложных изделий и деталей.
Однако у этого процесса есть свои проблемы. Например, детали, полученные литьем под давлением, охлаждаются с помощью строительных каналов - по сути, проходов, расположенных близко к поверхности формы - через формы. Эти каналы обычно являются прямыми линиями, что иногда может приводить к неравномерному охлаждению, увеличивая риск деформации детали.
Эффективное охлаждение достигается с помощью конформных охлаждающих каналов, которые повторяют форму детали. Однако эти типы каналов трудно изготовить с использованием обычных методов, что делает 3D-печать привлекательной альтернативой для создания литьевых форм.
Создание форм с конформными каналами охлаждения не только помогает повысить качество отформованных деталей, но и помогает значительно сократить время охлаждения.
3D-печать помогает оптимизировать линию литья под давлением
В качестве примера можно привести компанию Alfred Kärcher GmbH &Co. KG, которая ежегодно продает миллионы своих моечных машин высокого давления K2 по всему миру. Пытаясь удовлетворить такой спрос, компания столкнулась с узким местом в производстве, в результате чего им потребовалось увеличить производство кожухов шайб.
Вместо того, чтобы покупать больше машин для литья под давлением, Kärcher начал искать способы повышения производительности существующих машин. Компания нашла решение в 3D-печати металлом.
Компания Kärcher обратилась в LBC Engineering, часть Renishaw GmbH, которая обнаружила, что на продолжительность цикла формования влияет неэффективность процесса охлаждения. В формах для обсадных труб использовались традиционные системы охлаждения, просверленные по прямым линиям, создавая горячие точки, которые увеличивали время цикла.
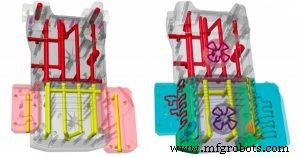
Компания LBC Engineering изменила конструкцию пресс-формы, создав два сердечника, напечатанных на 3D-принтере, чтобы обеспечить конформное охлаждение в выявленных горячих точках.
Напечатанные на 3D-принтере конформные каналы охлаждения помогли снизить температуру стенок в формах со 100 ° C до 70 ° C, сократив время охлаждения с 22 до 10 секунд, то есть на 55%.
Вместе с некоторыми настройками периферийных компонентов, таких как система подачи и транспортировки материала, время цикла для оболочек сократилось с 52 до 37 секунд. 3D-печать обеспечила львиную долю этого сокращения, что позволило Kärcher повысить производительность своей линии и достичь целей по производству обсадных труб.
В другом примере специалист по литью под давлением Пэт Заффино разработал технологию многослойного роботизированного осаждения, которая позволяет печатать конформные каналы охлаждения на поверхности форм для литья под давлением в 3D.
Ранее в этом году Заффино основал новую компанию Conformal Cooling Solutions Inc. (CCS), чтобы продвигать преимущества использования конформных каналов охлаждения.
«Создание конформных каналов охлаждения. которые повторяют форму полости и сердечника, способствуют однородности температуры в формованных пластиковых материалах, и формовщики, использующие эту технологию, видят поразительные результаты:сокращение времени цикла, улучшение качества пластиковых деталей и, прежде всего, снижение затрат '', - сказал он. в интервью canplastics.com.
По мере того, как технология становится дешевле и проще в использовании, пресс-формы с конформными каналами охлаждения, напечатанными на 3D-принтере, в конечном итоге могут стать новым стандартом в отрасли.
2. Шаблоны для 3D-печати для литья по выплавляемым моделям
В литье по выплавляемым моделям используются одноразовые восковые модели и керамические корпуса для создания сложных и детальных дизайнов деталей. Традиционно эти выкройки изготавливаются методом литья под давлением. Однако стоимость форм для литья под давлением может достигать нескольких тысяч долларов, а сроки изготовления - от одной до четырех недель. Это делает процесс недоступным для людей, которые могут не иметь такого большого капитала или иметь короткие сроки поставки запчастей.
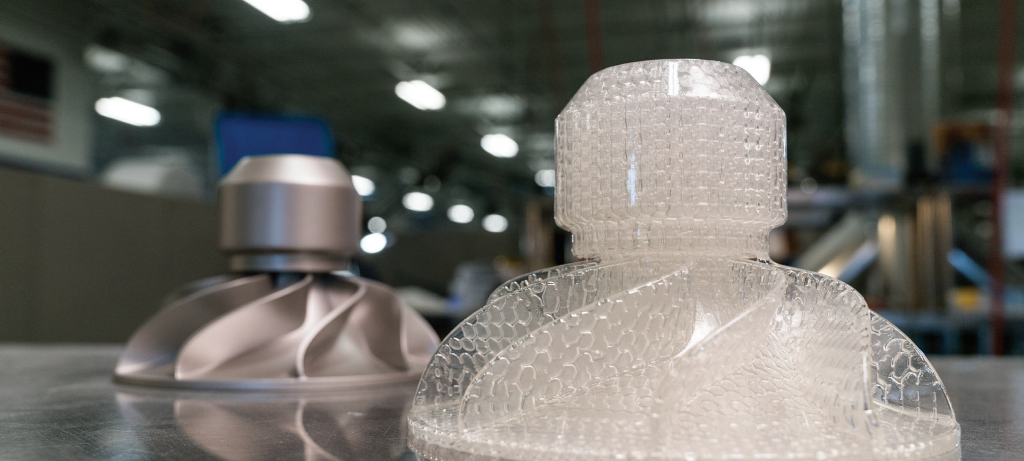
По этой причине компании могут выбирать для 3D-печати выкройки из материала, подходящего для литья по выплавляемым моделям. Многие производители 3D-принтеров разработали материалы для 3D-печати специально для литья, включая воск, литьевые смолы и некоторые термопласты на основе PLA и ABS.
Эти материалы обычно используются со стереолитографией (смолы) и FDM ( пластмассы), создавая высокоточные узоры с отличными характеристиками выгорания.
Еще одно преимущество этого подхода - относительно низкий риск, связанный с его использованием. Выкройки можно напечатать на 3D-принтере с помощью профессиональных настольных 3D-принтеров, которые стоят менее 5000 долларов, что составляет небольшую часть стоимости более дорогого промышленного оборудования для 3D-печати.
Сокращение сроков изготовления отливок с помощью 3D-печати
Модели литья по выплавляемым моделям, напечатанные на 3D-принтере, все чаще используются для создания индивидуальных ювелирных изделий с замысловатым дизайном и в более короткие сроки. Например, канадская ювелирная компания Vowsmith, специализирующаяся на изготовлении колец по индивидуальному заказу, смогла сократить время производства и доставки на 50% за счет интеграции восковых 3D-принтеров 3D Systems в свой рабочий процесс. За один принт компания произвела от 35 до 40 персонализированных выкроек колец, готовых к отливке.
Эта технология также все шире применяется в литейных цехах для создания сложных моделей для широкого спектра промышленных применений. Например, Invest Cast, Inc. недавно интегрировала новое цифровое решение для литья под давлением 3D Systems в свое производство моделей.
Возможность изготавливать готовые литые детали без использования пресс-формы дала клиентам Invest Cast свободу выбора. быстро и с минимальными затратами протестируйте несколько итераций, что в конечном итоге позволит получить более качественные конечные детали.
По словам Invest Cast, 3D-принтер ProJet MJP 2500 IC от 3D Systems значительно сократил время процесса литья по выплавляемым моделям . Эта технология позволяет компании переходить от модели к металлу за 2-5 дней, что ниже среднего времени выполнения заказа, составляющего примерно 6-12 недель с формами для литья по выплавляемым моделям.
3. Повышение производительности с помощью режущих инструментов, напечатанных на 3D-принтере
3D-печать может использоваться для создания режущих инструментов - небольших твердосплавных пластин, удаляющих материал с запрограммированной траектории.
Некоторые материалы с высокими эксплуатационными характеристиками, такие как сверхвысокопрочные стали, титан и никелевые сплавы, трудно поддаются обработке и могут привести к быстрому износу инструмента.
Инструменты для 3D-печати с нестандартной геометрией, со встроенными каналами охлаждения, которые могут эффективно отводить избыточное тепло, образующееся рядом с зоной резания во время обработки, могут увеличить срок службы инструмента и его производительность.
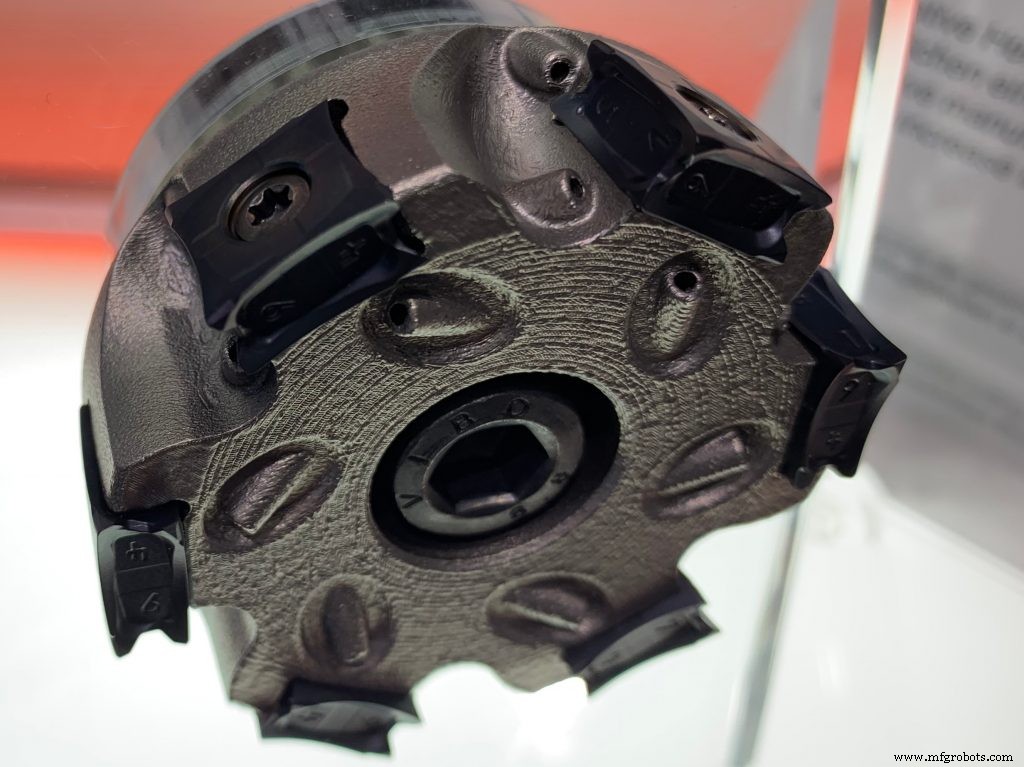
Специалист по инструментам, компания LMT Tools Inc., использовала эту технологию для создания внутренних каналов для охлаждающей жидкости в корпусе фрезерного инструмента, ранее имевших прямые отверстия. Свобода 3D-печати для создания изогнутых каналов позволяет фрезерному инструменту LMT подавать охлаждающую жидкость именно туда, где она необходима. LMT сообщает, что благодаря этому изменению конструкции испытательная резка показала увеличение срока службы инструмента при фрезеровании титана на 50 процентов.
Komet Group увеличивает производительность инструмента с помощью 3D-печати
Один из ведущих мировых поставщиков прецизионных режущих инструментов, Komet Group, также применяет 3D-печать металлом для производства инструментов.
Используя алюминиевый сплав и лазерную технологию от британского специалиста Renishaw, компания Komet смогла расширить режущие кромки инструмента и оптимизировать его геометрию для повышения производительности инструмента.
Например, инженеры оптимизировали каналы охлаждающей жидкости инструмента, чтобы обеспечить подачу охлаждающей жидкости на каждую режущую кромку через отдельный канал. Благодаря этим усовершенствованиям конструкции время обработки на единицу может быть сокращено до 50%.
AM также дает возможность снизить вес компонентов, поскольку материал можно использовать только там, где это необходимо для оптимальной функциональности компонента. Также сообщается, что он превосходит традиционные методы производства с точки зрения времени доставки для любых специальных или экспериментальных инструментов, необходимых клиентам Komet.
3D-печать более эффективной фрезерной головки
Кроме того, шведский производитель инструментальных систем Sandvik Coromant недавно представил новую фрезу с металлической головкой, напечатанной на 3D-принтере. Этот первый компонент для компании знаменует собой шаг в сторону участия компании в 3D-печати для конечного использования.
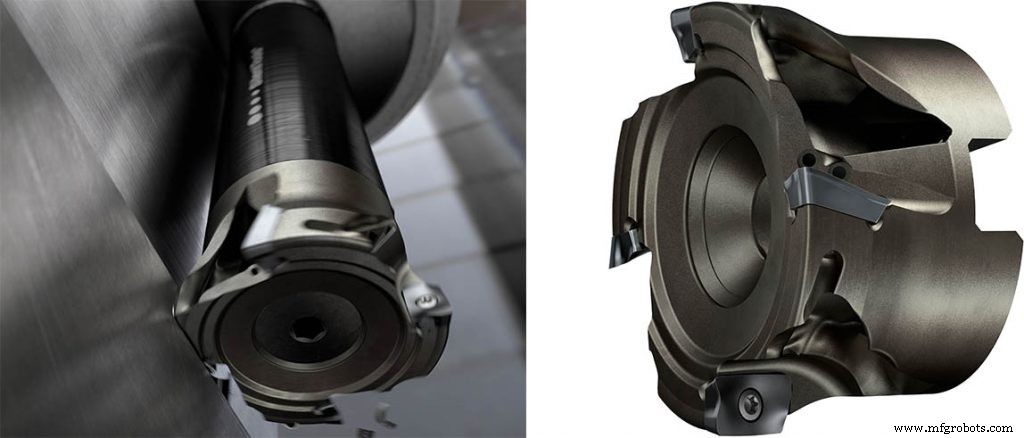
Новая легкая фреза CoroMill 390, производимая Sandvik Coromant, представляет собой фрезерную головку по металлу на основе конструкции CoroMill 390. Инструмент, изготовленный с использованием порошка Osprey из титанового сплава торговой марки Sandvik, был специально разработан для устранения проблем с вибрацией при фрезеровании металлов с большими вылетами.
Такие особенности являются обычным требованием для компонентов, используемых в аэрокосмической и нефтегазовой промышленности. Глубокие полости в детали, обработанной на станке с ЧПУ, могут быть повреждены вибрацией, что приводит к замедлению производства, сокращению срока службы инструмента и плохой чистоте поверхности. Компания сообщает, что при использовании в сочетании с фрезерными адаптерами Silent Tools, инструмент, напечатанный на 3D-принтере, может повысить производительность обработки на 50 процентов.
4. Ремонт изношенных и поврежденных инструментов
3D-печать можно использовать не только для создания новых инструментов и форм, но и для ремонта поврежденных инструментов. Компании в аэрокосмической отрасли, судостроении и производстве промышленных товаров начинают использовать процессы AM, такие как Direct Energy Deposition (DED), для восстановления компонентов до их первоначальной формы.
Также известная как лазерная наплавка, DED использует лазер для создания сварочной ванны на поверхности компонента. Затем материал добавляется в ванну расплава в виде порошка или проволоки. Расплавленные частицы сливаются и затвердевают, а соплом манипулируют, чтобы придать компоненту желаемую структуру.
Ранее в этом году консорциум из 7 британских компаний и организаций запустил проект DigiTool стоимостью 1,2 миллиона фунтов стерлингов. , чтобы обеспечить недорогой ремонт инструментов и штампов с использованием технологий AM.
С помощью 3D-печати компании, работающие в секторе инструментов и штампов, могут сократить расходы на замену штампов и ремонт с потенциалом для ускорения вверх процесс обслуживания. Это поможет компаниям сэкономить на затратах и материалах, одновременно улучшив свою устойчивость с меньшими потерями.
Более быстрый ремонт вставки пресс-формы
Немецкая компания по производству инструментов и форм HWF использовала 3D-печать для ремонта вставки формы. Одной из проблем, с которыми столкнулась компания HWF, было создание конструкции размером 300 x 20 x 20 мм из типичного материала пресс-формы.
В прошлом подобные конструкции строились с использованием ручной метод лазерной наплавки с подачей проволоки, чтобы избежать риска появления трещин, деформации и изменения металлургических свойств. Однако сварщику может потребоваться от 60 до 80 часов, чтобы выполнить задачу.
Сегодня HWF использует технологию DED от OR Laser, которая позволяет создавать такую же структуру путем нанесения слоев толщиной 250 мкм, производительностью 5000 мм³ в час. Таким образом, время производства может быть сокращено до 24 часов.
Благодаря этому процессу основной материал также подвергается гораздо меньшему воздействию, чем раньше, что значительно снижает риск появления трещин и подрезов материала, часто вызываемых обычными методами ремонта.
5. Повышение гибкости с помощью гибридных процессов
Объединение аддитивных и вычитающих возможностей в гибридной системе - еще один способ дополнить традиционное производство AM. В этом сценарии аддитивные и субтрактивные технологии могут открыть ряд возможностей для расширенного универсального производства.
Гибридное производство использует наиболее ценные возможности обеих технологий:геометрическую сложность AM и высокую точность субтрактивных методов. Это означает, что деталь может быть аддитивно создана и обработана за одну операцию, что ускоряет производственный процесс.
Сейчас на рынке доступно несколько коммерческих гибридных систем. Например, DMG MORI сочетает DED с пятиосевым ЧПУ в своей гибридной производственной системе.
Между тем, Мацуура и Содик применили другой подход, объединив технологию Powder Bed Fusion (PBF) и возможности ЧПУ в своих гибридных производственных системах. Чтобы не отставать от конкурентов, DMG MORI недавно представила собственную гибридную систему PBF и ЧПУ.
В дополнение к автономной гибридной системе существует также возможность дооснащения существующего обрабатывающего центра с ЧПУ лазерной наплавочной головкой Ambit с подачей порошка от Hybrid Manufacturing Technologies.
Компании также могут добавить к станку с ЧПУ комбинацию возможностей подачи порошка и проволоки с технологией 3D Hybrid. Это позволяет превратить обычную субтрактивную систему в гибридную производственную систему с относительно минимальными затратами и усилиями.
Хотя перспективы гибридного производства впечатляют, мы только начали изучать, как эта технология может быть применяется эффективно и жизнеспособно.
Использование 3D-печати как дополнительной технологии
3D-печать может стать ценным активом для производителей, стремящихся оптимизировать свои традиционные производственные процессы.
Эта технология может быть использована для производства высокопроизводительных форм и сложных моделей литья, а также для повышения эффективности обрабатывающих инструментов. Кроме того, гибридные машины могут предложить компаниям большую свободу и гибкость при проектировании и производстве.
Таким образом, вместо того, чтобы рассматривать аддитивное производство как конкурирующую технологию, производителям следует использовать его как еще один инструмент в наборе инструментов и сделать шаг вперед, чтобы воспользоваться преимуществами, которые оно дает.
3D печать
- 5 преимуществ 3D-печати на производстве
- 4 способа, которыми 3D-печать меняет медицинскую промышленность
- 8 способов, которыми промышленная 3D-печать меняет производство
- 6 способов снижения производственных затрат с помощью 3D-печати
- 6 способов снизить стоимость 3D-печати
- 3D-печать везде
- 5 способов, которыми 3D-печать меняет автомобильную промышленность
- Аддитивное производство в медицине и стоматологии
- Будущее 3D-печати в производстве
- Является ли 3D-печать будущим производства?