Обеспечение качества 3D-печати на металле:решение 3 общих проблем
Обеспечение качества (QA), возможно, является наиболее важным и, тем не менее, одним из самых сложных шагов в 3D-печати.
Поскольку 3D-печать все чаще используется в высокопроизводительных промышленных приложениях, эта технология должна обеспечивать стабильную и надежную поставку высококачественных деталей со свойствами, необходимыми для удовлетворения требований приложений. Однако когда дело доходит до 3D-печати металлом, это постоянная проблема для многих производителей, желающих инвестировать в эту технологию.
В сегодняшней статье будут рассмотрены некоторые из ключевых проблем, с которыми компании сталкиваются при попытке наладить процессы контроля качества металлических деталей, напечатанных на 3D-принтере, и изучить некоторые из доступных решений.
Задача 1. Обеспечение качества ваших материалов
Обеспечение того, чтобы деталь, напечатанная на 3D-принтере, соответствовала стандартам очень требовательных приложений, во многом зависит от качества используемого материала.
Однако квалификация материала является постоянной проблемой для компаний, производящих металлический порошок или работающих с ним. Одним из факторов, усложняющих процесс, является необходимость поддерживать чистоту металлических порошков, используемых для аддитивного производства.
Это особенно актуально для критически важных с точки зрения безопасности приложений, таких как детали самолетов или медицинские устройства, где материал используемый материал должен быть на 100% свободным от загрязнений. Примеси могут изменить свойства конечной детали, что, в свою очередь, может привести к неудачной печати.
Однако существует несколько способов загрязнения металлических порошков.
Например, риск загрязнения может возникнуть во время самого процесса печати или при хранении, транспортировке и обращении. Возьмем первый пример:например, на рабочей пластине может остаться какой-то остаток другого порошка, что приведет к смешиванию двух разных порошков. Поэтому тщательная очистка рабочего стола после каждого производственного цикла является важным профилактическим шагом.
Другой риск возникает при повторном использовании порошка, оставшегося от процесса печати. Хотя возможность повторного использования порошкового материала может помочь снизить потери, важно отметить, что повторное использование порошка таким образом потенциально может изменить состав частиц, поскольку влага, кислород и азот абсорбируются.
Неизбежно потребуются методы испытаний, подходящие для аддитивного производства, чтобы гарантировать отсутствие загрязнения.
Решение:рассмотрите возможность компьютерной томографии
Одним из наиболее точных способов обнаружения загрязнений в металлических порошках является сканирование с помощью компьютерной томографии (КТ).
КТ-сканер делает сотни рентгеновских снимков под разными углами, из которых создается трехмерное изображение. Современные компьютерные томографы могут захватывать детали размером до трех микрон, а некоторые микроКТ-сканеры с высоким разрешением работают в гораздо меньшем микрометровом масштабе, достигая размера вокселя 0,5 микрона.
Современное оборудование microCT может проверять металлы, начиная от алюминия и титана и заканчивая более тяжелыми металлическими сплавами, такими как нержавеющая сталь и инконель.
При использовании для проверки металлических порошков для 3D-печати сканеры компьютерной томографии могут предоставить инженерам подробные данные о микроструктуре порошка. Эти данные могут использоваться для обнаружения примесей посторонних частиц, а также для измерения распределения частиц по размеру и форме и обнаружения пористости внутри частиц. Получение этой информации - один из способов, которым инженеры могут подтвердить пригодность порошка для производства.
Одна компания, предоставляющая услуги компьютерного сканирования для аддитивного производства, - это Expanse Microtechnologies.
В интервью AMFG Джеймс Хайнбо, президент и соучредитель компании, отмечает:«Порошки - это ключевой момент во всей цепочке поставок аддитивного производства. Понимание того, что делает хороший порошок, который распределяется и хорошо печатается, является ключевой задачей для компаний.
«Важно понимать:1) есть ли идеальная морфология или идеальное распределение по размеру или морфологическому составу, которые могут хорошо взаимодействовать с широким спектром устройств для повторного нанесения покрытия и принтеров, и 2) как мы можем уменьшить дефекты в порошках, такие как включения и внутричастичная пористость, которая, как показали исследования, часто застревает в детали и не может выйти из нее во время процесса печати ».
Это две области, которыми Expanse Microtechnologies занимается с помощью своего патентованного решения для сканирования MicroCT.
Компания разработала передовые методы обработки изображений, с помощью которых она может создавать подробные отчеты о пористости материала, морфологии частиц и пор, а также о распределении частиц по размеру и форме.
Наличие этой информации позволяет пользователям аддитивного производства выявлять любые проблемы с сырьем и понимать связи между используемыми материалами и уровнем качества печатаемых компонентов.
Хотя тестирование и аттестация сырья для аддитивного производства может быть сложной задачей, это один из наиболее важных шагов для обеспечения качества детали, произведенной аддитивным способом. В настоящее время компьютерная томография является одним из самых надежных и полезных инструментов, которые можно использовать для проверки исходных материалов AM.
Задача 2. Установление контроля над процессом
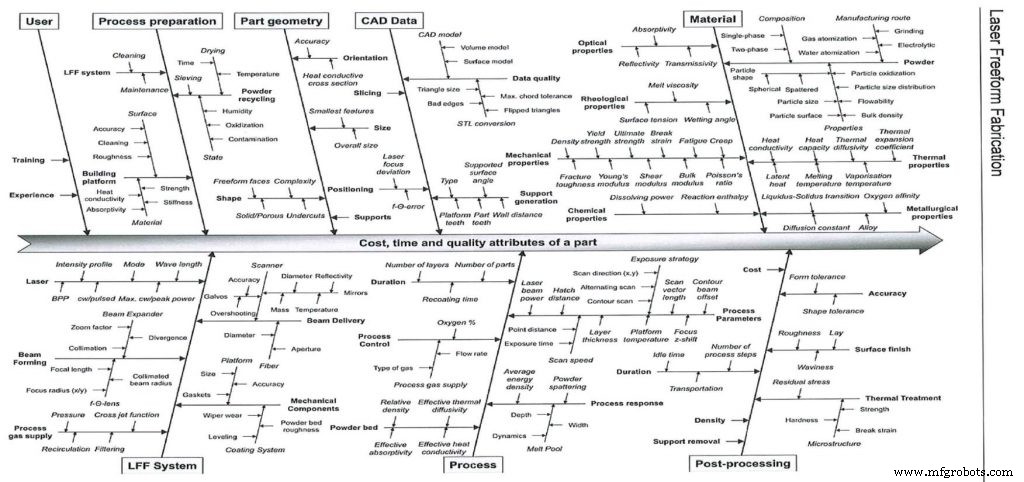
Когда дело доходит до 3D-печати металлом - и, в частности, технологий наплавки в порошковом слое - существует широкий спектр переменных, которые могут повлиять на форму и структуру детали. Эти переменные охватывают весь рабочий процесс AM, от проектирования до подготовки сборки и последующей обработки.
Возьмем в качестве примера процесс печати. Здесь лишь некоторые из параметров, определяющих успех или неудачу процесса, включают путь и интенсивность лазера и скорость лезвия для повторного нанесения покрытия принтера. Другие факторы включают в себя дизайн опорных конструкций и даже такие тонкости, как количество повторных переработок порошка.
Хотя этот список далеко не исчерпывающий, каждый фактор влияет на результат конструкции и отклонения каким-либо образом могут повлиять на качество конечной детали.
В настоящее время метод проб и ошибок является наиболее распространенным подходом к работе с широким диапазоном переменных для достижения процесса, который дает воспроизводимые части. Однако это может включать в себя многократное изготовление готовой детали, а также всестороннее тестирование самой детали.
Конечно, применение этого подхода - очень дорогостоящий и неэффективный процесс, который сводит на нет одно из основных преимуществ технологии - возможность производить небольшие партии деталей с минимальными затратами.
Поэтому компаниям необходимо применять более устойчивый и осуществимый подход к управлению процессами и аттестации деталей, произведенных аддитивным способом.
Решение:разработать замкнутую систему контроля качества
Чтобы обеспечить более быстрый, надежный и устойчивый процесс обеспечения качества деталей, напечатанных на 3D-принтере, необходимо объединить три элемента. Это включает в себя планирование сборки, мониторинг сборки и контроль обратной связи.
- Планирование сборки
Один из способов лучше понять процесс печати - это моделирование. Используя моделирование, инженеры могут проверить, как деталь будет вести себя в виртуальной цифровой среде, прежде чем проект будет отправлен на печать.
Моделирование процесса AM позволяет инженерам анализировать сложные процессы, происходящие в процессе печати.
Поскольку 3D-печать металлом подвержена таким проблемам, как коробление и искажение, моделирование позволяет понять, как, например, деталь будет искажаться в процессе печати. Другой пример - использование моделирования для точного определения того, как материал будет плавиться и затвердевать.
Затем инженеры могут использовать эти данные для планирования сборки, выбирая наиболее успешную ориентацию детали и стратегии поддержки.
Тем не менее, у программного обеспечения для моделирования есть свои ограничения. «Сегодня все программное обеспечение для моделирования имеет некоторый уровень допущений, ограничивающих точность, которую оно может обеспечить. Это, вероятно, самый большой недостаток прямо сейчас:они не могут быть такими точными, как вам хотелось бы », - сказал главный технолог ANSYS Дэйв Коновер в недавнем интервью AMFG.
Однако технологии моделирования стремительно развиваются, и поставщики программного обеспечения продолжают совершенствовать свои предложения. В конечном итоге интеграция программного обеспечения для моделирования на этапах проектирования и планирования поможет исключить метод проб и ошибок, значительно снизив при этом вероятность сбоев при печати.
- Мониторинг сборки
Системы контроля в процессе производства могут дополнительно помочь в процессе аттестации детали. Датчики и камеры могут использоваться для измерения различных аспектов сборки в режиме реального времени, помогая документировать процесс сборки и обеспечивать выполнение требований.
Благодаря процессам AM порошкового слоя камеры могут фиксировать размер и температуру ванны расплава, что напрямую влияет на микроструктуру, свойства материала, качество поверхности и общие характеристики детали.
Инженеры затем может использовать эти данные для прогнозирования вероятности дефектов, таких как коробление или растрескивание, и вмешиваться в процесс задолго до того, как дефекты возникнут. Поскольку эти данные задокументированы, это может помочь избежать условий процесса, которые могут привести к этим дефектам в будущем.
В настоящее время существует ограниченное количество технологий непрерывного мониторинга, оптимизированных для AM.
Sigma Labs - одна из компаний, которая предлагает решение для внутрипроизводственного контроля качества AM. Его система обеспечения качества PrintRite3D для аддитивного производства сочетает в себе мультисенсоры и оборудование PrintRite3D SENSORPAK с программным модулем PrintRite3D INSPECT.
Эта многогранная комбинация, зарегистрированная как технология IPQA, позволяет оптимизировать условия плавильной ванны во время процесса AM, используя данные датчиков и устанавливая показатели качества в процессе. Используя статистический анализ данных процесса, можно создавать отчеты о качестве деталей и использовать их для проверки повторяемости.
В будущем компания планирует добавить программный модуль ANALYTICS, ориентированный на использование аналитики Big Data. Модуль сможет извлекать значимую и полезную информацию из данных, собранных в процессе печати, чтобы еще больше упростить контроль качества в процессе.
Что касается самих 3D-принтеров, некоторые из них уже имеют встроенную возможность мониторинга. Например, производитель 3D-принтеров EOS предлагает пакет мониторинга EOSTATE. Аппаратное и программное решение основано на четырех различных модулях мониторинга, включая System and Laser, PowderBed, MeltPool и Exposure OT (оптическая томография), которые могут собирать важные данные в реальном времени.
EOSTATE Exposure OT заявляет, что EOS является единственным производителем систем металлического порошка, предлагающим своим клиентам инструмент для обеспечения качества, включающий оптическую томографию.
В этой системе наблюдения используется камера, которая собирает световое излучение в ближнем инфракрасном диапазоне, как и тепловизионная камера. Он может полностью отображать каждую часть в процессе сборки, слой за слоем, независимо от ее геометрии и размера. Благодаря такому подходу инженеры могут расширить диапазон обнаруживаемых явлений, влияющих на качество деталей AM.
MTU Aero Engines - одна из компаний, которая уже начала использовать это решение для мониторинга на своих серийных производственных линиях для AM детали авиационных двигателей.
- Завершение цикла
Определение и документирование параметров в процессе печати имеет решающее значение. Но способность действовать в соответствии с этой информацией в реальном времени - процесс, известный как управление с обратной связью, - делает этот подход еще более эффективным.
Управление с обратной связью, также известное как система с обратной связью, относится к способности обнаруживать отклонения в процессе печати и автоматически настраивать систему для их компенсации. Сохранение контроля над процессом сборки позволяет производителям добиваться согласованных геометрических характеристик, отделки поверхности и свойств материалов, лежащих в основе качества.
Одна компания, которая разработала процесс AM с обратной связью, - это Velo3D. Собрав более 92 миллионов долларов финансирования, Velo3D появилась прошлым летом, выпустив свое комплексное металлическое AM-решение. Он включает в себя 3D-принтер Velo3D Sapphire, программное обеспечение для подготовки к печати Flow и то, что компания называет технологией Intelligent Fusion.
За счет того, что эти ключевые элементы тесно интегрированы друг с другом, технология позволяет моделировать тепловые процессы, прогнозировать производительность печати и управлять обработкой с обратной связью. В результате система Sapphire может многократно и последовательно производить детали сложной геометрии, такие как выступы практически без опорных конструкций.
Программное обеспечение Velo3D Flow играет важную роль в реализации этих преимуществ. Программа выполняет моделирование и коррекцию перед печатью, оптимизируя конструкцию и регулируя геометрию и ориентацию детали. Это помогает подготовить файл, компенсируя любые деформации, чтобы деталь вышла правильно. Метрология процесса на месте, сопровождаемая замкнутым контуром управления бассейном расплава, работает в тандеме с программным обеспечением, что в конечном итоге увеличивает успешность первой части до более чем 90%.
Задача 3. Уменьшение количества человеческих ошибок
Человеческая ошибка, возможно, является самым большим фактором риска в обеспечении соответствия детали, напечатанной на 3D-принтере, всем необходимым стандартам.
Это связано с тем, что 3D-печать по-прежнему требует большего вмешательства человека, чем вы могли ожидать, от проектирования и удаления опор до постобработки и ручной проверки выполнения требований на каждом этапе.
Такой уровень вмешательства человека неизбежно увеличивает риск взлома последней части.
Возьмем для примера этап постпродакшна.
После завершения сборки ее нужно будет распаковать, а различные части, которые были напечатаны в этой сборке, необходимо будет идентифицировать и проверить, прежде чем они будут отправлены на постобработку.
Инженер-технолог, выполняющий эту задачу, обычно должен будет обратиться к распечатанному листу задания, по существу сопоставив 2D-изображение с его физическим аналогом и проверив список требований вручную.
Такой подход к проверке не только отнимает много времени, но и исключает видимость рабочего процесса из уравнения.
Тем не менее, многие компании, внедряющие AM, сталкиваются с трудностями при изменении руководства задачи, включенные в более быстрый, точный, автоматизированный процесс.
Поскольку снижение вероятности человеческой ошибки так важно для обеспечения качества деталей, напечатанных на 3D-принтере, одним из способов добиться этого является использование цифровых методов для автоматизации как можно большего числа этапов проверки.
Решение:внедрить программное обеспечение рабочего процесса для аддитивного производства
Программное обеспечение Workflow предлагает цифровую централизованную платформу, которая помогает проектным и производственным группам управлять производственными процессами AM.
В контексте обеспечения качества программное обеспечение рабочего процесса часто может предоставить полную структуру, помогающую компаниям обеспечить выполнение требований ко всем частям.
Кроме того, руководители производства могут использовать программное обеспечение для документооборота, чтобы сделать процесс проверки деталей безбумажным и отслеживаемым. Вместо того, чтобы вручную проверять каждую деталь с листом заданий в руке, физические детали можно сравнивать с их трехмерными цифровыми аналогами.
Например, инструмент управления постпроизводством AMFG предоставляет средство трехмерного просмотра, которое включает в себя все данные детали, что позволяет пользователям более точно проверять деталь и ее свойства.
Инструмент позволяет пользователям отслеживать соотношение удачных и неудачных деталей. Детали, отмеченные как неисправные, автоматически возвращаются во внутреннюю производственную очередь платформы для воспроизведения. Самым большим преимуществом этого является то, что пользователи могут отслеживать каждое действие, выполняемое деталью, добавляя отслеживаемость и подотчетность к необходимости управления качеством.
Существуют ли отраслевые стандарты обеспечения качества для AM?
На данный момент мы убедились, что понимание того, как квалифицировать процессы, материалы и внедрять цифровые стратегии, является ключом к тому, чтобы компании могли получить выгоду от 3D-печати для производства.
Отраслевые стандарты будут играть ключевую роль в этом процессе. этот процесс. При традиционном производстве стандарты уже стали обычным явлением, помогая компаниям обеспечивать качество своей продукции и находить точки соприкосновения. Конечно, у традиционного производства были десятилетия, если не столетия, чтобы разработать соответствующие стандарты.
3D-печать, напротив, все еще относительно новый процесс, и многие стандарты и сертификаты все еще находятся в стадии разработки. В будущем отрасли потребуется разработать методы испытаний, протоколы и справочные данные, чтобы сократить затраты и время на аттестацию материалов, процессов и деталей AM.
К счастью, это область, которая быстро развивается. Буквально в прошлом году AMST International опубликовала свой стандарт F3303, в котором излагаются способы квалификации машин и процессов, используемых для создания деталей с использованием лазерного или электронно-лучевого наплавления порошка. Было также отмечено, что уже разрабатывается дополнительный стандарт для поддержки квалификации деталей, обеспечения качества и последующей обработки деталей, изготовленных методом плавления в порошковом слое.
Наряду с ASTM International, Национальный институт стандартов и технологий (NIST) работает над разработкой стандартов QA для индустрии AM. Например, NIST запустил проект AM Part Qualification, сфокусированный на «измерениях, методах и метрологических системах, необходимых для создания надежных измерений после обработки, развития глубокого понимания механических характеристик и аттестации AM частей».
Следить за качеством
Обеспечение качества материалов и контроль процесса имеют решающее значение для производства металлических деталей неизменно высокого качества с помощью 3D-печати.
Каким бы сложным это ни казалось на первый взгляд, производители могут обнадежить, поскольку существуют решения для поддержки процесса обеспечения качества, подкрепленные постоянным развитием отраслевых стандартов.
Решение этих задач и стратегическое внедрение правильных решений для вашей компании значительно помогут вам воспользоваться преимуществами 3D-печати для дорогостоящих и ресурсоемких приложений.
3D печать
- Ожидается, что порошки тугоплавких металлов станут сырьем для 3D-печати
- Порошки тугоплавких металлов VS Технология 3D-печати
- Анализ того, что новая технология печати на металле означает для AM
- Контроль качества в реальном времени:какая система вам подходит?
- Опорные конструкции для 3D-печати металлом - более простой подход
- H.C. AMPERPRINT Старка:новый инструмент для 3D-печати металлом
- Какие порошки для 3D-печати по металлу можно использовать в 2020 году? [Руководство]
- 6 Важные соображения при проектировании для 3D-печати из металла
- Советы по проектированию для 3D-печати с прямым лазерным спеканием металла
- Обзор технологии:когда действительно стоит перейти на 3D-печать металлом