Двухкомпонентная эпоксидная смола для увеличения производства композитных авиационных конструкций с помощью RTM
Это третий из моей серии блогов о технологиях, которые вы должны проверить на CAMX 2019 (23-26 сентября, Анахайм, Калифорния, США). Компания Hexion (Колумбус, Огайо, США) разработала двухкомпонентную (2K) систему для RTM аэроструктур на основе своей эпоксидной смолы Epikote System 600. Введение ниже объяснит, почему это развитие важно. После этого я более подробно расскажу об этой новой системе 2K и о том, как Hexion выполняет требования OEM-производителей в аэрокосмической отрасли по обеспечению качества смешанной смолы на месте. Внизу я также обсуждаю 2K эпоксидную смолу для инфузии / RTM Hexion для огнестойких (FR) приложений.
Почему 2K смолы для RTM?
Ранее в этом году я писал о программах в компании Alpex Technologies (Милс, Австрия), специализирующейся на инструментальной оснастке, и Composites Technology Center, дочерней компании Airbus (CTC, Stade, Германия), по производству композитных деталей самолетов с использованием литьевого формования полимеров (RTM) . Использование RTM в авиакосмической сфере не новость. Существуют и производятся различные детали самолетов, изготовленные с использованием RTM, в том числе:
- Руль для бизнес-джета Gulfstream G250 (Israel Aerospace Industries и North Coast Composites)
- Лопасти и корпус вентилятора турбовентиляторного авиационного двигателя LEAP (Albany Engineered Composites)
- Дверная коробка A350 (Airbus Helicopters Donauworth)
- Демонстрация пассажирской двери A350 (Elbit Cyclone)
- Демонстрационный многошпачок A320 (Airbus Bremen)
- Компания Matrix Composites произвела более 6000 компонентов для F-22 с использованием RTM.
Однако RTM в аэрокосмической отрасли традиционно представляет собой процесс низкого давления, время цикла которого измеряется часами. Программы Alpex и CTC ориентированы на использование автоматизации, быстрого впрыска и длительности цикла от 15 до 20 минут предлагаемые РТМ высокого давления (HP-RTM). В моей статье «HP-RTM для серийного производства экономичных аэроструктур из углепластика» я обсуждал вопрос использования 2-компонентных (2K) эпоксидных смол по сравнению с текущей нормой использования предварительно смешанных, 1-компонентных (1K) систем:
«Шиллер [Ян Шиллер, руководитель проекта CTC по производственным системам и ведущий контакт по технологиям RTM] отмечает, что все предыдущие RTM в самолетных конструкциях использовались только системы 1К смешивается поставщиком, который затем сертифицирует смесь и несет ответственность за соответствие смолы квалификационным требованиям. «Сейчас мы рассматриваем системы 2K, но наша задача - обеспечить качество микширования , - поясняет он. Предварительно смешанные системы 1K требуют холодной транспортировки и хранения, чтобы предотвратить реакцию до обработки детали. Таким образом, преимущества систем 2K включают устранение этих затрат, а также более высокую реактивность для более быстрой обработки ».
«Однако одна проблема заключается в том, что обеспечение качества (ОК) перейдет от поставщика смолы к производителю деталей. «Для этого контроля качества требуется определение соотношения компонентов и качество смешанной смолы . Оба необходимы для квалификации нового материала Airbus. Таким образом, это означает измерения двух компонентов непосредственно перед смешиванием и смолы после смешивания . . Сегодня у нас есть только датчики перед смесительной головкой, показывающие, сколько смолы и сколько отвердителя добавлено в смесь. Этого недостаточно для квалификации ».
Компания Hexion (Колумус, Огайо, США), лидер в разработке быстроотверждаемых эпоксидных смол для HP-RTM в автомобильных композитах (см. «HP-RTM на подъеме»), объявила в марте 2019 года, что она разработала систему 2K для RTM аэроструктуры на основе эпоксидной смолы Epikote System 600. Я взял интервью у лидера Hexion Epoxy Global Aerospace Segment, Жана Ривьера, чтобы узнать больше об их системе 2K для аэрокосмической промышленности и о том, как они удовлетворяют этот спрос на обеспечение качества смешанной смолы на месте.
Преодоление ограничений систем 1K
«Как и в случае с препрегом, системы 1K для RTM и инфузии в аэрокосмической отрасли должны храниться в холодном состоянии и иметь ограниченный срок хранения», - говорит Ривьер. «Используя двухкомпонентную (2K) эпоксидную систему, вы снимаете эти ограничения. Мы видели двухкомпонентные и высокореактивные эпоксидные смолы, используемые в производстве ветряных лопастей и автомобильных конструкций. Так почему бы не в аэрокосмической отрасли? »
Ривьер объясняет, что, поговорив об этом со многими клиентами, компания Hexion поняла основную проблему - вам необходимо подтверждение правильности пропорции смешивания в любое время до впрыска в форму. Без этого для производителя запчастей возникает неприемлемый риск », - отмечает он. Он добавляет, что раньше не было спроса на объемы производства ветряных лопастей и автомобилей. Однако теперь Airbus и Boeing хотят превысить текущие темпы производства, стремясь при этом производить больше композитных деталей на каждый самолет. «Итак, теперь существует необходимость отказаться от укладки препрега и перейти к 2K эпоксидной смоле для аэрокосмической RTM или инфузии», - говорит Ривьер.
На схемах цепочки поставок ниже показано, что технология 2K не только устраняет этапы хранения в холодильнике и подогрева, но и снимает ограничения на размер контейнера для смолы при транспортировке. «Вы должны уменьшить массу предварительно смешанной смолы до 20 литров и поддерживать эти бочки при очень низкой температуре, - говорит Ривьер, - иначе смола может начать реагировать. Для системы 2K стандартные 200-литровые бочки могут быть отправлены без ограничений по низкой температуре. Таким образом, меньше риска, не требуется сильного охлаждения и меньше мер предосторожности ».
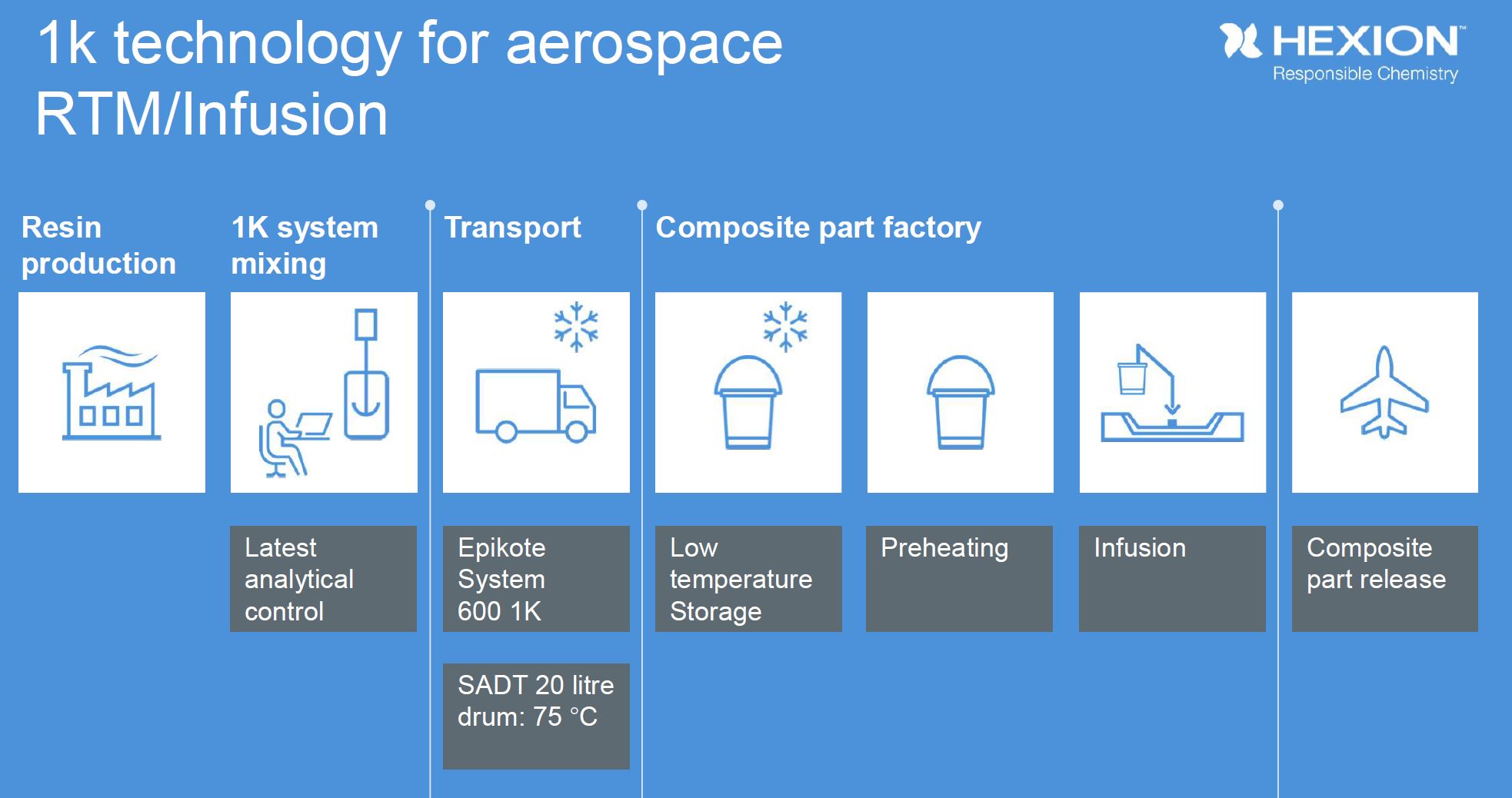
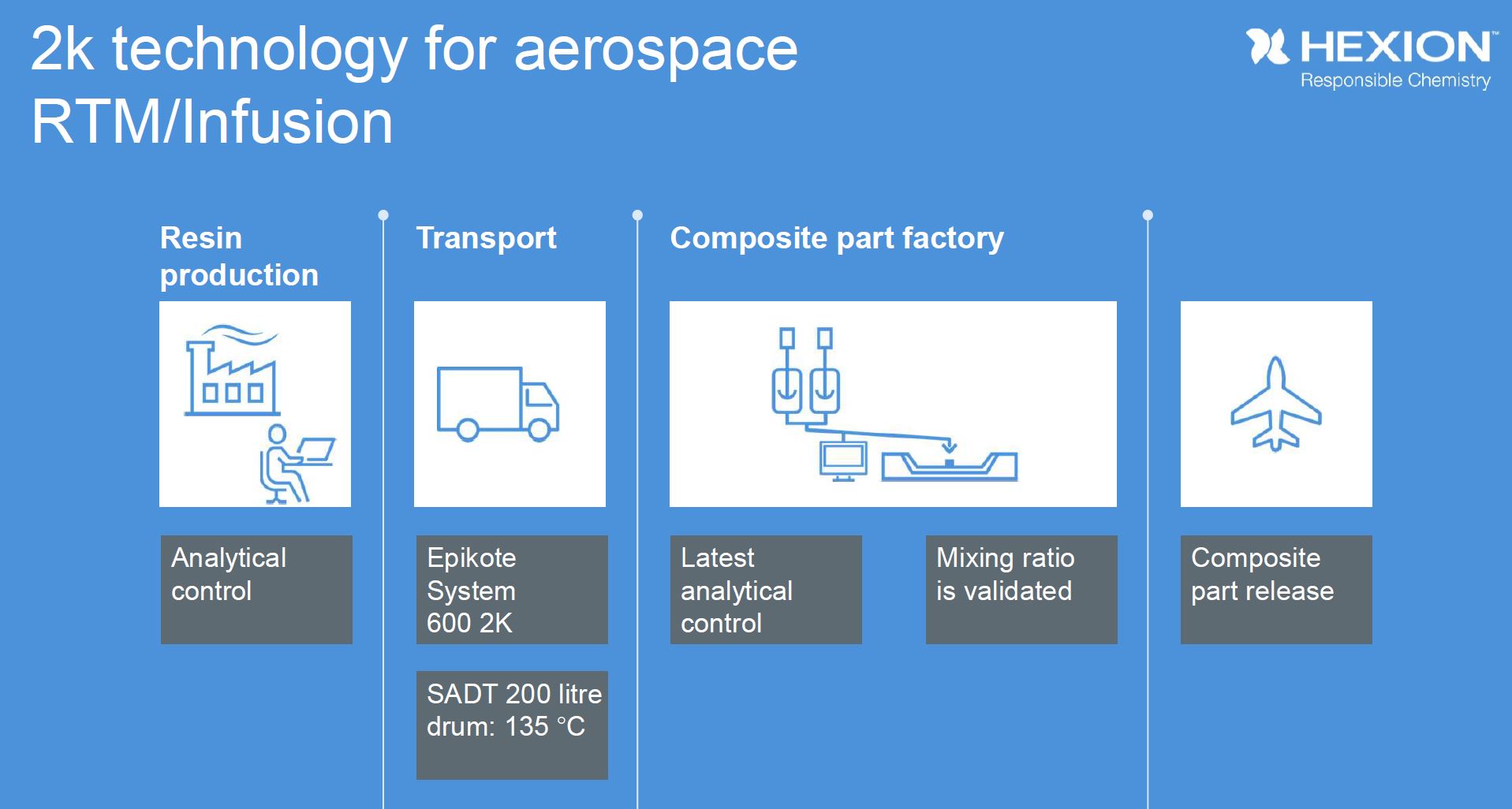
Приведенные выше цепочки поставок показывают, как меняется аналитический контроль. В то время как для систем со смолой 1K на производстве выполняется только начальный контроль, для системы 2K управление осуществляется в нескольких контрольных точках. В дополнение к контролю компонентов A и B во время заводского производства соотношение смешивания A:B также контролируется цифровым способом в оборудовании для смешивания, дозирования и дозирования (MMD), а также непосредственно перед впрыском смолы в форму. ИСТОЧНИК | Гексион.
Аналитический контроль
Чтобы разработать эту технологию 2K, Hexion работал с Hübers (Бохольт, Германия), производителем оборудования для смешивания, дозирования и дозирования (MMD), и Composyst (Hurlach, Германия), которая имеет эксклюзивную лицензию на запатентованный Airbus процесс с вакуумной поддержкой ( ВАП) для инфузий. Hübers имеет прочную репутацию в области высокопроизводительных систем MMD, используемых в производстве электрических и электронных компонентов (например, литье из смолы и пропитанные компоненты для трансформаторов и т. Д.), В то время как Composyst является экспертом в области впрыска и инфузии смолы для приложений Airbus, и, следовательно, , понимает, что производители самолетов ищут в отношении обработки и обеспечения качества (ОК) смешанных смол.
«Аналитический контроль вступает в игру после того, как компоненты A и B эпоксидной смолы были точно смешаны на оборудовании Hübers и готовятся к загрузке в форму», - поясняет Ривьер. Черные трубки между системой Hübers MMD и системой инфузии VAP с вакуумным мешком на изображении ниже являются ключевым компонентом этой аналитической системы контроля. «Здесь у нас есть аналитическое устройство, которое контролирует соотношение смеси в реальном времени», - говорит Ривьер. «Мы продемонстрировали измерение соотношения компонентов смеси каждые 12 секунд, но возможно и более частое измерение. Действительно, технология позволяет непрерывно контролировать соотношение компонентов смеси, которое регистрируется и регистрируется ».
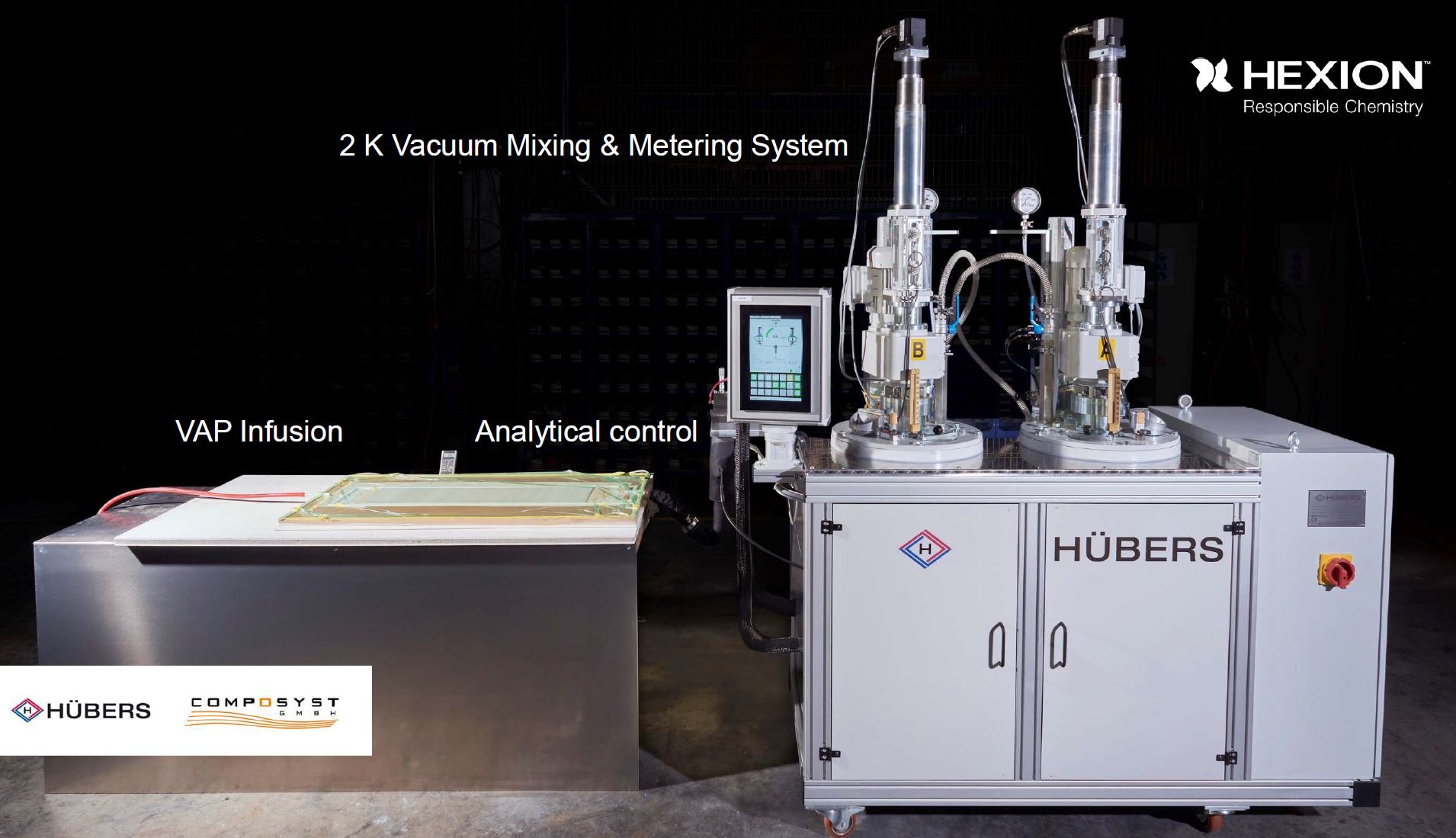
Обратите внимание на черные трубки между оборудованием Hübers MMD и установкой для инфузии VAP, где компания Hexion разработала поточное измерение соотношения смол в смеси перед инъекцией. Гексион
«С этой системой, - продолжает он, - существует двойной контроль:нормальный контроль в блоке MMD и наш аналитический контроль перед впрыском сверху. Во-первых, Ривьер отмечает, что станки Hübers MMD хорошо известны своей точностью и аккуратностью. «Они имеют двойную насосную систему для двух компонентов и должны обеспечивать точность объема и температуры, а также соотношения компонентов смеси для приложений, в которые они поставляют. Затем наша система добавляет второе измерение после смешивания и непосредственно перед впрыском, где вы можете установить цели для сигналов тревоги ». Если измеренное соотношение смеси не соответствует целевым показателям и срабатывает сигнал тревоги, система откачивает смешанную смолу в отдельный сосуд, минуя форму, чтобы она не вводится в заваренную часть. «После этого можно возобновить процесс и продолжить закачку», - отмечает Ривьер.
Он говорит, что аналитическая система управления предварительным впрыском и пост-смешиванием Hexion обеспечивает независимую запись для прослеживаемости, а также может быть интегрирована в блок MMD, в зависимости от потребностей клиента. Ривьер отмечает, что установка Hübers MMD также выполняет тщательную дегазацию смолы, которая требуется в электронной промышленности, когда в компонентах нанесения не должно быть пустот или пористости. «Эта система также обеспечивает портативный контроль давления на пресс-форму, управляя потоком смолы на высоком или низком уровне», - отмечает он. «Вы можете добиться очень хорошей пропитки с помощью этого типа контроля, а также можете сократить время процесса инфузии, соблюдая аэрокосмические требования к качеству с точки зрения пористости и объема волокна».
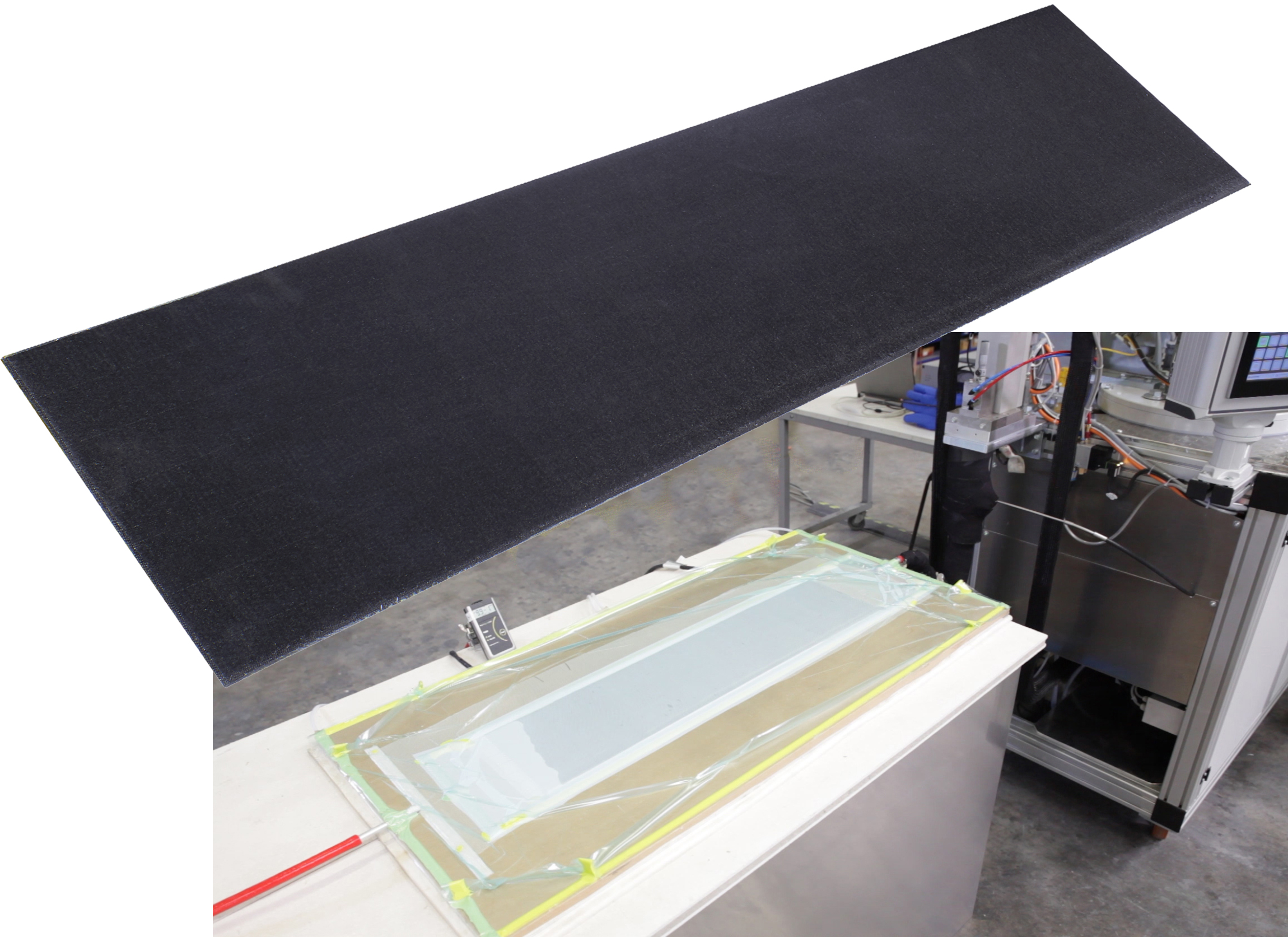
На фотографиях показана установка для инфузии с использованием оборудования Hübers MMD и аналитического контроля Hexion 2K, а также ламината UD из углеродного волокна толщиной 2 сантиметра, приготовленного с использованием этой установки, с получением более 60% объема волокна. ИСТОЧНИК | Гексион
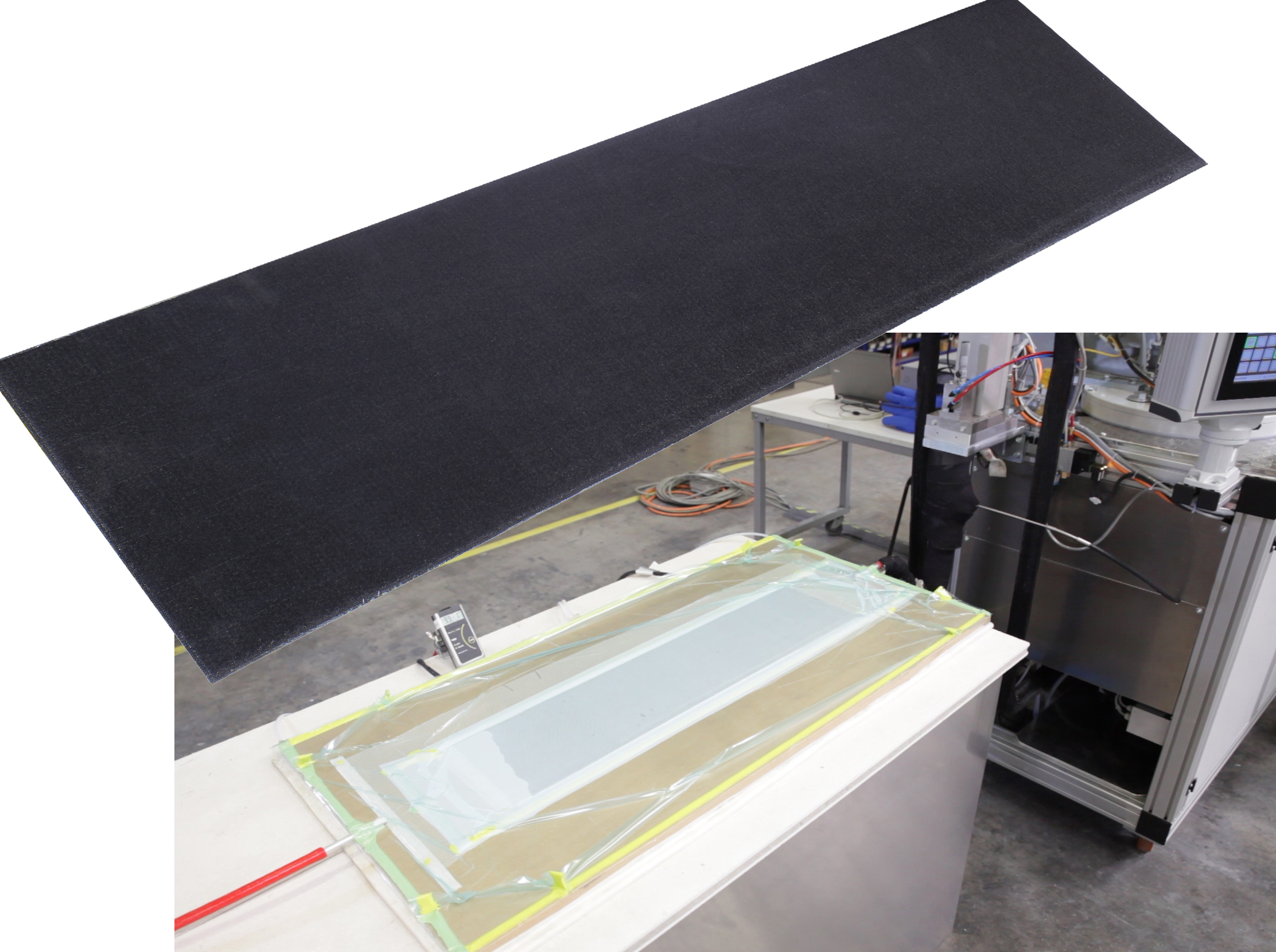
Окно улучшенной обработки
«Поскольку смешивание осуществляется с помощью статического смесителя и за короткий промежуток времени непосредственно перед впрыском, смесь смолы обеспечивает более длительную жизнеспособность (до 40% по сравнению с 1K)», - отмечает Ривьер. . Это обеспечивает лучшее окно обработки, и мы производим толстые ламинаты из углеродного волокна с объемом волокна 60%. Механические характеристики систем 2K и 1K одинаковы, потому что химический состав одинаков. Мы считаем, что это будет более надежный процесс, и полная ценность будет тогда, когда вы подключите управление смешиванием к установке впрыска смолы ».
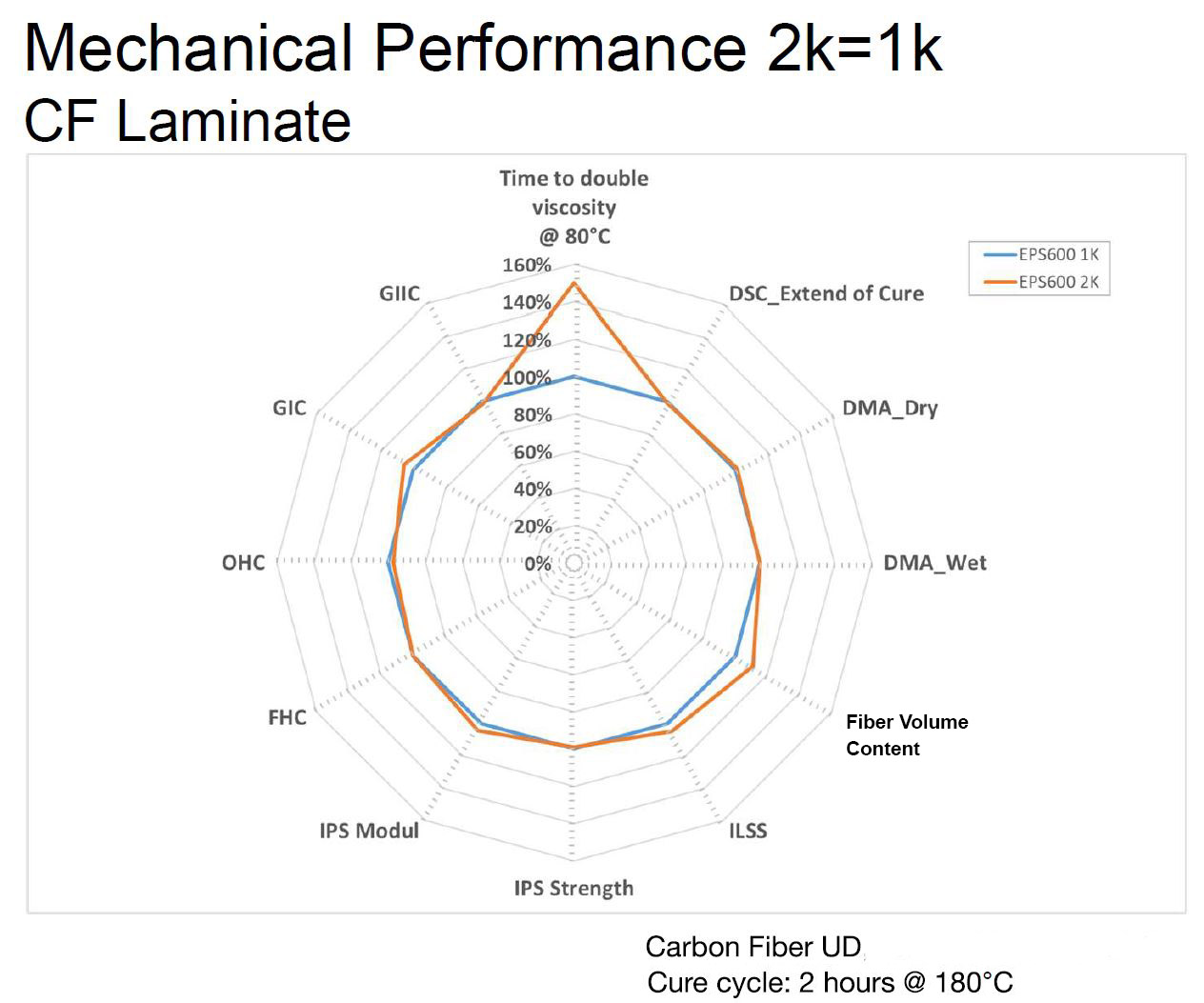
ИСТОЧНИК | Гексион
Hexion представит подробную информацию как о своей системе 2K Epikote 600 для RTM, так и о своей эпоксидной смоле EPON FlameX для соответствия требованиям по пожарной, дымовой и токсичности (FST) самолетов (см. Ниже) в CAMX Theater на полу выставки:
- Новая технология 2K для производства эпоксидных смол в аэрокосмической отрасли
Вторник, 24 сентября - 11:00 -11:25 - Эпоксидные системы FlameX для пожарной безопасности
Вторник, 24 сентября - 11:30 - 11:55
Вы также можете получить более подробную информацию на стенде Hexion Y24.
Эпоксидная смола EPON FlameX для настаивания / RTM огнестойких композитов
Hexion также разработал 2-компонентную эпоксидную смолу для вливания / RTM деталей, которая должна соответствовать требованиям огнестойкости (FR) и пламени, дыма, токсичности (FST). Направленные на замену фенольных препрегов жидким эпоксидным формованием, движущими силами этого развития являются:
- Повышение производительности.
- Правила REACH для безгалогенных нефенольных систем.
- Более прочные и жесткие смолы по сравнению с хрупкими фенолами.
- Экономичен по сравнению с фенольными смолами, но намного дешевле, чем термопласты.
В системе EPON FlameX компании Hexion не используются галогены или добавки в виде твердых частиц для достижения огнестойкости, а вместо этого они встраиваются в молекулярную основу смолы. Во время инфузии не происходит фильтрации твердых частиц. Смола хорошо впитывается с вязкостью 250 сП при 60–70 ° C (140–158 ° F) и затвердевает за 1,5 часа при 150 ° C (302 ° F). Для достижения максимальных структурных свойств рекомендуется пост-отверждение при температуре 180 ° C в автономном режиме или с опорой на инструменты.
Детали, изготовленные с помощью этой системы, проходят следующее без дополнительных покрытий или мер огнестойкости:
- Вертикальное горение 60-х годов FAR25.853 (a)
- Дымовая токсичность BSS7239
- Плотность дыма BSS7238
Он также выдерживает тепловыделение OSU 65/65 в определенных конфигурациях с сертифицированным вспучивающимся гелевым покрытием или покрытием. Это требуется только для частей, которых можно коснуться во время руления, взлета и посадки самолета.
«Мы продемонстрировали подвесные контейнеры, изготовление которых в настоящее время требует 10-12 часов с использованием обычных процессов фенольного препрега, но может быть произведено за 90-120 минут с помощью инфузии или RTM с использованием системы FlameX», - говорит Натан Бруно, специалист по эпоксидным покрытиям и разработке продукции Hexion. . «Кроме того, из-за отсутствия наполнителей он имеет более низкую плотность по сравнению с эпоксидными смолами с наполнителем».
Применения включают интерьеры самолетов, грузовые пространства, туалеты, кухню и компоненты сидений, а также морские, железнодорожные и архитектурные интерьеры.
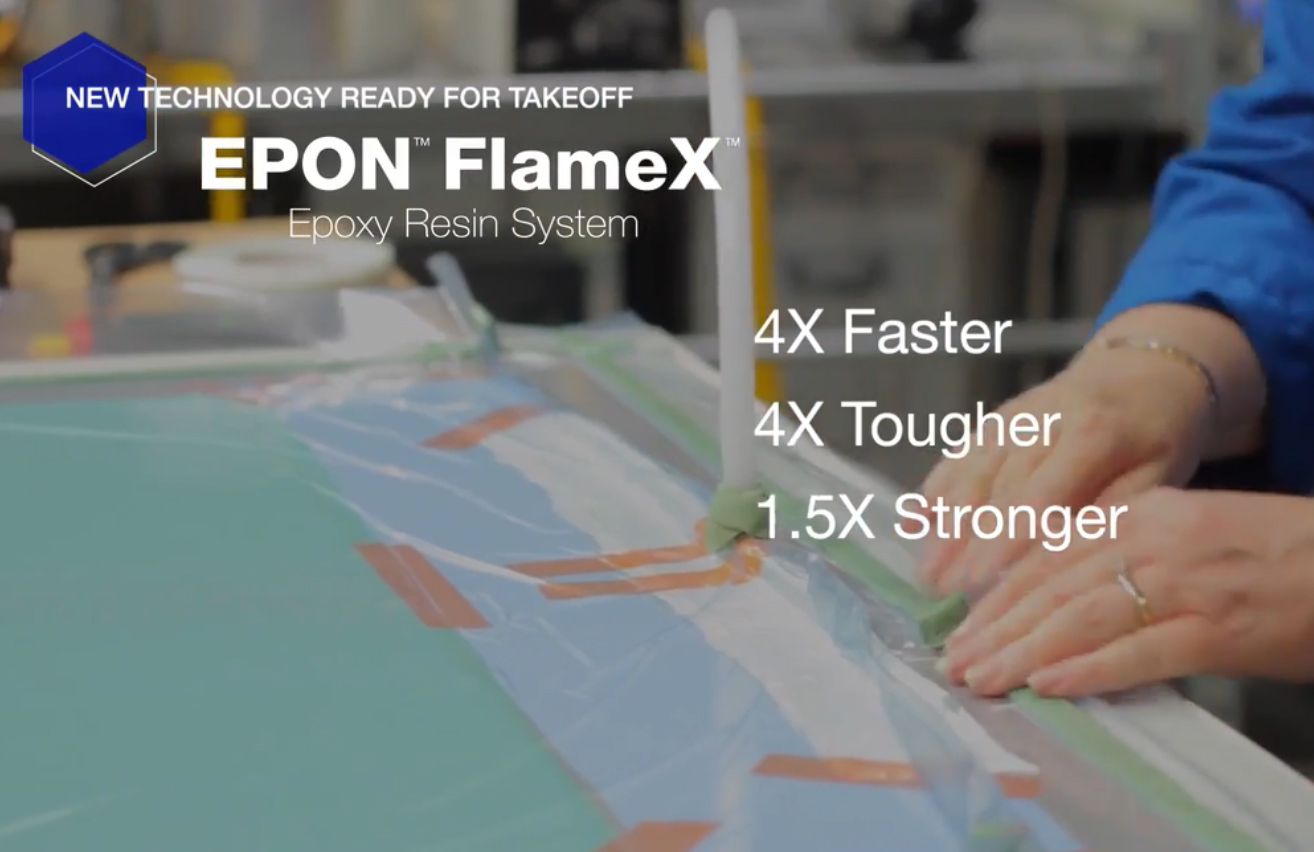
Смола
- Lanxess добавляет две новые производственные линии для композитного материала Tepex
- Чистящие составы для производства тонкостенных полиолефиновых упаковок
- Использование эпоксидной смолы в искусстве набирает популярность
- Fraunhofer вводит в эксплуатацию автоматизированные производственные ячейки Engel для НИОКР термопластичных компо…
- Broetje-Automation расширяет портфолио AFP для серийного производства композитных материалов
- INEOS Styrolution для создания производственной площадки для термопластичного композита StyLight
- Total Composite Solutions (TCS) запускает раствор эпоксидного препрега для аэрокосмической промышленности
- Hexion представляет двухкомпонентный эпоксидный раствор для производства аэрокосмических композитов
- Techsil выпускает прозрачный эпоксидный клей для композитных подложек
- Rhodes Interform производит композитный пресс для AMRC