Углеродное волокно / эпоксидная смола для уменьшения массы автомобилей, массовое производство
В рамках проекта IACMI 3.2 проводилась оценка композитов, армированных углеродным волокном, с добавлением новой системы смолы на основе эпоксидной смолы для разработки структурных композитных деталей сложной геометрии для замены металлов в высоконагруженных, критически важных для безопасности применениях на основных конструкциях кузова крупногабаритных пассажиров. транспортных средств. Одним из первых оцениваемых применений было использование препрега из углеродного волокна / эпоксидной смолы на средней стойке испытываемого автомобиля. Высококачественный препрег непосредственно уменьшил массу на 3 килограмма и позволил уменьшить толщину окружающего листового металла, который затем можно было бы использовать из менее дорогих сплавов, предлагая дополнительный вес и экономию средств. Источник | Ford Motor Co.
Автопроизводители в большинстве регионов сталкиваются с непростыми требованиями к 2025 году по сокращению выбросов из выхлопных труб и / или повышению топливной экономичности легковых автомобилей. Однако разработка принципиально новой автомобильной технологии для удовлетворения этих требований требует больших затрат, поэтому во многих странах используются консорциумы, позволяющие участникам цепочки поставок разделять расходы на предконкурентные исследования.
В США одной из таких организаций является Институт инноваций в области производства композитов (IACMI - The Composites Institute, Ноксвилл, штат Теннеси, США). Среди инициатив организации члены IACMI, представляющие промышленность, научные круги и правительство, работают над многосторонними проектами - включая комплексную разработку материалов / процессов, моделирование / симуляцию, соединение различных материалов и переработку - для решения инженерных проблем, увеличения массы транспортного средства, снижения энергопотребления. потребление и выбросы, а также создание новых рабочих мест в США.
Проект 3.2 и невозможная система смол
Проект 3.2 был одним из первых проектов IACMI, когда он был сформирован в июне 2015 года, хотя технология, используемая в проекте, фактически начала разрабатываться за несколько лет до создания IACMI в сотрудничестве с Ford Motor Co. (Дирборн, штат Мичиган. , США) и то, что тогда было Dow Automotive (ныне Dow Chemical Co., Мидленд, Мичиган, США). Когда образовался IACMI и начался проект 3.2, Форд и Доу включили в программу свои предыдущие работы по новой системе эпоксидной смолы. После присоединения к IACMI программа расширилась и в конечном итоге включила в себя несколько этапов, представляющих новые применения этой инновационной смолы:стойка B из препрега, крышка для цельнолистового формовочного компаунда (SMC) и задняя дверь из SMC / алюминия.
Семейство смол под названием VORAFUSE, разработанное Dow для Ford, предназначено для использования в препрегах и SMC, а также для обработки на оборудовании для компрессионного формования, которое широко доступно в автомобильной промышленности Северной Америки. Согласно требованиям Форда температура стеклования смолы (T g ) составляет 150-160 ° C, он формуется при 145-155 ° C и отверждается менее чем за 2 минуты при 150 ° C (хотя возможно отверждение менее чем за 1 минуту), что делает его достаточно быстрым для больших объемов ( Более 100000 автомобилей в год). Он обеспечивает отверждение после формования более 95%. Система не содержит растворителей и летучих органических соединений (ЛОС).
«CTQ [критические требования к качеству], определенные Ford, уникальны и никогда ранее не были достигнуты ни в одном коммерческом продукте», - поясняет Дэйв Банк, сотрудник отдела исследований и разработок Dow Polyurethanes. «По этой причине для удовлетворения этих высоких требований требовались новые химические продукты и множество весьма нетрадиционных продуктов».
«Термодинамическое разделение стабильности при хранении и полимеризации в смеси смола / вулканизующий агент дает сухую пасту, которую можно вливать в углеродное волокно без ускорения отверждения и получения сухой, нелипкой формовочной массы», - добавляет Бэнк. «Тем не менее, когда условия формования достигают 150 ° C, химический состав становится« горячим », и отверждение идет быстро». Компания Dow подала 21 заявку на патент, на данный момент получила четыре заявки на эту технологию.
Дополнительные возможности системы VORAFUSE:
- Он стабилен при хранении при комнатной температуре более 50 дней, но обеспечивает мгновенное отверждение при температуре 150 ° C или выше. Он не требует хранения в морозильной камере перед резкой и формованием комплекта, если температура хранения не превышает 40 ° C.
- Его нелипкий химический состав идеально подходит для автоматизированного обращения. Поскольку ему не хватает липкости традиционного препрега, он не вызовет налипания и связанных с этим проблем с роботами и другим оборудованием для автоматизированной обработки.
- Он содержит новую смазку для внутренней пресс-формы (IMR), поэтому переработчики могут формовать 1000 деталей до того, как им придется наносить внешнюю смазку для пресс-формы на поверхности инструмента. Эпоксидная смола обычно противоположна IMR, потому что это очень эффективный клей для металлов.
- Неотвержденный продукт можно переработать в ценные детали путем измельчения и подачи материала обратно в формовочные системы в виде прерывистого армированного волокном компаунда, который идеально подходит для формования сложных геометрических фигур, таких как ребра / выступы. В отличие от обычного эпоксидного препрега и SMC, весь неотвержденный лом можно использовать повторно, что делает материал более экологичным и снижает потери лома, что увеличивает стоимость деталей.
Этап 1. Препрег B, основа
После того, как VORAFUSE был включен в Проект 3.2, IACMI начал работу над автомобильным приложением, которое станет Фазой 1 всего проекта. В состав команды входили Ford, Dow, DowAksa US LLC (Тусон, Азия, американское подразделение DowAksa BV, совместного предприятия 50/50 между Dow Chemical и Aksa Akrilik Kimya Sanayii A.Ş., Чифтликкёй-Ялова, Турция); Университет штата Мичиган (Ист-Лансинг, штат Мичиган, США); Университет Пердью (Западный Лафайет, Индиана, США); Университет Теннесси-Ноксвилл (Ноксвилл, штат Теннеси, США); Continental Structural Plastics (CSP, Оберн-Хиллз, Мичиган, США); и Национальная лаборатория Ок-Ридж (Ок-Ридж, штат Теннеси, США).
На первом этапе исследователи разработали непрерывный (плетеный и не гофрированный) препрег, армированный углеродным волокном, пропитанный эпоксидной смолой. Смола VORAFUSE P6300 была разработана с учетом совместимости с углеродным волокном DowAksa A42 D012 24K со стандартным модулем упругости. Целью команды было использовать препрег из углеродного волокна / эпоксидной смолы для разработки структурных композитных деталей сложной геометрии для замены штампованного металла в высоконагруженных, критически важных для безопасности приложениях на основных конструкциях кузова крупногабаритных транспортных средств.
Для демонстратора технологий:центральная стойка на одной стороне Ford Fusion использовался тестовый автомобиль. Сначала жизнеспособность была оценена с помощью моделирования, а затем были отлиты физические детали и подвергнуты всем необходимым испытаниям, включая полномасштабные аварии транспортных средств. Детали прошли отлично, уменьшив массу на 3 кг с каждой стороны по сравнению с традиционными металлами. Неотвержденный лом был переработан, чтобы сформировать сложные ребристые конструкции колонны. Высокопроизводительный композит позволил уменьшить толщину окружающего листового металла, который затем можно было бы использовать из менее дорогостоящих сплавов, что обеспечило дополнительный вес и снижение затрат.
Пройдя все требования Ford, этот материал впервые в коммерческих целях использовался для изготовления передней панели крыши и закрывающей панели переднего пола автомобиля Ford GT , интенсивно использующего углеродный композит. суперкар.
Неудивительно, что препрег из углеродного волокна / эпоксидной смолы имеет надбавку к стоимости, поэтому лучше всего подходит для автомобилей со значительными требованиями к снижению массы, которые могут доплачивать за возможность значительной экономии веса.
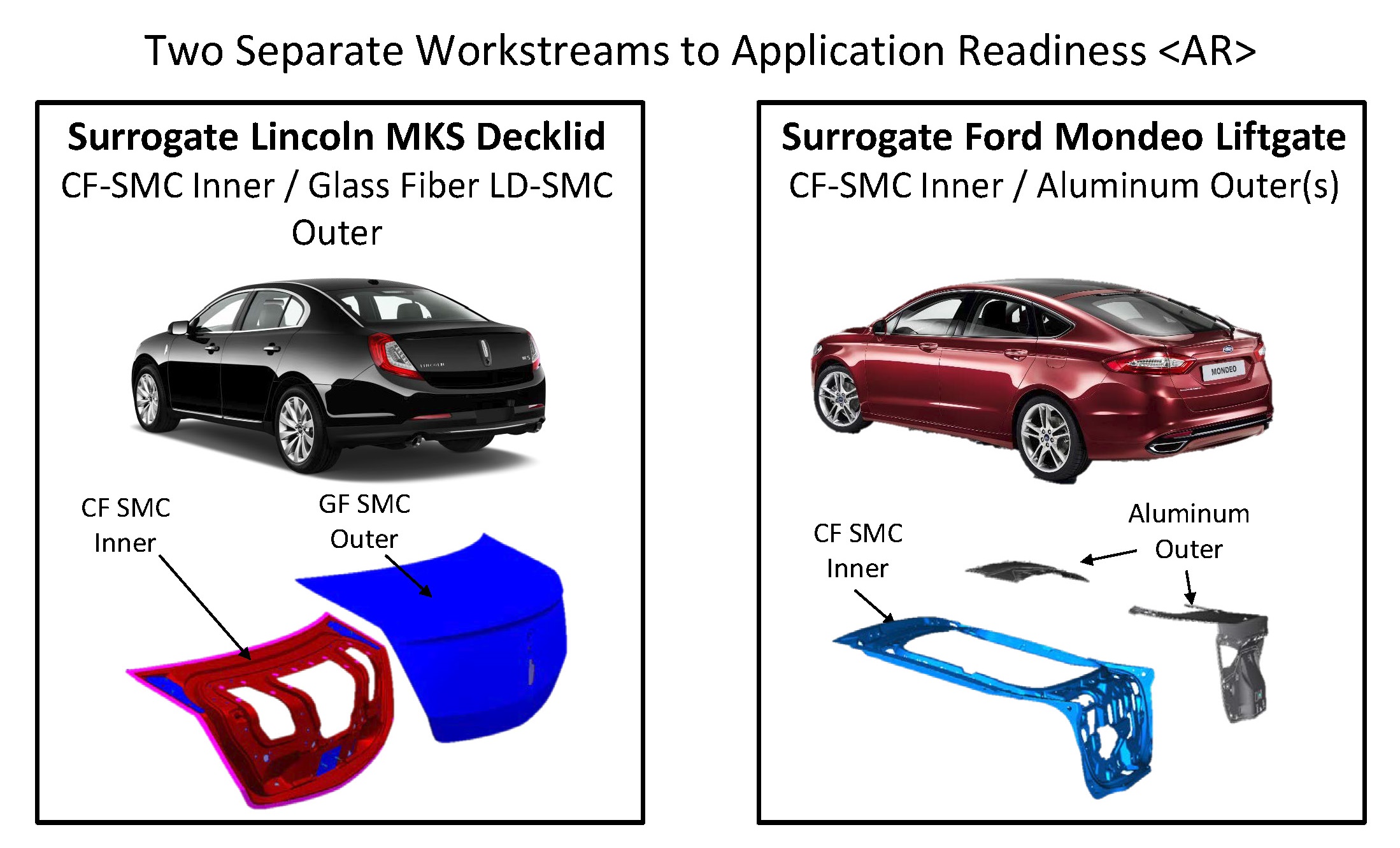
Этап 2 / рабочее направление 1. Полное закрытие крышки для SMC
Опираясь на успехи препрегов, исследователи проекта затем исследовали прерывистый SMC, армированный углеродным волокном, с новой эпоксидной смолой в сложных трехмерных структурах с критически важными для безопасности функциями. В одном демонстраторе углеродное волокно / эпоксидная смола SMC использовалась в качестве внутренней / структурной панели приклеенной крышки багажника (крышки багажника), а в другом демонстраторе она использовалась для внутренней / структурной панели гораздо более крупной и более сложной приклеенной задней двери ( задний люк / дверь с оконным стеклом, электродвигателями стеклоочистителей, фарами и т. д.). В обоих направлениях работы исходные конструктивные ограничения, оборудование, методы соединения и структурные клеи остались неизменными. Были использованы сложные механические мишени с пределом прочности на разрыв более 300 МПа и жесткостью на растяжение более 40 ГПа, что сопоставимо с существующими литыми магнием и алюминием. SMC также требовалась более высокая текучесть, чем у препрега, поэтому была разработана несколько другая марка, VORAFUSE M6400.
Для демонстрации крышки багажника, которая представляла собой постепенное продвижение по сравнению с существующей технологией стекла / SMC, углеродное волокно / эпоксидная смола SMC заменила обычный структурный армированный стекловолокном ненасыщенный полиэфирный SMC для внутренней части крышки на Lincoln MKS прототип автомобиля. Внутренняя панель SMC из углеродного волокна / эпоксидной смолы была приклеена к внешней панели SMC из стекловолокна / полиэстера низкой плотности (LD, 1,25 SG), которая заменила существующую панель SMC из стекловолокна / полиэстера стандартной плотности (1,9 SG). Как старые, так и новые материалы внешней панели были совместимы с классом А. Оригинальные инструменты были повторно использованы для формования внутренних панелей из углеродного волокна / эпоксидной смолы SMC и внешних панелей из стекловолокна / полиэстера. Усадка, хотя и немного различающаяся между обеими системами смол, была достаточно близкой, чтобы не вызывать проблем с подгонкой и отделкой (другими словами, никаких значительных изменений размеров не наблюдалось).
При виртуальном прототипировании связанная сборка подвергалась ряду сложных нагрузок, включая жесткость на кручение, жесткость переднего угла, деформацию водопада и нагрузки на защелку. Затем были отлиты, скреплены и испытаны десятки внутренних и внешних панелей, включая удары сзади со скоростью 89 километров в час. Сборки без проблем прошли как виртуальное, так и физическое тестирование.
Масса деклида уменьшилась на 30% (с 10,5 до 7,33 кг) по сравнению с эталоном. Однако, если бы бюджет позволял переоборудовать внутреннюю панель - которую можно было бы спроектировать более тонкой, учитывая ее более высокие механические характеристики по сравнению с существующей моделью - тогда исследователи подсчитали, что масса могла бы быть уменьшена как минимум на 35% с помощью 2-миллиметровых стенок и даже больше. со стенками толщиной 1,5 мм.
SMC из углеродного волокна / эпоксидной смолы соответствует всем требованиям Ford и теперь может использоваться на коммерческих платформах, хотя его стоимость будет выше, чем при использовании обычного SMC из стекловолокна / полиэстера.
Этап 2 / направление 2:SMC / алюминиевая задняя дверь
Для последнего проекта исследователи обратились к действительно сложному сценарию:замена легкого металла на углеродное волокно / эпоксидная смола SMC для производства гибридной (металл / композит) сборки для более крупных и сложных подъемных дверей на Ford Mondeo пятидверные / хэтчбек тестовые автомобили. Чтобы свести к минимуму изменения в последовательности сборки транспортного средства, исследователи разработали сборку, которая будет добавлена к кузову в белом (BIW) перед электрофоретической обработкой ржавым покрытием (электронным покрытием) и связанными циклами покраски и запекания.
Углеродное волокно / эпоксидная смола SMC заменила магний для структурных / внутренних панелей, которые были связаны с существующими алюминиевыми внешними панелями. Поскольку для изготовления композитной панели необходимо было создать новую оснастку, деталь была переработана. Толщина панели варьировалась в соответствии с требованиями к жесткости / прочности и добавлением оребрения. Кроме того, в местах крепления газовых стоек, защелок, петель и замков использовалась металлическая арматура, которая делала композитную панель несколько толще - что позволяло пространство в упаковке.
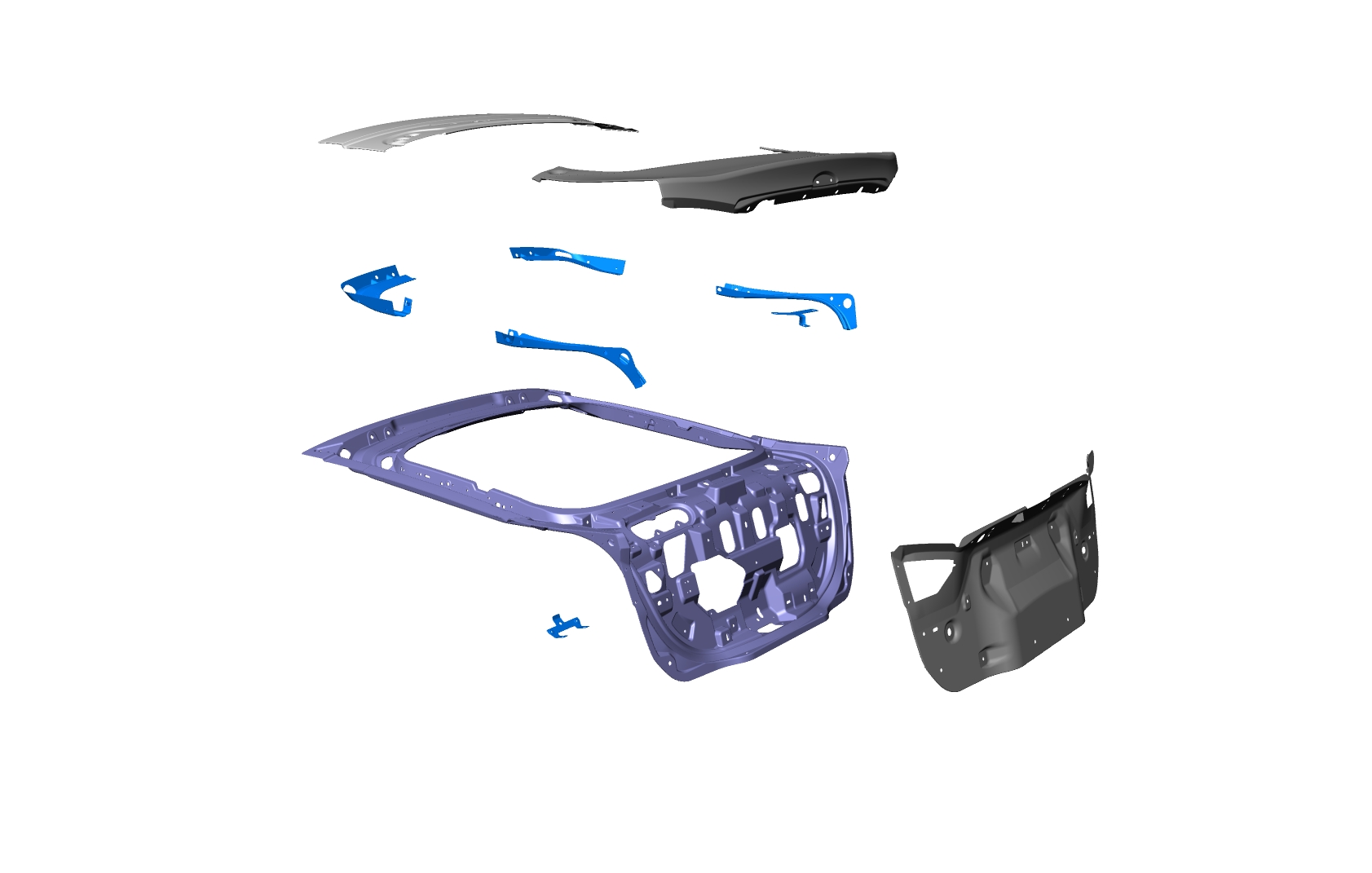
Покомпонентное изображение SMC / алюминиевой задней двери (с металлической фурнитурой) для пятидверной версии Ford Mondeo / хэтчбека. Источник | Ford Motor Co.
К этим сборкам из разных материалов были предъявлены строгие требования, включая скручивающие и изгибающие нагрузки, поперечную устойчивость, коррозионную стойкость, долговечность и испытания на удар сзади. Они также должны были соответствовать строгим требованиям к стабильности размеров в отношении полей и гладкости.
Хотя гибридная система легко соответствовала большинству требований, возникали проблемы с подгонкой и отделкой из-за несоответствия коэффициента линейного теплового расширения (CLTE) между композитными внутренними панелями и алюминиевыми внешними панелями, что приводило к накоплению остаточных напряжений в клеевых соединениях и деформации панели после охлаждения. вниз. Последующая работа с командой моделирования Университета Пердью была сосредоточена на улучшении прогнозов модуля, прочности и кинетики отверждения эпоксидного клея 1K (выбранного из-за его способности выдерживать температуры электронного покрытия) в надежде на обратное проектирование клея, который работал бы лучше. Искажение уменьшилось на порядок, но немного не попал в цель. Возможны несколько решений:можно попробовать клей 2K / отверждения при комнатной температуре или индукционного отверждения или разработать новый высокотемпературный клей. В долгосрочной перспективе замена алюминия на композит из углеродного волокна на внешней панели устранила бы проблему, равно как и отключение задней двери и добавление ее позже в процессе сборки автомобиля. Однако оба варианта увеличивают стоимость.
Проект 3.2 сейчас завершается, но в результате были получены интересные технологии, некоторые из которых - препрег стойки B и колпак SMC - готовы к коммерческому использованию, а некоторые указывают на области, в которых требуется дальнейшая работа.
«Работа с IACMI и нашими промышленными и академическими партнерами позволила нам гораздо глубже погрузиться в технологии, начиная с первого директора, развивать фундаментальную науку и использовать гораздо более широкую базу знаний, чем мы могли бы сделать в одиночку», - резюмирует руководитель проекта 3.2 Патрик Бланшар. ведущий технический специалист - передовые полимерные системы, исследования и инновации Ford. «Мы с нетерпением ждем выявления новых коммерческих возможностей и исследований и разработок для продолжения сотрудничества с нашими партнерами из IACMI».
Смола
- Устройства из углеродного волокна для вашего дома
- Топ-3 применения 3D-печати из углеродного волокна на производстве
- Инновационные способы использования углеродного волокна
- Углеродное волокно в автомобильных приложениях
- 5 забавных вариантов использования листов из углеродного волокна
- Для чего используется обертка из углеродного волокна?
- Материалы:полипропилен, армированный стеклом и углеродным волокном, для автомобилей
- Hexion представляет двухкомпонентный эпоксидный раствор для производства аэрокосмических композитов
- Покрытие моторной яхты впечатляет углеродным волокном / эпоксидной смолой
- Серия, разработанная для автомобильной производственной линии