Ребра Wing of Tomorrow:одноразовые, термопластичные, уплотнение OOA
Программа Airbus «Крыло завтрашнего дня» (WOT), запущенная в 2015 году, в течение последних шести лет изучала более конкурентоспособные по стоимости, высокопроизводительные материалы, технологии производства и сборки для узкофюзеляжных крыльев коммерческих самолетов (см. CW Предыдущее освещение программы WOT).
По словам Арнта Оффринги, директора GKN Aerospace Global Technology Center, Нидерланды (Хогевен), Компания GKN Aerospace (Бристоль, Великобритания) очень активно участвовала в программе WOT, включая разработку демонстрационного лонжерона крыла, изготовленного методом литья под давлением (RTM), и четырех алюминиевых нервюр крыла. Другой технологический демонстратор, недавно представленный GKN Aerospace, включал разработку как конкурентоспособного по стоимости ребра из термопластичного композитного материала, так и инновационной модульной прессовой системы для одноразового производства вне автоклава (OOA) для его производства.
Переход к термопластам
В 2018 году компания GKN Aerospace начала внутреннее обсуждение материалов и производственных технологий, которые можно было бы использовать для производства пяти демонстраторов
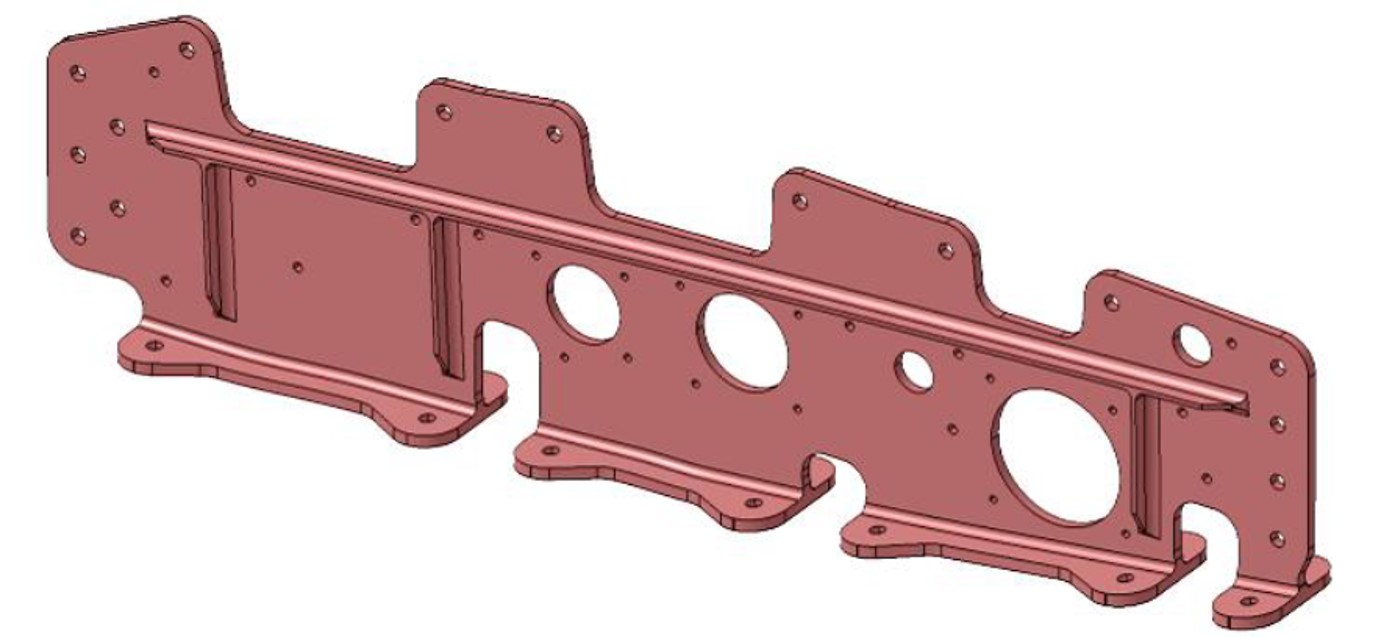
Проектирование нервюры. Чтобы получить тонкую и легкую деталь, конструкция ребра (вверху) включает технологию стыкового соединения GKN (внизу) с литыми под давлением наполнителями жесткости (посередине, показаны зеленым цветом).
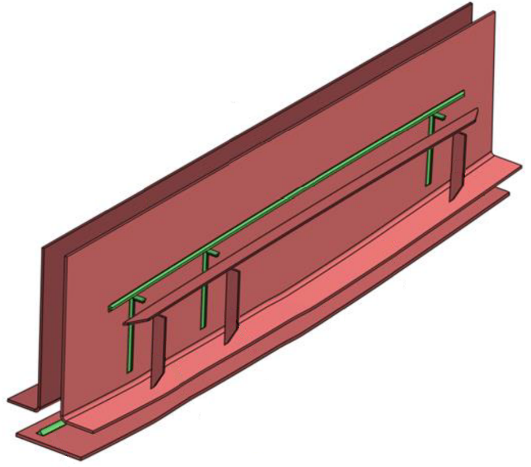
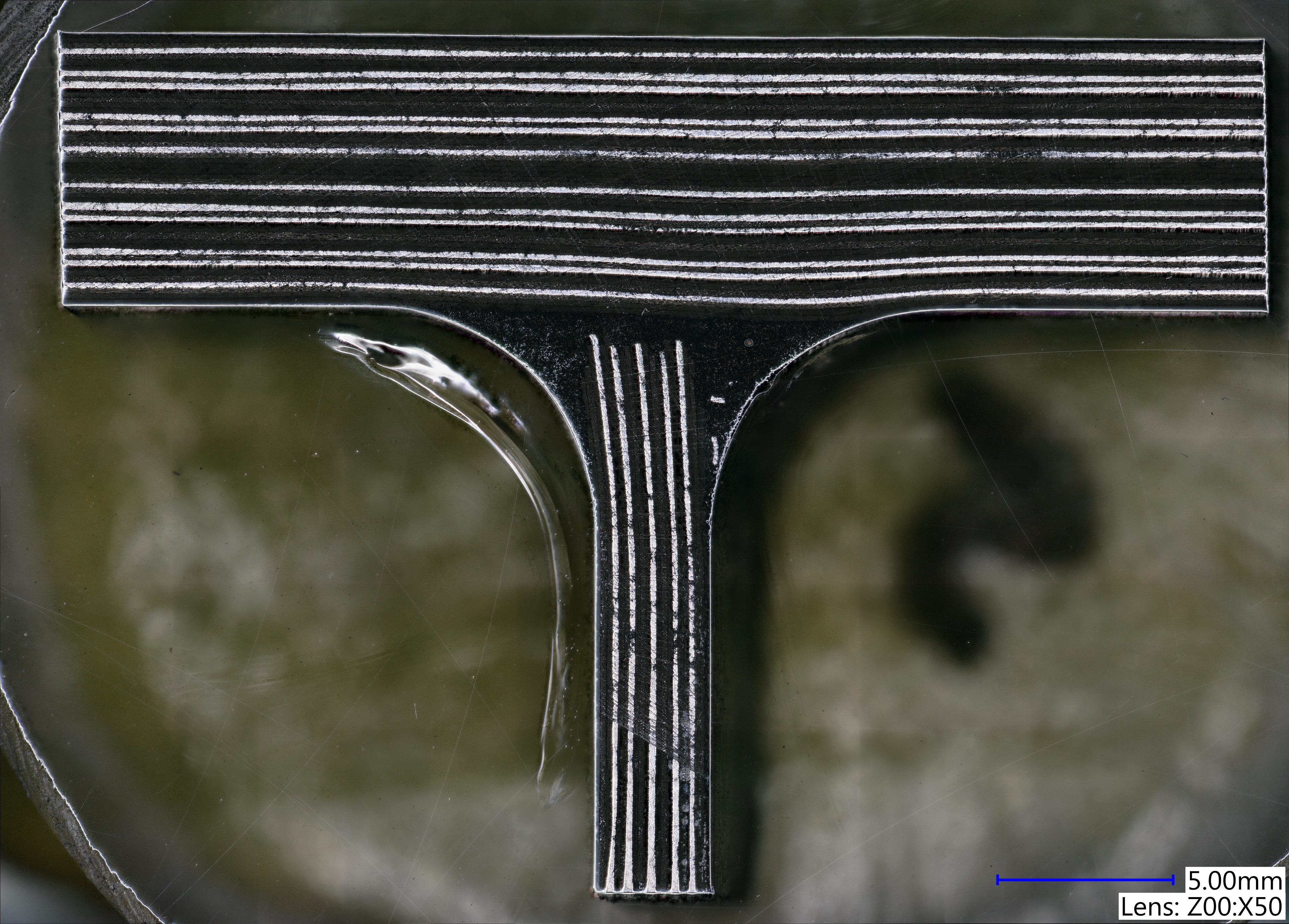
ребра для программы WOT. GKN Aerospace сравнила несколько вариантов материалов, включая термореактивные и термопластичные композиты. Алюминий, традиционный материал для нервюр коммерческих самолетов, был выбран для производства четырех больших внутренних нервюр, но для меньшего внешнего выступа компания решила изучить композитный вариант. Оффринга отмечает, что, поскольку демонстрационный образец WOT будет представлять собой композитное крыло, разработка композитной нервюры, которая может конкурировать с алюминием, является логическим шагом.
«Составные нервюры на композитном крыле выгодны по нескольким причинам», - говорит он. «Во-первых, использование композитов с композитами означает, что нет разницы в тепловом расширении между материалами, как это было бы с металлической нервюрой на композитном крыле или наоборот. Во-вторых, у вас не будет проблем или опасений по поводу коррозии. Композиты также означают уменьшенный вес. И последнее, но не менее важное:использование композитов упрощает проверку ».
Оффринга объясняет, что типичные металлические нервюры требуют визуального осмотра человеком после сборки окончательного крыла. Однако из-за расположения нервюр внутри крыла это означает, что в нижней части крыльев необходимо будет вырезать большие эллиптические люки, чтобы люди могли войти в крыло и осмотреть их. «Если вы перейдете на составное ребро, у вас будет меньше усталости в ребрах и меньше потенциальных усталостных трещин, которые вам придется проверять. Осмотр становится намного проще и менее интенсивным, и вам больше не нужно встраивать люки в обшивку крыльев. Это будет сплошная крылатая шкура », - говорит он.
Снижение веса, устойчивость к коррозии и менее инвазивный контроль можно получить как за счет термореактивных, так и из термопластичных композитов. «Мы провели внутреннее исследование и посмотрели на вес, стоимость и индустриализацию, и после сравнения различных технологий был сделан выбор в пользу термопластов, потому что они имели наибольший потенциал и лучшее экономическое обоснование с точки зрения затрат», - говорит Оффринга. .
Учитывая его близость к британскому технологическому центру крыла в Филтоне, принадлежащему Airbus, где будут проходить испытания демонстратора WOT, британский филиал GKN Aerospace в Бристоле является основным центром работы компании по WOT. Однако, учитывая опыт GKN Aerospace Netherlands в области термопластов с тех пор, как она была Fokker Technologies, две команды GKN Aerospace объединили свои усилия для создания демонстратора ребер. «Дизайн был выполнен в Великобритании, но разработка производства велась в Нидерландах, так что это было действительно хорошее сотрудничество между различными командами GKN Aerospace», - говорит Оффринга.
Сью Партридж, глава WOT в Airbus, отмечает:«Сотрудничество с партнерами - важный аспект программы Wing of Tomorrow. Объединив наши ресурсы, мы можем продвигать решения, которые используют возможности обеих наших организаций для достижения лучших результатов ».
Для ребер WOT, поставленных Airbus, GKN Aerospace использовала ленты APC из углеродного волокна / полиэфиркетонекетона (PEKK-FC) компании Solvay (Брюссель, Бельгия) на основе быстро кристаллизующегося состава Novaspire PEKK-FC (FC). Оффринга отмечает, что легкоплавкий углеродное волокно / полиарилэфиркетон (PAEK) Toray Advanced Composites (Морган Хилл, Калифорния, США) также оценивается как вариант для будущих структур ребер.
Разработка нервюры крыла нового поколения
На типичном узкофюзеляжном крыле самолета более 20 нервюр. Демонстрационная нервюра из термопластичного композита является 14-й на крыле демонстратора; другие продемонстрируют альтернативные материалы и процессы.
По словам Оффринги, ребра из термопластичного композита часто изготавливаются методом штамповки для небольших самолетов. Однако GKN Aerospace исключила традиционную штамповку в качестве опции для нервюры WOT, поскольку крылья коммерческих самолетов, даже для узкофюзеляжных самолетов, таких как демонстратор WOT, подвергаются очень высоким нагрузкам сжатия и растяжения.
«Если бы вы собирались штамповать ребро из термопласта в традиционном смысле, тогда вам нужно было бы сделать очень толстое ребро с толстым полотном, чтобы сделать его прочнее и выдержать действующие на него силы», - говорит Оффринга:и это нежелательно с учетом требований к снижению веса. Кроме того, штамповка не может создать двухсторонний компонент нижнего фланца на нервюре, где эта часть соединяется с нижней обшивкой крыла; потребуется изготовить дополнительный компонент и прикрутить его к остальной части выступа. GKN Aerospace нуждался в производственном процессе, который обеспечивал бы большую гибкость при проектировании, которое разработала команда.
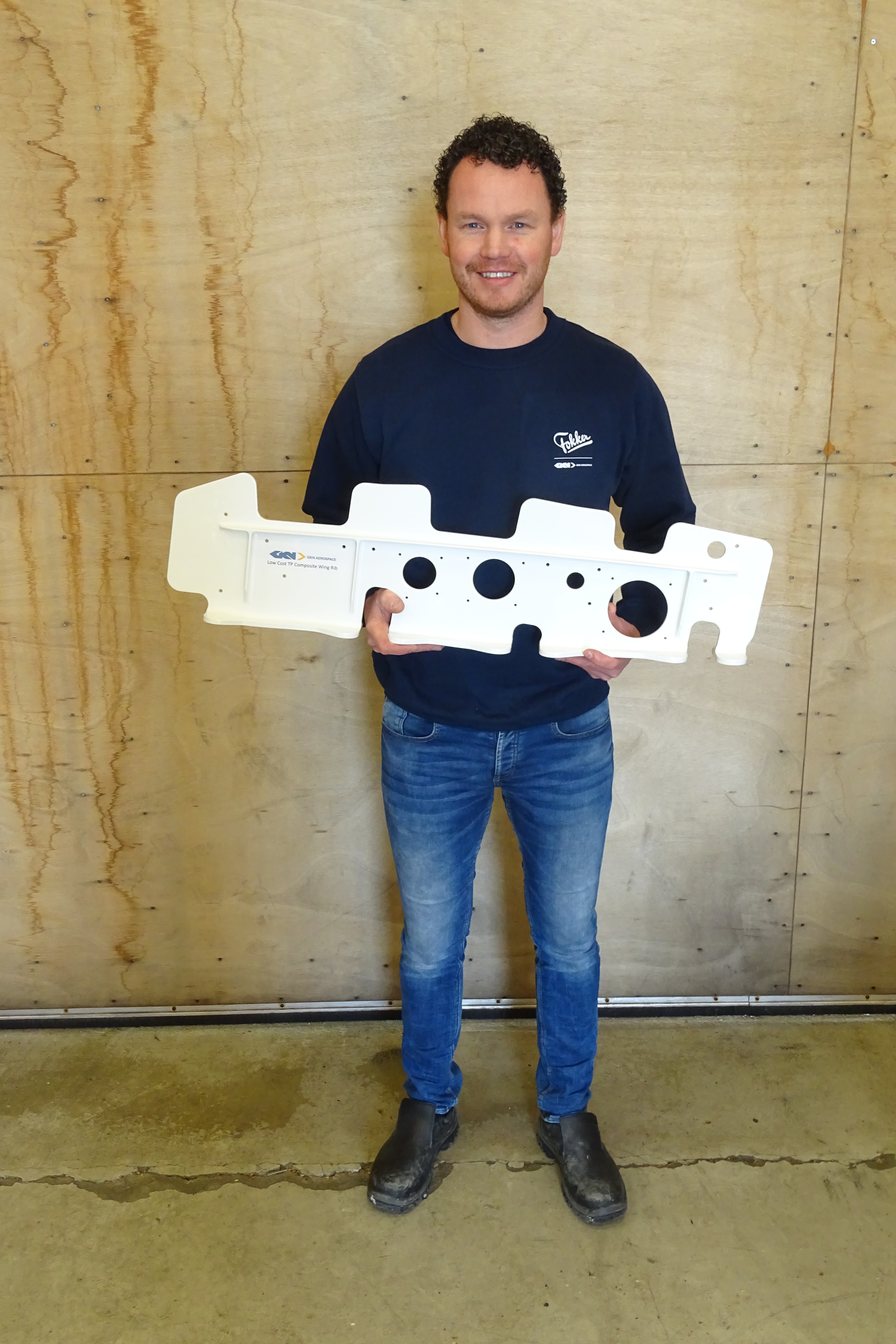
Ребро из термопласта GKN Aerospace длиной 90 сантиметров и высотой 24 сантиметра имеет вертикальную перемычку и двунаправленный фланец толщиной 8 миллиметров, выступающий из нижней части выступа. Чтобы соответствовать требованиям по весу, толщина полотна составляет всего 7 миллиметров. Чтобы предотвратить коробление и увеличить жесткость, перемычка усилена элементами жесткости толщиной 3 миллиметра с использованием технологии стыкового соединения GKN Aerospace, в которой используются плоские заготовки жесткости и литьевые «наполнители» для создания прочного непрерывного соединения (см. «Термопласты»). первичные авиационные конструкции делают еще один шаг вперед », чтобы узнать об использовании этой технологии на панели фюзеляжа Gulfstream, изготовленной из углеродного волокна / лент PEKK-FC компании Solvay).
«Мы знали, что если мы сможем сделать эту форму из композитных материалов и сделать ее прочной, то у нас будет очень легкая конструкция с требуемым снижением веса. Но проблема заключалась в том, как сделать такую сложную форму рентабельно и по высоким ценам? Именно на это мы и направили наши усилия, чтобы создать этот новый продукт », - говорит Оффринга.
Одноэтапное производство OOA
Этот процесс основан на технологии, которую GKN Aerospace ранее использовала для проекта TAPAS (доступная первичная конструкция самолета из термопласта), а также для разработки панели фюзеляжа для Gulfstream, в которой используется технология стыковых соединений компании. Для ребра WOT компания GKN Aerospace разработала одноэтапный процесс консолидации OOA. «Мы подняли нашу предыдущую работу на новый уровень, впервые выйдя из автоклава», - отмечает Оффринга.
Сначала однонаправленные (UD) термопластические ленты разрезаются до нужной ширины, и используется ламинатор для предварительного формования плоских элементов в две L-образные заготовки полотна. Заготовки перемычки, плоская заготовка для фланца и меньшие заготовки и литые под давлением элементы-наполнители, составляющие стрингеры, загружаются в инструмент, который помещается внутри модульного пресса для совместной консолидации, аналогичного прессу для литья под давлением. (RTM) нажмите. Пресс закрывается, и система баллонов используется для создания давления как в горизонтальном, так и в вертикальном направлениях, имитируя давление в автоклаве. Интегрированная система резистивного нагрева нагревает композит на короткое время до температуры плавления перед охлаждением для отверждения.
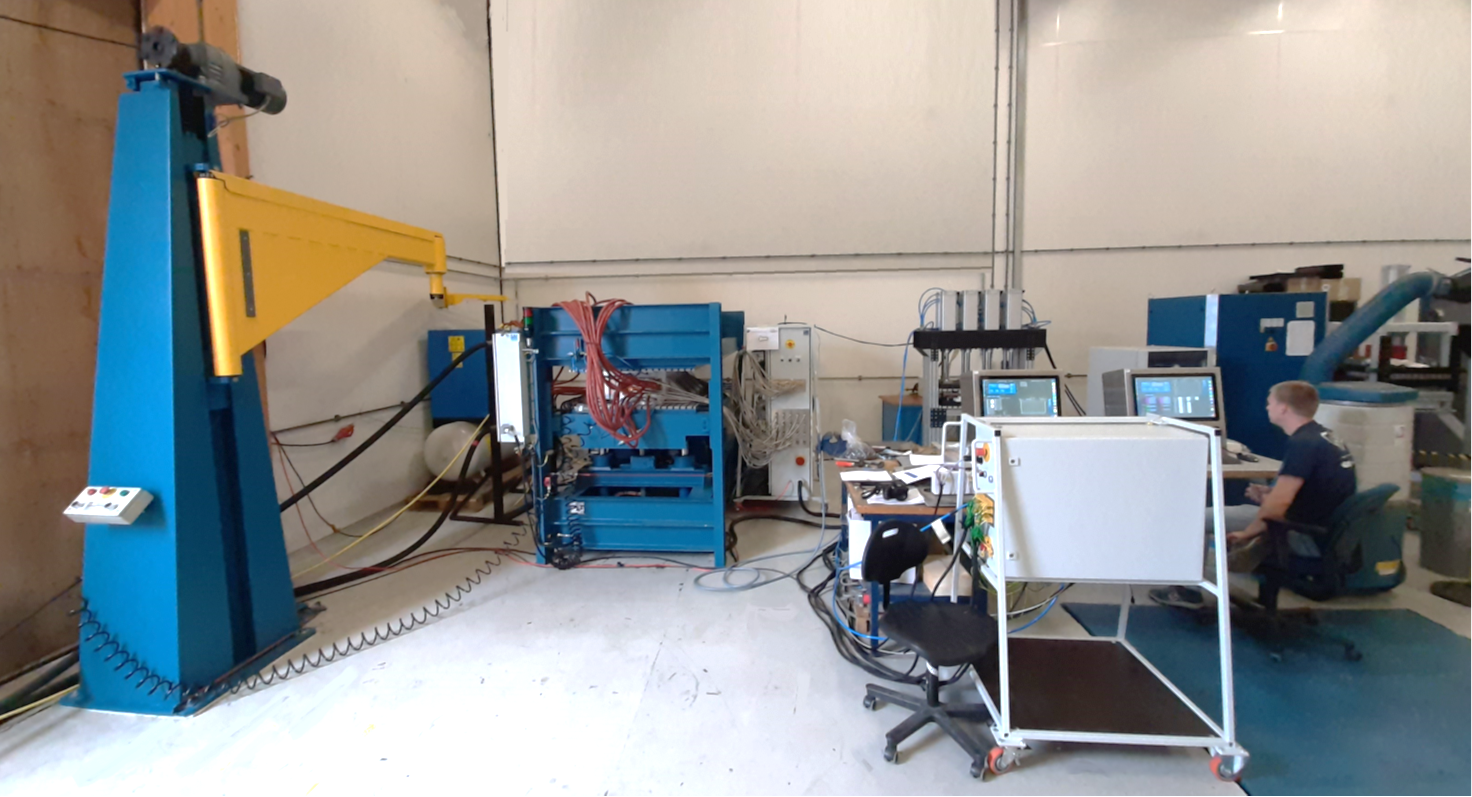
«Большую часть усилий мы направили на настройку и оптимизацию инструментария», - говорит Оффринга. Система спроектирована как модульная; инструмент можно заменить, чтобы разместить ребра с другими размерами или другие типы деталей, сохраняя при этом ту же систему нагрева и охлаждения. Хотя эти ребра не нужны, пресс, разработанный GKN Aerospace в технологическом центре, может работать с деталями длиной до 6 метров, которые также могут включать другие панели или балки.
Система управления технологическим процессом играет ключевую роль при переработке термопластов. Термопласты плавятся при более высоких температурах, чем термореактивные, и их необходимо охлаждать в рамках контролируемого последовательного процесса, чтобы минимизировать коробление и максимизировать стойкость. «Очень важно контролировать точный процесс от начала до конца», - говорит Оффринга. «Управление температурным режимом цикла нагрева очень важно». (см. врезку «Проблемы формовки термопластов (TP)» в этой статье, чтобы получить более подробную информацию о проблемах и важности контроля процесса при использовании термопластов).
Специальные приспособления используются для того, чтобы тонкие интегрированные ребра жесткости легко снимались с инструмента. Извлеченная деталь имеет почти чистую форму, а затем обрезается, чтобы сформировать готовую деталь. От подачи инструмента до его извлечения весь процесс занимает около 45 минут. Это означает, что с помощью одного пресса можно изготовить около 15 нервюр крыла за восьмичасовую смену.
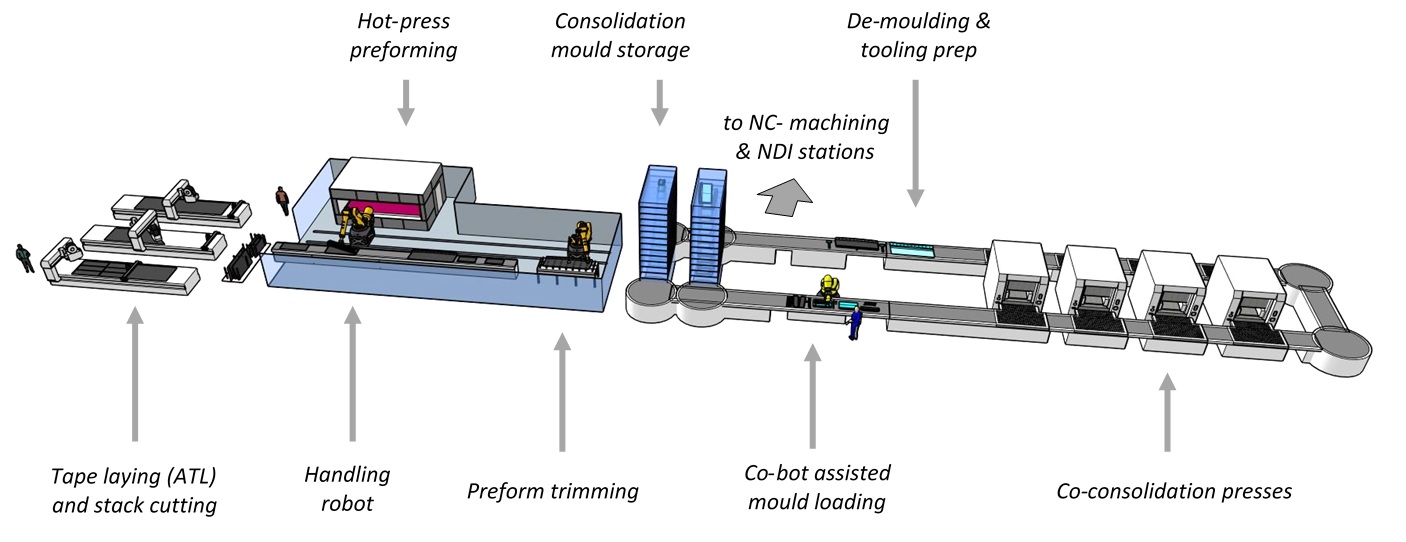
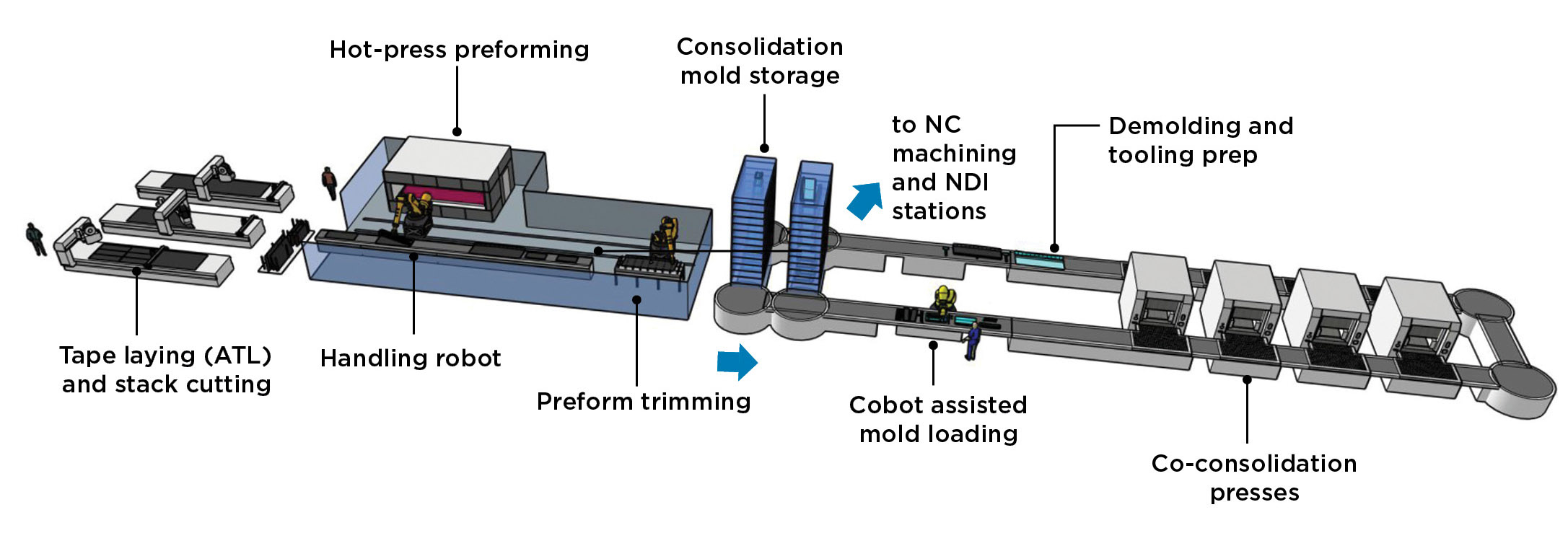
«В итоге получается простой производственный процесс», - отмечает Оффринга. «Мы делаем много вещей одновременно:объединяем преформы разной формы, создаем нижнюю часть ребра, чтобы иметь двунаправленный фланец, и в то же время мы повышаем жесткость полотна с помощью технологии стыкового соединения. Однако в конечном итоге мы берем все элементы материала, помещаем их в инструмент и создаем одну однородную деталь за один этап обработки ».
Тестирование, доставка и не только
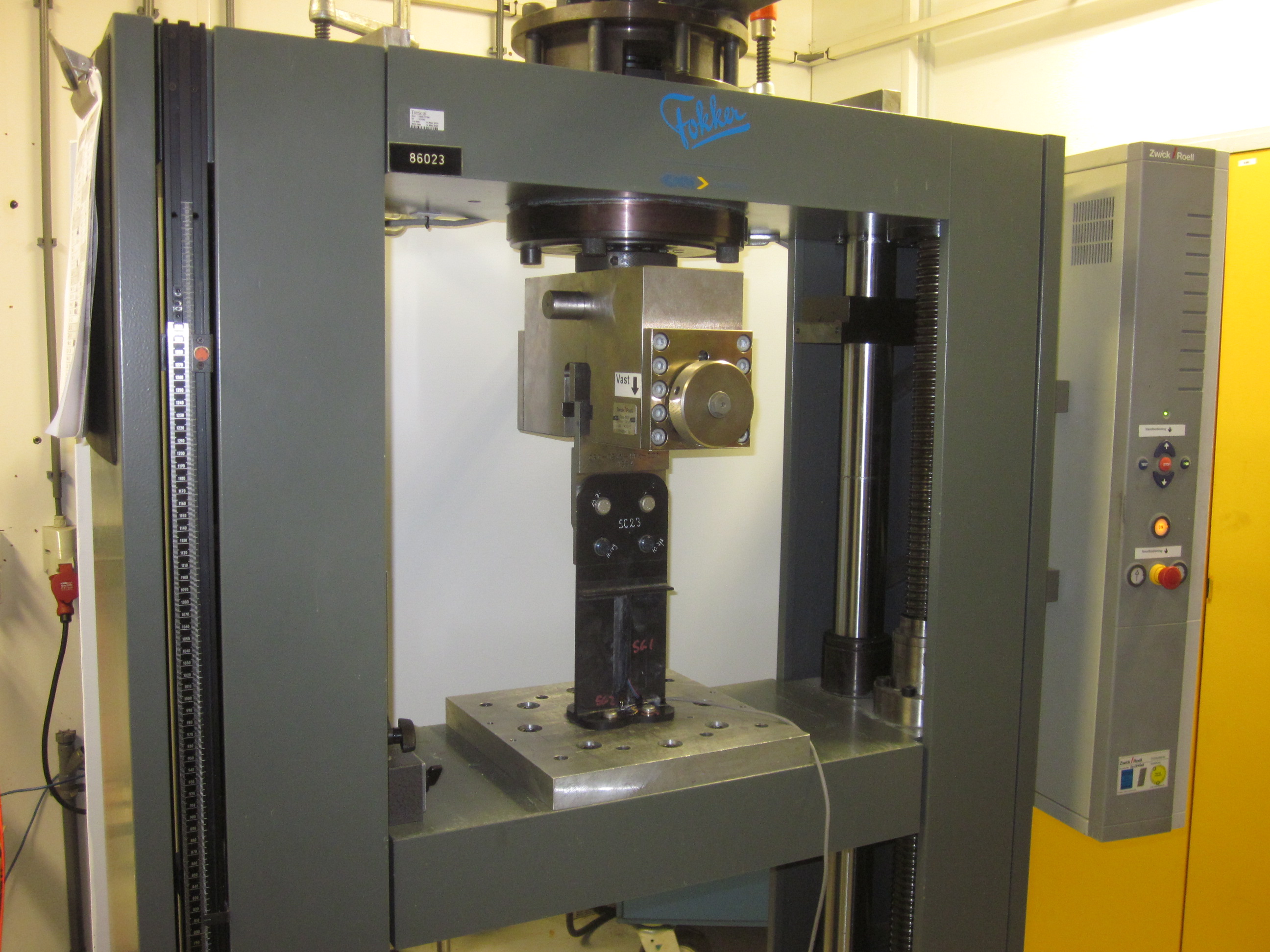
Тестирование. Компоненты были испытаны на соответствие требованиям прочности на растяжение и сжатие на объектах GKN в Айл-оф-Уайт и Хогевен.
В конце 2019 года подкомпоненты ребер были испытаны на объектах GKN Aerospace на острове Уайт и в Хоогевене, и Offringa заявляет, что они прошли требования к растягивающей и сжимающей нагрузке «с большим отрывом». Он добавляет:«Он прочный, жесткий, его легко производить. Эта концепция оказалась именно такой, как мы и надеялись ». По сравнению с алюминиевой версией, Offringa заявляет, что версия из термопластичного композита обеспечивает значительную экономию веса и конкурентоспособную стоимость.
Компания поставила Airbus три нервюры, одно из которых будет собрано и испытано на демонстраторе WOT. GKN Aerospace продолжает работать над оптимизацией процессов и материалов для коммерческих аэрокосмических нервюр, как для Wing of Tomorrow, так и для последующих.
Смола
- Армированный непрерывным волокном термопластический композит, полностью сделанный из природных ресурсов
- Solvay увеличивает емкость термопластичного композитного материала
- Fraunhofer вводит в эксплуатацию автоматизированные производственные ячейки Engel для НИОКР термопластичных компо…
- Институт конструкций и дизайна DLR увеличивает зрелость термопластичных композитных конструкций фюзеляжа
- Solvay завершает установку объекта в Южной Каролине, увеличивает емкость термопластичного композита в США
- INEOS Styrolution для создания производственной площадки для термопластичного композита StyLight
- Xenia представляет термопластичные композитные компаунды CF / PP
- Труба из термопластичного композитного материала на подъеме в глубоком море
- NIARs NCAMP, квалифицирующий термопластический композит TenCate
- TenCate празднует сборку консорциума термопластичных композитов в Бразилии