Простейший станок с ЧПУ с минимальным количеством деталей — лазерный гравер своими руками
<основной класс="главный сайт" id="главный">
В этом уроке я покажу вам, как я построил простейший станок с ЧПУ с минимальным количеством деталей и без использования 3D-принтера. Вот так. Я использую 3D-принтеры для большинства своих последних проектов, потому что, конечно же, они отлично подходят для прототипирования, поскольку мы можем легко сделать с ними любую форму, какую захотим. Однако не у всех есть 3D-принтер, поэтому я хотел показать вам, что мы можем делать вещи даже без помощи 3D-принтеров или других станков с ЧПУ.
Вы можете посмотреть следующее видео или прочитать письменный учебник ниже.
Обзор
Я покажу вам, как я построил этот станок с ЧПУ, используя только один электроинструмент, дрель и несколько ручных инструментов. Материал, который я использовал для этой сборки, — это плита МДФ толщиной 8 мм, которая на самом деле довольно прочная и, вероятно, более жесткая, чем материал PLA, напечатанный на 3D-принтере, и в то же время с ней легко работать.
В этом видео я буду использовать этот станок с ЧПУ в качестве лазерного гравера, а в будущем видео я планирую заставить его работать в качестве перьевого плоттера.
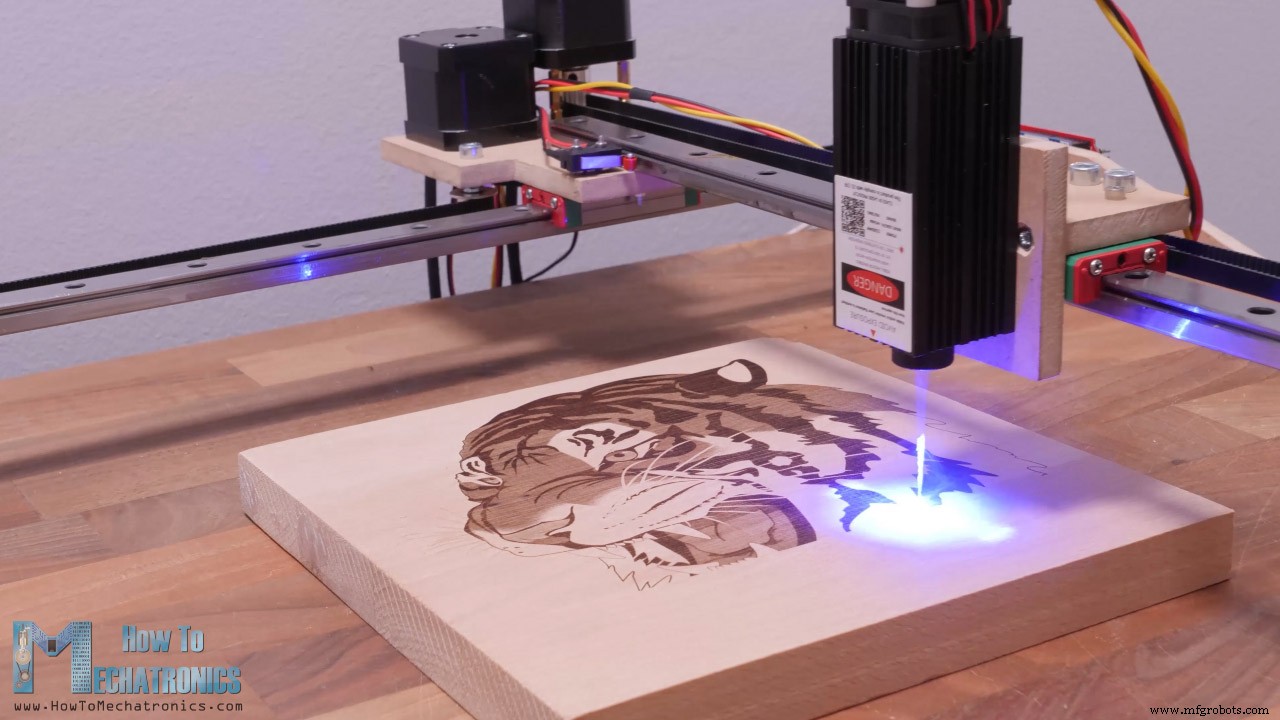
Очевидно, что такая конструкция станка не может обеспечить большую жесткость, поэтому мы не можем использовать его в качестве фрезерного станка с ЧПУ или фрезерного станка. Хотя, если бы мы подключили более мощный лазер, мы могли бы использовать его для резки различных материалов, таких как эта плита МДФ, которую мы используем здесь, или другой тип деревянных досок, и с довольно хорошей точностью.
Рабочая зона довольно большая 390 на 360 мм, а уровень детализации, который может произвести этот лазерный гравер, впечатляет. Честно говоря, я был удивлен, насколько хороши получились гравюры.
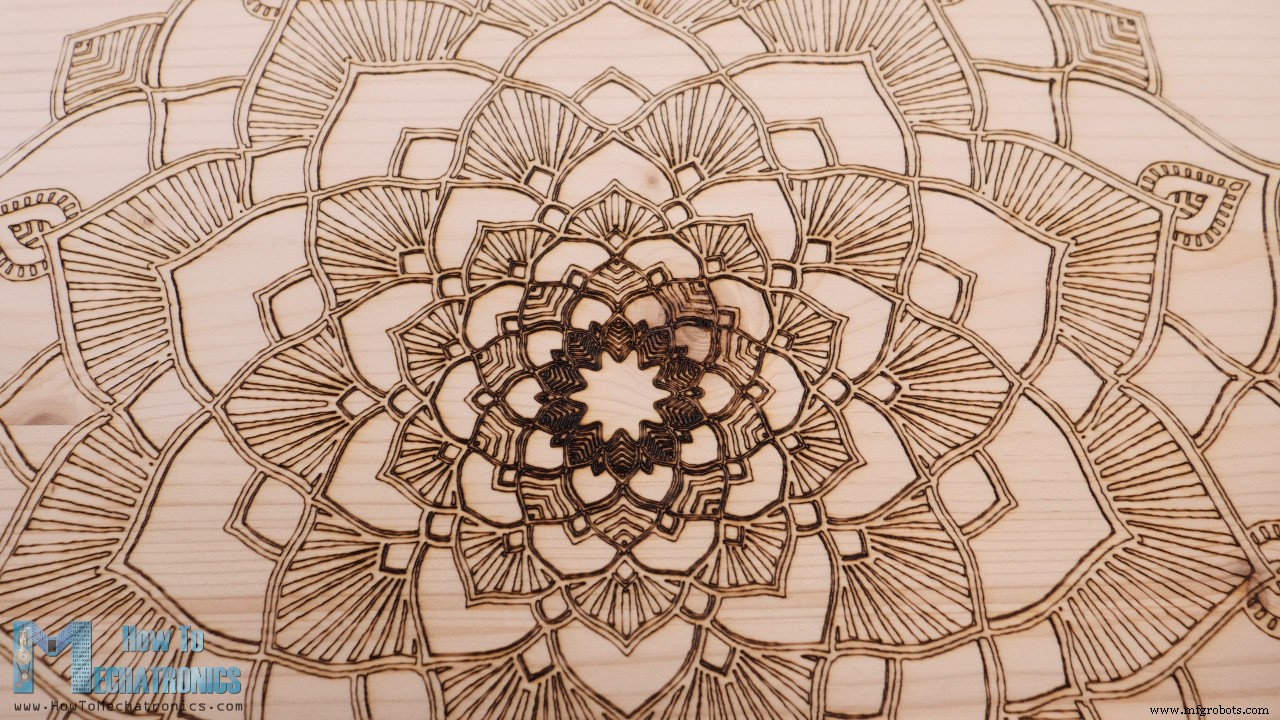
Мозгом этого станка с ЧПУ является плата Arduino UNO в сочетании с щитом ЧПУ, но более подробная информация об этом, а также о том, как подготовить чертежи или изображения для лазерной гравировки, создать G-коды и управлять станком с помощью бесплатного открытого исходные программы, чуть позже в видео.
3D-модель лазерного гравировального станка с ЧПУ своими руками
Я начал с проектирования машины с помощью SOLIDWORKS for Makers. Двумя основными компонентами этого станка с ЧПУ являются линейные направляющие MGN15H вместе с соответствующими скользящими блоками.
Для привода блоков или двух осей мы используем два шаговых двигателя NEMA 17 и несколько подходящих шкивов GT2 и зубчатые ремни. Для соединения всего вместе мы используем плиту МДФ толщиной 8 мм, а для возврата машины в исходное положение — два концевых микровыключателя.
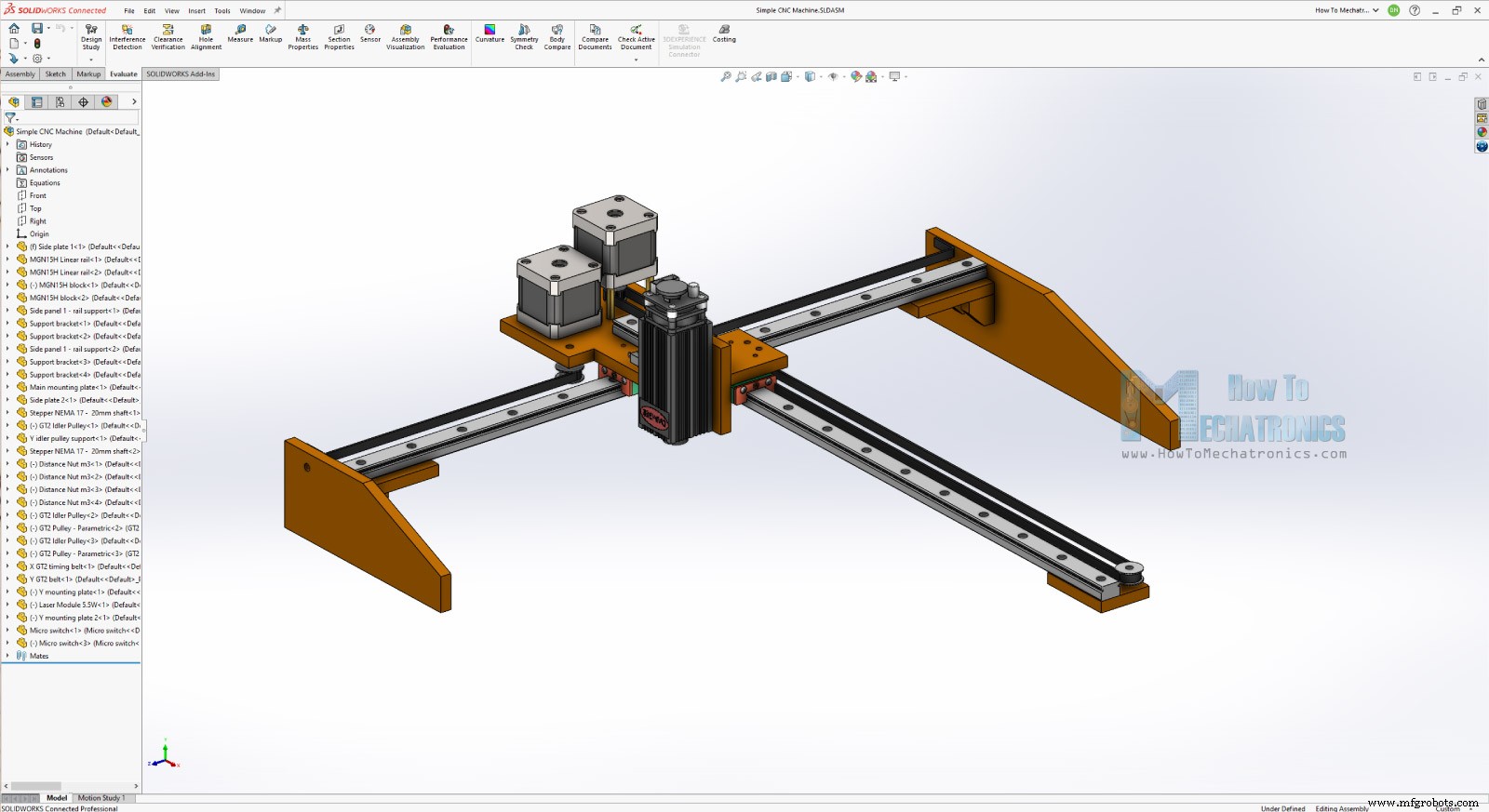
Вот и все, станок с ЧПУ с минимальным количеством деталей.
Скачать 3D-модель можно здесь:
Вы можете найти и скачать эту 3D-модель, а также изучить ее в своем браузере на Thangs:
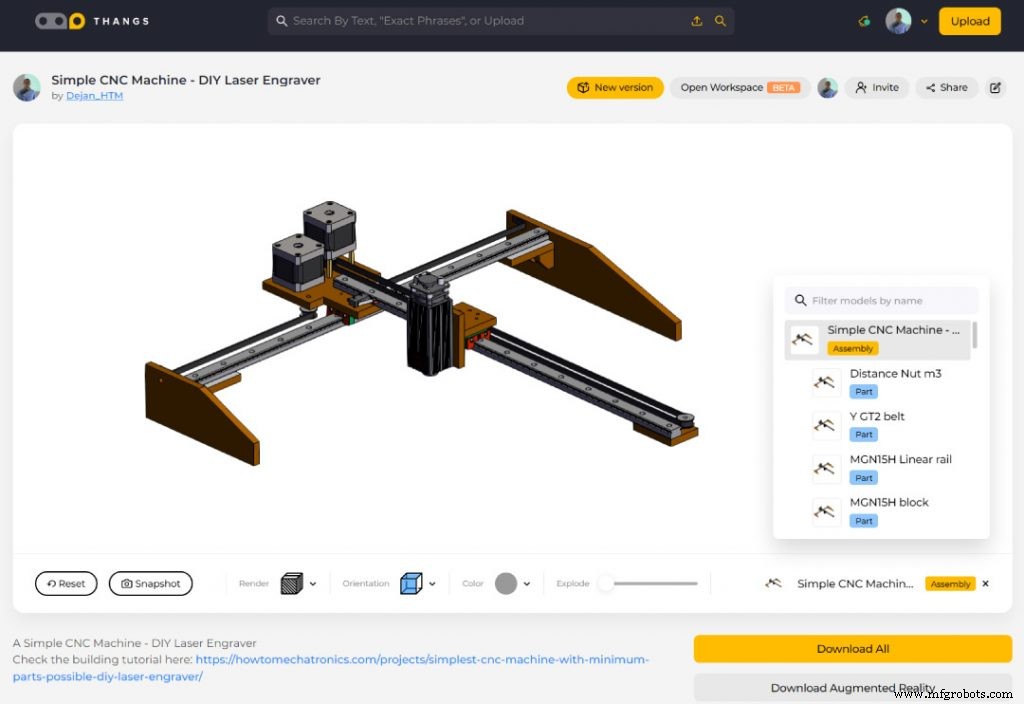
Загрузите 3D-модель сборки с Thangs.
Спасибо Thangs за поддержку этого руководства.
Вот рисунок центральной монтажной пластины:
См. также:Станок для резки пенопласта с ЧПУ Arduino
Сборка машины
Итак, теперь мы можем начать сборку машины. Вот список компонентов, необходимых для сборки этого станка с ЧПУ своими руками. Список компонентов электроники можно найти ниже в разделе принципиальных схем статьи.
- Линейная направляющая MGN15H …………………………… Amazon / Бангуд / Алиэкспресс
- Шаговый двигатель — NEMA 17 ………….…
- Ремень GT2 + зубчатый шкив…………………… Amazon /
- Натяжной шкив GT2 ………………………………… Amazon / Бангуд / Алиэкспресс
- Распорные гайки …………………………….…….. / Banggood / Алиэкспресс
- Набор болтов и гаек …………………………… Amazon / Бангуд / Алиэкспресс или в местном хозяйственном магазине + винты с плоской головкой 3x16 мм
- Винты M2x20x2, M3x12x20, M3x16x6, M5x25x5, винты 3x16x20x20
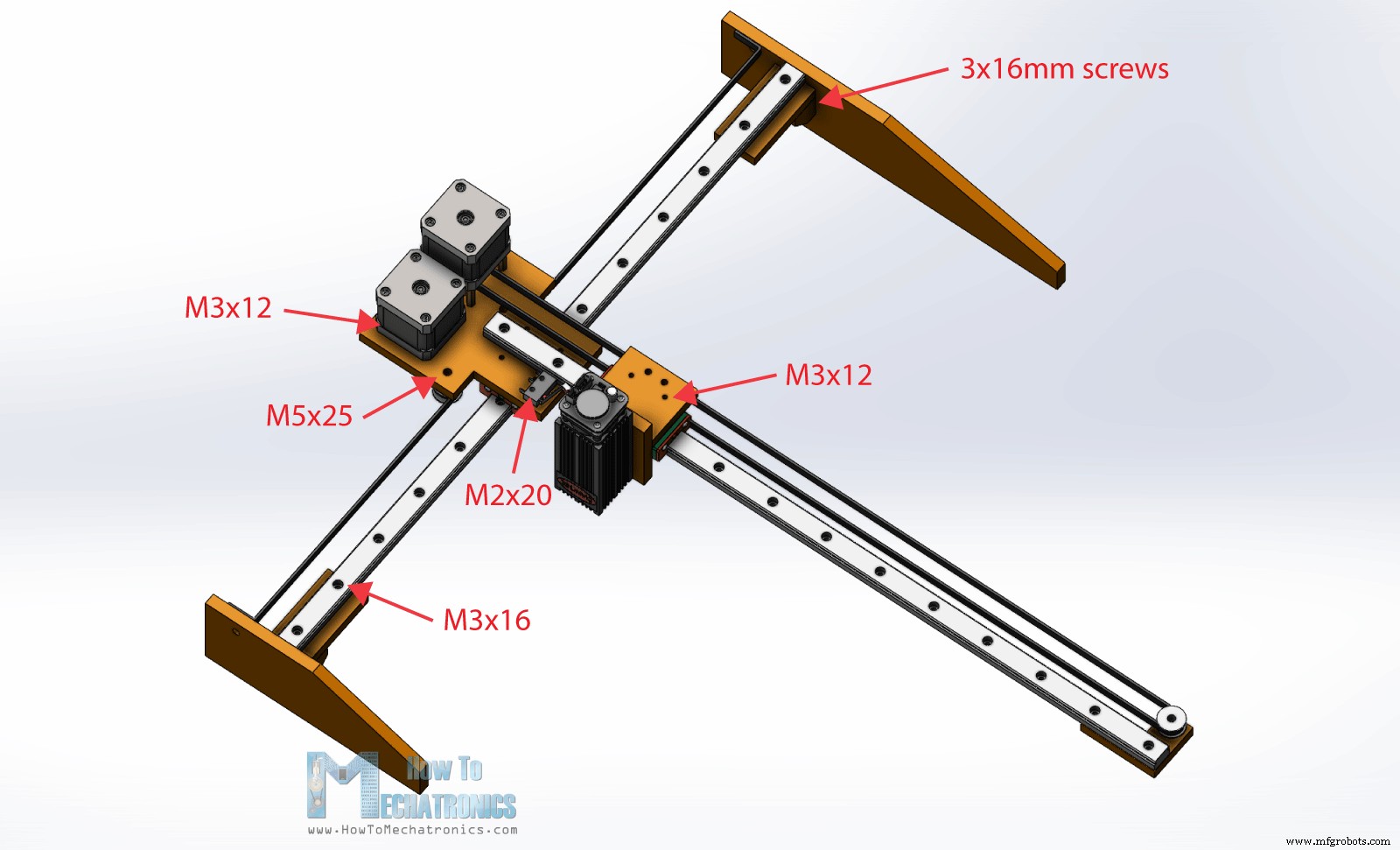
Вот плита МДФ толщиной 8 мм, которую я буду использовать, и по чертежам, которые я взял из 3D-модели, теперь я буду нарезать куски по размеру.
Связанный:Самодельный перьевой плоттер с автоматической сменой инструмента | Чертежный станок с ЧПУ
Для этого я использовал самый простой способ:карандаш для разметки мест, где мне нужно было вырезать, и ручную пилу для их вырезания.
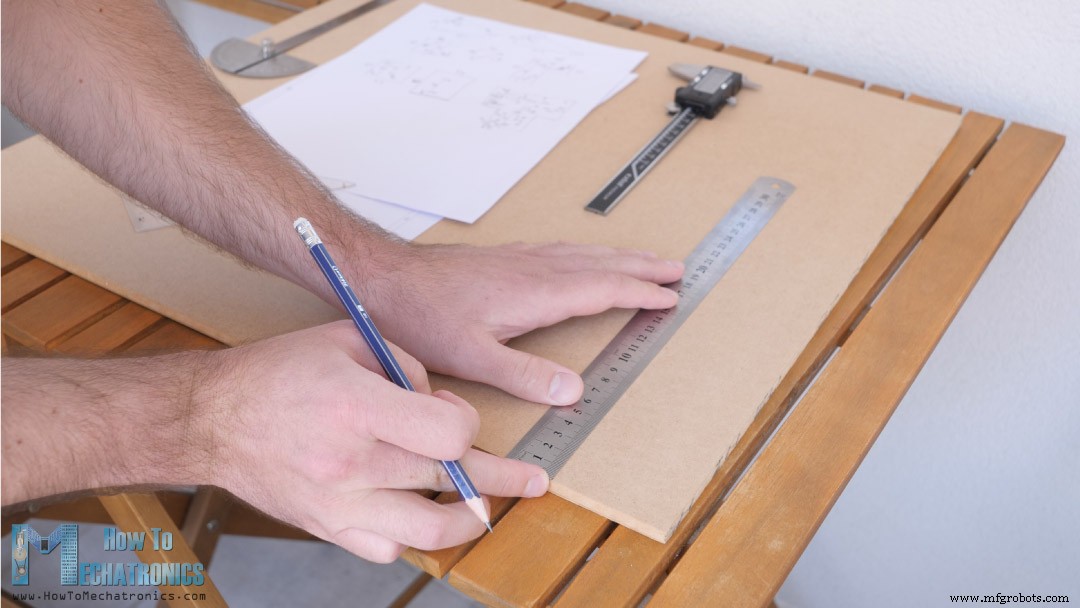
Конечно, требуется некоторое усилие, чтобы вырезать все детали вручную, но тем не менее, мы можем сделать их довольно красивыми и чистыми даже с помощью этого метода.
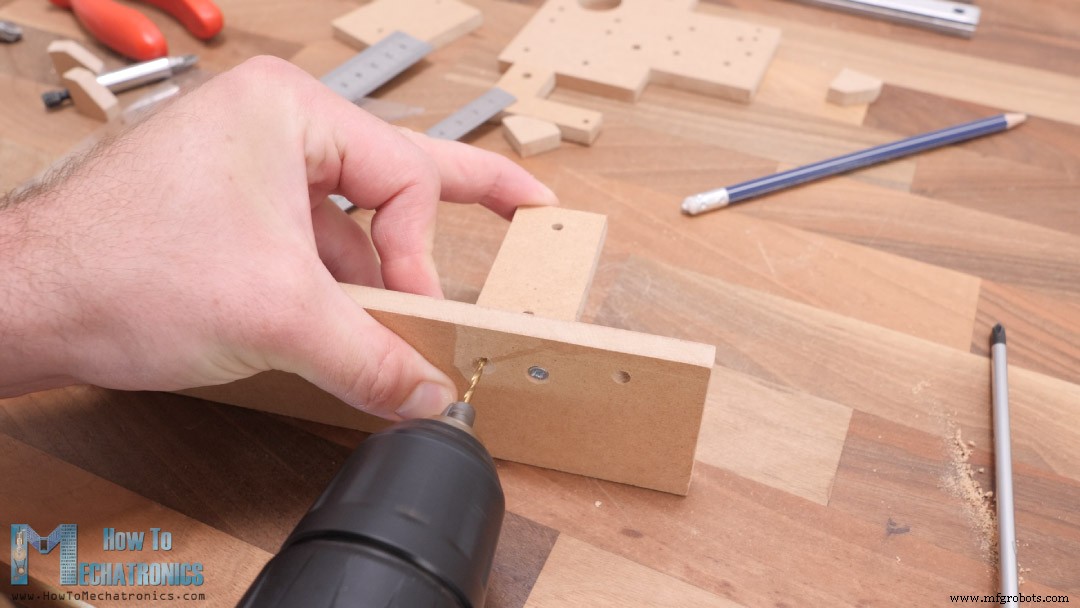
После того, как я вырезал все детали по размеру, я приступил к проделыванию в них отверстий. Точное выполнение отверстий на самом деле важнее, чем вырезание деталей. Расположение отверстий должно быть очень точным, так как они должны совпадать с другими частями, имеющими точные и фиксированные размеры, такими как линейные рельсы и шаговые двигатели.
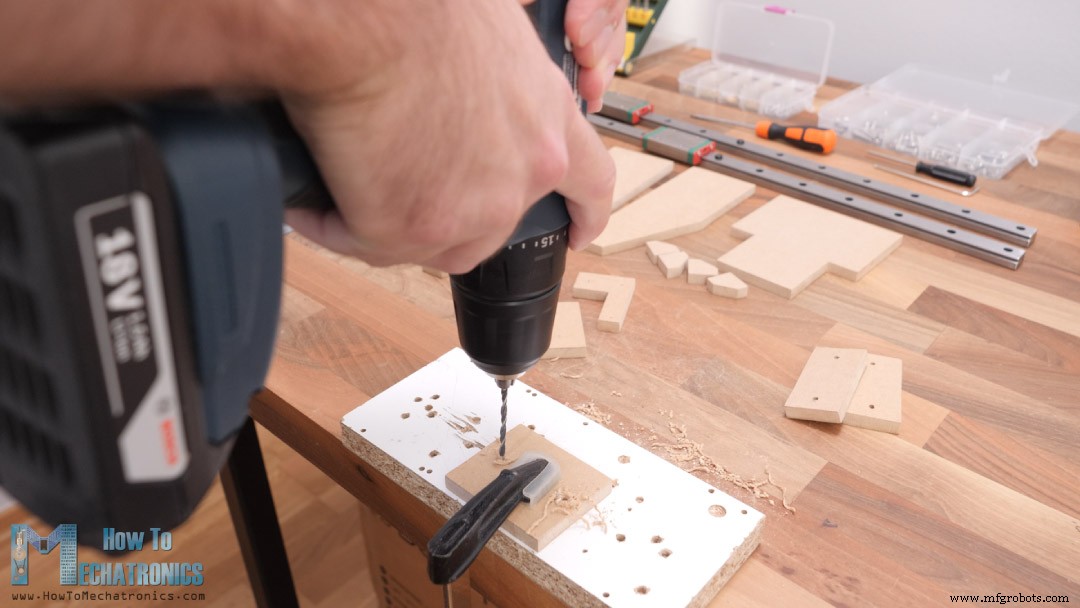
Центральная пластина, на которой установлены ось Y и шаговые двигатели, имеет много отверстий, и чтобы сделать их правильно, я напечатал чертеж этой детали в реальном размере.
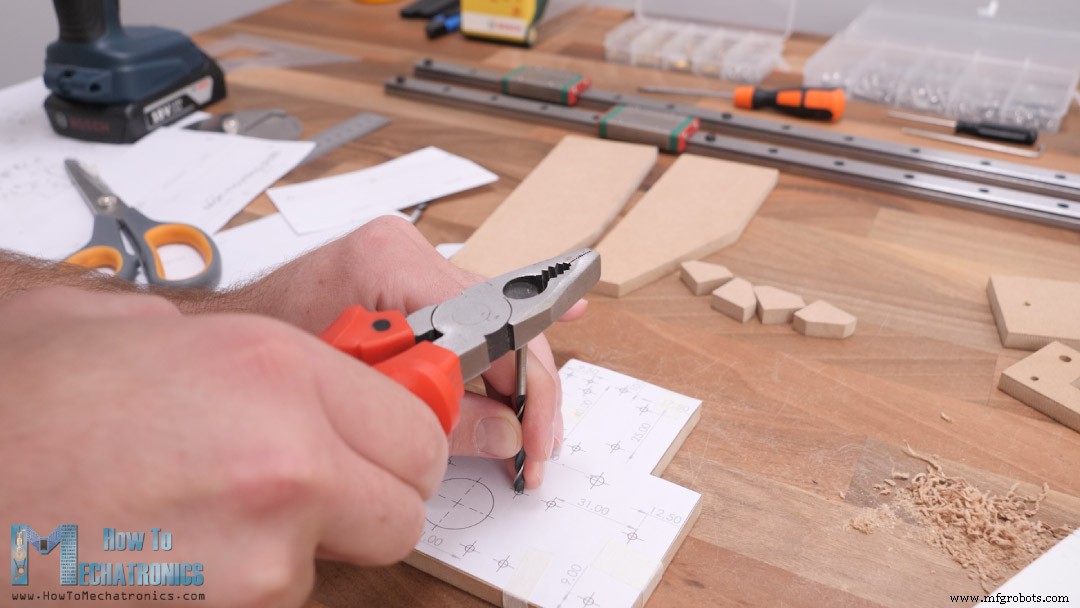
Обычные принтеры легко доступны для всех, поэтому я не буду обманывать, если буду использовать один из них для создания этого проекта. Таким образом, мы можем расположить деталь и чертеж и отметить расположение отверстий. Затем мы можем просверлить отверстия, хотя это не означает, что мы получим их на 100% точно. Мы все еще делаем эту работу вручную, поэтому нам нужно быть очень сконцентрированными и терпеливыми, чтобы все сделать правильно.
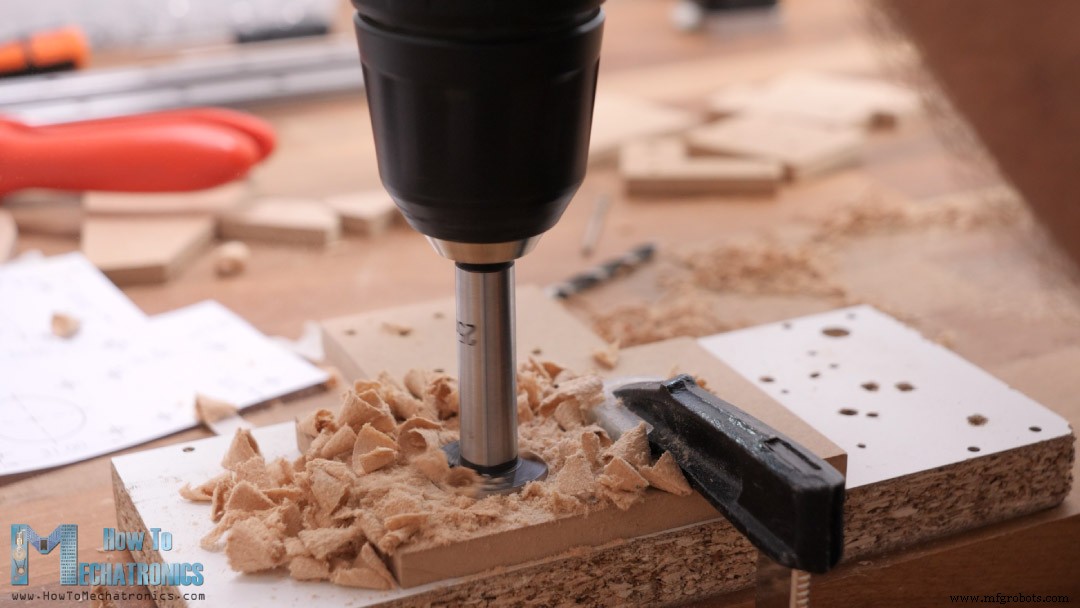
Нам понадобится сверло на 3 и 5 мм, а также одно сверло на 25 мм для изготовления отверстия под шаговый двигатель.
Далее я продолжил сборку основания станка, на котором будет закреплена направляющая оси X. Для этого я отметил место, где должна быть закреплена опорная часть рельса, и просверлил два отверстия в базовой части и одно отверстие в опорной части.
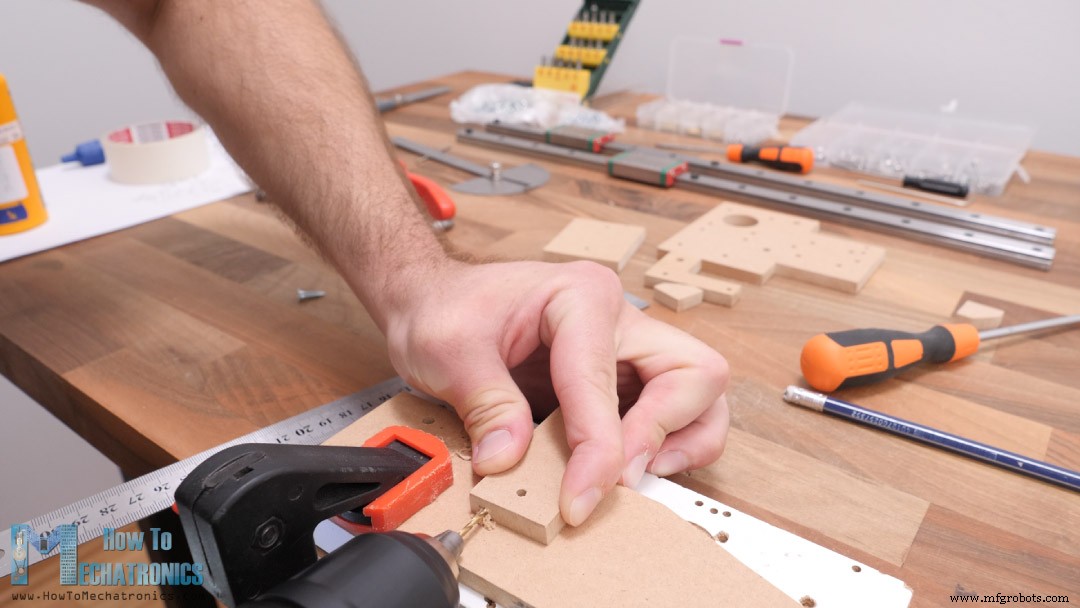
Затем я закрепил эти две части первым 3-миллиметровым винтом и небольшим количеством столярного клея. Установив первый винт, я проверил его прямоугольность, а затем предварительно просверлил второе отверстие в опорном материале 2-миллиметровым сверлом.
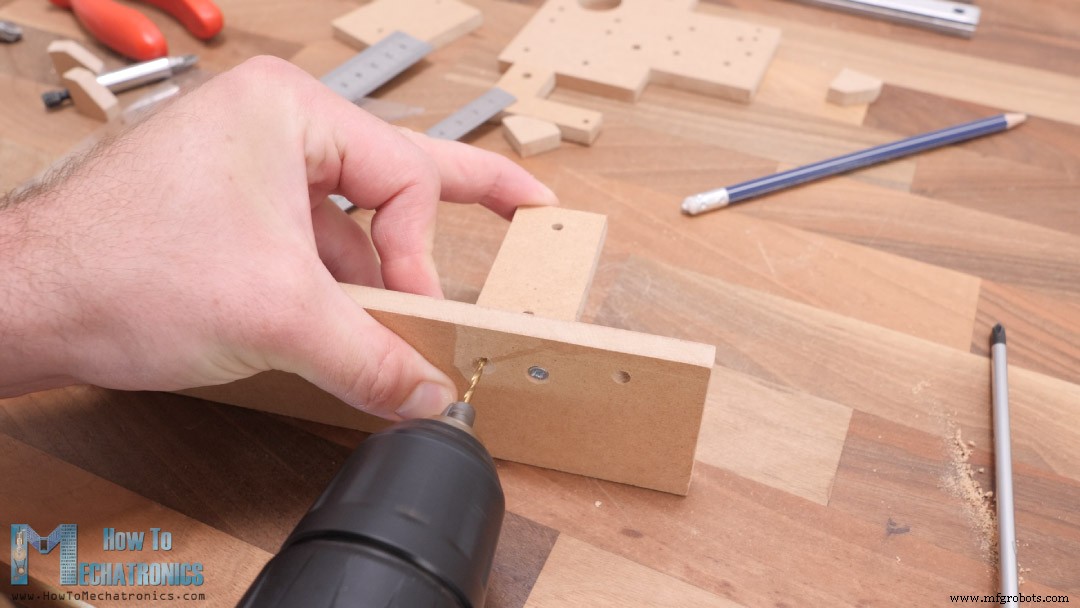
Аналогичным образом я добавил две скобки для лучшей поддержки.
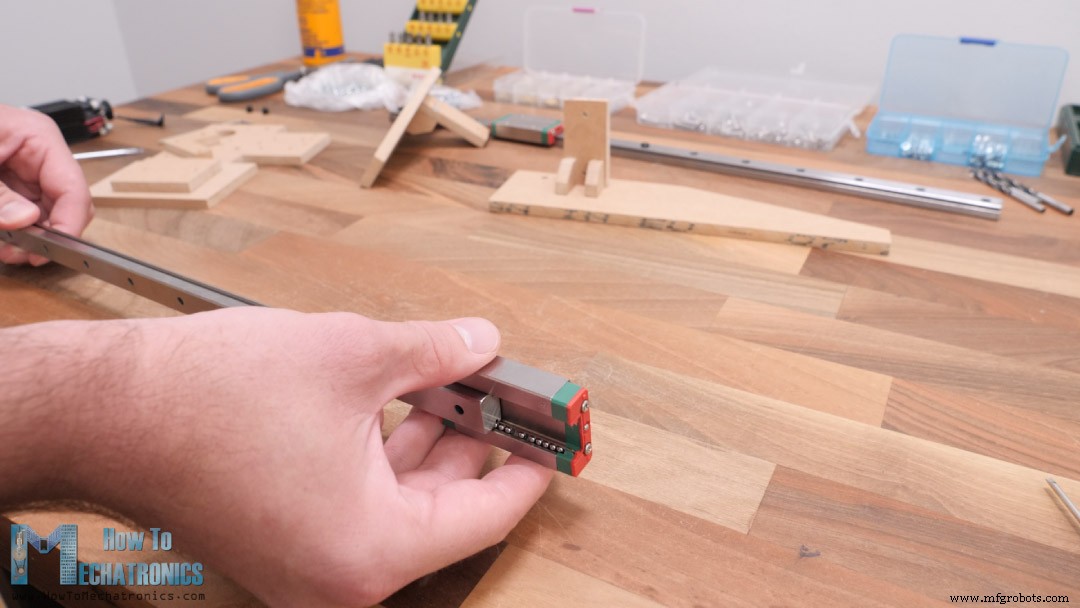
Честно говоря, этот метод сборки этих деталей из МДФ не очень хорош, так как очень сложно сделать их ровными, так как все мы делаем вручную, а плиты МДФ имеют толщину всего 8 мм, что дополнительно усложняет этот процесс. Возможно, лучшим и простым способом было бы использование металлических скоб, которые вы можете легко найти в хозяйственном магазине.
Тем не менее, как только у меня были готовы две стороны, я установил на них направляющую оси X.
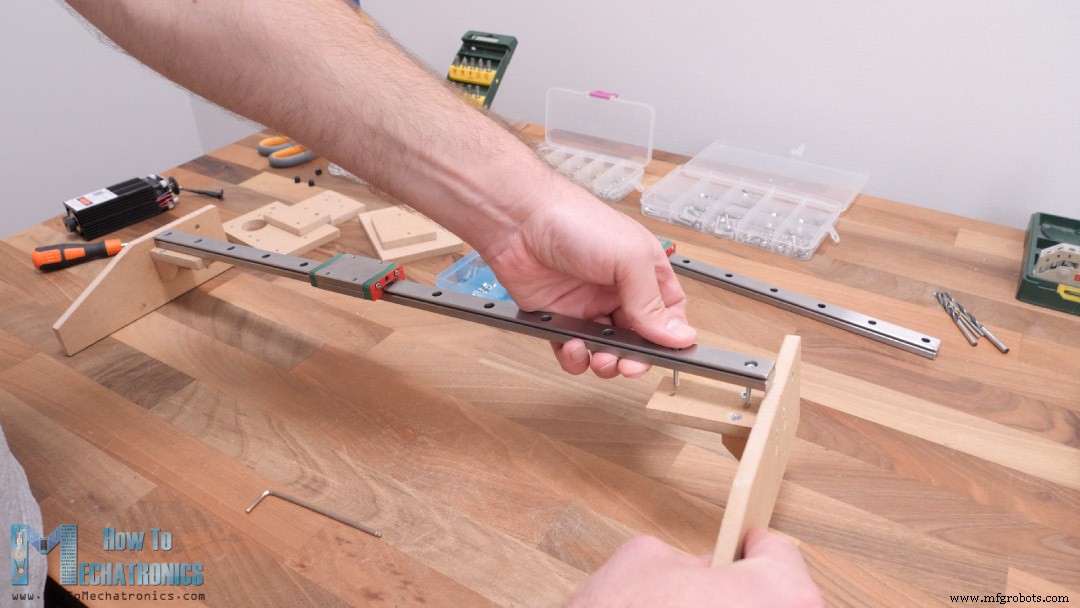
Эти направляющие MGN15H обеспечивают очень плавное движение без люфтов, так как в их скользящих блоках есть шарики или ролики.
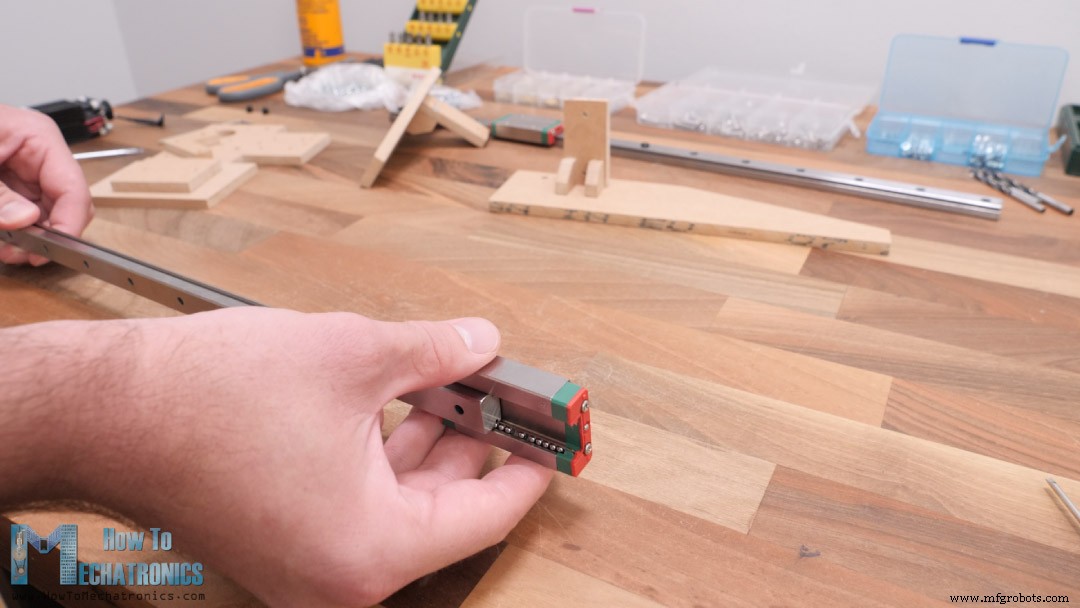
Перед установкой их следует хорошо очистить и смазать. Я закрепил линейную направляющую двумя болтами M3 с каждой стороны.
Далее нам нужно установить ось Y поверх скользящего блока оси X. Для этой цели мы будем использовать центральную пластину.
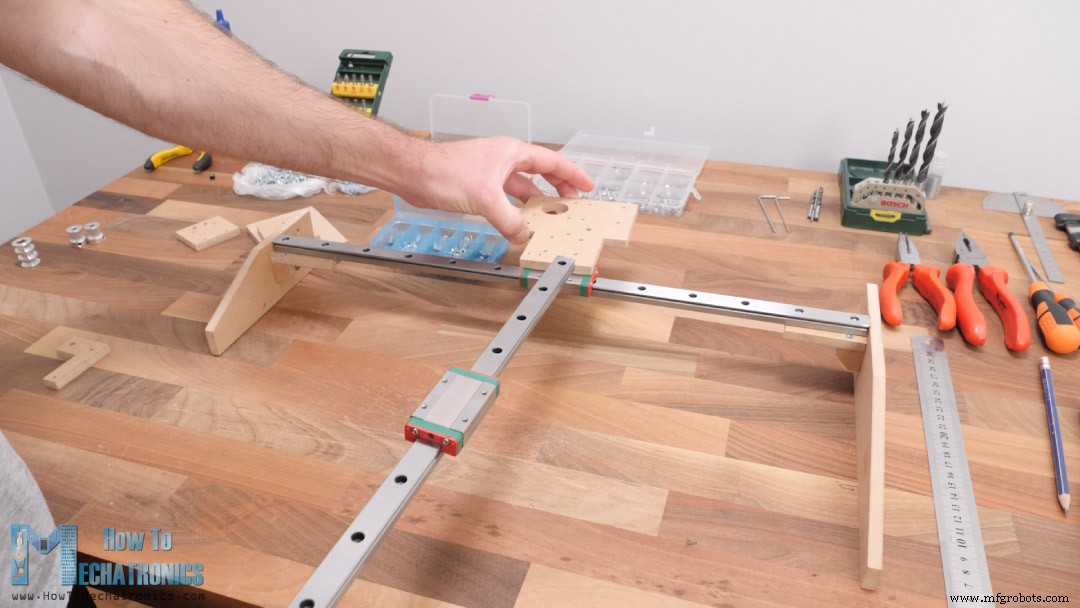
Опять же, мы используем болты M3 для скрепления деталей. Для крепления шаговых двигателей нам также понадобятся болты M3.
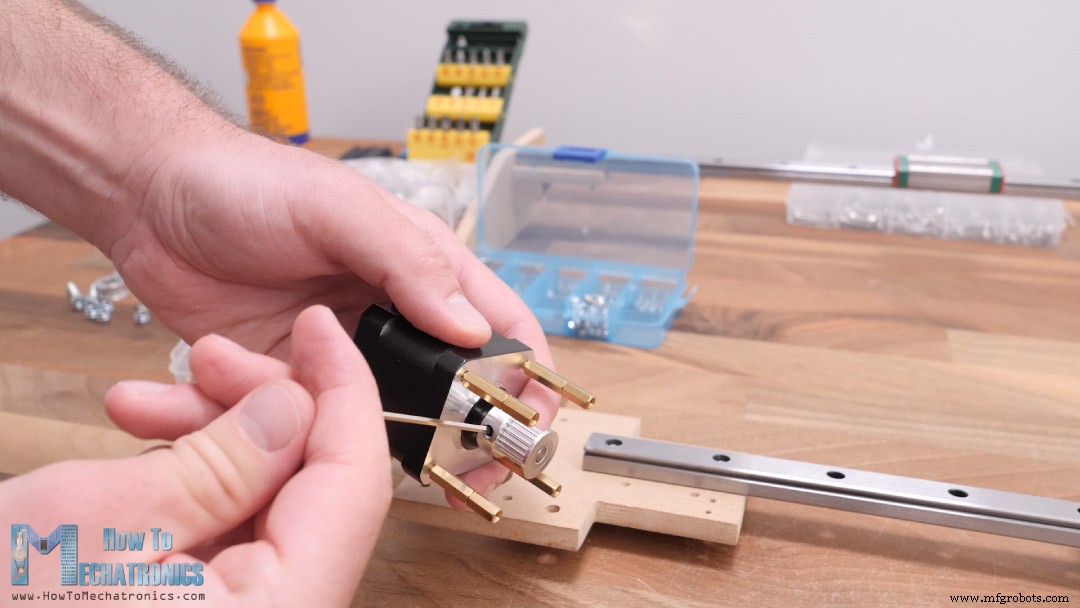
В дополнение к этому, для одного из степперов я использую распорные гайки, чтобы получить правильную высоту установки для него, хотя я, вероятно, мог бы установить этот степпер на нижней стороне пластины, и поэтому нам пришлось бы использовать эти орехи расстояния.
Для привода оси X нам необходимо установить два промежуточных шкива GT2 рядом с валом шагового двигателя, чтобы мы могли создать надлежащее натяжение между ремнем и шкивом шагового двигателя.
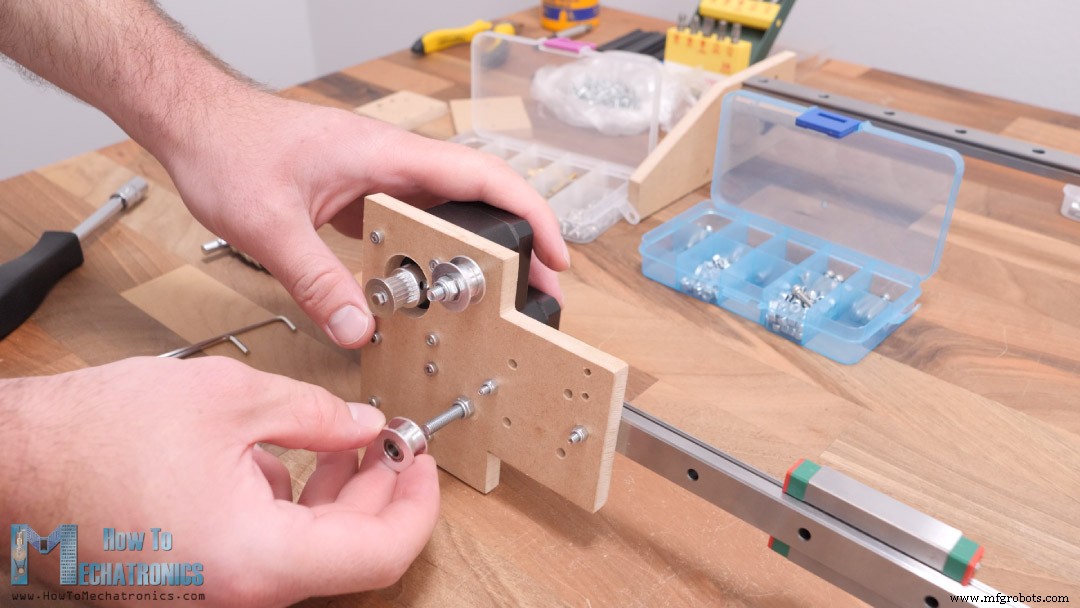
Нам понадобятся болты М5 и гайки для их крепления. Что касается оси Y, нам нужен только один натяжной ролик с другой стороны рельса, так как ремень для этой оси будет установлен в виде петли.
Хорошо, так что дальше брак или соединение рельсов осей X и Y вместе. Мы делаем это, используя четыре болта M3. Это соединение имеет решающее значение для точности, так как от него зависит точность всей машины.
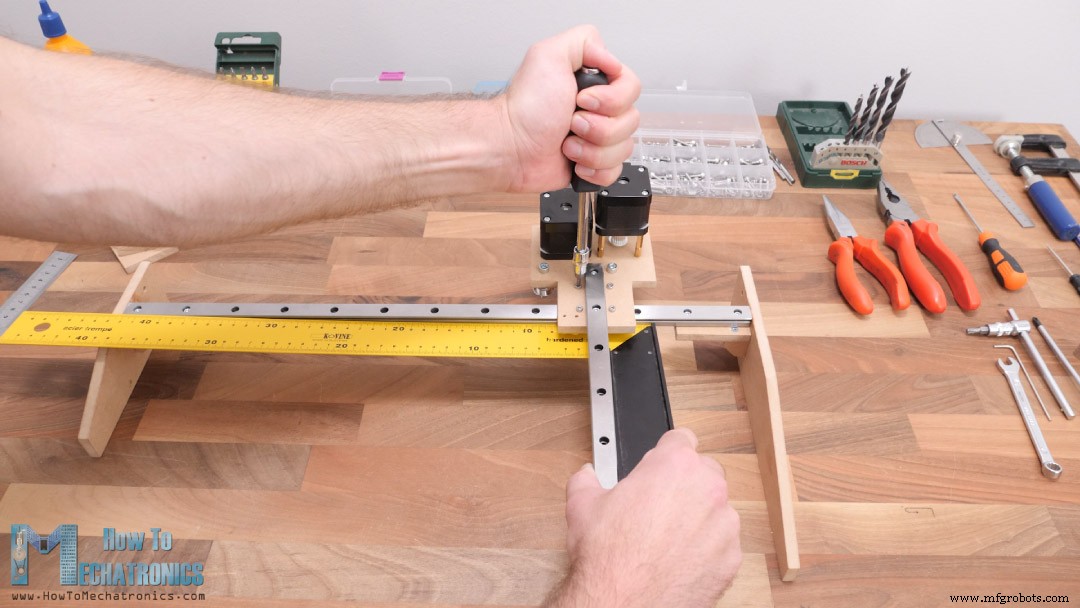
Используя квадратную линейку, мы должны проверить, перпендикулярны ли две оси друг другу, и если нет, мы должны правильно их настроить.
Затем мы можем установить детали, которые идут на скользящий блок оси Y и фактически удерживают концевой эффектор или лазерный модуль в этом случае. Используя метод, описанный ранее, я собрал эти детали и прикрепил их к скользящему блоку с помощью четырех болтов M3.
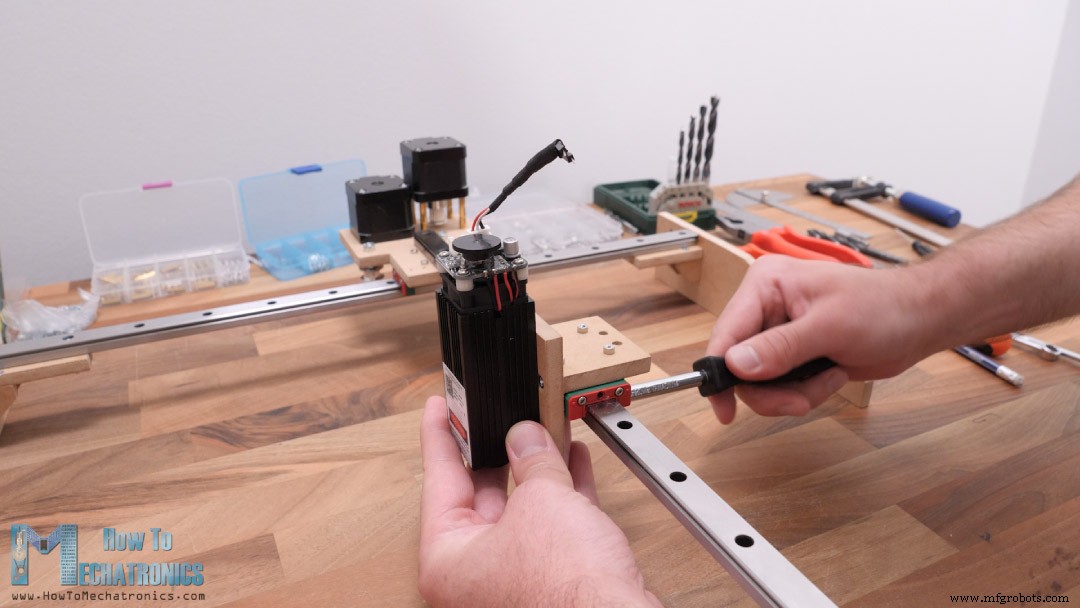
Теперь мы можем закрепить лазерный модуль двумя болтами M3.
Я продолжил установку ремней GT2. Я измерил нужную мне длину и обрезал ремень по размеру.
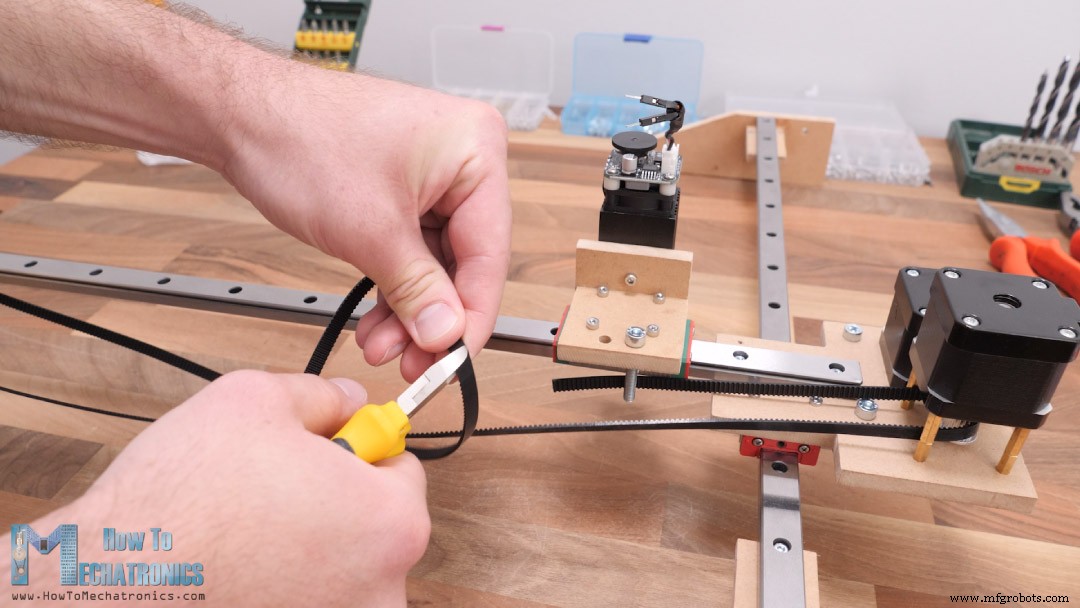
Для крепления ремня к скользящему блоку я использовал два болта М5 и стяжки.
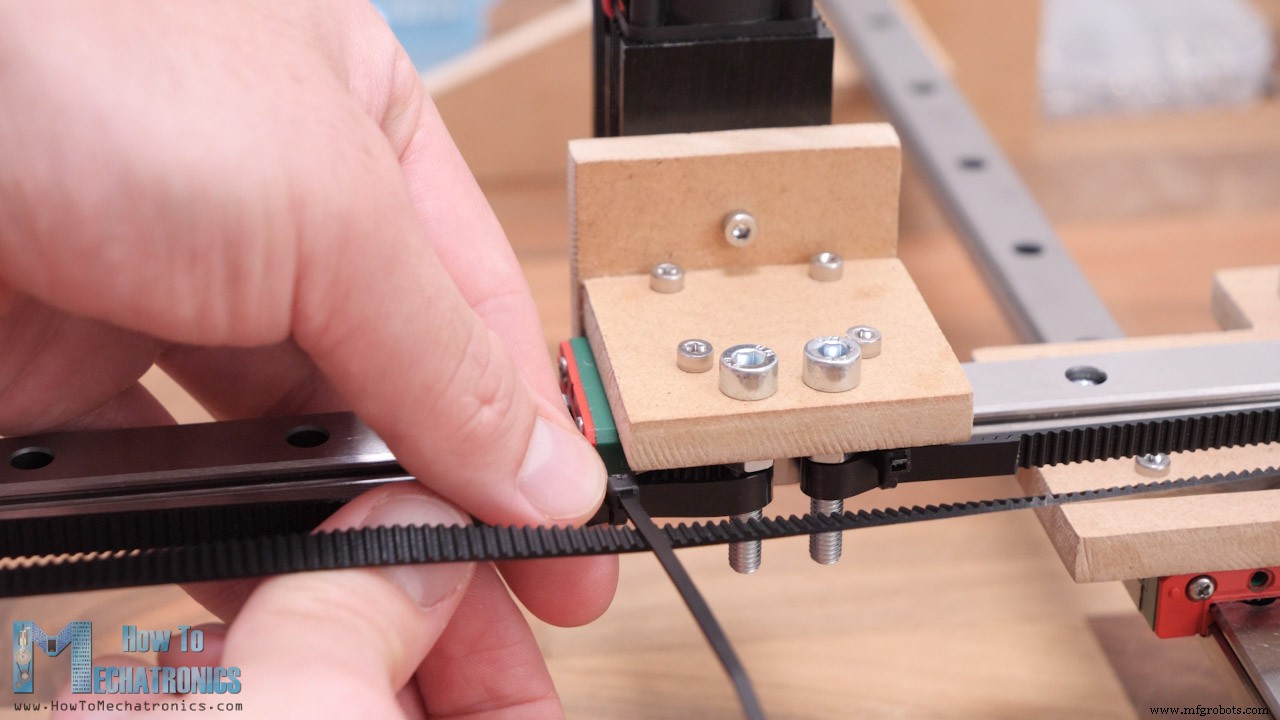
Я прикрепил первую сторону ремня к болту M5 с помощью стяжки, а затем натянул ремень с другой стороны и прикрепил его ко второму болту с помощью стяжки.
Что касается оси X, ремень будет натянут по линии от одной стороны к другой, проходя через три шкива таким образом, чтобы обеспечить натяжение или сцепление со шкивом шагового двигателя.
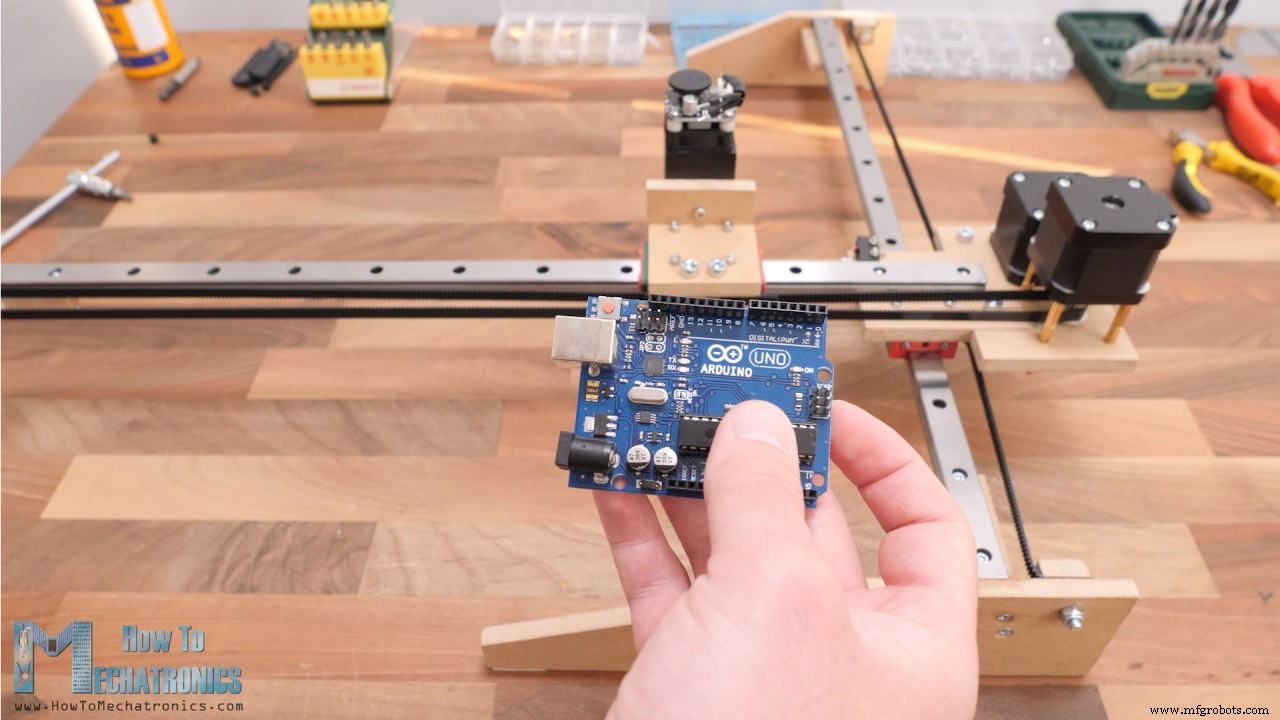
Я закрепил ремень с обеих сторон одним болтом и квадратным куском МДФ.
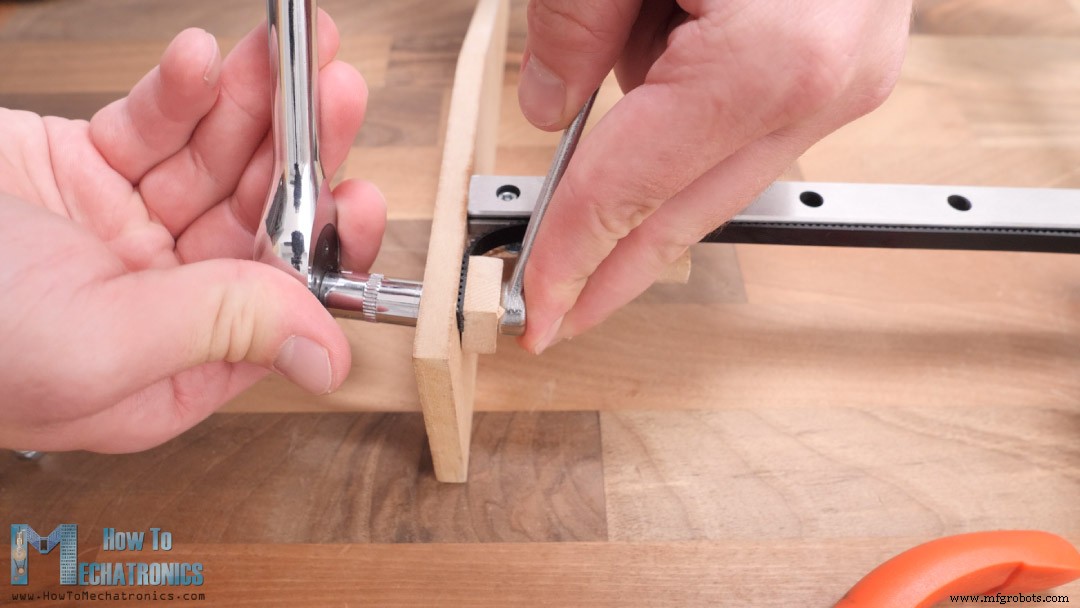
На этом наш станок с ЧПУ почти готов. Есть еще несколько вещей, которые нам нужно сделать.
Снизу я приклеил несколько мебельных накладок, чтобы машина устойчивее стояла на месте.
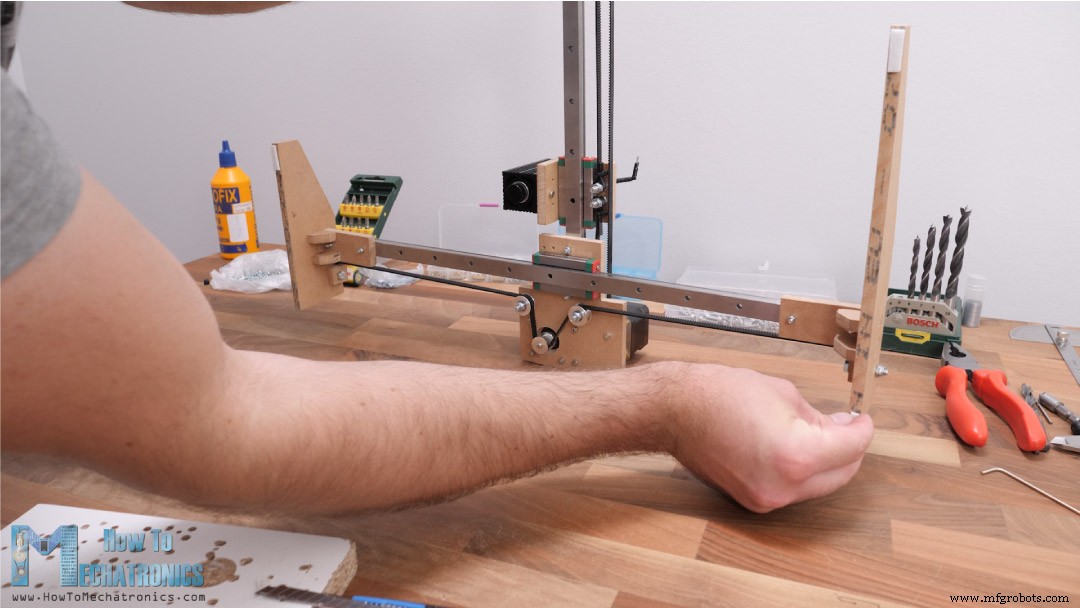
Затем я установил микроконцевик для оси Y. Для этого нам понадобятся два болта M2.
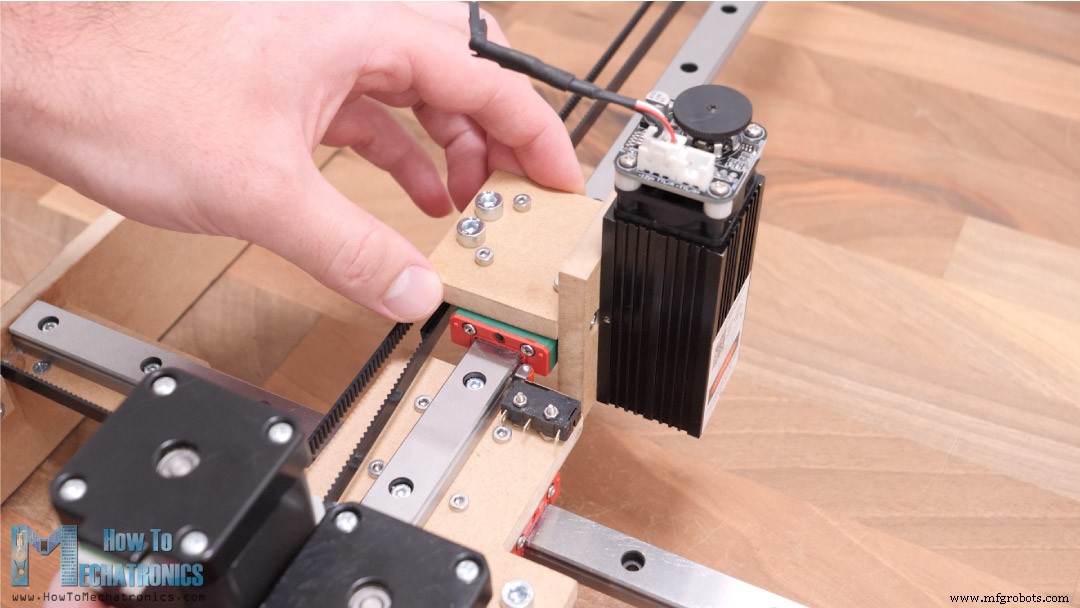
Что касается концевого выключателя оси X, я забыл сделать эти отверстия на центральной пластине, поэтому я отметил их и просверлил на месте.
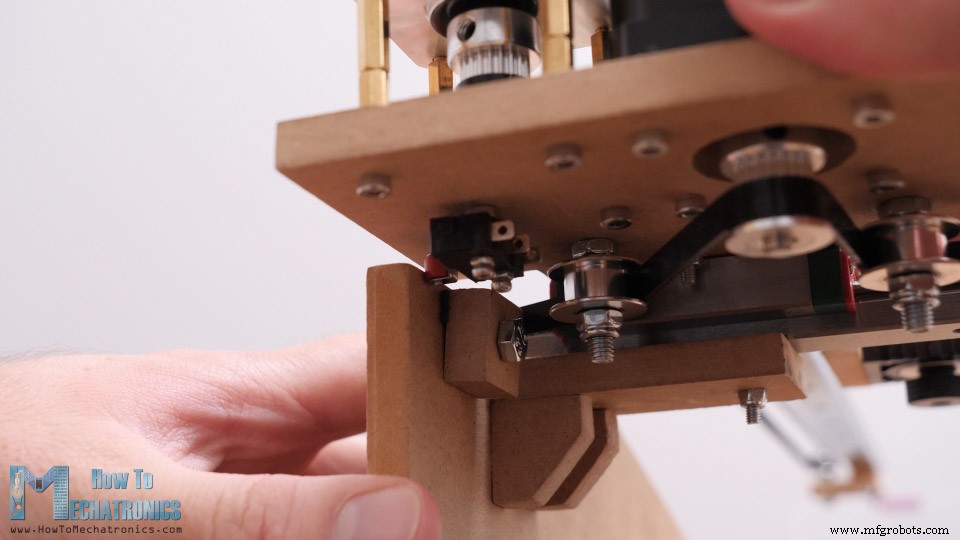
Было немного трудно закрепить этот концевой выключатель на месте, но в конце концов получилось хорошо.
Подключение электронных компонентов
Механическая часть завершена, теперь можно переходить к подключению электронных компонентов. Как я уже упоминал, мы будем использовать плату Arduino UNO в сочетании с CNC Shield и двумя шаговыми драйверами DRV8825 или A4988.
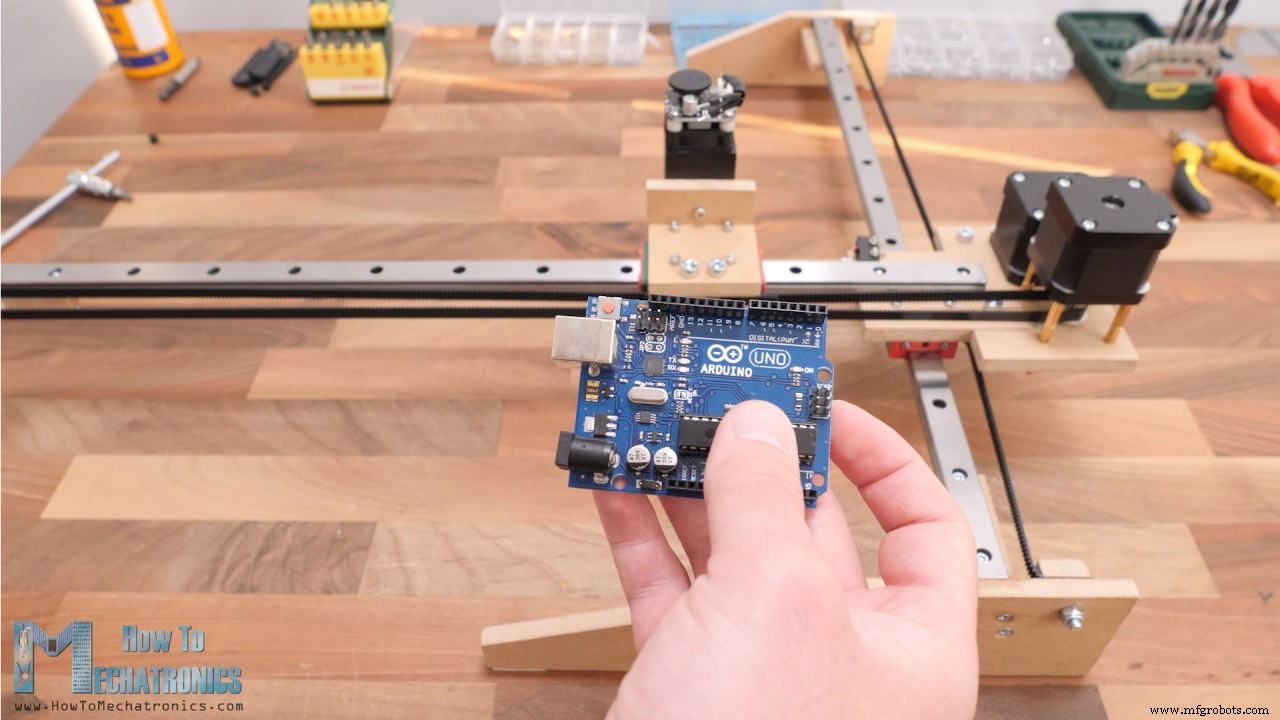
Я закреплю плату Arduino сбоку машины, поэтому я отметил два отверстия для Arduino и просверлил их 3-миллиметровым сверлом. Я использовал гайки с расстоянием 5 мм между боковой панелью и платой Arduino.
Экран ЧПУ просто устанавливается поверх платы Arduino. Нам нужно вставить 3 перемычки для каждого драйвера, чтобы выбрать самое высокое разрешение шагового двигателя.
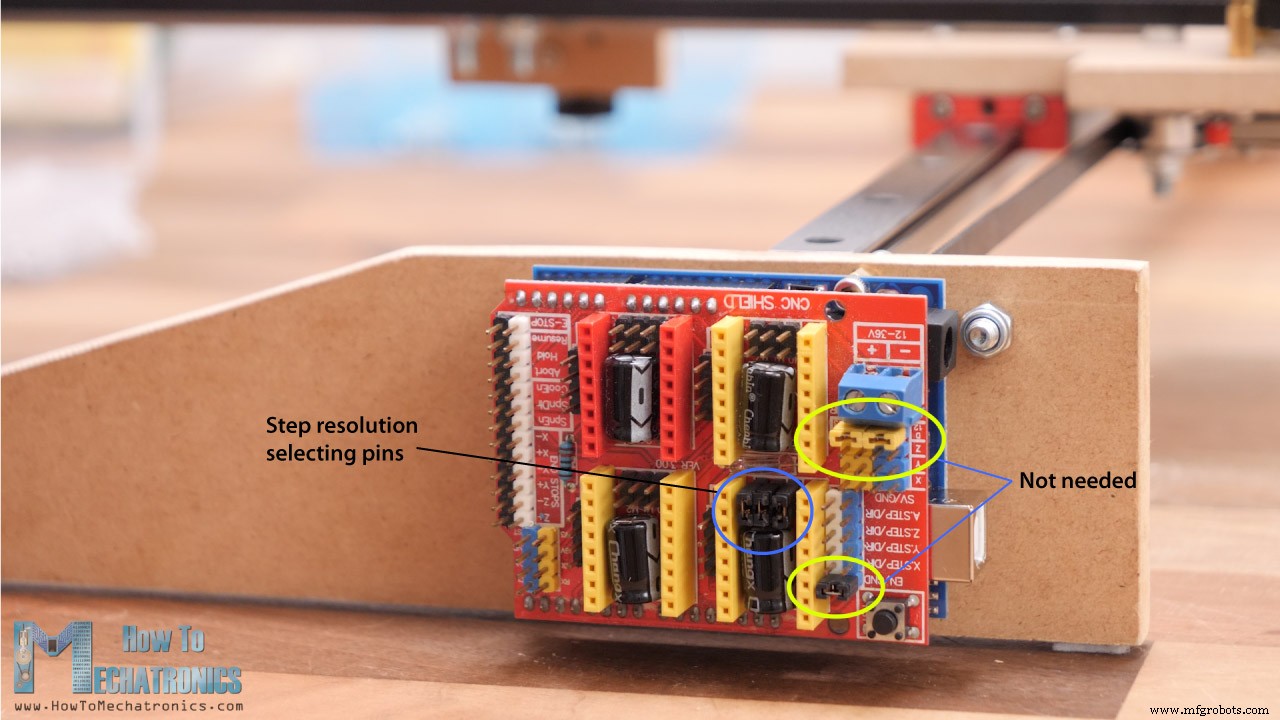
Обратите внимание, что эти три перемычки должны быть удалены, так как они нам не нужны. Я использовал их в одном из своих предыдущих проектов.
Затем мы можем подключить шаговые двигатели на месте с помощью прилагаемых кабелей. Для подключения концевых выключателей нам понадобится двухпроводное соединение.
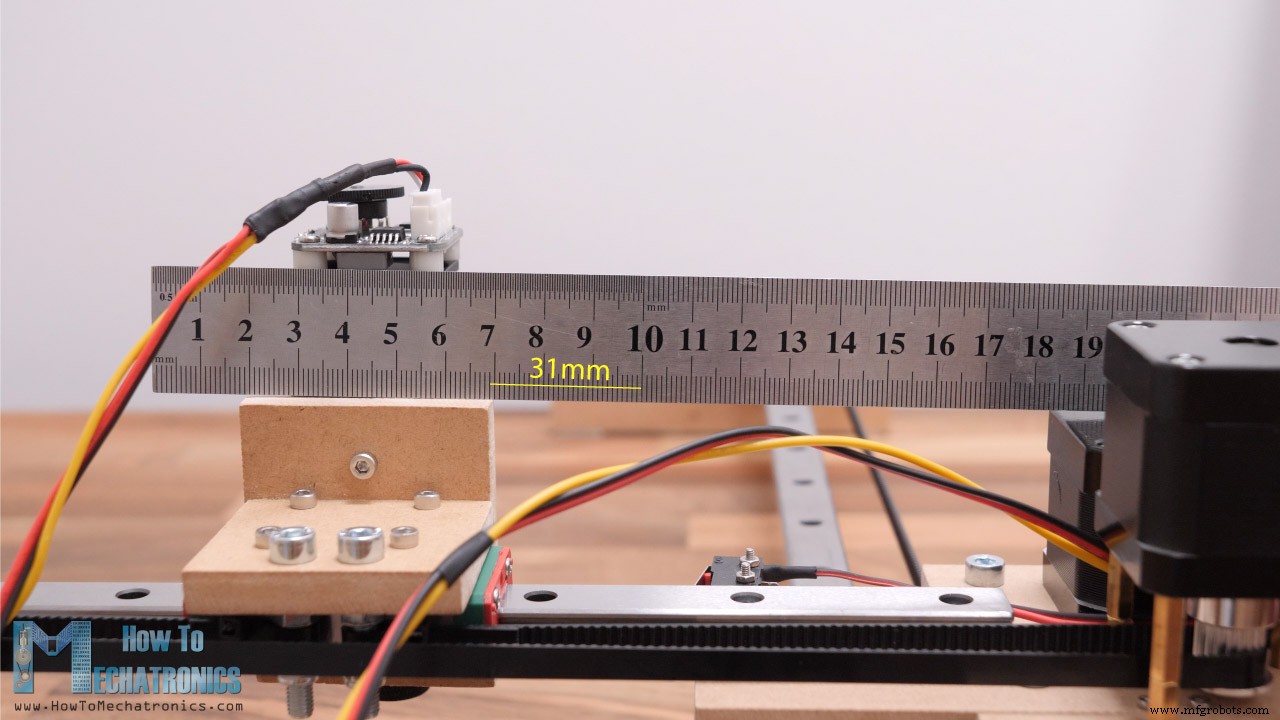
Я припаял один конец проводов непосредственно к торцевым упорам, а с другой стороны припаял штыревые разъемы, чтобы можно было легко подключить их к экрану ЧПУ.
Что касается подключения лазерного модуля, то нам понадобится 3 провода, GND, 12В и сигнальная линия для ШИМ-управления. Эти провода должны быть немного длиннее, чтобы они могли доходить до самой дальней точки машины.
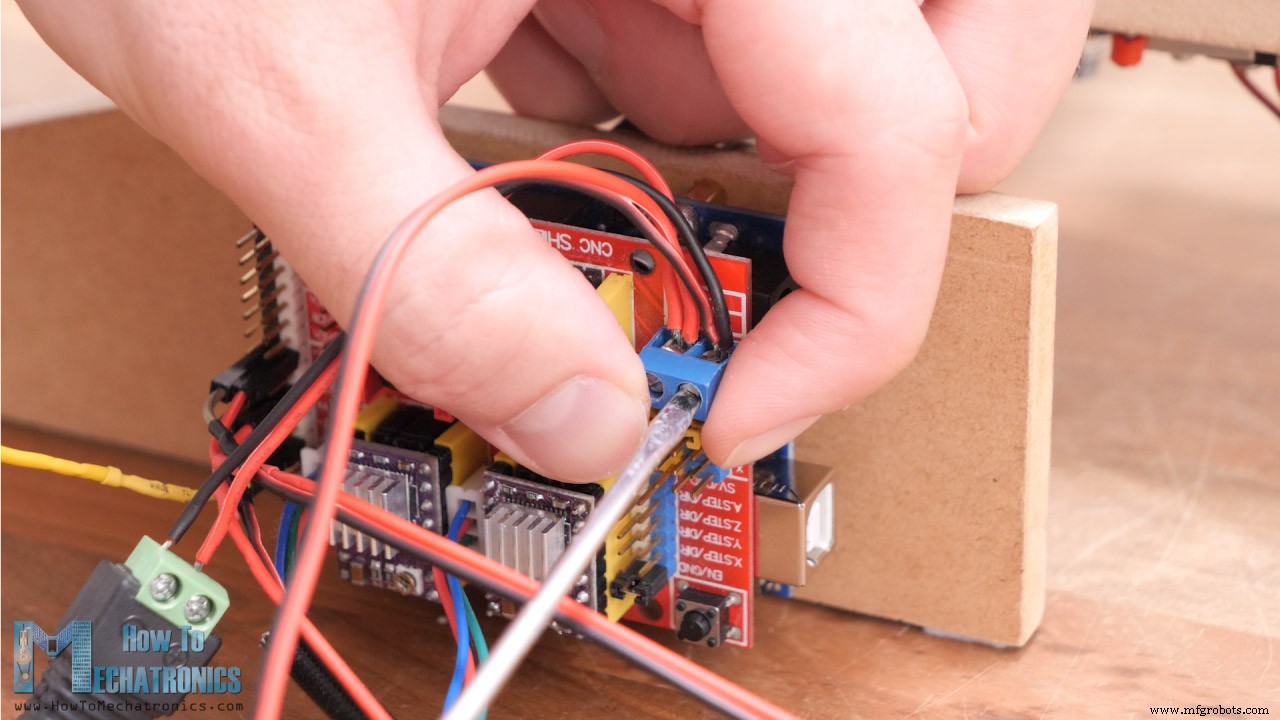
С одной стороны у нас есть 3-контактный разъем, который идет в лазерный модуль, а с другой стороны у нас есть провода GND и 12V, которые будут идти к разъему питания платы ЧПУ и сигнальная линия, которую необходимо подключить. к стопорному штифту Z+ или Z-.
Схема схемы лазерного гравера с ЧПУ своими руками
Вот принципиальная схема того, как все должно быть подключено.
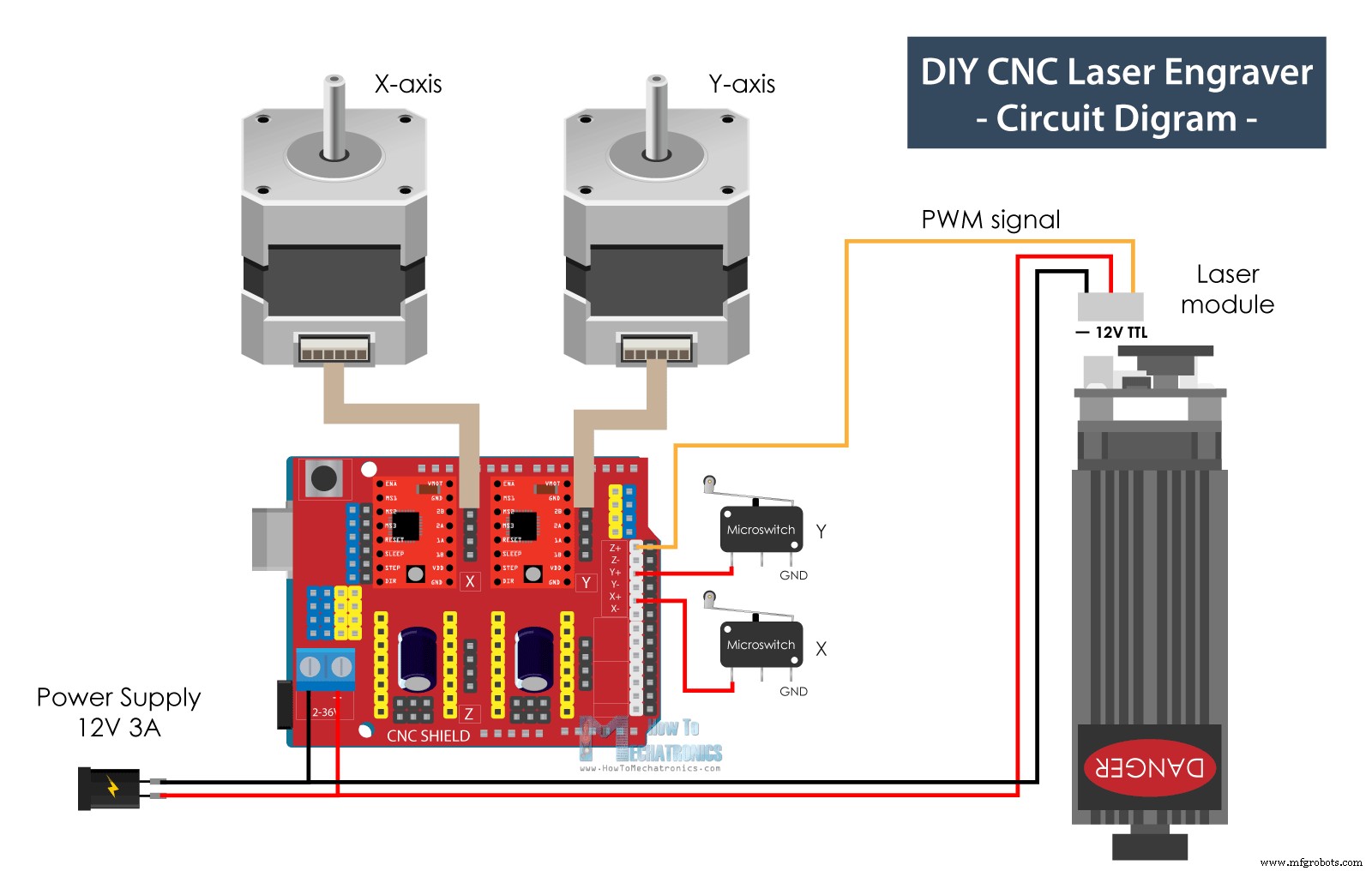
Вы можете получить компоненты, необходимые для этого проекта, по ссылкам ниже:
- Шаговый двигатель — NEMA 17………………
- Драйвер шагового двигателя DRV8825……….……..…
- Arduino CNC Shield ………………………. Амазонка / Бангуд / Алиэкспресс
- Ардуино Уно……………………………………
- Концевой выключатель ……………………………………. Амазонка / Бангуд / Алиэкспресс
- Источник питания постоянного тока …………………………. Амазонка / Banggood / Алиэкспресс
- Лазерный модуль ………………………………. Амазонка / Бангуд / Алиэкспресс
- Защитные очки от лазера…………………….. Amazon / Банггод / Алиэкспресс
Итак, мы используем плату Arduino UNO в сочетании с CNC Shield и двумя шаговыми драйверами DRV8825 или A4988. У нас есть два микроконцевых выключателя для возврата станка в исходное положение и лазерный модуль на 12 В, которым можно управлять с помощью ШИМ. Для питания нам понадобится блок питания 12В с минимальной силой тока 3 Ампера.
Прошивка и управляющее ПО
На этом мы фактически закончили сборку машины. Теперь осталось дать ему жизнь или сделать из него настоящий станок с ЧПУ. Для этого нам нужно установить прошивку на Arduino для управления движением станка с ЧПУ.
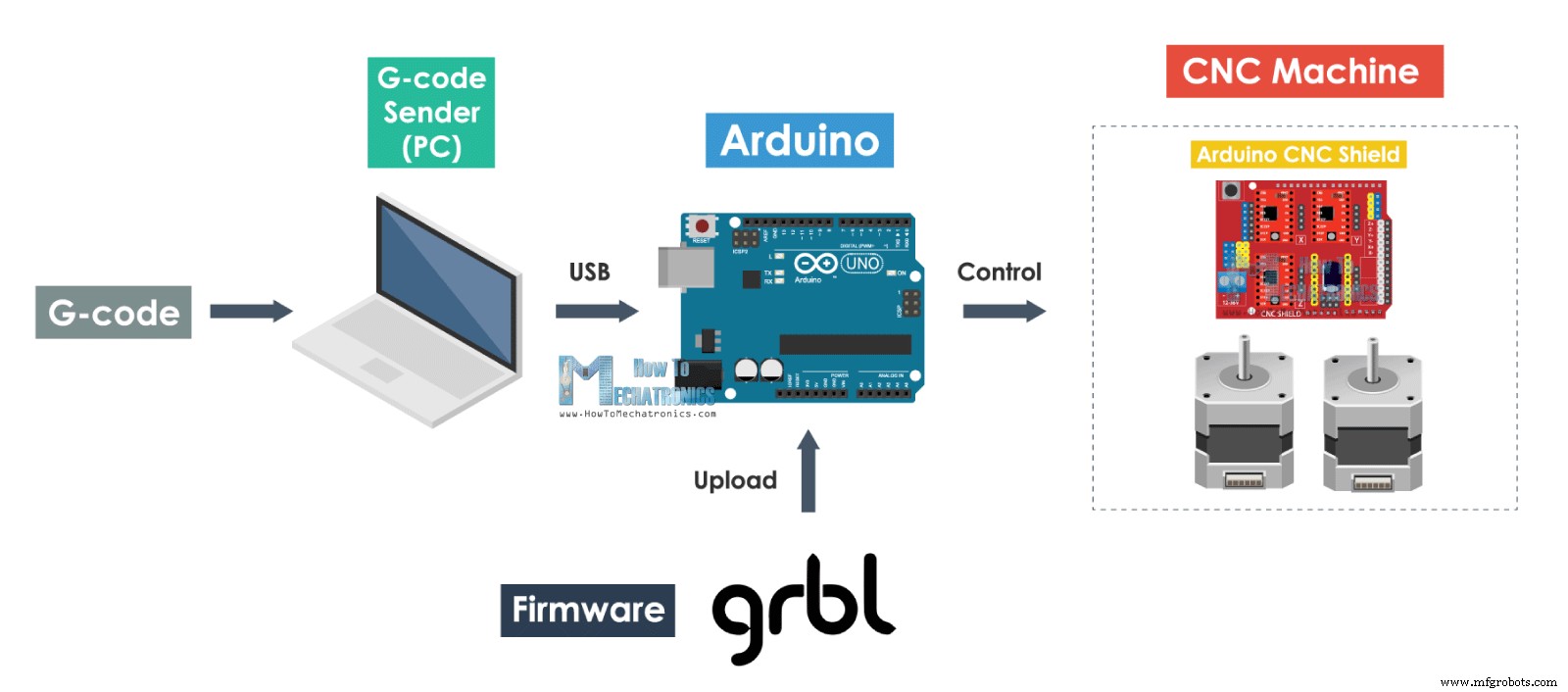
Наиболее популярным выбором для станков с ЧПУ своими руками является прошивка GRBL с открытым исходным кодом. Помимо прошивки GRBL нам также понадобится управляющее ПО, через которое мы будем отправлять G-коды и указывать машине, что делать. В этом случае мы будем использовать контроллер LaserGRBL. Это программное обеспечение специально создано для управления лазерными граверами с прошивкой GRBL, и я могу сказать вам, что это действительно потрясающий контроллер для этой цели, учитывая, что он также имеет открытый исходный код.
С LaserGRBL у нас есть возможность напрямую прошивать или загружать прошивку GRBL в Arduino, поэтому нам не нужно делать это вручную. Мы даже можем выбрать готовую к использованию версию для двухкоординатных станков только с реферированием по осям X и Y, точно такую же, как та, которая нам нужна.
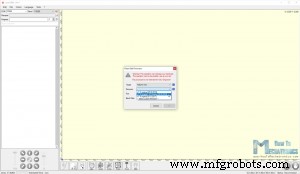
Итак, как только мы прошиваем нашу Arduino прошивкой GRBL, мы можем подключить нашу машину к контроллеру и открыть окно конфигурации GRBL, чтобы мы могли настроить некоторые параметры в соответствии с нашей машиной.
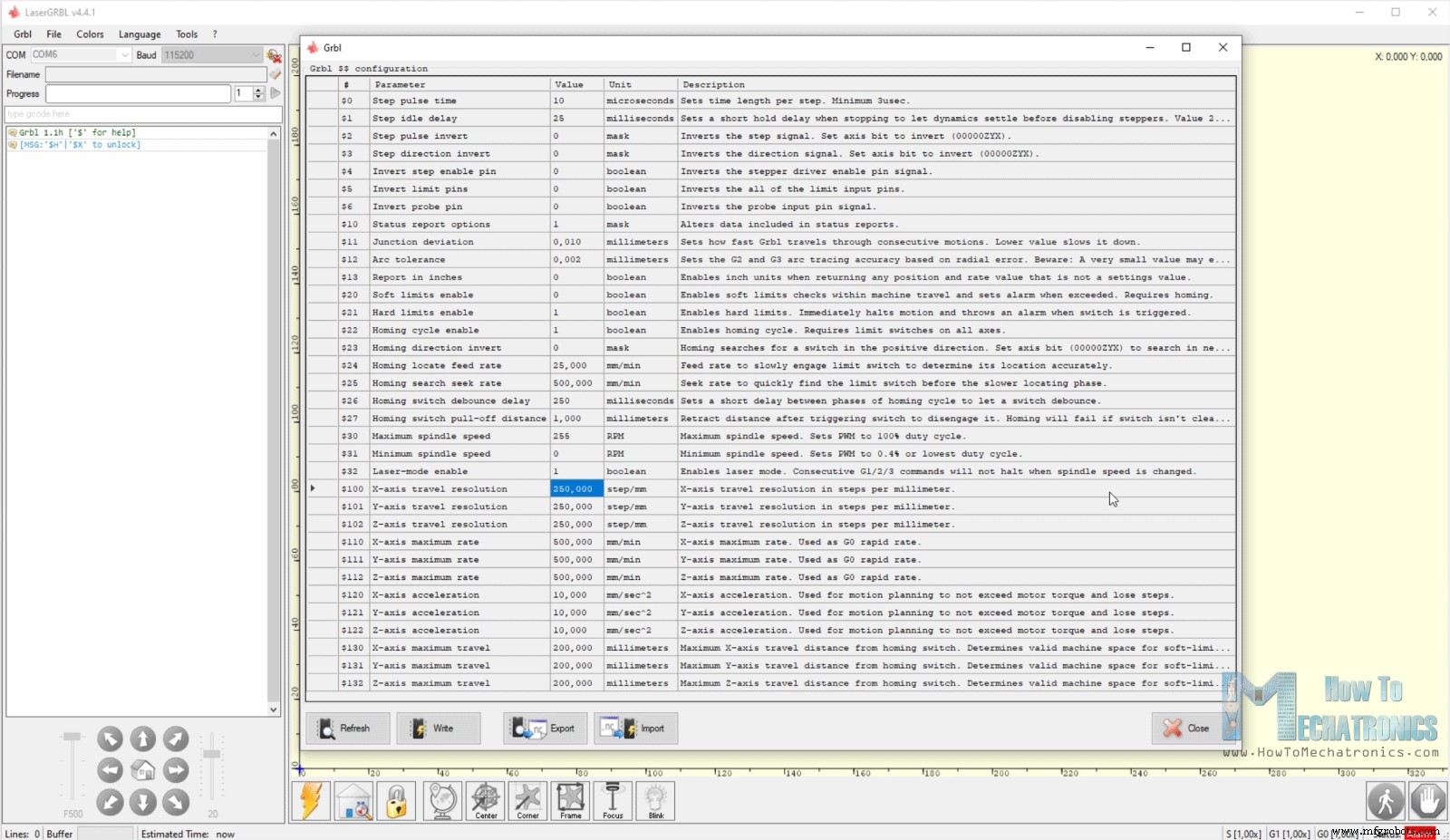
Первое, что мы должны настроить здесь, это разрешение перемещения или значения шагов/мм для осей X и Y. Эти значения показывают, сколько шагов должен сделать двигатель, чтобы переместиться на 1 мм. Это зависит от типа имеющегося у нас шагового двигателя, выбранного разрешения шага и передачи движения, в данном случае ремня и шкива GT2.
Вот как мы можем рассчитать эти значения для нашей машины. Значения по умолчанию здесь обычно составляют 250 шагов/мм. Теперь мы можем перемещать станок с помощью команд JOG, например, на 20 мм, и мы должны заметить, насколько на самом деле сдвинется станок.
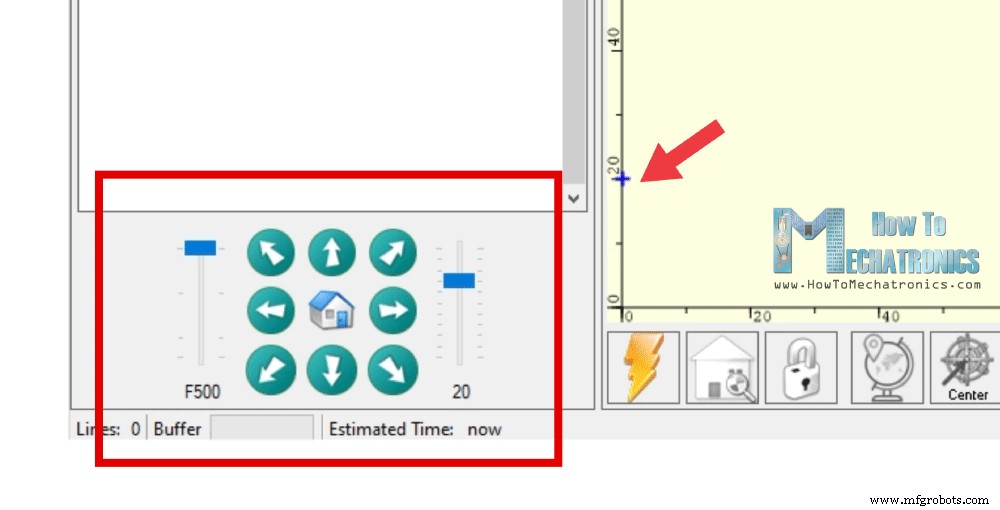
В моем случае при 20-миллиметровом шаге по оси Y фактическое перемещение составило 31 мм.
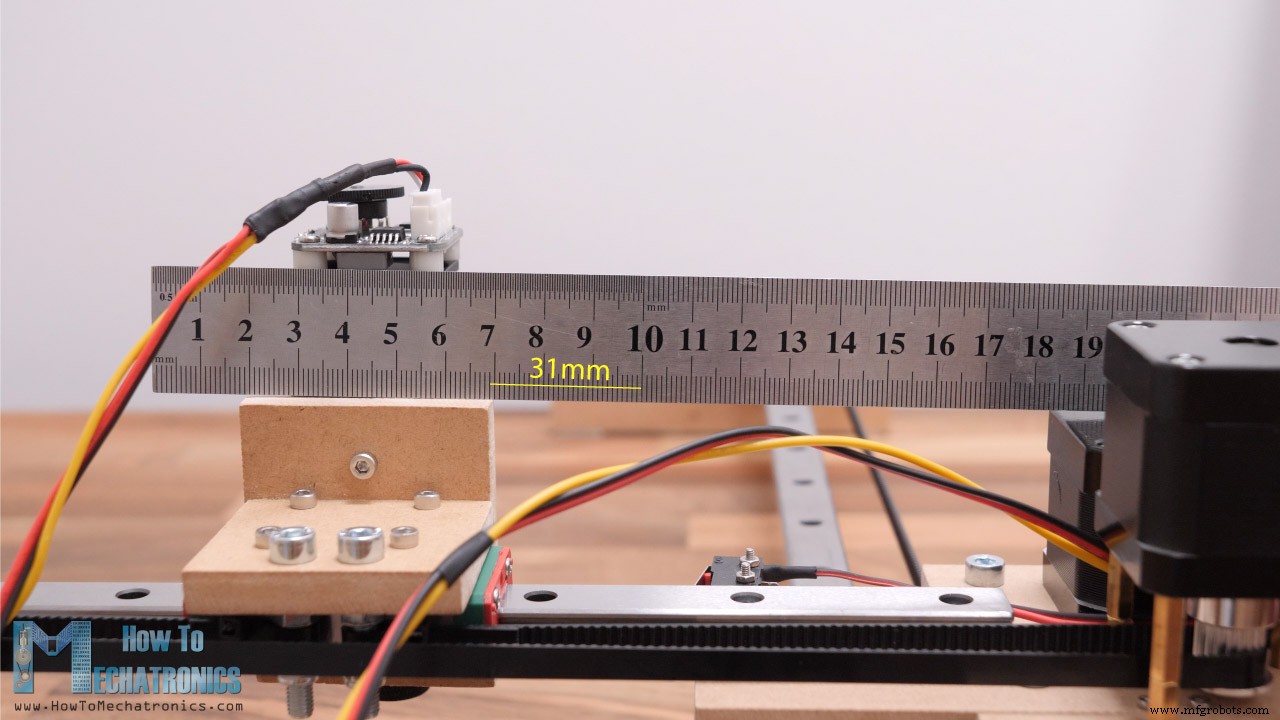
Итак, 20/31 =0,645, и если мы умножим это значение на 250, мы получим 161,29. Итак, это значение, которое мы должны установить в качестве значения шагов/мм для нашей машины.
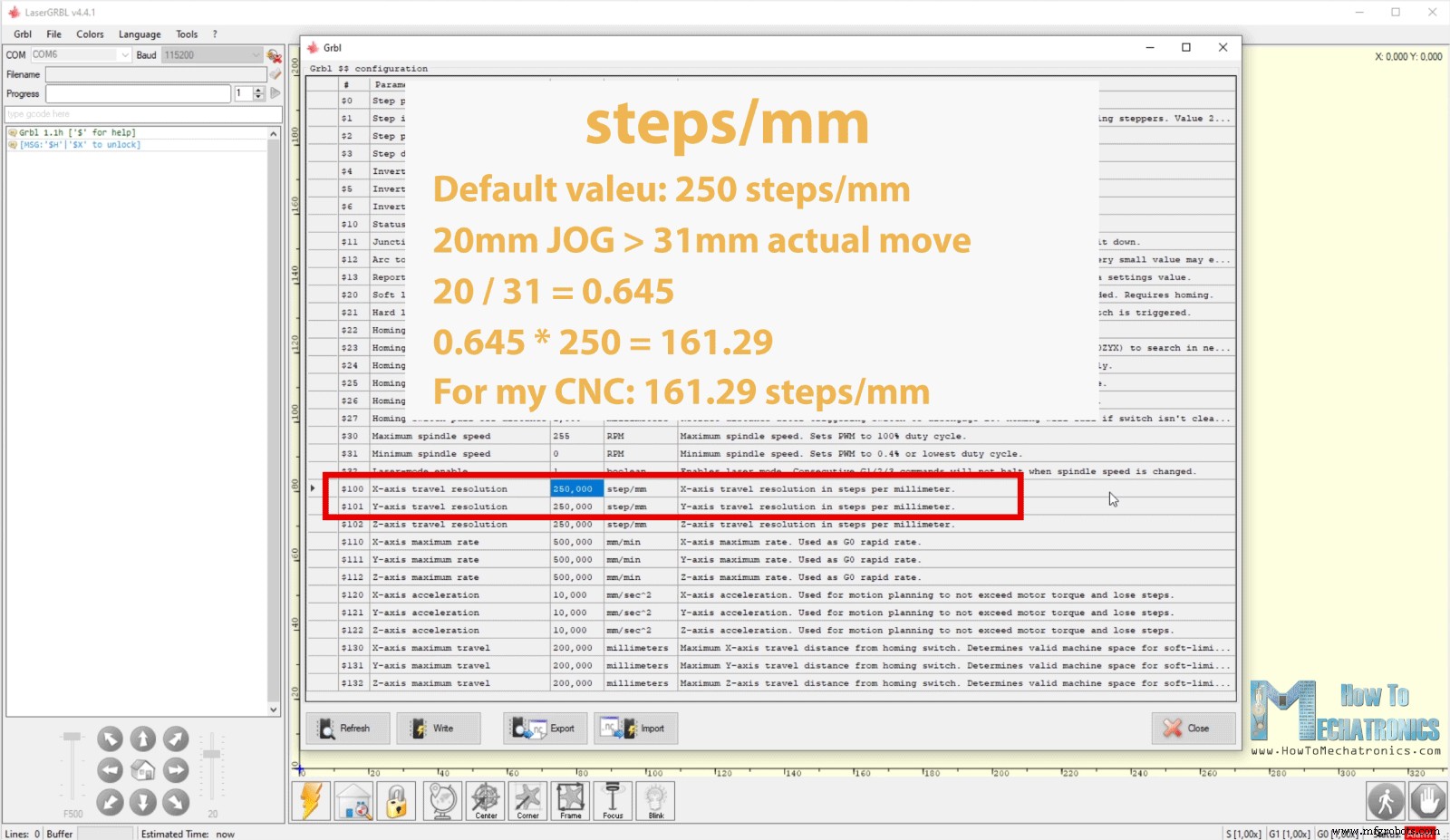
Если мы попытаемся переместить машину сейчас с обновленными значениями, машина должна переместиться на точное расстояние. Если вы недовольны результатом, вы все равно можете точно настроить эти значения, нарисовав квадраты и измерив их. В итоге я использовал значение 160 шагов/мм.
Тем не менее, есть и другие важные параметры, которые также необходимо отрегулировать. Например, мы должны включить Жесткие ограничения, которые являются фактическими концевыми выключателями, Мягкие ограничения, которые определяют рабочую область, установить направление возврата, которое определяет, где наши концевые выключатели расположены на машине, и так далее.
Вы можете скачать мой набор параметров и импортировать их в свою прошивку.
Генерация G-кодов для лазерной гравировки
Еще одна замечательная особенность этого программного обеспечения заключается в том, что оно также имеет встроенный генератор G-кода. Это означает, что мы можем загружать любую фотографию, картинку, карандашный рисунок и т. д. прямо в программу и генерировать G-код для гравировки в соответствии с нашими потребностями. Инструмент растрового изображения достаточно универсален и позволяет выбирать из множества параметров, таких как трассировка от строки к строке, векторизация, сглаживание 1-битного черно-белого изображения и т. д.
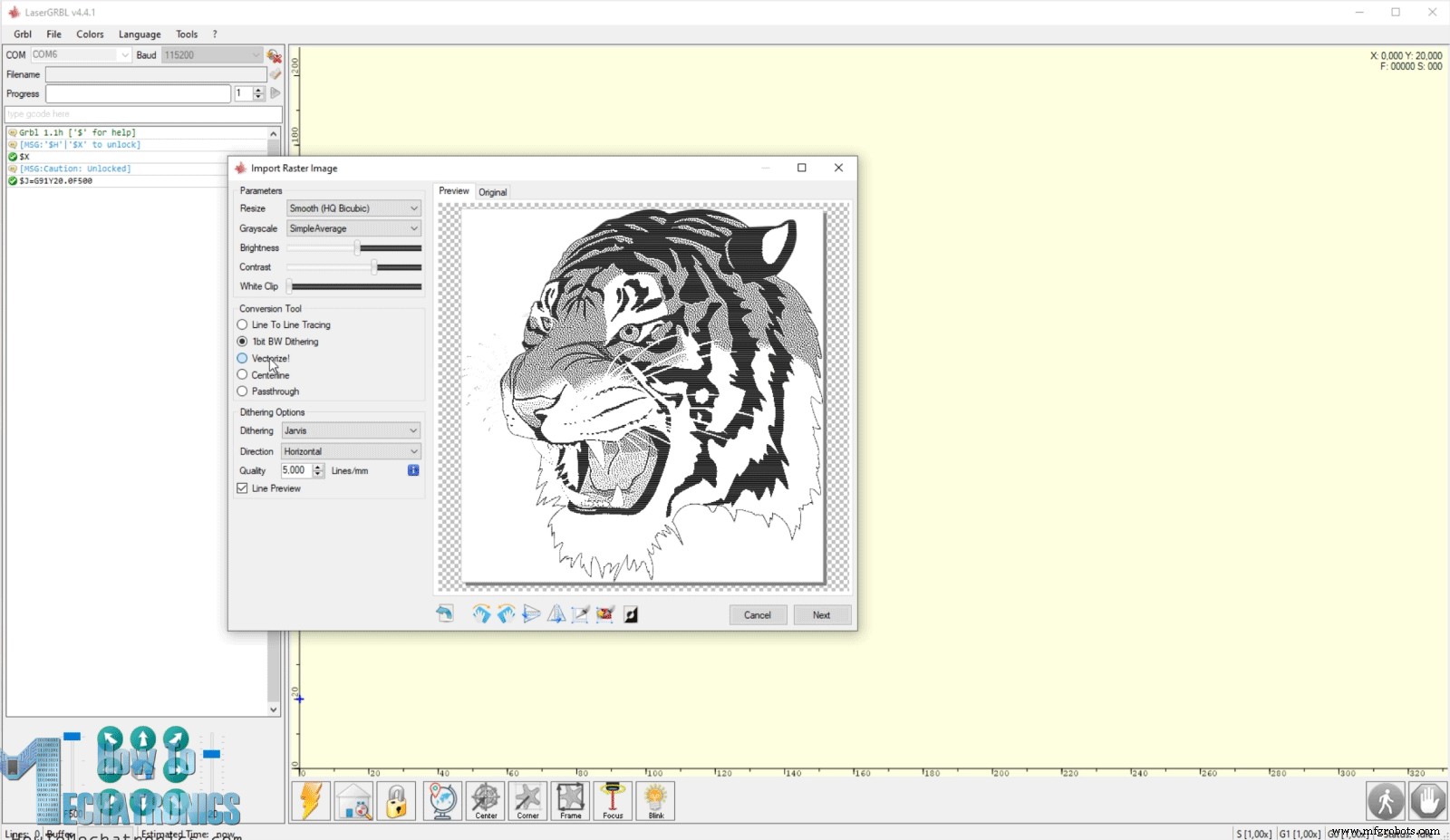
Конечно, если вы хотите, вы также можете сгенерировать G-код с помощью другого программного обеспечения, такого как, например, Inkscape и его плагин Inkscape-Lasertools для создания G-кодов и загрузить их здесь. Я уже объяснял, как использовать этот метод для создания G-кодов, в моем предыдущем видео для лазерного гравера SCARA Robot, так что для получения более подробной информации вы можете посмотреть это видео.
Сейчас я покажу вам, как можно сгенерировать G-код для лазерной гравировки из фотографии с помощью LaserGRBL. Здесь у меня есть фотография собаки, которую я открою с помощью программы.
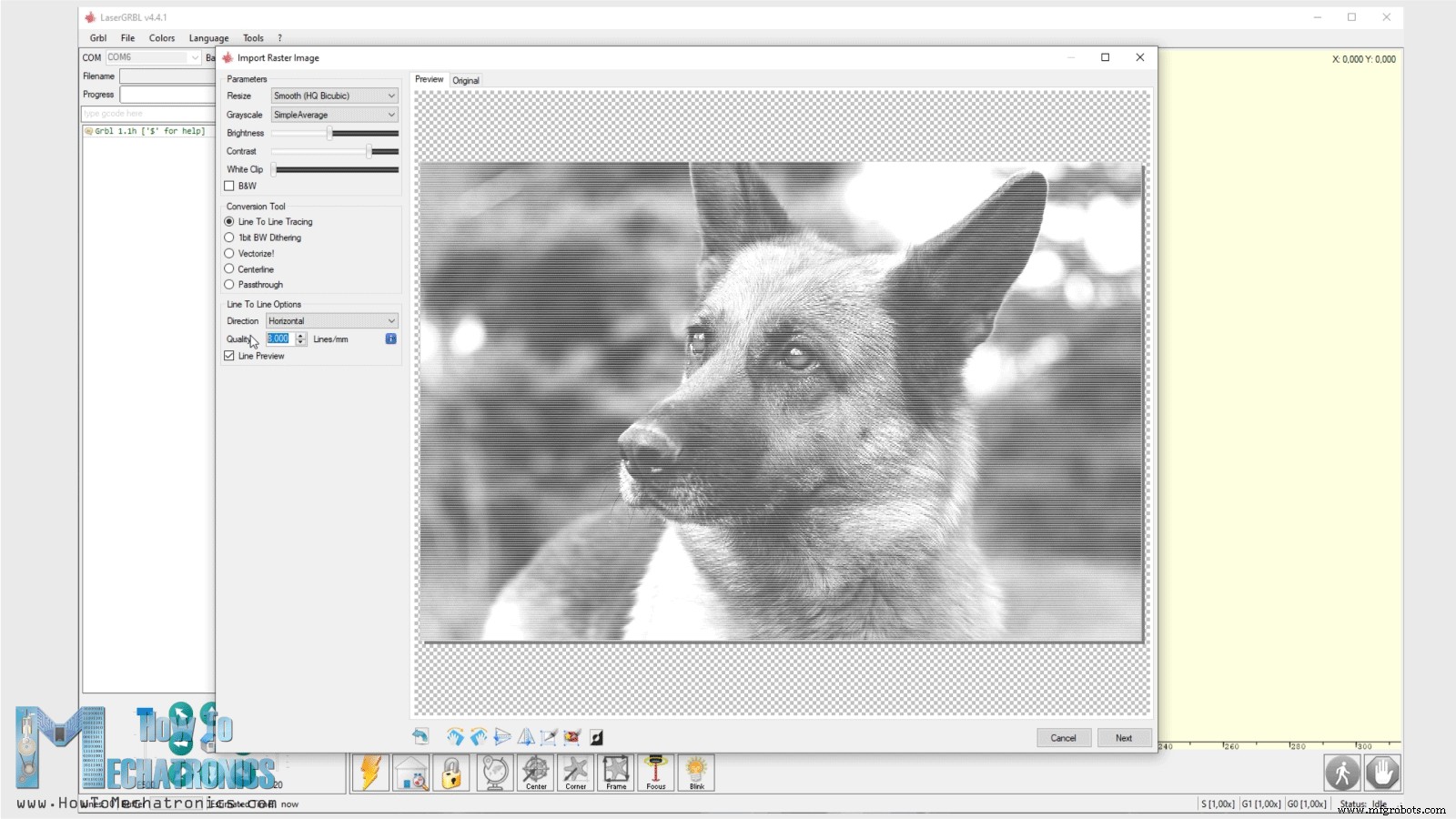
Используя параметр «Яркость и контрастность», мы можем настроить изображение по своему желанию. Мы можем выбрать тип преобразования фотографии, например, трассировка Line-to-Line, 1-битный черно-белый дизеринг или векторный формат. Я буду использовать трассировку от линии к линии для этой фотографии, и здесь мы также можем выбрать направление линии и качество гравировки, которое определяется количеством линий на миллиметр.
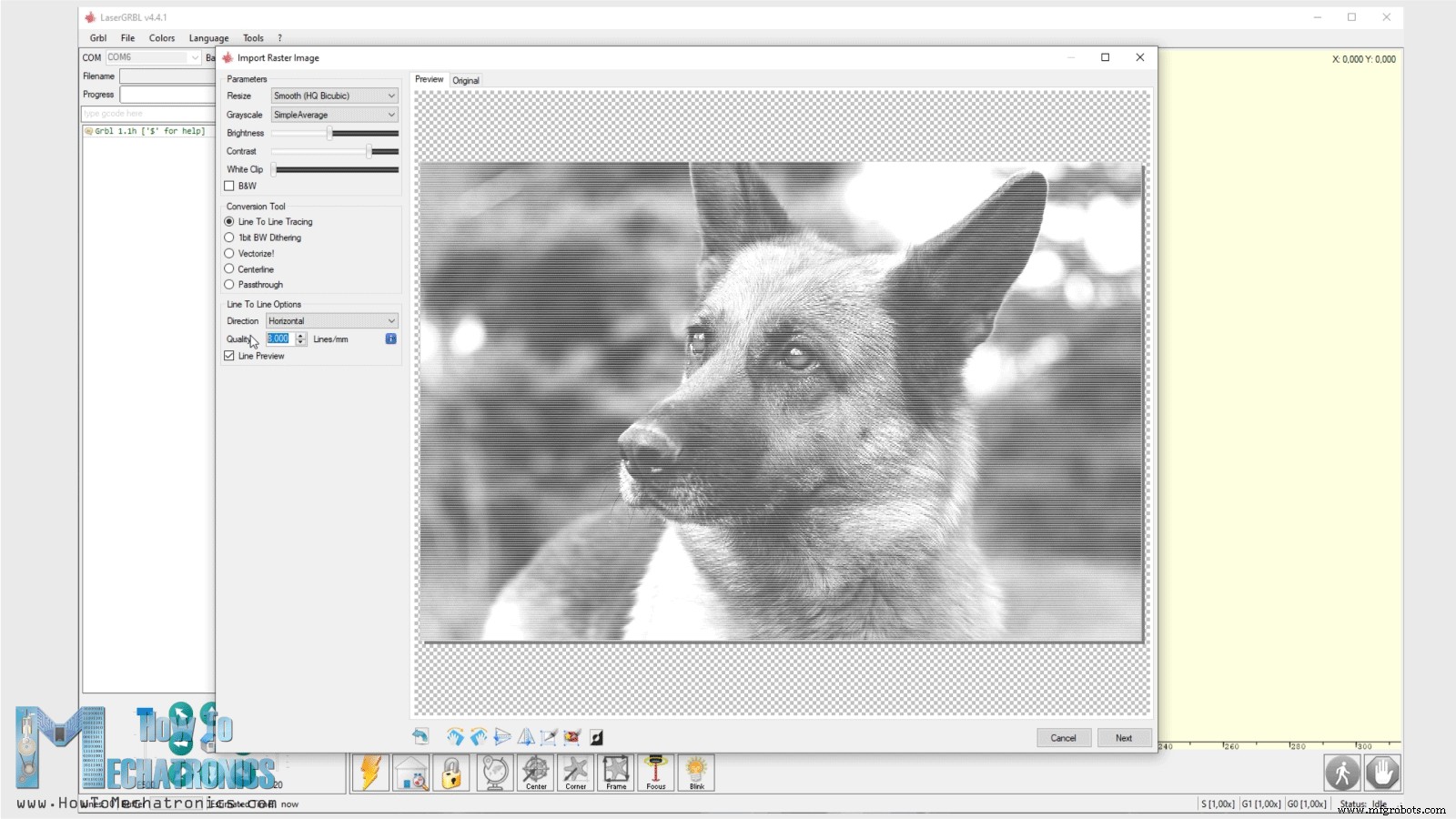
Затем мы можем выбрать скорость гравировки, установить минимальное и максимальное значения ШИМ для мощности лазера и задать размер гравировки.
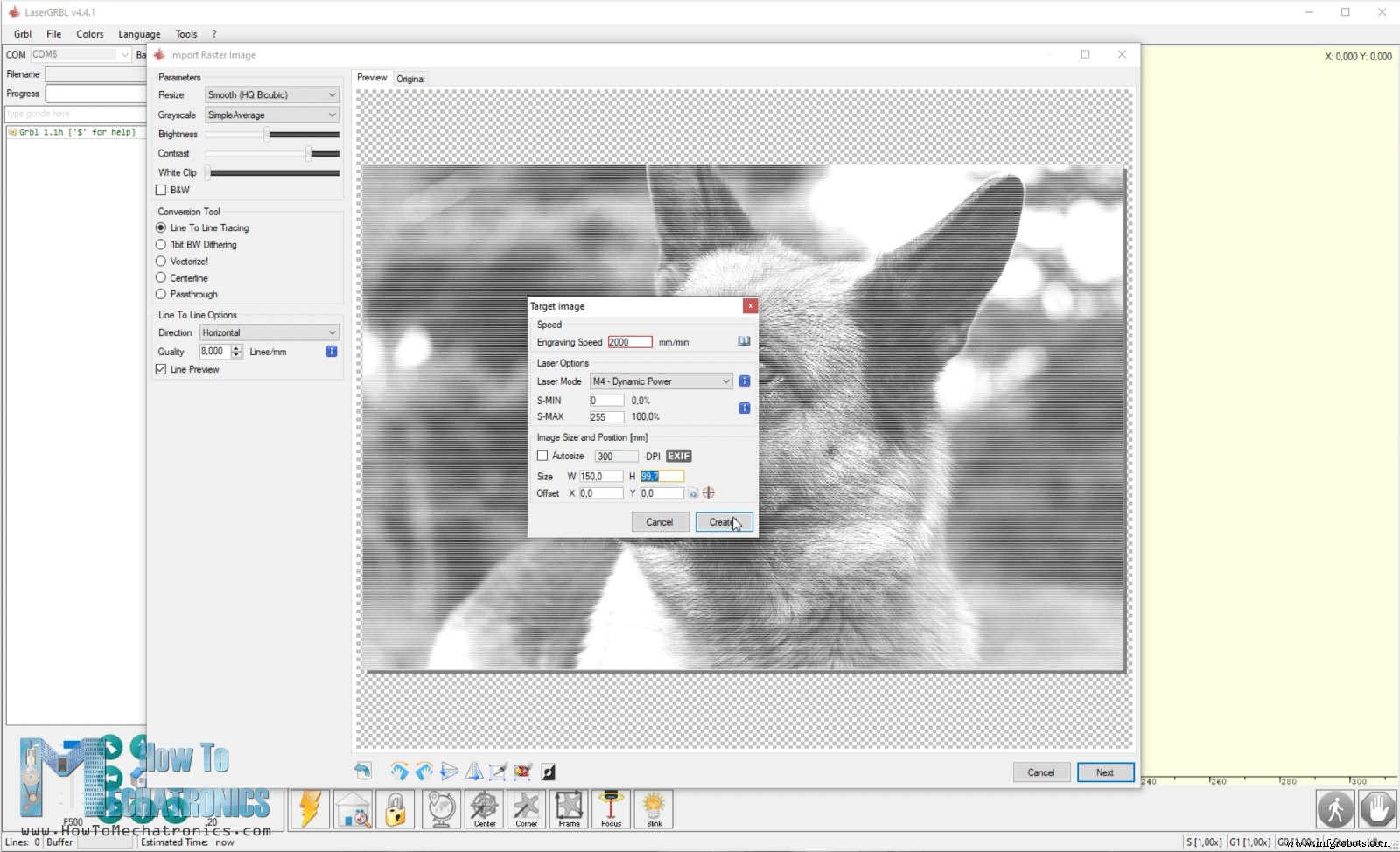
И все, программа сгенерирует G-код для этой гравировки. Прежде чем мы начнем его, мы можем использовать кнопку «Рамка», чтобы наметить или показать нам, где будет происходить гравировка, чтобы мы могли настроить нашу заготовку по мере необходимости.
Обратите внимание, что мы должны использовать очки для защиты от лазера, которые защитят наши глаза от ультрафиолетового излучения лазера, так как это очень опасно.
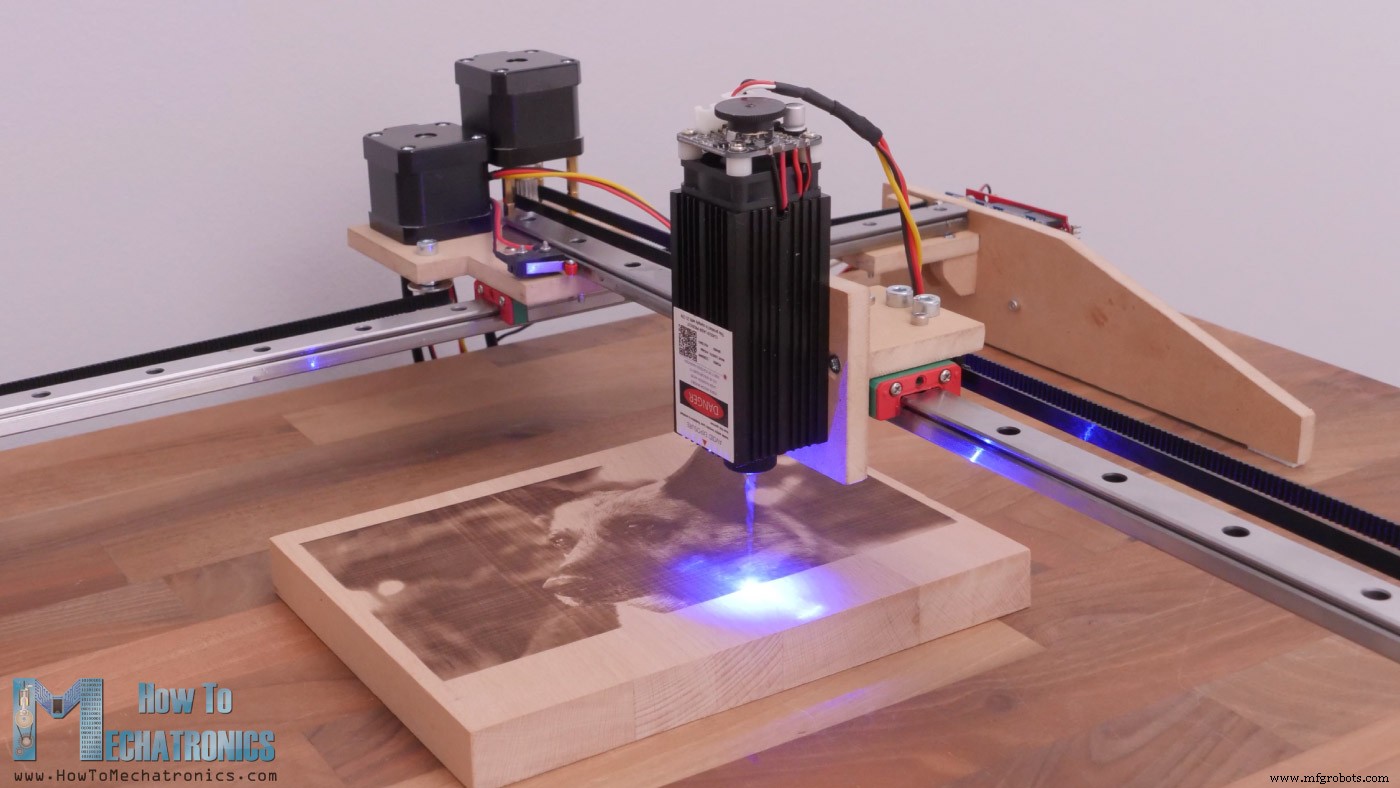
Если мы правильно откалибровали нашу машину, мы можем получить неплохие гравюры. Для калибровки мы могли бы использовать это изображение, которое я сделал, которое имеет квадраты от 100% до 10% прозрачности.
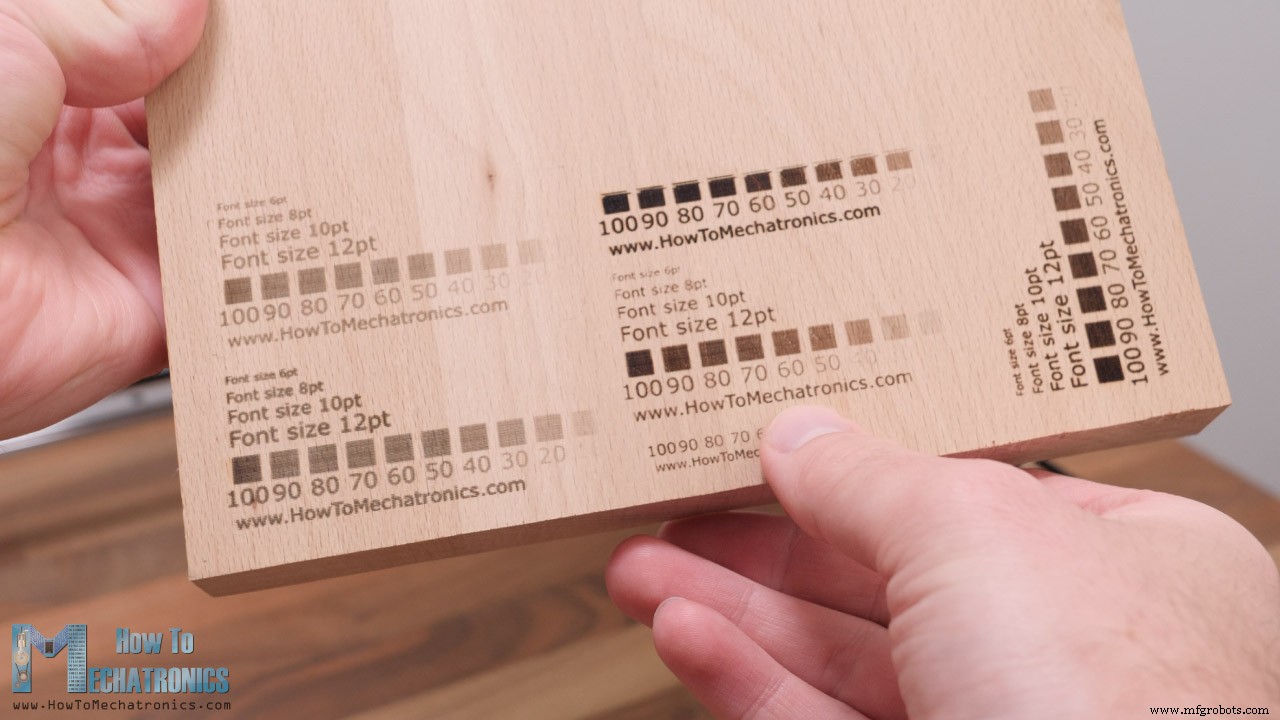
В соответствии с результатами отрегулируйте скорость гравировки и значение ШИМ для мощности лазера.
Здесь вы можете скачать калибровочное изображение:
Итак, это все для этого урока. Надеюсь, вам понравилось и вы узнали что-то новое. Если у вас есть какие-либо вопросы, не стесняйтесь задавать их в разделе комментариев ниже и не забудьте проверить некоторые из моих других проектов Arduino.
Производственный процесс
- для экономии денег на деталях станков с ЧПУ
- Самодельные простейшие часы Numitron IV9 с Arduino
- Маркировка деталей гравировальным наполнителем
- Алюминиевый станок с ЧПУ:преимущества и возможные альтернативы
- Обработка длинных заготовок на токарных станках с ЧПУ с наклонной станиной(2)
- Обработка длинных заготовок на токарных станках с наклонной станиной
- Станки с ЧПУ:типы, детали и преимущества
- 10 прецизионных компонентов, изготовленных на станках с ЧПУ
- Части токарного станка
- Детали и элементы систем станков с ЧПУ