Как мы использовали 3D-печать для проверки конструкции и схемы клапана для нашего аварийного механического вентилятора
Когда в начале 2020 года пандемия COVID-19 стала серьезной проблемой в Северной Америке, было много неизвестных. Как распространялся COVID-19? Каковы были симптомы? Может ли COVID-19 распространяться при отсутствии симптомов? Были ли какие-либо длительные последствия или сопутствующие болезни? Как далеко и как быстро произойдет распространение? Поможет ли ношение масок сдержать распространение? Когда будет готова вакцина?
Однако среди всех этих неизвестных факт был очевиден:если распространение пандемии и количество серьезных случаев росли в геометрической прогрессии, вентиляторы будут иметь решающее значение для надлежащего лечения пациентов. Еще один факт:во многих странах, включая собственную базу Protocase в Канаде, не было достаточного запаса вентиляторов для такого сценария.
На ранних стадиях пандемии COVID-19 федеральное правительство считало Protocase необходимым из-за нашей клиентской базы организаций, работающих в области инноваций, медицины, аэрокосмической и оборонной промышленности. Но помимо того, что мы были открыты и готовы изготавливать нестандартные детали и корпуса для наших клиентов, чтобы они могли продолжать внедрять инновации и разрабатывать новые технологии, команда Protocase хотела внести свой вклад в борьбу с пандемией COVID-19. Проэкт? Создайте функциональный портативный аппарат ИВЛ которые можно было бы быстро изготовить и собрать.
Вызов
После встречи с группой медицинских работников, включая врачей скорой помощи, респираторных терапевтов и других, для обсуждения критериев функционального аппарата ИВЛ наша группа исследований и разработок наметила пневматическую систему. Одной из важнейших частей конструкции аппарата ИВЛ являются клапаны, которые, работая в тандеме с ответвлениями трубок, образуют контур вдоха и выдоха. Команде нужно было найти три распространенных типа клапанов. :обратный клапан, обратный клапан с регулируемым давлением и соленоид.
Одна проблема — готовые к покупке клапаны пользовались исключительно высоким спросом.
«Все как бы набрасывались на версии этих деталей, которые подходили бы для вентиляторов и всех различных решений для борьбы с пандемией. Были некоторые перебои в цепочке поставок», — говорит Джастин Льюис, инженер-механик в группе исследований и разработок Protocase. «После того, как мы немного потрудились, пытаясь заказать нужные нам клапаны, мы решили сделать их сами. Конечные клапаны, по сути, представляют собой версию тех деталей, которые мы могли бы быстро изготовить из того, что у нас было в доме, без необходимости иметь дело со сроками выполнения заказа».
Конструкции клапанов были составлены быстро, поскольку общая конструкция (и обязательные критерии функции клапана) уже были хорошо определены и установлены.
«По сути, нам дали список критериев, которым должны были соответствовать врачи и респираторные терапевты, с которыми мы консультировались», — говорит Джордан Роуз, инженер-механик по исследованиям и разработкам в Protocase. «Основываясь на пневматической конструкции всей системы, вы можете примерно определить, при каком давлении должны действовать эти штуки. Это вторая половина информации, которая нам нужна для продолжения. Мы рассмотрели, как работает обратный клапан, и при каком давлении и скорости потока они должны работать, используя математику, которую мы изучили в инженерной школе».
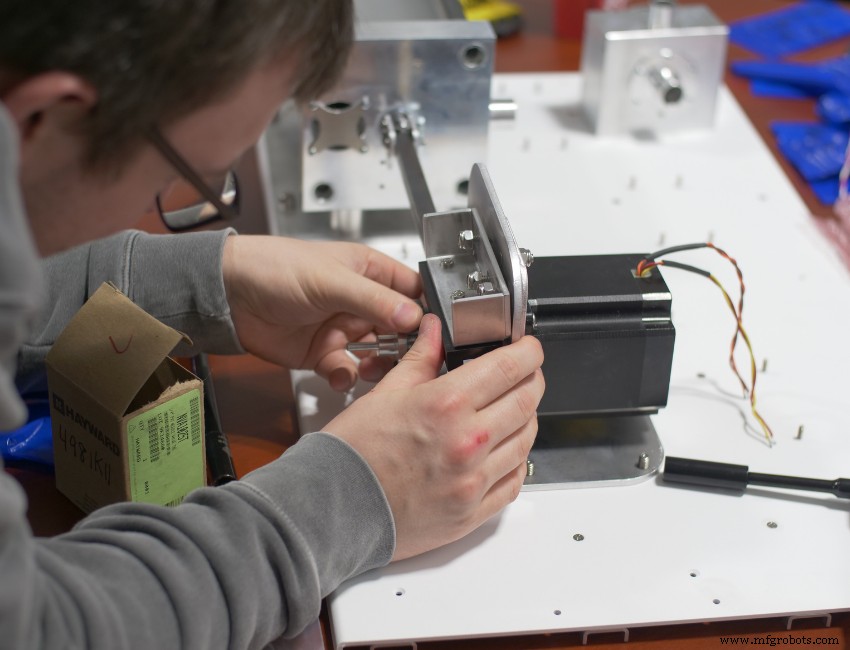
«Это промышленный Lego. Речь идет о том, чтобы увидеть все в целом, все построено из этих основных блоков», — объясняет Льюис. «Это основные блоки — нам просто нужно построить их и соединить вместе в правильном порядке, чтобы все они достигли цели».
После того, как конструкция клапана была хорошо определена, а также были установлены требования к давлению и потоку, команда приступила к работе над созданием первоначальных прототипов. Для этой задачи 3D-печать была логичным первым шагом, так как она позволила бы проверить размеры и проверить расчеты давления и скорости потока.
«Поскольку процесс обработки значительно дольше, важно сначала выполнить 3D-печать деталей для подтверждения спецификаций, — говорит Роуз.
«3D-печать подтвердила правильность всей схемы», — добавляет Льюис. «Это позволило нам собрать все воедино и сказать:«Окей, это работает», прежде чем вкладывать все время и деньги в создание надлежащих механически обработанных деталей».
Команда сделала несколько итераций 3D-печати обратного клапана и регулируемого обратного клапана, пытаясь максимально упростить конструкцию и убедиться, что она работает правильно. Например, в ранней конструкции регулируемого обратного клапана клапан имел круг и выступ на одной стороне.
«Причина, по которой я это сделал, заключалась в том, чтобы увидеть, какая поддержка требуется для этого круглого босса. Потому что в противном случае вам может понадобиться поддерживать его снизу», — говорит Роуз. «Я хотел попытаться избежать каких-либо проблем с поверхностью, чтобы шланг, который был в пневматической системе, подходил должным образом. В конце концов, мы перешли к форме прямой трубы, которая отлично сработала».
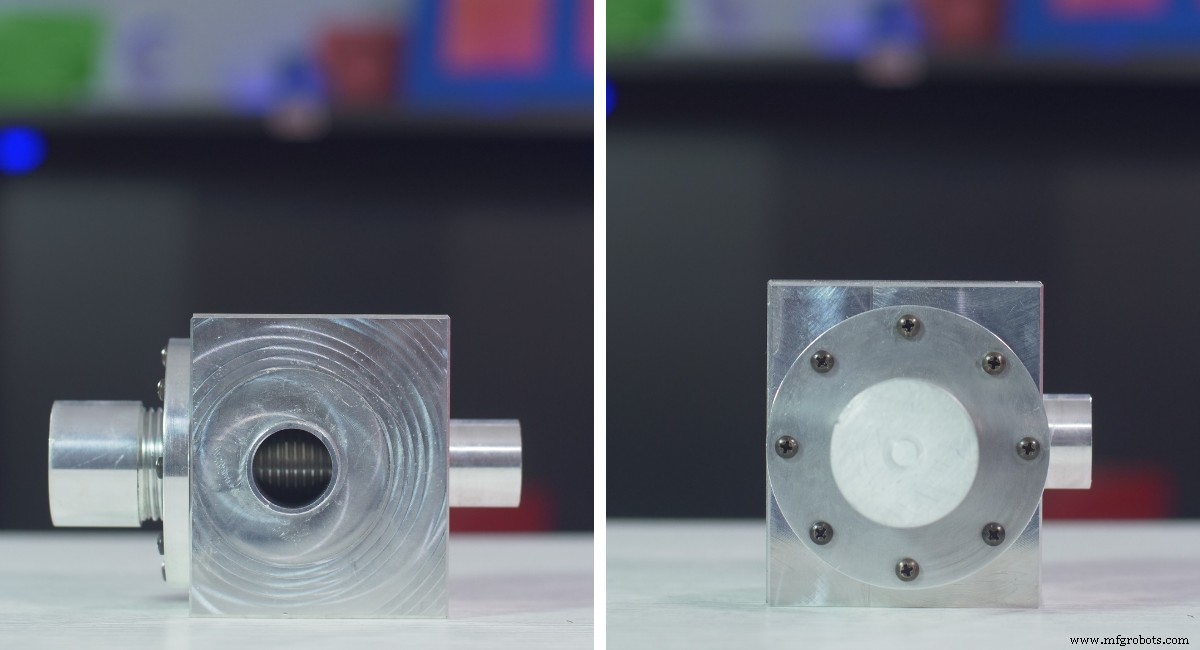
«В целом теория была хороша с самого начала, она больше касалась того, чтобы правильно загерметизировать и убедиться, что у нас есть правильные пружины», — говорит Льюис.
Единственным клапаном, который не был напечатан на 3D-принтере в качестве первоначального прототипа, был пневматический соленоид, и на то были веские причины.
«Снаружи он выглядит просто, потому что это просто большой металлический блок, но внутри него много разных камер», — объясняет Роуз. «Это не то, что можно было бы напечатать в 3D».
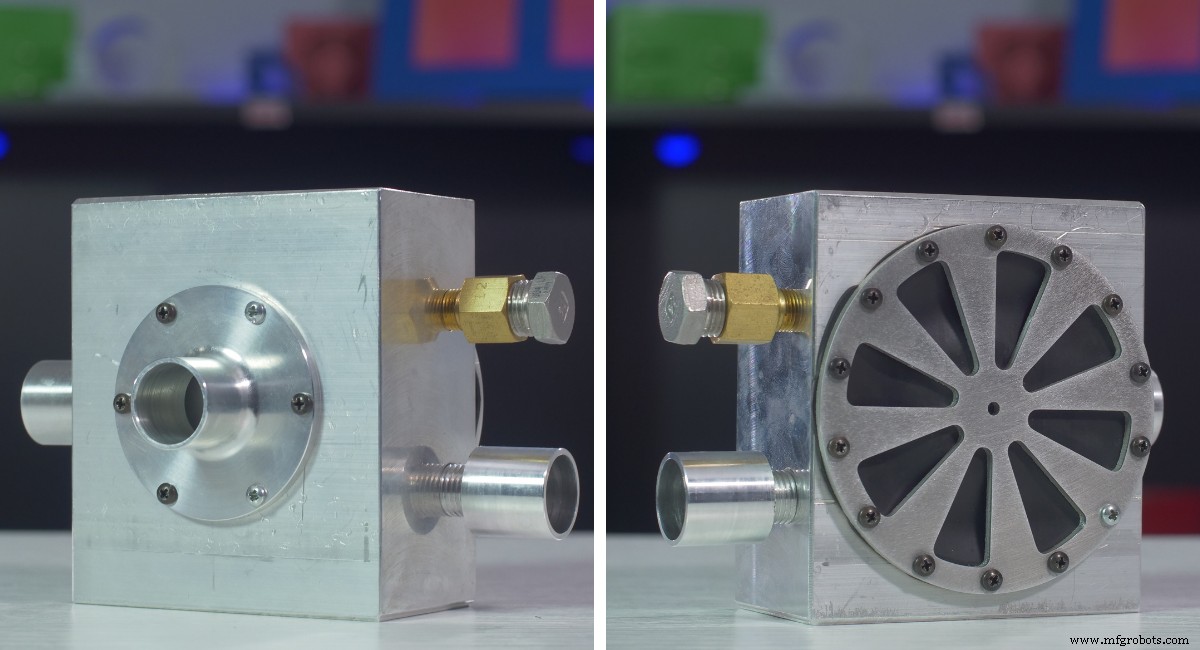
«С помощью 3D-печати может быть сложнее добиться уплотнения вала на материале такого типа», — говорит Льюис. «Отфрезеровав соленоид, мы смогли отшлифовать его до идеальной чистоты и вставить в него подогнанный вал, чтобы все надежно загерметизировалось».
Пневматический соленоид включает в себя все аспекты индивидуального производства Protocase, включая детали токарного станка с ЧПУ, фрезерованные детали, детали из листового металла, детали, напечатанные на 3D-принтере, а также прокладочный материал. Вместо того, чтобы нарезать резиновую прокладку на обычную прокладку, команда вырезала из резины круг с помощью фрезерного станка с ЧПУ, чтобы создать камеру обратного клапана.
Оглядываясь назад — и глядя вперед
В конце концов, использование 3D-печати в первую очередь было чрезвычайно полезным для обеспечения того, чтобы промышленные детали Lego подходили друг к другу и функционировали в соответствии с представленной схемой, не занимая драгоценное время, необходимое для обработки всех деталей на станке с ЧПУ.
«Приятно знать, что вы движетесь в правильном направлении. У вас есть схема, вы собираете все это вместе, а затем говорите:«Ой, подождите, все это устроено неправильно». Были времена, когда мы вносили коррективы в то, как была устроена вся система», — говорит Льюис. «Вы не хотите тратить кучу денег и времени на обработанные блоки, чтобы сделать это. Эти напечатанные на 3D-принтере детали были немного негерметичными, но мы знали, что вся система работает, поэтому мы могли с уверенностью инвестировать в следующий этап».
Даже окончательная версия клапанов, обработанных на станке с ЧПУ, может быть не самой простой и, возможно, неуклюжей по сравнению с готовыми к покупке аналогами на рынке, но на это есть причина, – говорит Роуз.
«Мы разработали их так, чтобы они соответствовали нашим возможностям, потому что, если бы нам когда-нибудь пришлось пойти и обработать 2000 из них, мы могли бы сделать их быстро», — объясняет он. «Мы активно старались не придумывать ничего необычного и не расширять границы нашей обработки».

Как и в случае любого прототипа или разработки продукта, полезно подумать о том, что получилось хорошо, а что можно было бы улучшить. В целом и Роуз, и Льюис сошлись во мнении, что проект остается на прочной основе благодаря оперативному производству, доступному для тестирования макетов и подтверждения спецификаций без каких-либо задержек.
Однако, оглядываясь назад, они видят преимущества использования электрической системы для вентилятора. Систему с электрической системой можно включить, когда вам это нужно, и выключить, когда вам это нужно, с помощью программного обеспечения. Пневматическая система, с другой стороны, имеет вакуумную систему, которая может быть сложной.
«Этот пневматический соленоид похож на игру на музыкальном инструменте», — уточняет Льюис. «Здорово, если вы можете настроить его на выходе, но если что-то изменится, вы не захотите, чтобы в больнице был кто-то, кто действительно знает, как работать с машиной. В идеале вам нужен кто-то, кто может легко отрегулировать ручку. С точки зрения чего-то, что мы могли бы сделать быстро внутри компании, система, которую мы спроектировали и построили, великолепна, но с марта мы узнали, что линии снабжения несколько вернулись в нормальное состояние, и мы, возможно, могли бы использовать электрическую систему. .”
«В то время это была единственная вещь, которую мы не могли получить — электрический соленоид», — добавляет Роуз. «Все были в панике. Теперь их намного проще найти.
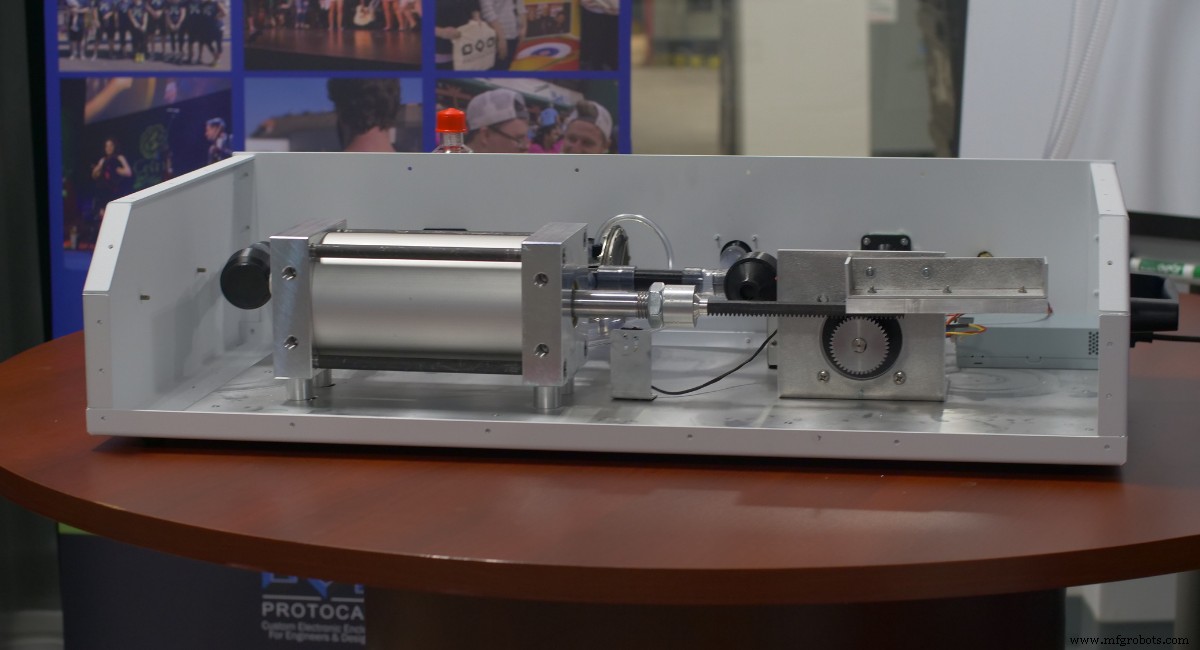
Глядя на общую картину, проект аппарата ИВЛ, включая проектирование и изготовление трех клапанов, помог определить работу команды разработчиков Protocase.
«Когда появился этот проект, казалось, что это глобальная чрезвычайная ситуация. Мы бросили все остальное и собрались вместе», — говорит Роуз. "При выполнении этого проекта мы поняли, что можем остановить другие наши проекты, чтобы сосредоточиться только на одной или двух вещах и действительно сузить круг задач".
Вместо того, чтобы слишком распыляться или изолироваться от работы друг друга, группа исследований и разработок теперь сосредоточилась на работе в команде.
«У нас есть конкретные цели, над которыми мы все можем работать вместе, и мы можем объединить наши ресурсы», — объясняет Льюис. «Это просто изменило то, как все работают над проектами, теперь мы почти относимся к каждому проекту как к своего рода чрезвычайной ситуации. Этот проект стал катализатором многих улучшений в нашем отделе исследований и разработок».
Промышленные технологии
- Как подготовить холодовую цепочку к требованиям вакцины COVID-19
- Как логистика изобразительного искусства меняет рынок искусства к лучшему
- Как подготовиться к следующему нарушению цепочки поставок
- Как обеспечить аварийную готовность на складе
- Каковы преимущества 3D-печати для производителей металла?
- Четыре новые возможности для алюминиевой промышленности
- Что такое Автокад? Как это работает и для чего используется
- Некоторые измерительные инструменты, необходимые для обработки механических деталей
- Как 3D-печать используется в производстве пресс-форм
- Что такое RFID-метки? Узнайте, как работают метки RFID, для чего они используются и о некоторых недостатках технол…