Что такое планирование процесса | Этапы планирования процесса, типы, преимущества
В этой статье вы узнаете о Что такое планирование процессов. ? Каковы требования Каковы этапы планирования процесса для этого процесса? , типы , преимущества , недостатки и последовательность включенных видов деятельности. Начнем с Определения. .
Что такое планирование процессов?
Планирование процесса процедура, используемая для разработки подробного перечня производственных операций, необходимых для изготовления детали или изделия. Это связь между дизайном продукта и производством продукта.
Планирование процесса устанавливает эффективную последовательность операций, выбирает надлежащее оборудование и инструменты и определяет их операции таким образом, чтобы продукт соответствовал всем требованиям, указанным в спецификации. При этом процесс будет выполняться с минимальными затратами и максимальной производительностью.
В основном есть два способа создания планов процессов. Они есть :
1. Планирование процесса вручную и 2. Автоматизированное планирование процессов
ТРЕБОВАНИЯ К ПЛАНИРОВАНИЮ ПРОЦЕССА
Достаточно хороший технологический план должен удовлетворять следующим требованиям:
<сильный>1. Краткое описание выполняемой работы, четко и исчерпывающе определяющее ее сервисную функцию.
2. Спецификации и стандарты, определяющие сервисную функцию.
3. Рабочие чертежи работы с полной спецификацией.
4. Рисунок заготовки.
5. Данные о количестве деталей, которые должны быть изготовлены за период. запасные части, необходимые для каждой единицы.
6. Общее количество деталей, которые должны быть изготовлены за период.
7. Данные об оборудовании, включающие технические характеристики и данные о мощности станков и другого имеющегося оборудования, данные о размещении и загрузке оборудования в цехе.
8. Условия, при которых должны быть организованы и осуществлены технологическое проектирование и производство, т. е. новые или существующие заводы, имеющееся на заводе оборудование, возможность получения нового оборудования и т. д.
9. Расположение завода.
<сильный>10. Наличие рабочей силы для укомплектования завода.
11. Дата начала работ и дата сдачи.
После понимания основных требований следующим шагом будут этапы планирования процесса. .
Процесс Этапы планирования
Целью планирования процесса является определение и описание наилучшего процесса, необходимого для производства детали. Для достижения этих целей можно выполнить следующие этапы планирования процесса:
1. Ознакомиться с сервисной функцией детали.
2. Изучить и критически проанализировать производственные спецификации и различные стандарты, например, точность, производительность, эффективность и т. д., которые определяют сервисную функцию.
3. Ознакомиться с годовым выпуском продукции.
4. Изучить и критически проанализировать рабочие чертежи, чтобы увидеть, возможно ли во всех отношениях изготовить деталь, а также выявить и исправить любые ошибки в чертежах.
5. Определить, какие детали производить и какие приобретать, с их полной идентификацией и необходимым количеством.
6. Подготовить список сырья надлежащего качества и количества, которое будет закуплено со стороны, с указанием их формы, размера и особых свойств.
<сильный>7. Выбрать наиболее экономичный процесс получения заготовок и определить объемы производства для целей калькуляции.
8. Определить наиболее экономичный процесс изготовления деталей с учетом текущих производственных обязательств, даты поставки, количества, которое необходимо произвести, и стандарта качества.
9. Определить наилучшую последовательность операций, выполняемых над каждой деталью в конкретном процессе.
10. Подобрать станки, которые будут выполнять операции с требуемой точностью.
11. Чтобы выбрать любые другие аксессуары и оборудование, такие как приспособления, приспособления, штампы, калибры и т. д., которые могут потребоваться для повышения производительности.
12. Располагать оборудование и рабочие места, рассчитывать нагрузки на машины и вносить необходимые коррективы в процессе.
13. Пересмотреть процесс, чтобы исправить все ошибки и недостатки, обнаруженные при реализации процесса в реальном производстве.
14. Для определения этапов контроля, процедуры контроля и предельных калибров, необходимых на разных этапах производства для точного и быстрого контроля.
15. Определить время наладки и стандартное время для каждой операции и зафиксировать ставку платежей.
16. Определить вид труда для успешного выполнения задания.
17. Чтобы определить предполагаемую стоимость продукта, чтобы увидеть, будет ли он реализован на рынке продаж.
Стоит отметить, что планирование процесса является динамическим для упрощения обработки с учетом процесса технологических изменений, и планировщики должны анализировать производственный процесс в производстве.
Некоторые из вышеупомянутых шагов в планировании процесса, которые требуют дальнейшего объяснения, изложены ниже более подробно.
Производственные характеристики: Основным документом, в котором перечислены производственные спецификации, является рабочий чертеж. На чертеже указано:
1. Размеры и точность обработки с допустимым отклонением от правильной геометрической формы.
<сильный>2. Точность согласования различных поверхностей с допустимым отклонением.
3. Места, подлежащие термической обработке, и вид требуемой термической обработки. 4. Качество поверхности.
5. Метод механической обработки, необходимый для получения заданной чистоты поверхности, если это необходимо.
6. Места защитного покрытия с указанием типа и толщины этого покрытия. 7. Расположение места для измерения размеров на готовой детали. 8. Специальные процедуры проверки, такие как рентген, гидравлические испытания, если это необходимо.
Наконец, спецификации должны быть согласованы с процессом обработки и контролем в максимально возможной степени. При необходимости могут быть внесены небольшие изменения или поправки, чтобы планирование было успешным.
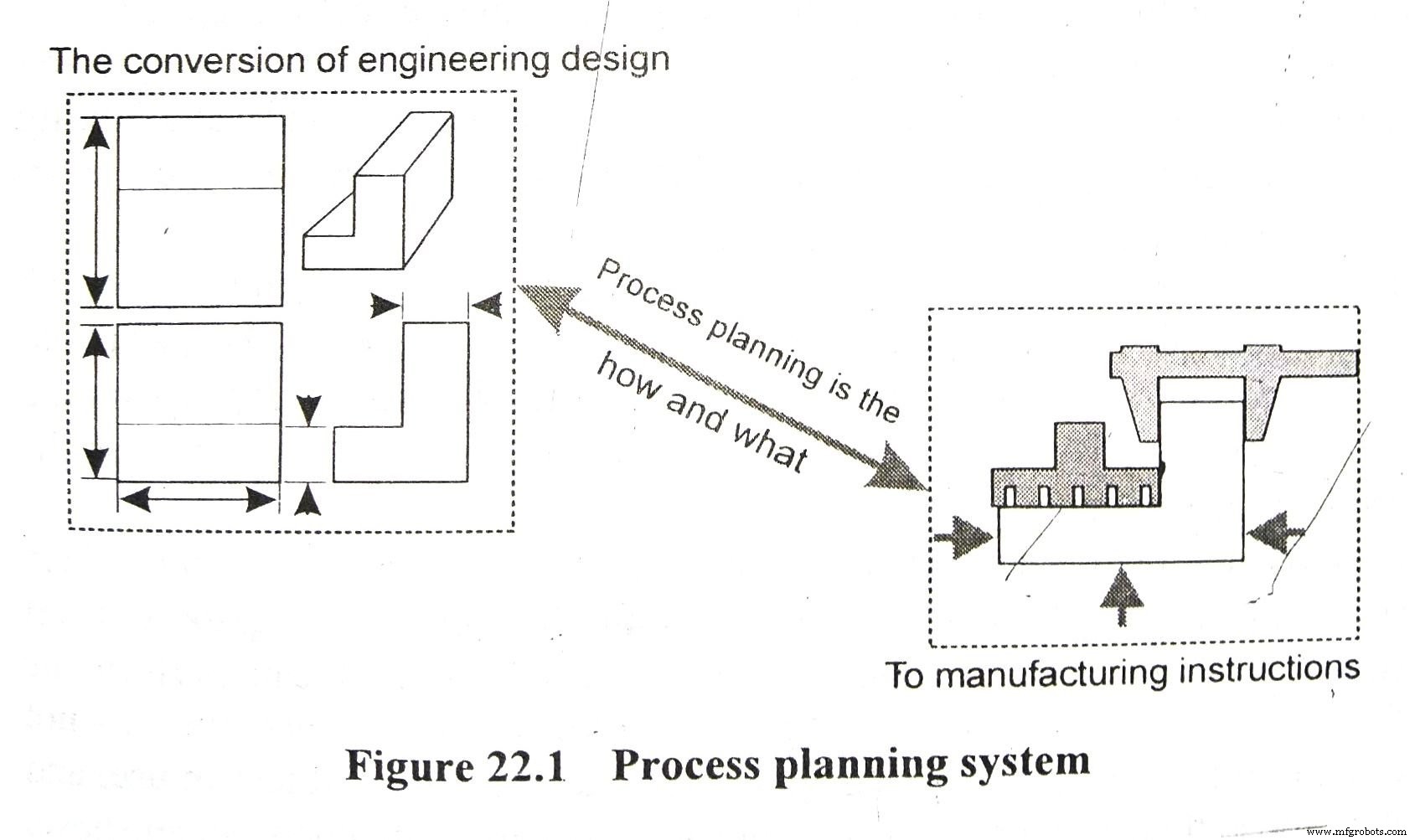
Определение пробела: Планирование процесса фактически начинается с выбора заготовок. Размер заготовки и характеристики готовой детали взаимосвязаны и определяют общий контур операций механической обработки и отделки.
Точность заготовки, зависящая от способа ее изготовления, и характеристики готовой детали определяют общую схему процесса обработки и ее подразделения на черновые, получистовые и чистовые операции.
Выбор станков :марк> Следующим этапом планирования процесса является выбор станков, который во многом определяется выбором метода или процесса обработки детали. Другими словами, принципы, управляющие процессами механической обработки, должны лежать в основе выбора станков. Несмотря на то, что трудно сформулировать определенное правило выбора станка для любого типа обработки, при выборе станка для конкретной операции необходимо учитывать следующие факторы:
1. Размер, форма и материал заготовки.
<сильный>2. Требуется точность и чистота поверхности.
<сильный>3. Требуемая производительность и производительность станка.
<сильный>4. Мощность станка, чтобы узнать, достаточна ли она для выполнения операции или нет.
5. Выполнение операции, чтобы узнать, является ли это экономичным или нет. 6. Легкость и удобство в работе на станке.
Диаграммы доступности :марк> Таблица наличия представляет собой список станков, упорядоченный по классам (т. е. классифицированный список), например, токарные станки с двигателями, токарно-револьверные станки, автоматические станки и т. п., с указанием их идентификации и номера модели, местоположения, общего состояния, доступного инструмента, скорости резания. и подачи и т. д. Однако, в случае новых станков, скорости резания и подачи получаются из имеющегося у них каталога. Эта таблица доступности необходима при выборе станков для нового продукта на существующем заводе.
График нагрузки машины показывает, какая машина простаивает, а какая загружена. Соответственно, планировщик процесса выберет конкретный станок, который может быть использован для выполнения операции механической обработки. Планировщик процессов не столько заботится о графике загрузки машин, сколько планировщик производства.
Таблицы возможностей :марк> Диаграмма возможностей может быть определена как диаграмма, которая показывает способность станка выполнять работу. Диаграмма возможностей показывает, какую часть своей номинальной мощности станок может удовлетворительно выполнять. Станок, как и любой другой станок, не остается в том же состоянии, в котором он был куплен, из-за износа в процессе эксплуатации и со временем теряет свою точность. Диаграмма возможностей, показывающая текущее состояние машины, служит руководством для планировщика процесса при выборе подходящей машины.
ПЛАНИРОВАНИЕ ПОСЛЕДОВАТЕЛЬНОСТИ ОПЕРАЦИЙ
Определение наилучшей последовательности операций является одним из важных шагов в процессе планирования и реализации продукта, предназначенного для производства. И стоимость продукта, и качество продукта тесно связаны с последовательностью операций. Различная последовательность выполняемых операций приведет к различному времени работы, различному времени транспортировки к рабочему центру, различному инструментарию с учетом различных установочных и зажимных поверхностей.
Если для продукта создается новый завод, планировщик процесса имеет гораздо больше свободы в определении последовательности операций, которая может лучше всего подходить для этой цели. В случае существующей установки последовательность операций для нового продукта должна определяться на основе имеющегося оборудования и условий загрузки оборудования. В последнем случае планировщику процесса должна быть предоставлена следующая информация:
- Список доступных машин.
- Список доступных инструментов общего назначения.
- Возможности оборудования.
- График нагрузки машины.
- Стандартные данные.
Однако в любом случае существуют определенные фундаментальные принципы, которых необходимо придерживаться при планировании оптимальной последовательности операций. . Это:
1. Сначала следует с должным вниманием выбрать базовые поверхности. Выбор данных влияет на все последующие операции механической обработки и проверки. Поверхность, которая должна остаться необработанной, должна быть выбрана в качестве первой опорной поверхности наладки только в случае первой операции обработки. В последующих операциях установочной базой могут служить только обработанные поверхности.
2. Поверхности, обработка которых не уменьшит жесткость работы в сколько-нибудь заметной степени, должны быть обработаны раньше в последовательности.
3. Внутренние операции выполняются раньше внешних операций. Это не правило, которое нужно всегда соблюдать. Основная причина для выполнения внутренних операций Первым является то, что внутренние поверхности с меньшей вероятностью будут повреждены при обработке материалов и последующих процессах, поэтому их поверхности часто обеспечивают лучшее средство удержания работы и, таким образом, помогают обеспечить концентричность между внутренним и внешним диаметрами.
4. Операция в последовательности должна начинаться с удаления самого большого слоя металла. . Удаление толстых слоев тяжелыми надрезами выявит внутренние дефекты сырья (обычно отливок или поковок) гораздо быстрее, чем легкие надрезы. Заготовка также снимается с внутренних напряжений, что исключает опасность коробления при последующих операциях.
Большие усилия резания и зажима, которые могут быть связаны с тяжелым резанием, влияют на точность обработанных поверхностей другой части той же заготовки и требуют использования тех станков, которые предназначены для черновых операций. Кроме того, грубая или черновая обработка обычно выполняется быстрее с менее дорогими рабочими, чем чистовая обработка.
<сильный>5. Операции, в которых ожидается повышенное количество брака из-за выявления дефектов, как указано выше, должны выполняться как можно ближе к началу последовательности машин. Всегда полезно узнать, что работа над дефектным материалом выполняется как можно скорее с наименьшими затратами на вторичные процессы.
6. Отделочные операции следует выполнять в конце последовательности операций для снижения опасности повреждения готовых поверхностей, изменения их размеров и согласования по отношению к другим поверхностям детали.
<сильный>7. Черновые и чистовые операции следует выполнять на отдельных станках, чтобы точность станков, предназначенных для чистовой обработки, не нарушалась большими нагрузками при черновых работах.
8. Этапы проверки следует ввести (a) после черновой обработки (b) перед операциями, которые должны выполняться в других цехах и отделах, (c) перед трудоемкой и ответственной операцией (например, перед подготовкой опорных поверхностей) и после них, а также (d) после лазерной обработки.
<сильный>9. Последовательность операций механической обработки должна быть согласована с операциями термообработки. которые имеют жизненно важное значение при изготовлении деталей машин. Деформация рабочего места после термической обработки потребует увеличения припусков на последующие операции для необходимой коррекции геометрической формы детали механической обработкой.
<сильный>10. Обработка материалов является необходимостью любой производственной деятельности, поскольку она применяется к перемещению сырья, деталей в процессе производства, готовой продукции, упаковочных материалов и утилизации отходов. Таким образом, последовательность операций и обработка материалов тесно связаны. Это прибыльная область для возможного снижения затрат, и она занимает большую часть производственных затрат. Поэтому современная тенденция заключается в том, чтобы механизировать систему обработки везде, где это возможно.
11. По возможности следует избегать ожидания материалов на складах, а также в процессе производства, поскольку это связано с различными стоимостными параметрами, связанными с ними. Поэтому, насколько это возможно, они расположены рядом с местом использования для минимальных затрат. .
Последовательность операций не является жесткой. Он варьируется от продукта к продукту и даже в одном и том же продукте. Всегда есть возможности для улучшения, и их следует постоянно пересматривать для разработки лучших методов, повышения производительности и снижения затрат.
Процесс Лист планирования
Лист планирования процесса — это подробная запись, в которой вся информация, относящаяся к различным операциям, необходимым для изготовления детали, указана в табличной форме. Это также известно как аналитический лист. , инструкция , рабочий лист или схема процесса . Пример листа процесса приведен в таблице 22.1.
Описание операций и их элементов, указанных в технологической карте, должно давать предельно сжатую, но исчерпывающую информацию о том, что предстоит сделать и зачем. Данные должны четко указывать, как и чем должна быть выполнена работа и, если возможно, затраты времени, которые потребуются для ее выполнения.
Форма таких листов может варьироваться для разных условий производства. Характер технологической карты будет зависеть главным образом от масштабов производства и степени важности производимого продукта. Кроме того, различные типы листов используются в производственных концепциях, которые уже работают, и в организациях, проектирующих новые заводы.
Однако в большинстве случаев в таблицах процессов указана следующая информация:
1. Информация о заготовке, включая название, чертеж и сервисную функцию, если это возможно.
2. Информация о заготовке, включая материал, размер запаса при использовании в качестве заготовки, характер и т. д.
<сильный>3. Описание и номера операций и их элементов.
4. Информация о производственном оборудовании, таком как принадлежности к машинам, инструменты, вспомогательное оборудование и т. д.
5. Данные о приспособлениях, приспособлениях и инструментах, такие как описание, размеры или кодовые номера.
<сильный>6. Элементы стандартного времени, такие как время схватывания, время обработки, время обработки и т. д.
<сильный>7. Рейтинг рабочего места работника по каждой операции.
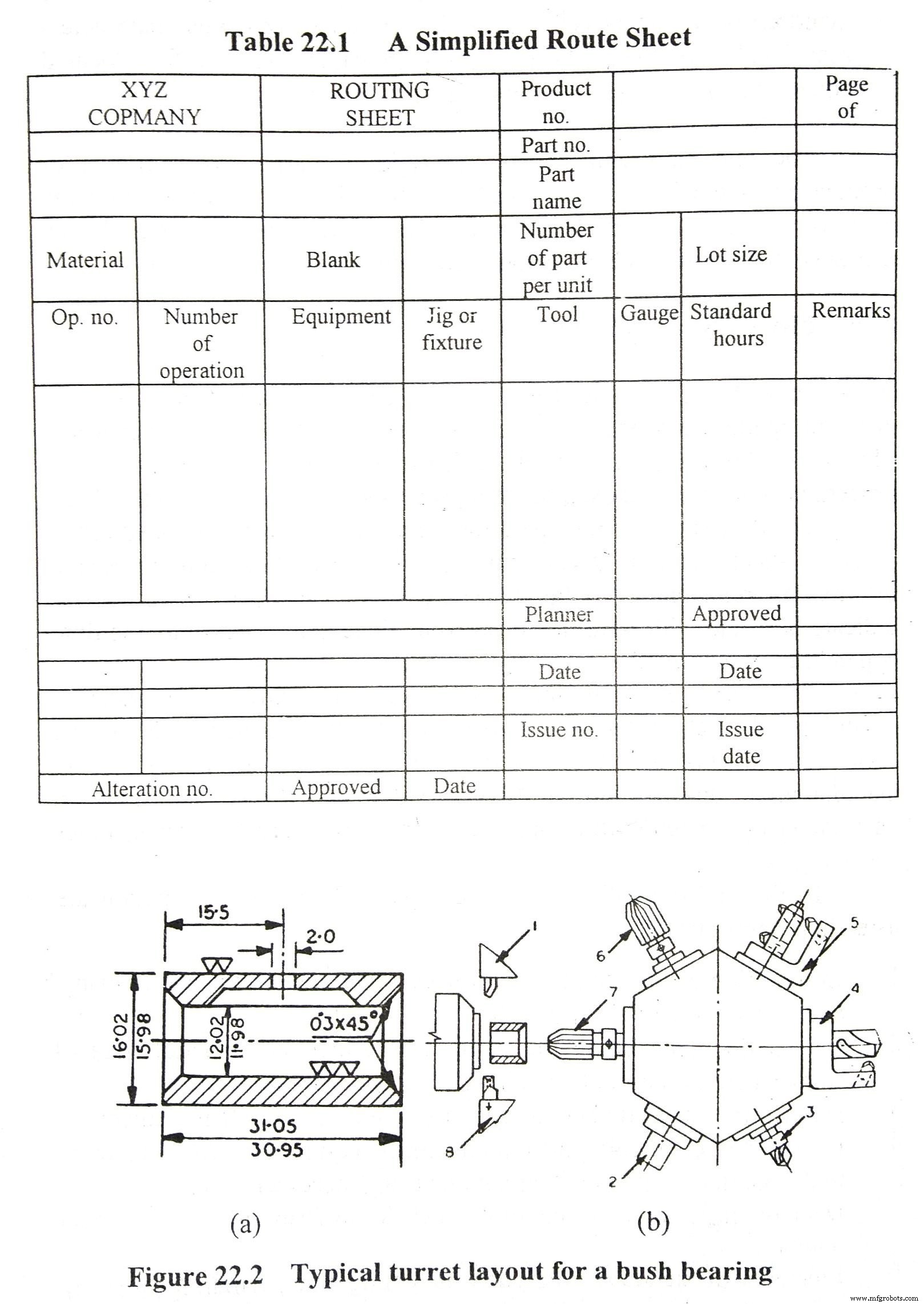
При планировании производственных процессов для операций механической обработки часто рисуются эскизы операций для различных операций, как показано на рис. 22.2. Поверхности, которые должны быть обработаны с заданным допуском.
Пример последовательности операций
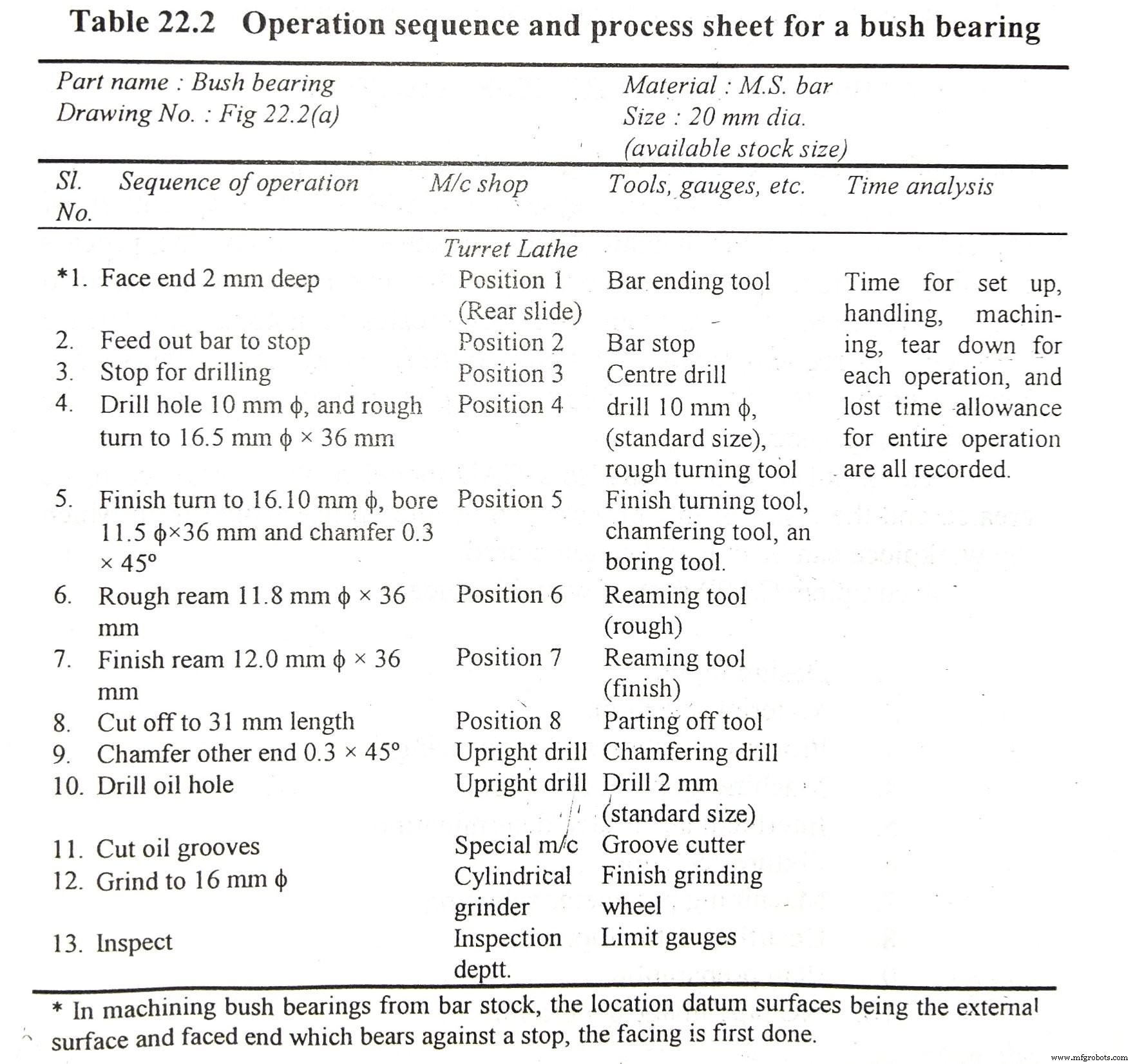
Недостатки ручного планирования процессов
Ручное планирование процессов (MPP) имеет много недостатков. Они:
- MPP во многом субъективны.
- Качество плана процесса напрямую связано с навыками и опытом планировщика.
- Внесение изменений в процесс чрезвычайно сложно.
- Технологические изменения или изменения размеров партий требуют изменения технологического плана. MPP медленно реагируют.
- Трудно проверить, является ли план процесса последовательным и оптимизированным. Если он не оптимизирован, он будет указывать на чрезмерные требования к инструментам и материалам.
- Утомительно вручную искать технологические планы однотипных деталей в большом количестве документации компании.
Компьютерное планирование процессов
Автоматизированное планирование процессов (CAPP) стала наиболее важным связующим звеном с интегрированными системами CAD/CAM. CAPP — это компьютерное приложение, помогающее человеку планировать процесс в выполнении функции планирования процесса. CAPP также не сокращает время и усилия, необходимые для подготовки согласованных планов процессов, а только создает автоматизированный интерфейс между автоматизированным проектированием (CAD) и автоматизированное производство (CAM) для достижения полной интеграции в производственную систему.
Входными данными этого процесса является CAD-модель создаваемой детали, а результатом этого процесса является подробный план процесса, на основе которого может быть создана/изготовлена заготовка.
Полная система CAPP будет включать:
1. Ввод дизайна.
2. Выбор материала.
3. Выбор процесса и последовательность.
4. Выбор машины и инструмента.
5. Определение промежуточной поверхности.
6. Выбор приспособления,
7. Выбор параметров обработки.
8. Оценка стоимости/времени.
<сильный>9. Подготовка плана.
10. Генерация изображения ленты ЧПУ.
Два основных подхода к автоматизированному планированию процессов:
1. Вариант и 2. Генеративный
1 . Вариант метода
Вариантный метод: Планирование вариантов процесса исследует сходство между компонентами (деталями) и выполняет поиск в базе данных для получения стандартного плана процесса для семейства деталей, к которому принадлежит компонент. План извлекается и модифицируется для создания подходящего плана для новой детали.
При вариантном подходе план процесса создается в два рабочих этапа. Они есть :
1. Подготовительный этап и 2. Стадия производства.
Подготовительный Этап
На подготовительном этапе существующие компоненты кодируются, классифицируются и группируются в семейства деталей. Классификация и кодирование предлагают относительно простой способ определения сходства между частями. Впоследствии семейства деталей могут быть сформированы путем группирования похожих деталей.
Устанавливаются различные схемы кодификации. MICLASS, DCLASS, OPITZ, CODE — вот некоторые из схем классификации. После формирования семейств деталей каждой семье присваивается типовой план. Стандартный план состоит из набора процессов обработки, который представляет собой общий набор процессов для изготовления деталей.
Производство Этап
На стадии производства поступающий компонент кодируется на основе его геометрических характеристик или требований к обработке. Здесь используется та же схема кодификации, что и на подготовительном этапе. Результирующий код используется в качестве основы для присвоения детали семейству деталей.
Если система кодирования используется эффективно, часть должна быть аналогична другим частям, принадлежащим к ее семейству. Технологический план для новой детали можно получить, изменив стандартный (семейства деталей, к которому принадлежит новая деталь) план, полученный из базы данных.
2 , Генеративный метод
Генеративный метод: Генеративное автоматизированное планирование процессов (GCAPP) синтезирует производственную информацию для создания плана процесса для нового компонента (детали). Логика принятия решений и методы оптимизации закодированы в самой системе, что приводит к минимальному или полному отсутствию участия человека в планировании процессов.
Генеративная система создает полный план процесса из инженерного чертежа или файла САПР.
Три области систем GCAPP:
<сильный>1. Определение компонента в терминах файла САПР. Он содержит характеристики детали и спецификацию детали.
2. Идентификация, сбор и представление знаний планировщика процессов. При этом учитываются обоснования решений, принятых планировщиком процессов в отношении выбора процессов, последовательности и т. д.
3. Совместимость логики планировщика
В GCAPP проектные спецификации вводятся в систему. Логика принятия решения распознает материал заготовки и особенности обработки детали. Кроме того, он определяет оптимальную последовательность операций, а также оптимальные типы и расположение приспособлений.
Недостатки генеративного автоматизированного планирования процессов
В системах GCAPP наблюдаются следующие недостатки.
<сильный>1. Ограниченное использование до настоящего времени. Требуемая информация (например, допуски) обычно недоступна в модели САПР.
2. В систему необходимо добавить много знаний, чтобы она могла обрабатывать все различные типы подаваемых деталей.
<сильный>3. Из-за большой степени сложности алгоритмов и огромных вычислительных затрат некоторые системы специализируются на разработке планов для определенных типов геометрии. Некоторые системы доходят до проверки технологичности детали и предложения изменений в конструкции, если это необходимо.
Итак, вы узнали об этапах планирования процессов, определениях, типах, последовательности действий, преимуществах и недостатках различных типов планирования процессов. Пожалуйста, поделитесь этой статьей со своими друзьями и поделитесь своим мнением в комментариях ниже.
Промышленные технологии
- Что такое методы тестирования:типы, преимущества и недостатки
- Что такое виртуальная машина - типы и преимущества
- Что такое дизайн встроенной системы:этапы процесса проектирования
- Что такое протяжка? - Процесс, работа и типы
- Что такое ковка? - определение, процесс и типы
- Что такое науглероживание? - Определение, типы и процесс
- Что такое литье металлов? - определение, типы и процесс
- Каковы основные этапы обработки?
- Какие существуют 4 типа производственного процесса?
- Какие этапы входят в процесс сборки печатной платы?