Новая технология стимулирует развитие роботизированной сварки
Не пора ли автоматизировать сварочные операции? Беспокоитесь о том, как долго вы сможете сохранить своих опытных сварщиков? Вам нужно увеличить пропускную способность, но вы не знаете, как это сделать с имеющейся рабочей силой? Вызов более прочным материалам? Разнообразие технических достижений позволяет относительно легко решить эти проблемы за счет автоматизации сварочных операций с удивительно быстрой окупаемостью.
В три раза быстрее
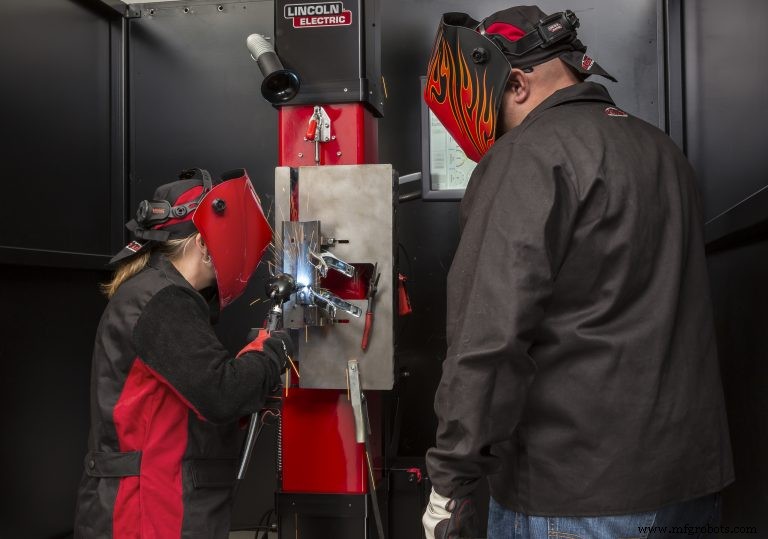
Существует две широкие категории автоматизированной сварки:так называемая «фиксированная» автоматизация и «гибкая» (или роботизированная) сварка. Фиксированная автоматизация часто зависит от приложения, и лучше всего, когда геометрия детали и сварной шов очень просты. Например, это вообще лучшее решение для сварки труб. Но для большинства промышленных применений и всего сложного роботизированная сварка идеально подходит, и именно ей посвящена эта статья.
Как объяснил Джейсон Ланге, менеджер по внутренним продажам Lincoln Electric Co. (Кливленд):«Основная цель робота — помочь с повторяемостью сварного шва. Во-вторых, уменьшить злоупотребление сварщиком. Движущиеся части в течение всего дня и ползание под разными приспособлениями утомительны для человека. Роботы улучшают эргономику».
Вдвойне важно облегчить работу сварщиков, потому что их становится все труднее найти. «По всей стране существует множество технических школ, инвестирующих в программы сварки, чтобы попытаться преодолеть этот разрыв», — продолжил Ланге. «Но в любой день количество людей, уходящих на пенсию, превышает количество поступающих на замену, создавая пустоту. Роботизированная сварка помогает заполнить этот пробел».
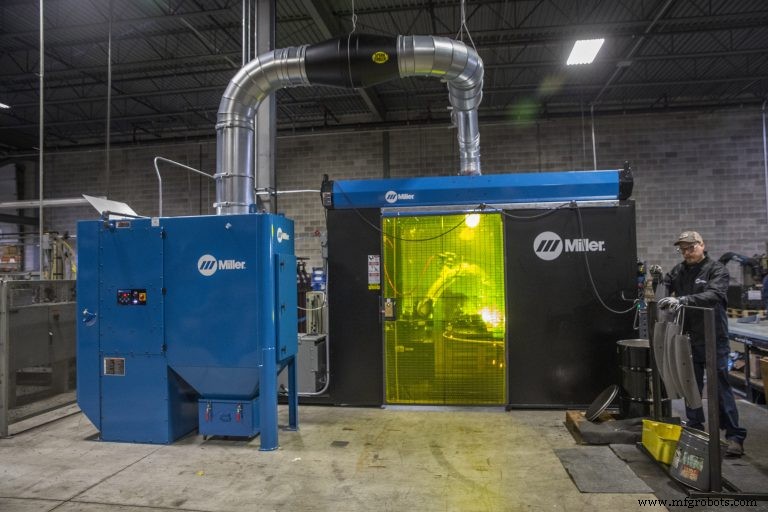
В то же время «окупаемость роботизированной системы, как правило, намного выше, чем вы думаете», — пояснил Эрик Миллер, менеджер по развитию бизнеса лазерной группы в Miller Electric Mfg. Co. (Appleton, WI). «Одна роботизированная система изготовит столько деталей, сколько три сварщика. Вы экономите две зарплаты за смену, а средняя стоимость готовых ячеек составляет от 100 000 до 120 000 долларов. Он окупается примерно за год. Как правило, если вы можете автоматизировать процесс и получить окупаемость менее чем за год, вы делаете это сразу же. Если это два года, вам следует серьезно подумать об этом».
Таким образом, роботизированная автоматизация является огромным подспорьем в увеличении пропускной способности. Но источники, опрошенные для этой статьи, подчеркнули, что это не замена квалифицированному труду. «Вам все еще нужен квалифицированный сварщик, чтобы управлять этим роботом», — сказал Ланге.
Изменение материалов — еще одна причина для автоматизации
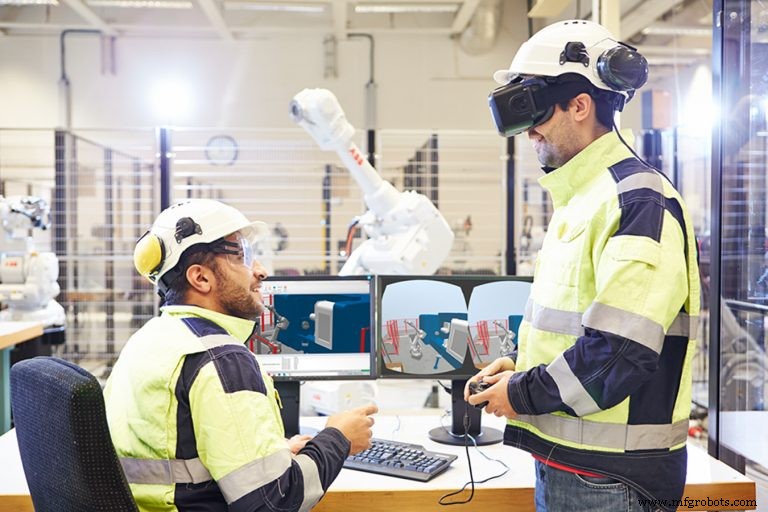
Изменения в рабочих материалах за последние десять лет привели к улучшениям в сварке, многие из которых невозможно применить вручную, например, лазерная сварка, по словам Эрвина ДиМаланты, директора направления сварки и резки, ABB Robotics (Оберн-Хиллз, Мичиган). . «Производители всего, от машин для добычи полезных ископаемых до автомобилей, используют разные материалы для снижения стоимости и веса, а также для размещения различных решений для силовых агрегатов», — сказал он. «Производители автомобилей перешли на более высокопрочные и сверхвысокопрочные стали, которые обладают металлургическими свойствами, делающими их более прочными, легкими и коррозионностойкими, но при этом обладающими высокой формуемостью и свариваемостью. Это коренным образом меняет то, как проектируются, формируются и собираются металлические конструкции». В то время как производители могли использовать традиционные штампы для вырезания деталей в деталях, теперь они используют процессы горячей штамповки и автоматизированные лазерные технологии для формовки и резки деталей.
«Другой пример — переход на алюминий для большего количества применений», — сказал ДиМаланта. «В зависимости от автомобиля до 90% кузова теперь может быть из алюминия. Из-за его более высокой проводимости вам нужно больше электрического тока для точечной сварки алюминия, а ток является синонимом тепла. Тем не менее, мы собираемся использовать более тонкие материалы. В некоторых автомобилях материалы имеют толщину около 1 мм. Итак, как вы справляетесь с этими тенденциями, которые развиваются в противоположных направлениях?»
Ответ заключается в улучшенной технологии как электронного, так и механического управления дуговой сваркой, а также более широком использовании лазерной сварки. Что касается дуговой сварки, ДиМаланта сказал, что «источники питания в настоящее время чрезвычайно продвинуты и управляются электронным способом. Нанесение материала в сварочную ванну тщательно контролируется с помощью индивидуальных форм волны». Миллер добавил, что такие специальные формы волны «контролируют подвод тепла к деталям, что может уменьшить деформацию, а также улучшить внешний вид сварных швов».
Он также указал на механический метод под названием Active Wire от Panasonic. «Это двунаправленная подача проволоки, при которой проволока подается вперед для создания короткого замыкания, а затем выводится из лужи в обратном направлении, повторяя это действие, похожее на швейную машину, с частотой 120 Гц. Это снижает тепловложение, а также значительно уменьшает разбрызгивание. Это также улучшает постоянство зажигания дуги на каждом сварном шве. Он очень популярен для сварки алюминия и тонколистового металла».
По словам ДиМаланта, чем легче компонент, тем более совершенными должны быть материалы, позволяющие создавать сложные конструкции при сохранении прочности. «Роботы и их передовые программные системы помогают связать процессы обработки этих материалов с траекторией движения робота».
Лазерная сварка — отличный вариант
Благодаря своей молниеносной способности сваривать широкий спектр материалов (в том числе разнородных), лазер, вероятно, является самым большим достижением в области сварки за последние десятилетия. И, по словам Масуда Харуни, старшего инженера по передовым технологиям лазерной сварки в компании Trumpf Inc. (Hoffman Estates, IL), «самая большая новость в области лазерной сварки за последние годы — это падение цен на лазеры».
«Системы лазерной сварки легче контролировать, — продолжает Харуни. «Вы выбираете одну мощность и одну скорость. После настройки вы обрабатываете всю деталь с небольшим разбрызгиванием. При дуговой сварке необходимо поддерживать дугу, а параметры сварки чувствительны к любым изменениям расстояния между горелкой и заготовкой. Различные части [заготовки] требуют большего или меньшего тока, и это снижает стабильность процесса. Несмотря на то, что контуры обратной связи в современных системах дуговой сварки очень хороши, эти системы никогда не настраиваются идеально. Компоненты, сваренные лазером, требуют гораздо меньше последующей обработки, чем компоненты дуговой сварки, которые часто приходится шлифовать. У вас также есть проблема с брызгами и необходимостью очистки сопла в системах дуговой сварки».
Возможно, что более важно, лазерная сварка позволяет получить более глубокий шов без теплового повреждения даже в таких материалах, как алюминий и магний, которые могут быть подвержены растрескиванию или пористости при дуговой сварке. Харуни объяснил это тем, что лазер может достигать плотности мощности 108 Вт на квадратный сантиметр. Это создает замочную скважину, глубокую полую область, созданную путем испарения металла заготовки. Когда лазерный луч движется вдоль детали, он поддерживает крошечную замочную скважину, окруженную расплавленной лужей, в то время как материал позади затвердевает.
«Вы получаете прочный глубокий сварной шов без чрезмерного нагрева детали», — сказал он. «Дуговая сварка не имеет удельной мощности, поэтому единственный способ добиться более глубокого сварного шва — увеличить погонную энергию. Механические свойства сварных деталей с меньшим тепловложением и меньшей деформацией намного лучше, чем у деталей с более высоким тепловложением».
Миллер заявил, что «первоначальное влияние лазерной сварки было на автомобильную сварку из-за большого объема и [технических преимуществ]. Производители листового металла также должны обратить внимание на лазерную сварку. Реальные преимущества заключаются в замене контактной точечной сварки, которая может быть сложной задачей для средних и малых объемов производства. Крепление может быть затруднено, так как требуется доступ как к верхней, так и к нижней стороне детали, тогда как для лазерной сварки требуется доступ только к верхней стороне, поэтому ее легче автоматизировать. Вы также можете использовать робота с меньшей полезной нагрузкой для лазерной сварки вместе с простой фиксированной оптикой».
По сравнению с роботом большой грузоподъемности с сильной рукой, несущей большой инструмент с двумя электродами, теперь производители могут использовать более безопасный робот весом 8 кг, установить на него технологическую головку и относительно легко автоматизировать контактную точечную сварку.
«Другая область листового металла, где лазерная сварка выгодна, — это производство коробок», — сказал он. «Сварные швы внешних углов, которые требуют косметического внешнего вида и практически не требуют последующей обработки металла, — это область, в которой мы наблюдаем большой интерес».
По словам Миллера, лазер является хорошим решением для деталей, доступ к которым ограничен. Для сварки лазеру требуется только прямая видимость, тогда как при дуговой сварке роботу приходится перемещать громоздкую горелку внутри и вокруг деталей, что может быть очень сложно. «При лазерной сварке мы часто находимся на расстоянии 500 мм от заготовки. Это как стрелять из лучевого пистолета. Лазер также имеет гораздо более высокие скорости обработки и меньшее общее тепловложение в деталь, что снижает искажения. Это идеальный инструмент для автогенной сварки».
Недостаток лазерной сварки, как объяснил Харуни, заключается в том, что вы «либо должны убедиться, что у вас практически нет зазора между компонентами, либо использовать линию сплавления, которая сочетает в себе лазерную сварку с проволокой, в которой вы расплавляете проволоку в ванну, чтобы вы может закрыть брешь. Но лазерная сварка настолько быстрее, что стоит дополнительных вложений в крепление. Например, если вы производите 50 деталей в день с помощью роботизированной дуговой сварки, роботизированная лазерная сварка может производить 300, 500 или даже тысячи таких же деталей в день».
Введение в автоматизацию сварки
Окунуться в автоматизацию сварки стало проще, чем когда-либо. Во-первых, основные игроки предлагают автономное программное обеспечение для настройки, которое программирует следующую работу на ПК с высокой степенью реализма, передает эту программу роботу и запускает сварку. АББ даже использует методы виртуальной реальности, чтобы пользователи могли «сотрудничать» с роботизированным сварочным оборудованием.
«Вы можете буквально взять робота за шею, так сказать, и управлять им так же, как собакой на поводке», — объяснил ДиМаланта. «Это может быть гораздо более интуитивно понятным, чем использование обучающего пульта».
Во-вторых, эти системы могут иметь механизмы, которые автоматически адаптируются к изменениям положения от одной детали к другой и отслеживают качество сварки.
Как объяснил Дэвид Шефер, специалист по продуктам в Miller Electric:«Существует несколько типов датчиков, которые реагируют на изменения в расположении суставов. Один из них просто сенсорный, а другой — отслеживание шва по дуге. При использовании сенсорного датчика робот может спуститься и использовать проволоку для дуговой сварки, чтобы исследовать деталь. Он проверяет разницу между запрограммированным местоположением и фактическим местоположением, чтобы фактически перепрограммировать себя.
«При отслеживании дугового шва, когда вы переплетаете соединение, например, при угловом сварном шве или сварке внахлестку, если это достаточно толстый материал, он обнаруживает изменение силы тока и определяет, когда он находится в соединении, а когда нет. соединение, а затем следует за этим сварным швом во время его сварки», — продолжил Шефер. «У вас также есть возможность использовать лазерную оптику вместо датчиков проводного типа, но основная идея та же».
Ланге из Lincoln Electric сказал, что «еще один способ сделать это — использовать камеру, которая делает двухмерное или трехмерное изображение детали. Мы можем компенсировать программы и компенсировать соединения в зависимости от физического расположения деталей. Новые камеры не так подвержены бликам от деталей, как это могло быть даже несколько лет назад. Они могут видеть больше цветов и читать определения деталей, отличая тени и отражения от деталей». Харуни добавил, что «современная оптика также дает нам возможность проверять качество сварного шва в режиме реального времени без необходимости разрушающего контроля».
В-третьих, все роботы предлагают ту или иную форму обнаружения столкновений. Миллер из Miller Electric сказал, что это представляет собой наиболее значительное улучшение самого манипулятора робота. «Ранее клиент создавал свою программу на основе известного положения X-Y-Z резака. Допустим, робот сварил половину смены, а оператор оставил зажим открытым. Скорее всего, робот врежется в зажим, погнув горелку. Это приведет к тому, что каждый сварной шов в этой программе будет не выровнен, потому что конец горелки был согнут, и это положение изменилось. Сегодня, если робот сталкивается с объектом даже на высокой скорости, он считывает возникающий в результате всплеск тока как препятствие. Это приводит к тому, что робот немедленно переходит в режим гибкого сервопривода, который откладывает наложение тормоза на определенное расстояние, указанное для каждой оси. По сути, робот «хромает». Это позволяет роботу рассеивать импульс, сводя к минимуму повреждение инструмента. Это означает, что вы можете совершить столкновение на высокой скорости, не погнув факел».
В-четвертых, все крупные игроки предлагают готовые роботизированные ячейки со всем необходимым на поддоне (или нескольких). «Рабочая ячейка будет полностью спроектированной единицей со всеми мерами безопасности», — сказал Ланге. «Обычно вы видите ограждение или стальные стены, как правило, сканеры безопасности, свет, кнопки, позволяющие роботу двигаться, ключевые блокировки и какое-то устройство позиционирования перед роботом, такое как поворотный стол или колесо обозрения. Эти устройства доставляют деталь в рабочую зону, в то время как оператор загружает дополнительные детали с противоположной стороны. Или у вас может быть просто фиксированный стол, за которым будет работать робот. Там также будет источник сварочного тока, горелка и несколько разверток для очистки бит, если это необходимо. Вам просто нужно подключить его к электричеству и источнику газа». А если какое-то из готовых решений не работает, доступны индивидуальные готовые решения.
О чем беспокоиться?
«Когда мы консультируемся с потенциальным клиентом по поводу автоматизации сварки, мы смотрим на его предшествующее производство», — пояснил Шефер из Miller Electric. «Если они используют лазеры и оборудование с ЧПУ для гибки, торможения и резки материала, они добьются гораздо большего успеха при роботизированной сварке, чем если бы они резали его вручную или использовали отрезную пилу. Теперь этим цехам это сойдет с рук, потому что, когда они сваривают детали вручную, сварщики могут соответствующим образом отрегулировать их, а робот — нет». Миллер добавил, что сварка обычно автоматизируется в последнюю очередь, поскольку в первую очередь должны быть точными предшествующие процессы. «Детали должны быть аккуратно вырезаны, а затем аккуратно согнуты. Тогда ты сможешь их сварить», — сказал он.
Помимо обеспечения повторяемости деталей, требуется крепление, которое ограничивает или устраняет зазоры, как объяснил Шефер:«Вы не можете сваривать воздух. Человек-оператор может увидеть зазор и отреагировать соответствующим образом, обычно увеличивая вылет проволоки, чтобы уменьшить силу тока, что снижает нагрев и проникновение, а затем начинает ткать, чтобы заполнить зазор. Робот этого не сделает. Он прогорит».
С другой стороны, Ланге сказал, что некоторые клиенты тратят тысячи или сотни тысяч долларов в некоторых случаях на оснастку для крепления деталей, когда они могут сократить эту цену вдвое, улучшив предшествующие процессы. Это обеспечивает требуемую повторяемость на последующих этапах, что в конечном итоге снижает стоимость оснастки и уменьшает количество переделок и брака. чтобы сварить себя и сварить через автоматизированное устройство», — сказал Ланге.
Итак, кого следует обучить автоматизированной сварке? Либо опытный сварщик, либо кто-то, кто хочет научиться сварке (что занимает несколько недель) плюс автоматизация сварки.
Шефер предупредил:«На предприятии нужна правильная культура. Люди, имеющие работу, могут чувствовать угрозу, связанную с автоматизацией на объекте. Я буду очень откровенен с моими людьми о преимуществах, о том, как это сделает компанию более эффективной, поможет ей расти и стать более конкурентоспособной и, в конечном итоге, наймет больше людей».
Наконец, размеры пакетов должны быть достаточно большими для автоматизации. Как выразился Ланге:«Время, необходимое для автономного программирования, установки робота и быстрой настройки, безусловно, дает хорошую отдачу, если размер вашей партии составляет примерно день или полтора дня. Если вы меняете деталь каждый час, рентабельность инвестиций может быть ниже».
Система управления автоматикой
- Новая беспроводная технология 2015 г.
- NPE2018 В фокусе новых технологий:революция «4.0»
- Новый центр медицинских технологий Hahn Automation
- Роботизированные системы автоматизации открывают новые возможности
- 4 способа улучшить характеристики роботизированной сварки
- Студенты создают роботизированную систему сортировки мусора с использованием технологии B&R
- Acieta запускает новую роботизированную загрузочную камеру
- Robotiq запускает новое роботизированное решение для сбора мусора
- AMRC внедряет инновации в технологии и экономику замкнутого цикла
- Роботизированный прорыв, сделанный Центром производственных технологий