Экскурсия по заводу:STELIA Aerospace, Меолт, Франция
Компания STELIA Aerospace (Тулуза, Франция), в которой работают 7000 сотрудников по всему миру и выручка в 2018 году составила 2,2 миллиарда евро, четко заявляет о своей основной продукции и позиции в отрасли:№ 1 в Европе / № 1 в Европе. 3 место в мире по авиационным конструкциям, 1 место в мире по креслам пилотов и экипажа и 3 место в мире по пассажирским местам первого и бизнес-класса.
Компания STELIA Aerospace использует композиты в передней части фюзеляжа Airbus A350, крыльях турбовинтовых самолетов ATR, различных конструкциях вертолетов и в некоторых изделиях для сидений, включая новейшее сиденье OPAL. Производственные мощности по производству композитов включают французские предприятия Méaulte (большие секции фюзеляжа) и Salaunes (более мелкие композитные детали), подробные детали и сборка в Марокко и Тунисе, а также широкий спектр композитных деталей для самолетов, обороны и космоса на предыдущем предприятии Composites Atlantic в Луненбурге, Новая Шотландия, Канада.
STELIA Aerospace была образована в результате слияния в 2015 году двух предыдущих дочерних компаний Airbus - Aerolia и Sogerma. Его площадка в Меолте - в 1,5 часах езды к северу от Парижа - охватывает 49 гектаров с производственными площадями в 150 000 квадратных метров, 1500 сотрудников и 500 субподрядчиков и является ключевым звеном в цепочке поставок Airbus. Его расположение в небольшом городке противоречит производственной силе, «поставившей в 2018 году 860 носовых секций фюзеляжа для самолетов A320, A330, A350, A380 и A400M», - говорит менеджер по связям с общественностью STELIA Méaulte Франсуа Фурнье. Он является моим проводником по производству носового фюзеляжа A350 на заводе «Фабрика будущего» и научно-исследовательскому центру STELIALAB в сопровождении Оливье Канала, руководителя отдела исследований и разработок, сборки и автоматизации STELIA Aerospace Méaulte, производства композитных материалов и цифровых технологий, и Саймона Мэр-Видже. , начальник отдела производства научно-технических композитов, СТАЛИАБ.
«Фабрика будущего»
Во время вводной презентации в здании штаб-квартиры предприятия Фурнье объясняет, что STELIA Aerospace инвестировала в технологии будущего, такие как цифровое производство и автоматизация, включая дополненную реальность / виртуальную реальность, используемые для повышения эффективности производства, и роботов / коботов для более эффективной сборки.
«Будущее за композитными материалами и металлические конструкции », - отмечает Canal. «Мы пытаемся определить будущие решения, которые не заменят наших сотрудников, а сделают их более эффективными».
Это стремление к эффективности, возможно, лучше всего иллюстрируется инициативой «Фабрика будущего», начатой пять лет назад с целью выхода на новый уровень производства A320 и A350. «Мы приняли новую промышленную стратегию для этого объекта», - вспоминает Канал, который был менеджером проекта по этой инициативе. «Мы хотели иметь возможность обеспечивать переменную производительность и разработали гибкие инструменты, которые можно было бы переназначать для разных программ».
Еще одним результатом этого переосмысления стало выделение зданий под определенные программы. «У каждого будет одна линия и одна команда, - говорит Канал, - и они будут спроектированы с использованием подхода бережливого производства, который направлен на устранение потерь рабочей силы, движения, материалов и процессов». STELIA Aerospace также модернизировала линейку A320 и повысила производительность на 10-20 процентов, «что на самом деле является значительным улучшением», - говорит Канал. «Мы достигли этого за 2,5 года, изменив более 50 процентов производственных площадей на этом сайте, сохранив при этом производство и 100% своевременная доставка без потери качества ». Этот успех объясняется поддержкой высшего руководства, «но мы также много работали, чтобы работники имели право собственности», - отмечает он.
Canal объясняет, что конструкция производственного здания A350 площадью 30 000 квадратных метров была продиктована потоком, примером которого является его U-образная форма, когда сырье поступает с одного конца, а готовые секции фюзеляжа выходят с другого. «Все, что нужно для производства наших конструкций А350, находится в этом здании, от начала сборки до окончательной сборки. Это важно, например, для быстрого и легкого выявления и устранения любых проблем с качеством », - говорит он.
Для A350 STELIA Aerospace производит носовую часть фюзеляжа 11, которая полностью выполнена из металла, чтобы лучше противостоять повреждениям от удара птиц, а также сложную гибридную сборку металл / композит для секции 12 и нижней части секции 11/12, которая включает в себя носовую часть. отсек шасси. Фурнье показывает видеоролик STELIA Aerospace «Фабрика будущего», указывая на импульсную линию, подобную той, которая используется при сборке автомобилей. «Мы установили демонстрационную линию, чтобы позволить рабочим обучать и демонстрировать эту движущуюся линию, которая работает в определенное время такта, чтобы обеспечить полную производительность», - говорит Канал.
Другой аспект - цифровые технологии. «Цифровые решения позволили нам разместить все технические схемы и шаги на планшете и обеспечить доступ к последним 3D-макетам для каждой секции», - говорит Канал. Таким образом, сотрудники получают информацию о важных деталях и изменениях, а менеджеры легко уведомляются о потенциальных проблемах. «Мы также разработали дополненную реальность для облегчения сборки, например, проекцию на корпуса фюзеляжа, показывающую, какие части и где должны быть выполнены крепления», - отмечает Канал. Он добавляет, что инспекционные коботы используются для завершения 3D-сканирования готовых секций, которые затем сравниваются с цифровым макетом, выявляя любые посторонние предметы или недостающие детали, проблемы с качеством и т. д.
Наш тур начался в чистом помещении производственного здания А350, где машины для автоматической укладки волокон (AFP) Coriolis (Квевен, Франция) укладывают большие корпуса фюзеляжа из армированного углеродным волокном полимера (CFRP) для нижней части секции 11/12 и короны. и две боковые оболочки для секции 12. Эти оболочки затем соединяются с предварительно изготовленными стрингерами, помещаются в вакуумные мешки и отверждаются в автоклаве. После отверждения они обрезаются и загружаются на инструменты, которые позволяют легко транспортировать их на всех этапах сборки, включая роботизированное сверление и установку крепежа. Каждая панель проверяется с помощью автоматизированного неразрушающего контроля (NDT). Готовые сборки доставляются на сборочную линию фюзеляжа Airbus в Сен-Назере, Франция.
СТАЛИАБ
Следующая остановка - научно-исследовательский центр STELIALAB площадью 2000 квадратных метров, который занимает левую половину IndustriLAB, регионального технологического и учебного центра, расположенного к югу от закрытого комплекса STELIA. Деятельность STELIALAB посвящена композитам, сборке и цифровым технологиям.
Здесь тур снова начинается в salle blanche . (чистая комната), довольно большая открытая комната с принадлежностями для упаковки и инструментами для укладки. Саймон Мэр-Вигер объясняет, что миссия группы состоит в том, чтобы определить будущее низкозатратного крупносерийного производства в основном крупных и сложных деталей. Индустриализация термореактивных композитов включает высокоскоростные процессы AFP и инфузии жидкой смолы (LRI), включая литье с переносом смолы (RTM), для больших закрытых коробчатых конструкций, таких как компоненты крыла, горизонтальные плоскости оперения и вертикальные плоскости оперения.
Выйдя из чистой комнаты, мы попадаем в комнату AFP, в которой находится машина Кориолиса, которая может укладывать детали длиной до 4 метров. Maire-Vigueur, посвященный научно-исследовательскому центру, отмечает, что он занят более 200 дней в году. STELIALAB разработал процесс интеграции сухих ребер жесткости, созданных AFP, и обшивок, отверждаемых в автоклаве (OOA) с помощью печи или самонагревающихся инструментов. «Мы предпочитаем LRI с более низким давлением впрыска, потому что можем использовать более дешевые инструменты», - говорит Мэр-Вигер.
Дорожная карта TPC
Эта машина AFP также использовалась для укладки обшивки для демонстратора фюзеляжа / хвостовой балки вертолета из термопластичного композита (TPC) в рамках программы разработки ARCHES TP. Показанный на Парижском авиасалоне в 2017 году, а также на выставке JEC World в 2018 и 2019 годах, он был изготовлен из 8 жгутов ленты из углеродного волокна / полиэфиркетонекетона (PEKK) шириной 0,25 дюйма с лазерным нагревом. «Мы интегрировали защиту от ударов молнии с AFP во время простоя», - отмечает Мэр-Вигер. «Кожа была обработана методом OOA с использованием пленки для упаковки в мешки Kapton, что на самом деле не очень удобно». Омега-образные стрингеры изготавливались из покупных однонаправленных ленточных плоских панелей, штампованных на фирме Aviacomp (Тулуза, Франция). Тот же процесс использовался для рам, но с использованием пластин, сделанных из тканого материала, поставляемого Porcher (Badinières, Франция) и проштампованного в Cetim (Нант, Франция). Хотя шпангоуты крепились механически стандартным способом, стрингеры крепились с помощью автоматизированной динамической индукционной сварки. «Это обеспечивает более низкую стоимость и новые возможности дизайна», - отмечает Мэр-Вигер. «Мы также продемонстрировали формовку точек крепления, например, для электрических жгутов».
Когда его спросили о проблемах программы, Maire-Vigueur ссылается на монтажные работы, сварку и 15-месячный график. «Даже штамповка без излишней деформации тканого материала была непростой», - добавляет он. Хотя конструкция хвостовой балки была завершена конструкторским бюро STELIA Aerospace в Тулузе, все производство контролировалось STELIALAB. Тем не менее, ARCHES TP был лишь одним шагом в дорожной карте STELIA Aerospace в области термопластичных композитов. Компания продолжает разрабатывать технологии TPC, чтобы продемонстрировать возможность создания полномасштабного фюзеляжа TPC в последующие годы.
Переосмысление авиастроек будущего
Выйдя из комнаты AFP, экскурсия продолжается через очень большой открытый зал, который разделен на безопасные «ячейки развития» временными стенами для защиты интеллектуальной собственности. Пройдя через холл и повернув налево, мы попадаем в зону с небольшим автоклавом Scholz (Coesfeld, Германия) с температурой 450 ° C и литьевой машиной для вливания смолы. «Поскольку наша дорожная карта направлена на лечение OOA, мы фактически используем автоклав как печь для отверждения термопластичных композитов без давления», - объясняет Мэр-Вигер. Есть занавешенная отделочная комната и зона рядом с ней с оборудованием неразрушающего контроля, включая небольшую систему C-сканирования.
Снова поворачиваем и попадаем в большую испытательную лабораторию. «Мы можем изучать шлифованные поперечные сечения для контроля качества и исследования материалов и процессов», - говорит Мэр-Вигер. В лаборатории также есть рука Romer (Hexagon Manufacturing Intelligence, Шропшир, Великобритания) для измерения координат и оборудование для измерения объемного соотношения волокон, твердости и химических испытаний. «Все инженеры в нашей команде R&T могут самостоятельно управлять материалами и процессами», - отмечает Мэр-Вигер. «Мы обучаем их навыкам работы от проектирования и производства до проверки и испытания готовых деталей. Это важно для понимания всего процесса и позволяет быстро оценить предполагаемые проблемы и их причины. Дизайн неотделим от производства и проверки качества ».
Конечная остановка - большая лаборатория автоматизации в одной из огороженных стеной территорий. Беглый взгляд на внутреннюю часть показывает работу по исследованию новой сборки с использованием роботов и коботов. «Мы смотрим на дальнейшее развитие более компактных, более функциональных инструментов и пытаемся представить, как можно было бы собирать детали быстрее и с меньшими затратами», - говорит Канал. «Наша культура - это культура, которая расширяет границы и открывает новые горизонты. Мы были лидером в области внедрения робототехники, а теперь мы являемся лидером в продвижении технологии композитов. Мы продемонстрировали нашу способность переосмысливать и переосмысливать будущее, и мы никогда не остановимся ».
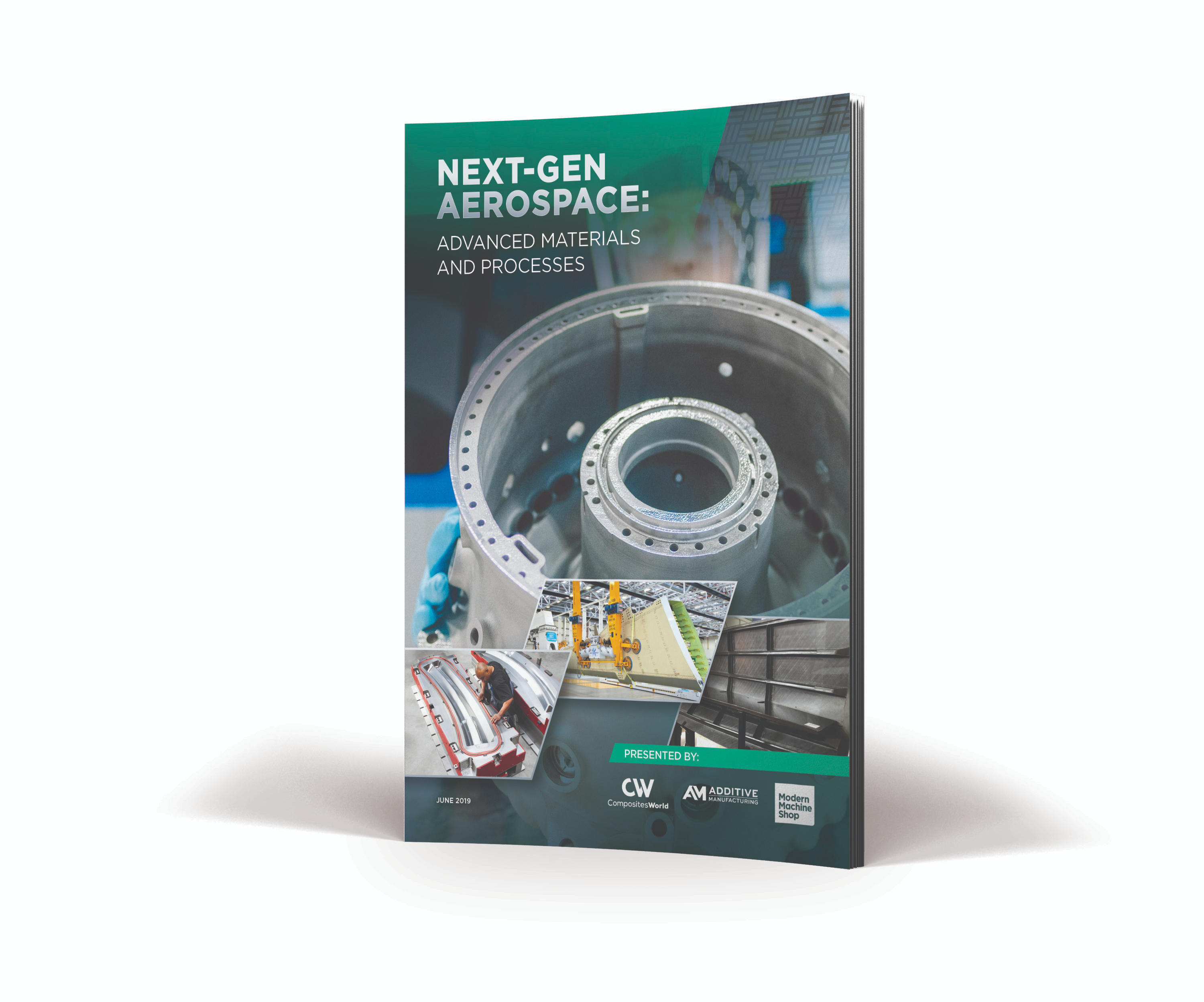
Новое поколение аэрокосмической промышленности
Поскольку в ближайшие 20 лет отрасль коммерческой авиации вырастет вдвое, удовлетворение спроса на пассажирские и грузовые самолеты потребует новых технологий и беспрецедентных темпов производства.
Узнайте больше о материалах и процессах, которые будут использоваться в самолетах следующего поколения, из коллекции историй от CompositesWorld, Modern Machine Shop и Аддитивное производство , доступно для чтения или скачивания бесплатно . Получите здесь.
Смола
- Vespel®:аэрокосмический материал
- Полипластики для расширения производства COC Topas
- Radici значительно увеличивает глобальные производственные мощности
- Polykemi инвестирует в собственный завод по производству компаундов в США
- Rethink Robotics получает новую штаб-квартиру и производственное предприятие
- Toyota выбирает участок в Северной Каролине для завода по производству аккумуляторных батарей для электромобил…
- Производители посещают Southco для ознакомления с заводом, обсуждения передовых методов непрерывного совершенс…
- Arkema Inc. строит завод по производству PEKK в США
- Hexion представляет двухкомпонентный эпоксидный раствор для производства аэрокосмических композитов
- Kaneka Aerospace получила сертификат AS9100D для аэрокосмической отрасли