Изготовление верхней половины многофункционального демонстратора фюзеляжа (MFFD)
Этот блог является продолжением презентации, проведенной Немецким аэрокосмическим центром . (DLR, Штутгарт и Аугсбург) на симпозиуме Технического университета в Мюнхене прошлой осенью и CW Резюме, опубликованное в тот же период времени, «Движение вперед на многофункциональном демонстраторе фюзеляжа (MFFD)». Этот проект также был описан в презентации, представленной Ларсом Ларсеном в 9:35 в третий день выставки ITHEC 2020:«Развитие роботизированной непрерывной ультразвуковой сварки на основе технологических данных для беспыльной сборки будущих конструкций фюзеляжа».
Как пояснил Ларсен, «главная задача - показать, что производственные затраты можно значительно снизить с помощью автоматизации». Для верхней половины MFFD это включает в себя консолидацию на месте с помощью автоматической укладки ленты / размещения волокон (ATL / AFP), чтобы избежать автоклавирования и беспыльной / беспыльной сварки при сборке. «Это должно позволить изменить последовательность линий сборки компонентов и окончательной сборки в будущем, - говорит Ларсен, - что позволит интегрировать системы до сборка." Это связано с тем, что в отличие от механической обработки отверстий под крепежные детали при сварке не образуются стружки или мусор, которые могут повредить предварительно установленные системы, такие как распределенная электроэнергия, внутренняя отделка и т. Д.
Этот блог основан на моем интервью с Себастьяном Новотны, руководителем отдела проектирования компонентов и технологий производства в Институте конструкций и дизайна DLR (BT, Штутгарт), и Фредериком Фишером, техническим руководителем по производству термопластичных композитов в Центре технологий производства легких материалов DLR ( ЗЛП, Аугсбург). Фишер также является менеджером проекта верхней части MFFD в DLR.
ПРИМЕЧАНИЕ. На изображении выше скользящие стрингеры относятся к процессу, разработанному в Clean Sky 2 компанией Applus + Labaoratories . (Барселона, Испания), см. Мой блог 2017 г. о формировании скольжения, а зажимы горячего прессования относятся к штамповке, см .:
- Ускорение термопластичных композитов в аэрокосмической отрасли.
- Термопластические композиты «отжимают» время, работая над небольшими, но важными деталями.
- Внутри очага из термопластичных композитов
Объединение конструкции, кабины и систем
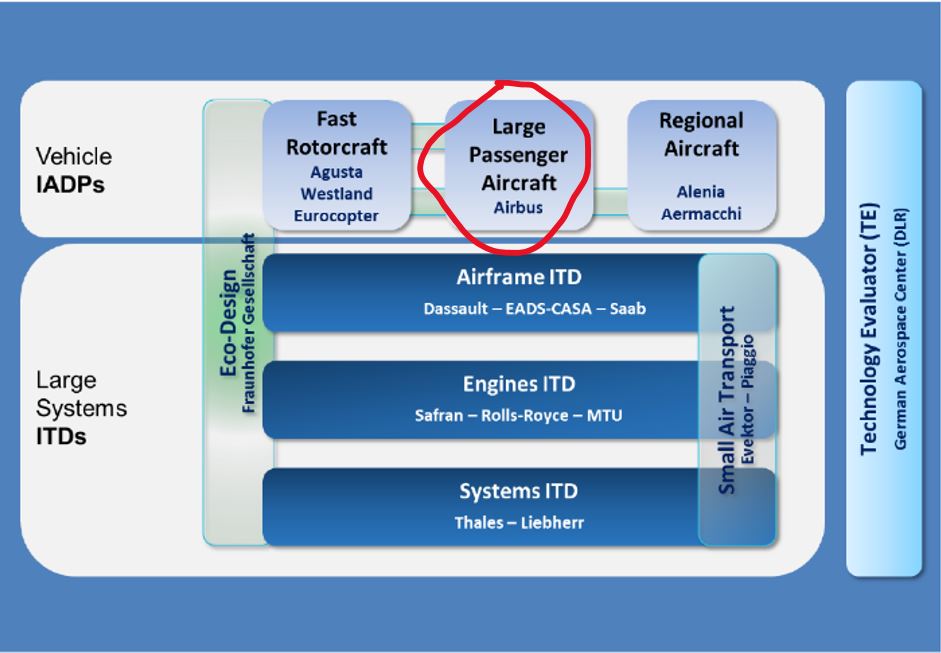
Я спросил Новотны об истории верхней половины MFFD. «Когда запустили Clean Sky 2, был объявлен первый конкурс заявок», - отвечает он. «Я думаю, что мы начали в 2015 году и выиграли тендер на проект под названием ICASUS, который был совместным партнерским проектом по программе больших пассажирских самолетов (LPA). Основное внимание уделялось дизайну многофункционального фюзеляжа. В то время это не был термопластический композит. Основная цель заключалась в объединении фюзеляжа, кабины, систем и конструкции в один процесс проектирования. Так что в основном проделанная работа - это то, что теперь стало демонстратором многофункционального фюзеляжа (MFFD), и является технологической поддержкой нашей работы над проектом верхней оболочки ».
ICASUS
Проект ICASUS направлен на разработку многофункциональных и высокоинтегрированных решений для многофункционального планера нового поколения, кабины и интегрированных систем фюзеляжа. Сегодня процесс производства и сборки узкофюзеляжных самолетов состоит из дорогостоящих и длительных последовательных этапов. Узкими местами, препятствующими более быстрым и ускоренным процессам, являются, в частности, сборка основных компонентов (MCA) и линия окончательной сборки (FAL). По этой причине ICASUS разработает новую концепцию производства и сборки будущих узкофюзеляжных самолетов наведения:
- Высокопроизводительное производство 60 самолетов в месяц;
- Снижение текущих затрат на фюзеляж на 1 миллион евро по сравнению с эталонным A321 ACF (Advanced Cabin Flex);
- Снижение веса фюзеляжа на 1 тонну по сравнению с A321 ACF.
Подход будет заключаться в объединении изначально автаркичных дисциплин кабины / груза, систем и конструкции, чтобы в итоге получить наиболее многообещающую комбинацию и интеграцию соответствующих функций и требований. Это должно быть достигнуто за счет использования передовых материалов и применения новаторских принципов проектирования в сочетании с самой передовой системной архитектурой в сочетании с кабиной следующего поколения.
Основной движущей силой является значительное сокращение расхода топлива за счет применения легких систем и системной архитектуры / интеграции. Это требует междисциплинарной общей процедуры оптимизации, а также разработки и применения целостного подхода Индустрии 4.0. Необходимо использовать дизайн для автоматизированного производства, автоматизации, сенсоризации, анализа данных и безопасного обмена данными. Основные цели производства MFFD включают проверку рентабельности и крупносерийного производства многофункциональных композитных конструкций и содействие концепциям сертификации термопластичных соединений углепластика (например, сварка).
Как объединить кабину, системы и конструкцию фюзеляжа в одно целое? «У вас все еще будут эти дисциплины с соответствующими требованиями, но я думаю, что главная цель - это подход к сотрудничеству уже на ранней стадии», - объясняет Новотны. «Существовали строгие правила для процесса проектирования фюзеляжа самолета, которые создавали ограничения и мешали полностью оптимизировать конструкцию самолета. Первоначальная идея объединить структуру, кабину и системы заключалась в том, чтобы иметь процесс проектирования, который объединяет эти три аспекта, а затем пытается найти глобальный оптимум, а не только сначала для кабины, затем для конструкции, а затем для систем. . Но, конечно, есть много правил, и это непростой процесс, потому что он также включает в себя сертификацию ».
«Это непрерывный процесс в том смысле, что была создана цифровая платформа, и все европейские партнеры вносят свой вклад в этот единый цифровой дизайн», - говорит Фишер. «Развитие этой интегрированной конструкции для MFFD - это то, что происходило последние пару лет. Наша команда доставит верхнюю половину с приспособлениями для крепления кабины и системы. Видение состоит в том, чтобы произвести революцию в окончательной сборке, предоставив полностью оборудованные основные компоненты ».
Хотя DLR уже был частью проектного проекта для MFFD, он не получил окончательного одобрения для производственного проекта до 2019 года. Консорциум для строительства верхней половины включает Airbus в качестве общего руководителя проекта MFFD, Premium Aerotec (Аугсбург, Германия ) в качестве руководителя промышленного и структурного проектирования и поставщика рам, Aernnova (Витория-Гастейс, Испания) для производства стрингеров и DLR в качестве ведущего разработчика технологии укладки обшивки и сварки. За последний год, по словам Фишера, «мы усовершенствовали конструкцию верхней половины, чтобы гарантировать, что она может быть изготовлена с использованием выбранных технологий».
Консолидация на месте
В то время как нижняя половина MFFD производится с использованием ATL и AFP с последующим уплотнением в автоклаве, верхняя половина будет использовать консолидацию на месте во время ATL / AFP. Почему? «Чтобы получить максимальный результат от исследовательского проекта, мы решили бросить вызов базовым показателям, - говорит Фишер, - и воспользоваться возможностью использовать технологию в дополнение к нижней половине». Новотны добавляет:«Мы показали, что это очень многообещающий производственный метод, ориентированный на бережливое производство, сокращающее количество этапов производства. Но я думаю, что очевидно, что не существует единого производственного метода, который бы служил всем целям. Вам все равно нужно решить, в каждом конкретном случае, каков оптимальный производственный процесс для каждой детали ».
Два типа сварки
Другой выбор, сделанный для верхней половины, заключался в использовании двух различных технологий сварки. «Мы используем роботизированную непрерывную ультразвуковую сварку стрингеров, потому что, по нашему мнению, это наиболее подходящая технология для действительно длинных стыков, особенно для конфигурации стрингеров», - объясняет Фишер. Для сборки шпангоутов фюзеляжа была выбрана контактная сварка. «Этот выбор - результат интенсивного анализа, который мы провели в начале проекта вместе с Premium Aerotec. Мы рассмотрели различные сценарии сварки, что нужно было соединить и где ».
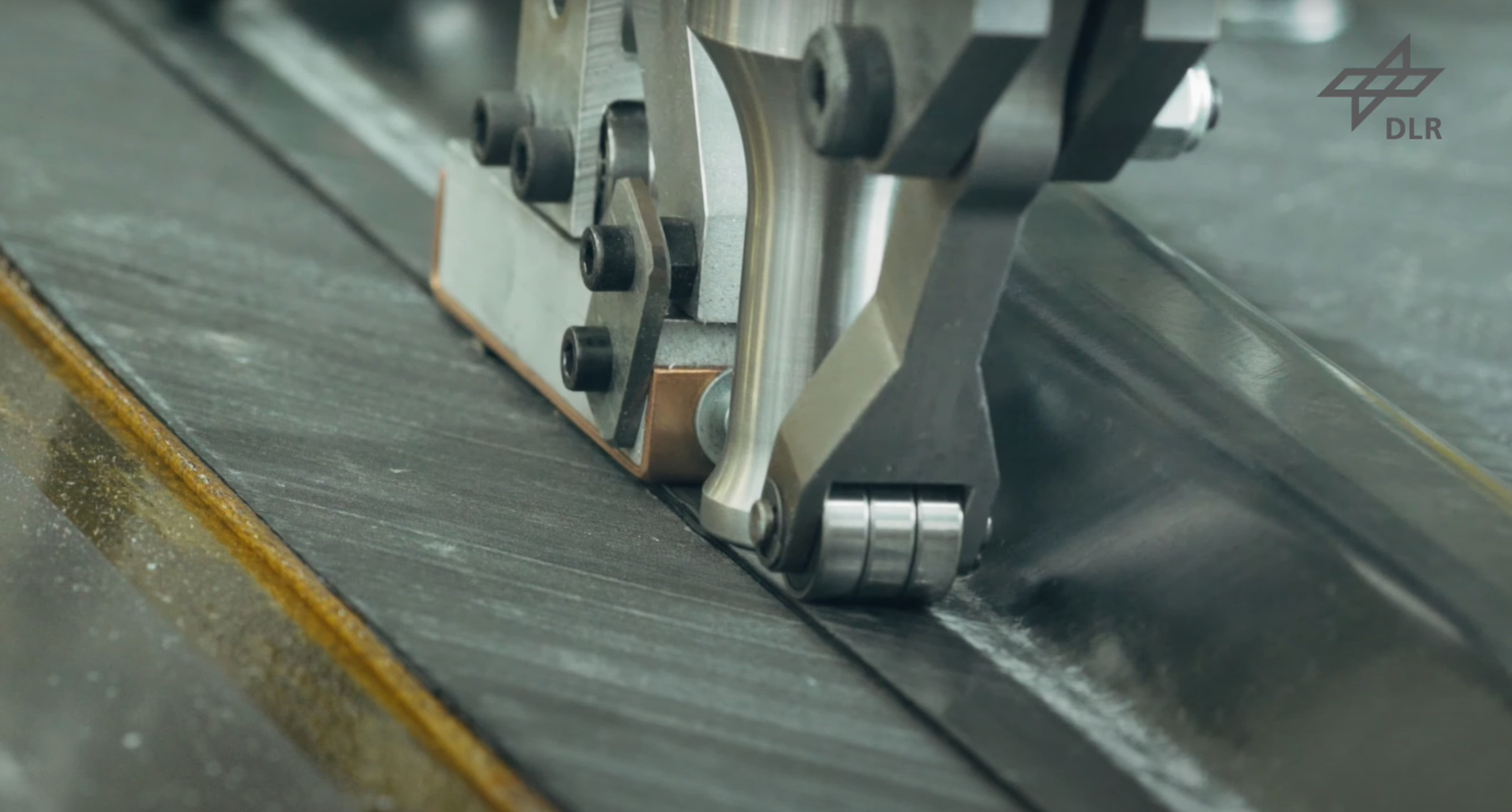
В непрерывной ультразвуковой сварке, разработанной DLR, используется стандартный промышленный робот. Сварочный концевой эффектор состоит из ролика предварительного прогона, сонотрода диаметром 25 мм и следующего за ним уплотняющего устройства. Концевой эффектор оснащен несколькими датчиками, что позволяет контролировать производственный процесс. Используя робот в качестве манипулятора, как показано на видео ниже, можно приваривать к обшивке различные геометрические формы, например изогнутую заднюю переборку давления или омега-стрингеры.
«Итак, у нас есть два процесса с одним большим отличием», - отмечает Фишер. «Один из них непрерывный процесс, а другой - прерывистый процесс. Для стыков Z-стрингеров длиной 8 метров мы выбрали непрерывную ультразвуковую сварку. А для очень сложного варианта использования - с точки зрения доступности и управления допусками - для приваривания прикрепленных фланцев рам к обшивке мы выбрали контактную сварку. Мы подгоним и предварительно оснастим элемент контактной сварки к геометрии рамы и получим сварочный инструмент в виде зажима, который пневматически закрывается, контактирует со сварочными элементами и затем запускает процесс сварки ».
Новотны отмечает, что контактная сварка имеет высшую степень зрелости и более высокую прочность, что хорошо согласуется с более высокой нагрузкой, наблюдаемой в соединениях между рамами и шипами. Он указывает, что в этом процессе рама приваривается к обшивке и приваривание шипа как к раме, так и к стрингеру.
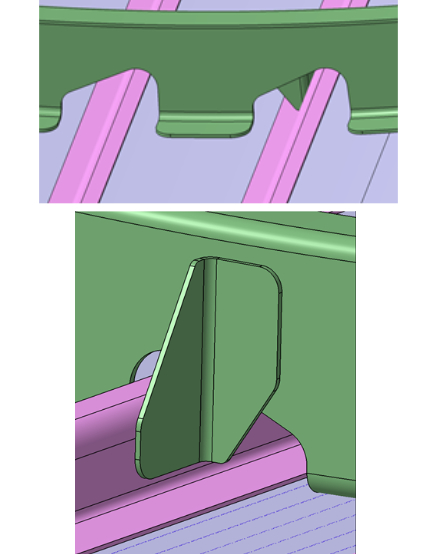
«Мы продемонстрировали интеграцию зажимов на типовых деталях на JEC 2017», - говорит Фишер. Новотны добавляет:«И в 2005–2008 годах у нас был проект HISYS с отделом высоких подъемников Airbus Bremen по контактной сварке с термопластом PEEK (полиэфирэфиркетон). Мы довели весь процесс приваривания ребер к обшивке до TRL 5. Итак, основы процесса достаточно хорошо изучены, и теперь мы можем сосредоточиться в основном на адаптации, автоматизации и надежности процесса ».
“ Фишер отмечает, что одним из ключевых факторов, позволяющих использовать различные сварочные технологии, даже несмотря на то, что они существуют уже давно, является их готовность к коммерческому применению в промышленности, включая необходимую автоматизацию, программирование и контроль качества. . Один из ключевых вопросов, который мы рассматриваем, - это как узнать, что сварной шов хороший. Мы хотим убедиться, что у нас есть данные о процессе, чтобы показать, что мы знаем, что сварной шов будет служить в течение длительного времени, и что мы не запрашиваем последующую проверку неразрушающим контролем с помощью ультразвука или другую общую проверку готовой сборки. Итак, одна из наших основных целей в этом проекте - обеспечение промышленного качества ».
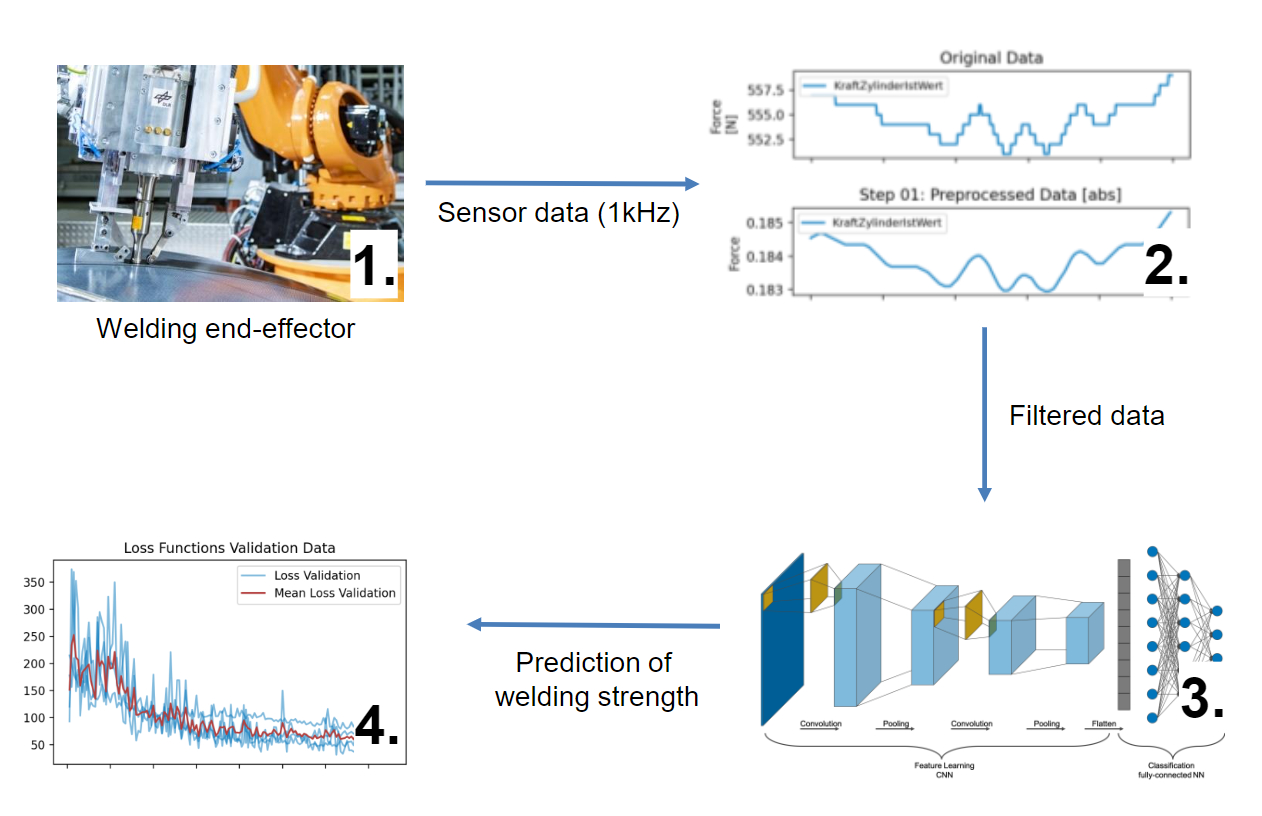
Переход на LM PAEK
Как объясняется в моем блоге «Доказательство сварки LM PAEK для многофункционального демонстратора фюзеляжа», хотя MFFD начинался с углеродного волокна / PEKK (полиэфиркетонекетона), к 10-му конкурсу заявок (CFP10) в марте 2019 года базовый материал был перешли на углепластик / ПАЭК (полиарилэфиркетон). PAEK - это общее семейство полимеров, в котором находятся PEEK, PEKK и LM PAEK. Какой опыт у верхней половины команды с LM PAEK? «Мы уже использовали его для ряда производственных испытаний», - говорит Фишер. «Характеристики материала весьма перспективны как для ультразвуковой, так и для контактной сварки. Тем не менее, материал находится в стадии разработки, и между всеми европейскими партнерами и поставщиком материалов был налажен процесс общего обмена извлеченными уроками и разработки руководящих принципов обработки ».
“ Однако, - добавляет Новотны, - я думаю, что это хорошо, что сейчас у нас есть такой выбор материалов, потому что много лет назад был только Cytec APC-2 и ничего больше. Особенно в Европе, иногда вы могли получить материал, а иногда вы получали «нет, извините». Теперь у нас есть несколько поставщиков материалов, которые активно работают с материалами, а также для различных процессов. Например, Victrex, как мы видели на симпозиуме TU в Мюнхене 2020 года, сейчас занимается оптимизацией для аддитивного производства. Также ведется некоторая работа по оптимизации для консолидации AFP на месте, а также некоторая работа по вторичной консолидации с использованием автоклава, а также различных производственных процессов вне автоклава (OOA). Так что сейчас происходит намного больше, и это увеличивает шансы получить хороший материал для каждого процесса ».
Хронология и следующие шаги
«Мы практически завершили процесс изготовления конструкции промежуточного демонстратора - А320 диаметром с двумя отсеками для рам и шириной 950 миллиметров - и построим эту меньшую половину корпуса в начале следующего года (2021 г.)», - говорит Фишер. . «Помимо этого, мы начали закупку оснастки для полноразмерной верхней половины корпуса, и мы наращиваем наши технологии, чтобы гарантировать, что мы сможем производить полноразмерную верхнюю половину вовремя в 2022 году. . »
Что это влечет за собой? Одна проблема - допуски сборки. «Продольные стыки по левой и правой сторонам верхней и нижней половин фюзеляжа разрабатывались в течение некоторого времени, - поясняет Фишер. «Исходя из этого, у нас есть определенные требования, и мы должны убедиться, что наши производственные допуски соответствуют этим требованиям».
«Основная история того, что мы пытаемся сделать с верхней оболочкой, - это продемонстрировать наиболее эффективные пути производства термопластичных композитов и проложить путь, который может составить конкуренцию алюминию для будущих самолетов», - говорит Фишер. Он отмечает, что DLR уже продемонстрировала это в своей работе с Premium Aerotec по разработке сварной задней перегородки из термопласта, показанной в 2018 и 2019 годах (см. Также «Новые горизонты в сварке термопластичных композитов»). Сварка и бережливое производство - ключевые факторы, способствующие развитию термопластов. И теперь мы должны вывести эти технологии из лабораторий в промышленность. И чтобы отрасли поверили, что они действительно могут использовать эти сварочные технологии, мы должны показать, что они могут быть автоматизированы, предсказуемы и управляемы для обеспечения надежности в реальных производственных задачах. И это то, что мы делаем ».
Смола
- Преимущества мелкосерийного производства
- Органические материалы - будущее производства пластмасс?
- Как выбрать лучшего поставщика пластмассовых изделий
- Сборочные роботы 101:что, где и как работают сборочные роботы на производстве
- Последние новости о переработке производства
- Роль блокчейна в производстве
- 8 потерь бережливого производства
- Что входит в производственный процесс?
- Будущее 3D-печати в производстве
- Является ли 3D-печать будущим производства?