Производство полидиметилсилоксановых наножидкостных чипов с помощью процесса наномоллирования на основе наконечников AFM
Аннотация
В современной области исследований наножидкостные устройства на основе полидиметилсилоксана (ПДМС) широко используются в медицине, химии и биологии. В настоящей статье была предложена новая технология наномоллинга (состоящая из АСМ-системы и пьезоэлектрического привода) для изготовления наноканалов (с регулируемыми размерами) на микросхемах PDMS, а размер наноканала контролировался управляющим напряжением и частотой, подаваемыми на пьезоэлектрический привод. . Более того, микроканальные и наноканальные формы были изготовлены соответственно с помощью УФ-литографии и наношлифования на основе наконечников АСМ, и, наконец, с помощью процесса переноса были получены ПДМС-пластины с микро / наноканалами. Также было исследовано влияние весового отношения ПДМС на размер наноканала. Процесс соединения микроканальных и наноканальных пластин проводился на самодельной системе юстировки, состоящей из оптического монокулярного микроскопа и прецизионных столиков. Кроме того, было проанализировано влияние размера наноканала на электрические характеристики раствора KCl (концентрация 1 мМ). Таким образом, можно сделать вывод, что наножидкостные устройства PDMS с множеством наноканалов глубиной менее 100 нм могут быть эффективно и экономично изготовлены с помощью предлагаемого метода.
Фон
Благодаря своему значительному потенциалу в химической, медицинской и биологической областях, микро / наножидкостные системы широко используются в анализе ДНК [1,2,3,4], разделении клеток [5], исследованиях белков [6,7,8], безопасность пищевых продуктов [9] и мониторинг окружающей среды [10]. С быстрым развитием технологии нанопроизводства потребность в наножидкостных устройствах с одномерным размером менее 100 нм постоянно растет [11]. Нанофлюидные чипы также могут быть эффективно использованы для обнаружения вирусов [12], манипуляции с наночастицами [13] и изучения диффузии ионов [14]. Однако эффективность обнаружения и чувствительность наножидкостных чипов зависит от размеров элементов и распределения наноканалов. Совершенно необходимо точно контролировать размеры наноканалов для обнаружения без меток на основе наножидкостей. Создание наноканалов с контролируемыми размерами и распределением элементов по-прежнему является проблемой для применения в области наножидкостей.
На сегодняшний день существует несколько методов, которые можно использовать для изготовления наножидкостных чипов. Реактивное ионное травление [15], обычная фотолитография [16], обработка высокоэнергетическим пучком [17], интерференционная литография [18], наноимпринтинг [19] и горячее тиснение [20, 21] наиболее часто используются для изготовления наножидкостные устройства; однако у всех этих методов есть свои ограничения. Реактивное ионное травление и обычная фотолитография - основные методы изготовления микро / наножидкостных каналов. Однако поперечные размеры изготовленных каналов зависят от длины волны падающего света, поэтому ширина созданных каналов часто находится в микрометровом масштабе, а не в наномасштабе [22]. Кроме того, неудобно менять фотошаблоны при изготовлении микро / наноструктур, имеющих разные особенности. Литография сфокусированным ионным пучком (FIB) и литография электронным пучком (EBL) представляют собой методы обработки пучка высокой энергии, с помощью которых можно легко изготовить высокоточный наножидкостный чип с наноканалами размером менее 100 нм. Однако вложения в производственное предприятие чрезвычайно высоки и необходимы строгие экологические требования [23]. Интерференционная литография (IL) подходит для изготовления простых периодических структур на большой площади; однако он не подходит для обработки одного наноканала [24, 25]. Разрешение обработки наноимпринтинга зависит от свойств шаблона, ключевым вопросом для этого подхода является то, как изготовить шаблон с высокоточными наноструктурами [26]. Кроме того, временное формование и метод на основе скрипа также используются для изготовления устройств микро / нанометров [27, 28]; однако при этих подходах очень сложно точно контролировать размер наноканала. Таким образом, для изготовления наножидкостного устройства требуется более осуществимый подход к производству с такими свойствами, как высокая точность обработки, простота использования, большой диапазон обработки и низкие требования к окружающей среде.
В последние годы из-за их высокой точности обработки сверхточные методы обработки, такие как наношлифовка, прецизионное шлифование и сверхточное точение, широко используются при изготовлении микро / наноструктур [29,30,31,32]. Более того, с момента изобретения атомно-силового микроскопа (АСМ) в 1986 году нанотехнология на основе иглы АСМ является мощным методом получения наноструктур [33]. Традиционное нанесение наночастиц на наконечник имеет некоторые ограничения, такие как ограниченная ширина обработки и низкая эффективность изготовления. Ширина наноканала, изготовленного с помощью этого подхода, зависит от геометрии наконечника АСМ, что означает, что наноканалы с контролируемой шириной недоступны. Кроме того, эффективность изготовления традиционного процесса наночастиц на основе наконечников относительно низка, особенно в случае использования подачи в процессе обработки для увеличения глубины и ширины полученной наноструктуры. Благодаря своим значительным преимуществам, таким как контролируемый размер обрабатываемой поверхности и высокая эффективность изготовления, нанопрофиляция на основе наконечников широко применяется для изготовления наноканалов. Gozen et al. [34, 35] изготовили наноструктуры на полиметилметакрилате (ПММА) с помощью процесса наномоллирования. Zhang et al. [36,37,38] подготовили трехмерные наноструктуры с помощью АСМ и изучили влияние различных параметров обработки. Park et al. [39] исследовали механизм процесса наномеханической обработки и обнаружили, что сила резания была значительно снижена; однако в предлагаемой системе оборудование для обработки оказалось относительно сложным, а процесс удаления материала не исследовался в деталях. Взаимосвязь между параметрами обработки, включая частоту возбуждения и напряжение, и габаритами полученного наноканала не изучалась. Кроме того, их работа не была сосредоточена на применении изготовленных наноканалов. Таким образом, необходимы дополнительные работы для изучения области применения этого подхода наномоллирования на основе наконечников AFM. Поликарбонат (ПК) из-за его превосходной обрабатываемости обычно используется для нанотехнологий [40]; тем не менее, его редко выбирают для изготовления наножидкостных чипов. Напротив, полидиметилсилоксан (ПДМС) широко используется для обработки микрожидкостных и наножидкостных чипов. Mata et al. [41] изучали влияние весового отношения PDMS на растягивающее напряжение. Park et al. [42] разработали новый метод повышения жесткости PDMS. Применение наножидкостных чипов в испытательной области без меток в основном зависит от электропроводности наноканалов [43], поэтому на результаты измерений часто влияют размерные размеры наноканалов [44].
Таким образом, чтобы преодолеть недостатки традиционного процесса царапания на наконечнике, в данном исследовании для проведения процесса изготовления наноканала используется подход наномилирования. Кроме того, лист ПК был выбран в качестве экспериментального образца для уменьшения износа наконечника, а также для снижения стоимости изготовления. Кроме того, размер наноканала на листе ПК контролировался управляющим напряжением и частотой, подаваемыми на пьезоэлектрический привод. Также было исследовано влияние весового отношения ПДМС на размер наноканала. Кроме того, чтобы проверить влияние различных размерных размеров на электрическую проводимость наноканалов, был проведен тест по измерению тока с использованием раствора KCl.
Методы
Настройка системы наномиллинга
Предлагаемая система наномиллинга на основе наконечника AFM состояла из коммерческого AFM (Dimension Icon, Bruker Company, Германия) и пьезоэлектрического привода (P-122.01, PI Company, Германия) (рис. 1a). Диапазон перемещения пьезоэлектрического актуатора как по оси x, так и по оси y был ограничен до 1 мкм. Кроме того, пьезоэлектрический привод приводился в действие синусоидальными сигналами с соответствующими напряжениями (генерируемыми коммерческим устройством-генератором сигналов (AFG1022; Tektronix, Inc., США)) при усилении усилителя сигнала (PZD350A; TREK, Inc., США). Лист ПК фиксировался на самодельном держателе (из эпоксидной смолы) фиксирующим винтом. Операция наномеханической обработки выполнялась с использованием иглы с прямоугольным пирамидальным покрытием, покрытой алмазом, толщиной 100 нм (DT-NCLR, Nanosensors, Швейцария). Кантилевер наконечника (нормальная жесткость пружины 68 Н / м) был изготовлен из кремния (рис. 1b), а силиконовый наконечник (радиус 10 нм) (TESPA, Bruker Company, Германия) использовался для измерения канавок после механическая обработка.
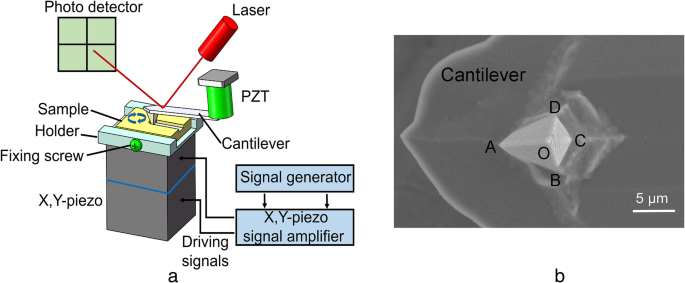
а Принципиальная схема системы наномиллинга. б СЭМ-микрофотография наконечника АСМ с алмазным покрытием
Изготовление форм для наноканалов и микроканалов
Маршрут изготовления наноканалов на микросхеме PDMS показан на рис. 2. Система AFM и пьезоэлектрический привод были использованы для изготовления форм для наноканалов (с контролируемыми размерами) на листе ПК. Лист ПК (молекулярная масса 35000) размером 15 мм × 12 мм × 1 мм был приобретен у Goodfellow. Среднее значение и стандартное отклонение шероховатости поверхности (Ra) листа ПК были измерены как 0,6 нм и 0,2 нм, соответственно (эти значения были получены путем сканирования области образца размером 50 мкм × 50 мкм в режиме постукивания АСМ). Для создания кругового движения пьезоэлектрический привод приводился в действие синусоидальными сигналами с разностью фаз 90 ° в направлениях x и y. Ширина обработанных наноканалов зависела от амплитуды создаваемого кругового движения. Диапазон управляющего напряжения, подаваемого на пьезоэлектрический привод, был установлен от 30 В до 150 В с шагом 30 В, и, кроме того, были выбраны две частоты погружения:100 Гц и 1500 Гц. Во время обработки в направлении кромкой вперед материалы выталкиваются в виде скоплений и часто оказываются равномерно распределенными по обеим сторонам наноканала [45], что помогает избежать утечки наножидкостных стружек во время процесса склеивания; поэтому в настоящем исследовании было выбрано направление обработки кромкой вперед. Наноканалы длиной 80 мкм были изготовлены с использованием модуля Nanoman системы АСМ. На любой процесс обработки влияет величина подачи; следовательно, чтобы исключить это влияние, скорость подачи должна изменяться в зависимости от частоты возбуждения. В настоящем исследовании значение подачи было установлено на 10 нм, а скорости подачи для частот 100 Гц и 1500 Гц были рассчитаны как 1 мкм / с и 15 мкм / с, соответственно. Нормальная нагрузка на иглу зависела от выходного напряжения, генерируемого позиционно-чувствительным фотодетектором (PSD); таким образом, различные нормальные нагрузки, использованные в нашем исследовании, были достигнуты путем установки относительного напряжения (уставки). Согласно нашей предыдущей работе [46], нормальная нагрузка обработки была рассчитана по формуле. (1), а чувствительность измерялась по наклону полученной кривой сила-расстояние [47].
$$ {F} _ {\ mathrm {N}} ={V} _ {\ mathrm {setpoint}} \ раз чувствительность \ times {K} _ {\ mathrm {N}} $$ (1)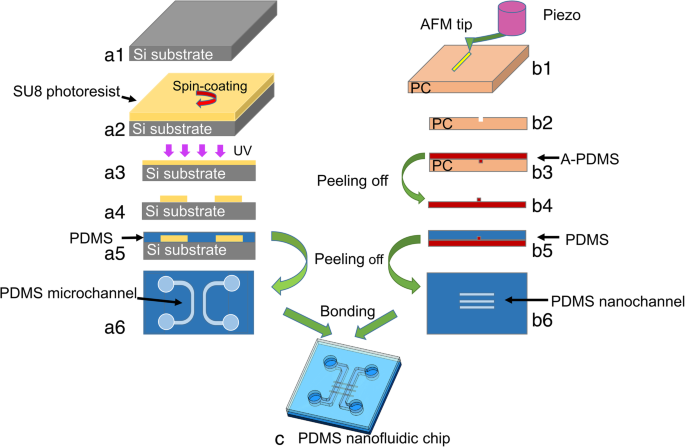
Блок-схема изготовления наножидкостного чипа:(a1) - (a6) Рабочие этапы изготовления микроканала на микросхеме PDMS; (а1) лист кремния, используемый для подложки для литографии; (а2) Спин-покрытие фоторезиста SU8 на подложке Si; (а3) воздействие УФ-излучения на слой SU8; (а4) Полученные выпуклые микроструктуры; (a5) покрытие PDMS на микроканальной форме; (a6) Окончательный чип PDMS с микроканалами; (b1) - (b2) Рабочие этапы изготовления наноканала на микросхеме PDMS; (b1) Царапины наконечника АСМ на листе ПК; (b2) Наноканальная форма, полученная после царапания; (b3) покрытие A-PDMS на наноканальной форме; (b4) чип A-PDMS с выпуклыми наноструктурами; (b5) Обычное покрытие PDMS на пресс-форме A-PDMS; (b6) Конечный чип PDMS с наноканалами; (c) Наножидкостный чип PDMS после соединения
Следовательно, нормальные нагрузки для процесса наномолола были установлены как 17 мкН и 25 мкН. Далее, для сравнения, наноканальные формы на листе ПК также изготавливались без вибрации, этот метод называется однократным царапанием. Нормальные нагрузки для процесса одиночного царапания были установлены как 25 мкН, 33 мкН, 42 мкН, 50 мкН и 58 мкН. Принципиальная диаграмма поперечного сечения пресс-формы для наноканалов представлена на рис. 2 (b2).
Формы для микроканалов были приготовлены методом УФ-литографии. Блок-схема на рис. 2 (a1 – a4) отображает детали операции процесса литографии. Фоторезист (SU-82015; MicroChem, США) наносили центрифугированием на Si-подложку при 500 об / с в течение 30 с и при 4000 об / с в течение 120 с. Пара микроканалов U-образной формы сформировала микроканальный чип (рис. 2 (a6)), который был соединен наноканалами с образованием окончательного наножидкостного чипа. Ширина микроканала 30 мкм, диаметр резервуара 1 мм. Кроме того, расстояние между двумя микроканалами U-образной формы составляло 50 мкм (дополнительный файл 1:рисунки S1 и S2).
Переносная печать микроканалов и наноканалов
Выпуклая микроканальная форма (рис. 2 (а4)) и вогнутая наноканальная форма (рис. 2 (b2)) были перенесены с помощью PDMS (Sylgard 184, Dow Corining, США) для приготовления окончательного наножидкостного чипа. На рис. 2 (b3) - (b6) представлен технологический процесс переноса наноканальной формы, который состоял из двух этапов:первого переноса и второго переноса. Чтобы исследовать влияние массового отношения мономера к отвердителю на размер наноканала, во время первого и второго процессов переноса использовали три различных массовых отношения PDMS (A-PDMS). Весовые коэффициенты PDMS для процесса печати с первым переносом были установлены как 9:1, 7:1 и 5:1, тогда как значения для второго переноса были установлены как 10:1, 9:1 и 8:1. На рис. 2 (а5) и (а6) показан процесс переноса микроканальной пресс-формы с использованием одноступенчатого подхода к переносу. Весовое соотношение PDMS 10:1 использовалось для переноса выпуклого микроканала. Во время всех процессов трансфертной печати двухкомпонентный эластомер PDMS сначала равномерно перемешивали, а затем выливали в контейнер для подготовки формы. Затем корпус выдерживали в вакуум-эксикаторе в течение 30 мин и дегазировали 2–3 раза для удаления всех захваченных пузырьков воздуха. Подготовленную форму выдерживали в нагревательной печи при 80 ° C в течение 4 часов, и, наконец, копия PDMS была осторожно отделена от формы.
Соединение микросхемы
Приготовленные наножидкостные чипы склеивали кислородно-плазменной обработкой (Zepto, Diener electronic, Германия) в течение 32 с при давлении в камере 1,5 мбар и мощности камеры 81 Вт (рис. 2 (в)). Поверхности микроканалов и наноканалов были очищены скотчем, а четыре резервуара на микросхемах микроканалов PDMS были пробиты перед склеиванием. Деионизированная вода использовалась для поддержания чистоты чипов после плазменной обработки, и чипы поддерживались выровненными вместе с помощью самодельной системы юстировки, состоящей из держателя, монокулярного микроскопа и одномерного прецизионного предметного столика (TSDT-401S; SIGMAKOKI, Япония. ) (Рис. 3а). Подробности самодельной системы центровки можно найти в ESI. Затем чипы были склеены при температуре 95 ° C в течение 20 минут, чтобы получить закрытый микро / наноканальный чип (рис. 3b).
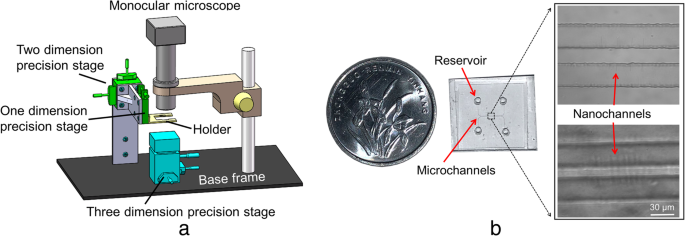
а Принципиальная схема самодельной системы центровки и б наножидкостный чип
Результаты и обсуждение
Траектория вращения пьезоэлектрического привода
Двумерный пьезоэлектрический привод является критическим компонентом для обеспечения вращательного движения в системе наномоллирования на основе наконечника AFM. Поэтому, чтобы охарактеризовать его движения в диапазоне управляющих напряжений и частот, были проведены предварительные испытания на царапание. В контактной модели с диапазоном сканирования 0 нм наконечник АСМ сначала приближался к поверхности листа ПК при данной нормальной нагрузке и оставался неподвижным. Вращение двумерного пьезоэлектрического привода контролировалось заданной частотой и напряжением. После завершения процесса царапания наконечник АСМ поднимался с поверхности листа ПК. Таким образом, амплитуда движения пьезоэлектрического привода была получена как функция напряжения и частоты возбуждения. Управляющие напряжения устанавливались в диапазоне 30–150 В с шагом 30 В, тогда как управляющие частоты были установлены на 100 Гц и 1500 Гц. Взаимосвязь между измеренными амплитудами и управляющими напряжениями на двух управляющих частотах отображается в дополнительном файле 1:Рисунок S3. Очевидно, что значения амплитуды обработки увеличивались с увеличением управляющих напряжений, а значение амплитуды обработки при 1500 Гц было больше, чем при 100 Гц. Было обнаружено, что ширина наноканала, изготовленного предлагаемым нами способом, составляет от 350 нм до 690 нм.
Изготовление наноканальных форм на листе ПК
Соотношения между размером наноканала и параметрами обработки при однократном царапании и наношлифовании представлены на рис. 4a и b соответственно. Ширина и глубина обработанных наноканалов представлены как W 0 и D 0 соответственно (рис. 5а).
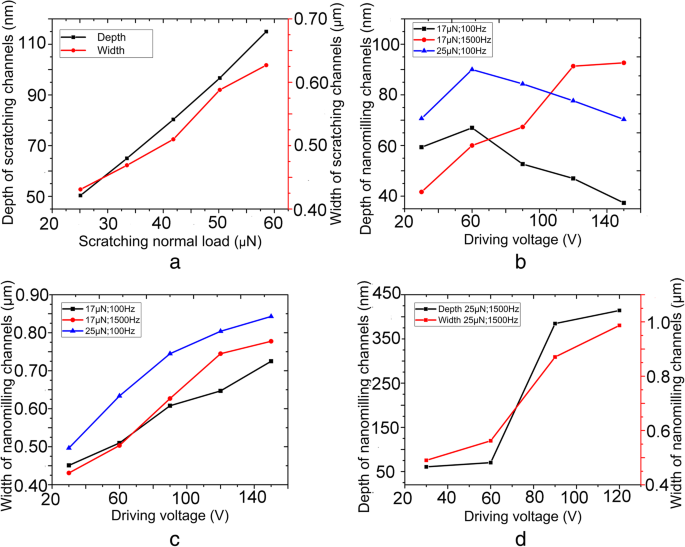
Взаимосвязь между размером обработанного наноканала и параметрами обработки: a однократное царапание при нормальных нагрузках от 25 мкН до 58 мкН, b глубина и c ширина обработанных каналов при изготовлении с нормальными нагрузками 17 мкН, 25 мкН и частотами возбуждения 100 Гц, 150 Гц, d глубина и ширина обработанных каналов при изготовлении с нормальной нагрузкой 25 мкН и частотой возбуждения 1500 Гц
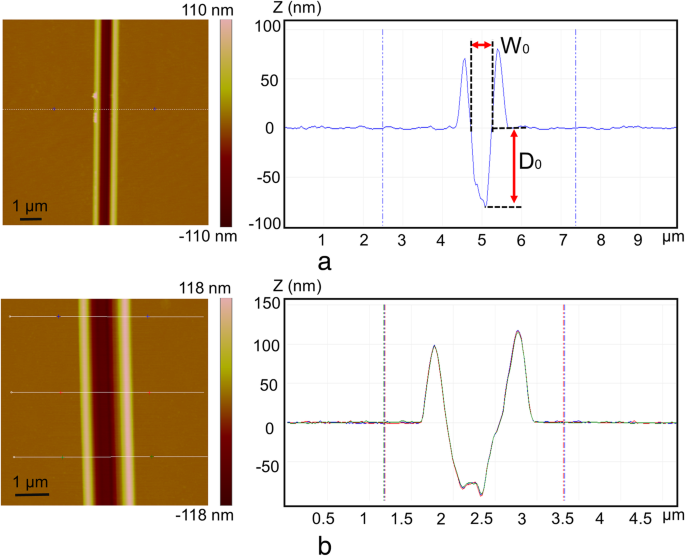
Типичные АСМ-изображения обработанного наноканала с различными параметрами обработки: a Царапины при нормальной нагрузке 42 мкН. б Наномолот при нормальной нагрузке 25 мкН, частоте 100 Гц и управляющем напряжении 60 В
Из рис. 4а видно, что ширина и глубина изготовленных наноканалов увеличивались с увеличением нормальных нагрузок. Типичное АСМ-изображение царапин при нормальной нагрузке 42 мкН показано на рис. 5а. Заметно, что материалы были вытеснены из наноканала, чтобы сформировать скопления, которые были равномерно распределены по обеим сторонам наноканала. Поскольку форма острия АСМ симметрична поверхности, которая была образована кромкой «OA» в процессе обработки (рис. 1b). Таким образом, материал равномерно выталкивался передним краем наконечника во время царапания кромкой вперед. Рисунки 4b, c и d иллюстрируют взаимосвязь между размером обработанного наноканала и управляющим напряжением. Из рис. 4б видно, что глубина наноканала увеличивалась вначале, а затем начала уменьшаться при частоте 100 Гц при нормальных нагрузках 17 мкН и 25 мкН. Лист ПК, используемый в нашем исследовании, представлял собой аморфный полимер, который демонстрирует упруго-вязкопластические свойства в сочетании с экспоненциальным деформационным упрочнением при высоких уровнях деформации [48, 49]. Нормальная нагрузка во время обработки была рассчитана по формуле. (2), где \ (\ overrightarrow {n} \) и \ (\ overrightarrow {t} \) - единичная нормаль и единичная касательная к вектору линии потока, соответственно, p и τ обозначает местное нормальное давление и напряжение сдвига, соответственно, а \ (\ overrightarrow {z} \) - единица измерения по вертикали [50].
$$ {F} _ {\ mathrm {N}} =p \ cdot \ int \ overrightarrow {n} \ cdot \ overrightarrow {z} ds- \ tau \ cdot \ int \ overrightarrow {t} \ cdot \ overrightarrow {zds } $$ (2)В настоящем исследовании размерные размеры изготовленных наноканалов были найдены в наномасштабе, поэтому значения местного нормального давления и напряжения сдвига были приняты постоянными. Далее, уравнение. (2) был преобразован в упрощенную форму уравнения. (3), где S n и S h соответственно - горизонтальная и вертикальная проекции границы раздела между зондом АСМ и образцом.
$$ {F} _ {\ mathrm {N}} =p \ cdot {S} _n- \ tau \ cdot {S} _h $$ (3)Отношения между S n и S h выражается в формуле. (4), где α и β соответственно - углы между поверхностью наконечника и вертикальной и горизонтальной плоскостями.
$$ {S} _ {\ mathrm {n}} =\ frac {S _ {\ mathrm {h}}} {\ cos \ alpha} \ cdot \ cos \ beta $$ (4)Нормальная нагрузка была рассчитана по формуле. (5).
$$ {F} _ {\ mathrm {N}} =\ left (p \ cdot \ frac {\ cos \ beta} {\ cos \ alpha} - \ tau \ right) \ cdot {S} _h $$ (5 )Это очевидно из уравнения. (1) что значения нормальной нагрузки были постоянными в течение всего процесса обработки. Согласно Briscoe et al. В [51] значение средней скорости деформации рассчитывалось по формуле. (6), где V и w обозначают скорость режущей кромки и толщину необрезанной стружки соответственно. Максимальное значение толщины неразрезанной стружки составило ~ 10 нм.
$$ {} _ {\ varepsilon} ^ {\ bullet} =\ frac {\ mathrm {d} \ varepsilon} {\ mathrm {d} t} \ приблизительно \ frac {V} {w} $$ (6)Кроме того, значения скорости наконечника были получены из уравнения. (7), где f частота входного сигнала.
$$ V =\ pi \ cdot {W} _o \ cdot f $$ (7)Значения средней скорости деформации при 100 Гц были найдены в диапазоне 1,42 × 10 4 . с -1 ~ 2,27 × 10 4 с -1 . Значения местного нормального давления ( p ) начал расти с увеличением скорости деформации, когда скорости деформации составляли 1,42 × 10 4 с -1 до 2,27 × 10 4 с -1 [52]. Значение τ был намного меньше, чем у p , это означает, что нормальная нагрузка в основном зависела от p . Следовательно, чтобы сохранить значения нормальной нагрузки (F N ) постоянна в течение всего процесса обработки, значения глубины обработки должны быть меньше при более высоких управляющих напряжениях. Однако на конечный размерный размер изготовленного наноканала повлияло восстановление материала образца. Восстановление образца уменьшалось с увеличением скорости обработки в диапазоне 142 ~ 227 мкм / с [53]:таким образом, это указывает на то, что более высокое упругое восстановление произошло при 30 В. Следовательно, глубина изготовленного наноканала при 30 В (~ 142 мкм / с) было меньше, чем у 60 В (~ 161 мкм / с). Дополнительный файл 1:Рисунок S4 (a) и рисунок 5b представляют собой типичные изображения АСМ наноканала, обработанного при 100 Гц при нормальных нагрузках 17 мкН и 25 мкН, соответственно. Очевидно, что скопление на правой стороне наноканала больше, чем на левой. Вращательное движение образца во время процесса наномоллирования происходит против часовой стрелки, и угол резания основной режущей кромки изменяется вместе с вращением. Толщина неразрезанной стружки слишком мала для образования стружки в начале и в конце цикла процесса нанопомола. Толщина неразрезанной стружки в середине цикла процесса нанопомола относительно велика; однако малый угол атаки способствует образованию скоплений. Таким образом, больше материалов перемещается в правую сторону канала, и скопления становятся асимметричными . Подробности формирования асимметричных скоплений можно найти в нашем предыдущем исследовании [54].
Из рис. 4b и d видно, что глубина наноканала начала увеличиваться с увеличением управляющих напряжений на частоте 1500 Гц при нормальных нагрузках 17 мкН и 25 мкН. На рисунке 4d показано, что глубина наноканала резко увеличилась с 60 В (~ 2,64 мм / с) до 90 В (~ 4,10 мм / с) при нормальной нагрузке 25 мкН. Согласно Geng et al. [55], на состояние съема материала в значительной степени влияет скорость резания. Материалы вытеснялись из наноканала в форме скопления во время обработки со скоростью 2,64 мм / с, тогда как состояние удаления материала было изменено с скопления на стружку при 4,10 мм / с (дополнительный файл 1:рисунок S4 (b)) . Следовательно, увеличение глубины обработки при 90 В (~ 4,10 мм / с) можно отнести к изменению состояния съема материала. Ширина изготовленного наноканала начала увеличиваться с увеличением управляющих напряжений. На рисунке 6 показана схематическая диаграмма траектории наконечника АСМ во время наномоллинга, пунктирные эллипсы, черные сплошные эллипсы и синие стрелки представляют собой законченный процесс обработки, текущий процесс обработки и направление движения наконечника AFM, соответственно. Ширина ( W 2 ) обработанного канала на рис. 6 (b) был больше, чем ( W 1 ) на рис.6 (а). AS 1 и AS 2 (красные сплошные линии) представляют длину контакта между поперечным сечением иглы АСМ и материалом образца. Значение AS 1 оказалось больше, чем у AS 2 когда ширина обработки « L 1 "Было равно" L 2 ”
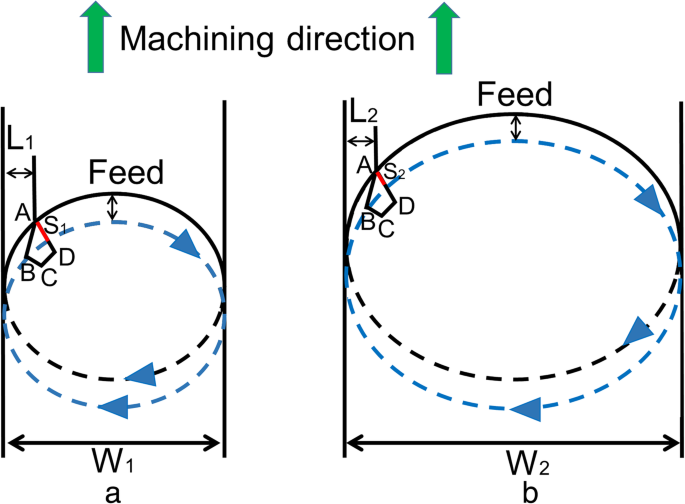
Схематическое изображение траектории иглы АСМ во время процесса наномоллинга:обработанная ширина наноканала ( a ) меньше, чем наноканал ( b ), а пунктирные эллипсы, черные сплошные эллипсы и синие стрелки представляют законченный процесс обработки, текущий процесс обработки и направление движения наконечника AFM соответственно
Значение S h в формуле. (5) было получено по формуле. (8), где D и AS соответственно - глубина обработанного канала и длина контакта между поперечным сечением иглы АСМ и материалом образца.
$$ {S} _h =\ frac {1} {2} \ cdot \ left | D \ left | \ cdot \ right | \; AS \ right | $$ (8)Следовательно, уравнение. (5) был в дальнейшем переписан в виде уравнения. (9).
$$ {F} _ {\ mathrm {N}} =\ frac {1} {2} \ cdot \ left (p \ cdot \ frac {\ cos \ beta} {\ cos \ alpha} - \ tau \ right) \ cdot \ left | D \ left | \ cdot \ right | AS \ right | $$ (9)Значения α и β оставались неизменными в течение всего процесса обработки. Значения скорости деформации при 1500 Гц были найдены в диапазоне 2,03 × 10 5 . ~ 3,66 × 10 5 с -1 ; следовательно, можно предположить, что местное нормальное давление ( p ) достиг своего предельного значения на частоте 1500 Гц. Кроме того, скорость обработки не оказывала влияния на восстановление образца при обработке при 30–150 В (~ 2,03–3,66 мм / с) [53]; таким образом, окончательные размерные размеры наноканала определялись только размерами механической обработки. Значения AS 2 (Рис. 6 (b)) оказались меньше, чем у AS 1 (Рис. 6 (a)) для большей ширины обработки, и в соответствии с формулой. Согласно (9) значение D было больше при меньшем AS. Следовательно, значения глубины обработки увеличивались с увеличением управляющих напряжений. Типичное изображение АСМ наноканала, изготовленного при нормальной нагрузке 25 мкН, управляющем напряжении 120 В и частоте 1500 Гц, представлено в Дополнительном файле 1:Рисунок S4 (b). Заметно, что материалы удалялись как при формировании чипа, так и при формировании скоплений, а вытесненные материалы накапливались только на одной стороне наноканала. Более того, выброшенные материалы накапливались в стружке внизу наноканала во время обработки при 150 В при нормальной нагрузке 25 мкН. Поэтому данные о размере изготовленного наноканала во время обработки при напряжении 150 В и частоте 1500 Гц (при нормальной нагрузке 25 мкН) были пустыми на рис. 4d.
Из рис. 4в видно, что ширина наноканала начала увеличиваться с увеличением управляющих напряжений. Более того, когда значения нормальной нагрузки и управляющего напряжения оставались постоянными, ширина наноканала, изготовленного на частоте 1500 Гц, была шире, чем ширина 100 Гц. Более того, глубина обработки наноканала, изготовленного на частоте 1500 Гц, была больше, чем у 100 Гц, и было обнаружено, что размер поперечного сечения наконечника больше во время обработки более глубокого наноканала. Таким образом, наноканалы были изготовлены шире при глубокой обработке.
Первая передача наноканальных форм
Наноканалы, обработанные методом одиночного царапания при нормальных нагрузках 25 мкН, 33 мкН, 41 мкН, 50 мкН и 58 мкН, были применены к первому процессу переноса. Кроме того, в процессе переноса также использовались наноканальные формы, изготовленные методом наномоллинга с частотой 100 Гц в диапазоне управляющих напряжений 30–150 В (с шагом 30 В). Наноканалы (глубина 80 нм и ширина 510 нм), обработанные методом однократного царапания, были названы «наноканалом I», тогда как наноканалы (глубина 50 нм и ширина 610 нм, глубина 90 нм и ширина 630 нм), изготовленные методом наношлифования, были названы «наноканалом». II »и« наноканал III »соответственно. В первом процессе переноса использовались три различных весовых соотношения PDMS (5:1, 7:1 и 9:1).
На рисунках 7a и b показано влияние различных весовых соотношений PDMS на размер стенки при нормальной нагрузке 25 мкН и частоте 100 Гц, а черная пунктирная линия представляет исходный размер наноканала до переноса. Типичное изображение АСМ и соответствующее поперечное сечение стенки, полученное из наноканала III при весовом соотношении 5:1 во время первого переноса, показаны на рис. 7c и d, и эта стенка была названа «стенкой III». Влияние различных весовых соотношений PDMS на размер стенки при однократном царапании с нормальной нагрузкой 17 мкН и частотой 100 Гц было показано в ESI (см. Дополнительный файл 1:Рисунки S5, S6, S7 и S8 ESI. для подробностей). The walls obtained from “nanochannel I” and “nanochannel II” were termed as “wall I” and “wall II,” respectively. It is evident that the heights of all walls at different PDMS weight ratios were approximately the same. The widths of the walls were larger than the original nanochannel width, and the width at the weight ratio of 5:1 was found to be the largest. Due to the thermal expansion of PC sheet, a small deviation was noticed between final wall size and original nanochannel size. It was also observed that the elasticity of PDMS increased as the PDMS weight ratio decreased from 5:1 to 7:1 [41, 42]. Hence, the wall obtained at the weight ratio of 5:1 was stiffer and its elastic recovery was smaller; thus, the width of the wall obtained at the weight ratio of 5:1 was the largest.
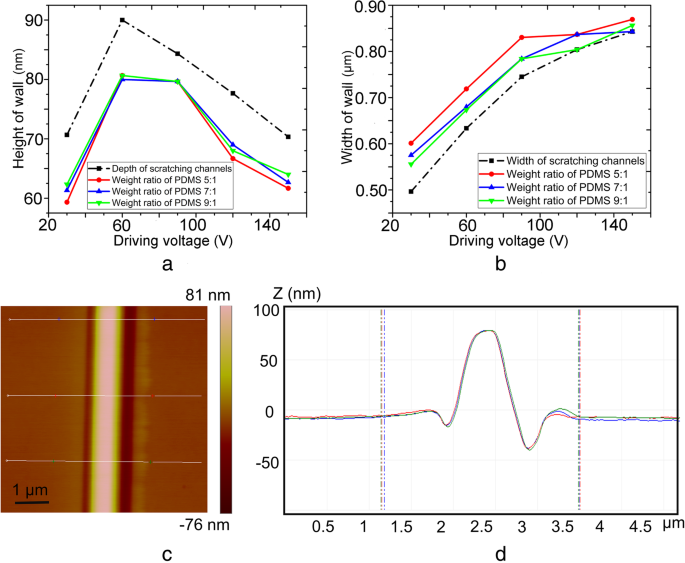
Relationship between a wall height, b wall width, and transfer parameters (various weight ratio of PDMS) during first transfer process, where the channel molds were fabricated with a normal load of 25 μN and a frequency of 100 Hz, and c typical AFM image and d corresponding cross-section of the wall obtained from nanochannel III at a weight ratio of 5:1
Second transfer of nanochannel molds
The final PDMS slabs with nanochannels were obtained during second transfer process based on the wall obtained at a weight ratio of 5:1 in the first transfer process. Three different PDMS weight ratios (10:1, 9:1, and 8:1) were used during second transfer process. Figure 8a and b present the relationship between nanochannel size obtained under a normal load of 25 μN and a frequency of 100 Hz and transfer parameters during second transfer. It is clear from Fig. 8a that the depths of the nanochannels were larger than the original machining size, moreover, the depth at 10:1 was found to be larger than other two ratios. Further, the widths of the wall were also larger than the original size, and the width at 10:1 was found to be the largest (Fig. 8b). Figure 8c and d present a typical AFM image and corresponding cross-section of the nanochannel (120 nm depth and 690 nm width) obtained from wall III at a weight ratio of 10:1 during second transfer, and it was termed as “nanochannel C.” The relationship between the nanochannel sizes obtained under single scratching process with a normal load of 25 μN and a frequency of 100 Hz and the transfer parameters during the second transfer process were shown in ESI (see Additional file 1:Figures. S9, S10, S11 and S12 of ESI for details), the nanochannels obtained from “wall I” and “wall II” were termed as “nanochannel A” and “nanochannel B”, respectively.
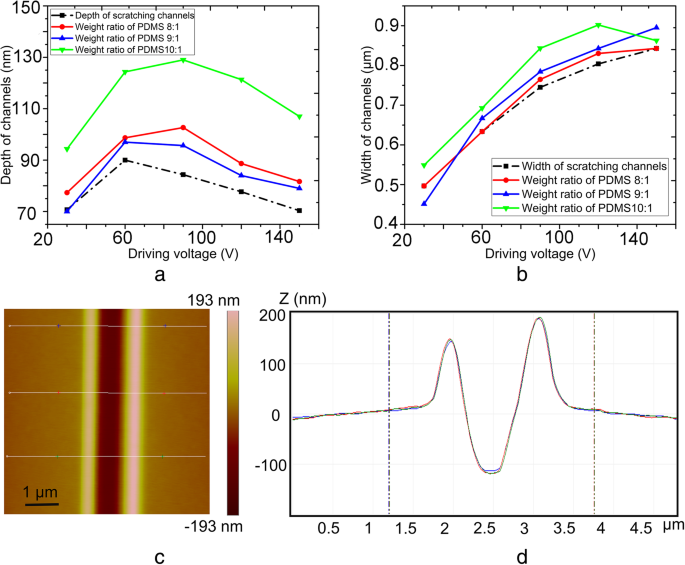
Relationship between a nanochannel height, b nanochannel width, and transfer parameters (various weight ratio of PDMS) during second transfer, where the channel molds were fabricated with a normal load of 25 μN and a frequency of 100 Hz, and c typical AFM image and d corresponding cross-section of the nanochannel obtained from wall III at a weight ratio of 10:1 during second transfer
The depths of nanochannels obtained from walls II and III were larger than the original machining size, whereas the depth obtained from wall I was smaller than the initial machining size. Furthermore, the changes in width were identical to the changes in depth. The aspect ratio of wall I was larger than those of walls II and III, thus each wall manifested different thermal expansion values. Hence, the changing trends of width and depth during second transfer were different though at the same PDMS weight ratio. The values of the depth and width of walls II and III at 9:1 and 8:1 were found to be closer to the original machining size compared with 10:1. Because the elastic recoveries of PDMS at 9:1and 8:1 are closer to 5:1 than 10:1, which indicates an almost similar recovery trend for PDMS at 9:1, 8:1, and 5:1.
Application of nanochannel devices in electric current measurement
Nanochannel devices are often used in the fields of single nanoparticle manipulation, electrokinetic transport phenomena, DNA analysis, and enzymatic reaction detection. The main working principle of nanofluidic chips depends on the variation in electric current; therefore, it is important to measure the electrical conductivities of nanochannel devices. The electrical conductance in a nanochannel can be estimated by Eq. (10) [56].
$$ G={10}^3N\;{}_Ae\frac{wh}{l}\sum {\mu}_i{c}_i+2{\mu}_e\frac{w}{l}{\delta}_n $$ (10)где μ я is the mobility of ion i , c я is the concentration of ion i , δ n is the effective surface charge inside the nanochannel, and NA and e signify Avogadro constant and electron charge, besides, w , h и l are the nanochannel width, height and length, respectively. It is obvious that the electrical conductance of a nanochannel is affected by the nanochannel feature dimensions and the solution concentration. The electric double layer (EDL) plays an important role in the nanochannel when the ratio of DEL thickness to the nanochannel height increases. The diffuse layer thickness of EDL is 3~5 times of the Debye length (λ Д ), which can be expressed by Eq. (11) [57].
$$ {\lambda}_D=\sqrt{\frac{\varepsilon_0{\varepsilon}_r{k}_bT}{2{n}_{i\infty }{(ze)}^2}} $$ (11)где n я ∞ denotes ion density in the solution, ε о is the permittivity of vacuum, ε r is the dielectric constant of electrolyte solution, z is the valency of buffer solution (z = z + − z - = 1 for KCl), and kb и T are the Boltzmann constant and temperature, respectively. In the present study, three different nanofluidic chips were obtained after the completion of transfer process. Nanofluidic chips consisted of nanochannels A, B, and C were termed as nanofluidic chips A, B, and C, respectively. Each nanofluidic chip contained four nanochannels. The widths and the depths of nanofluidic chips A, B, and C were measured as 60 nm and 500 nm, 80 nm and 680 nm, and 120 nm and 690 nm, respectively. The effective length of nanochannels in all chips was calculated as 50 μm. As shown in Fig. 8, pile-ups distribute on the sides of the nanochannels A, B, and C. The pile-ups may fill into the nanochannels and lead to a failure of the preparation for the nanofluidic chips. Thus, in order to verify the reliability of the fabricated nanochannel devices, electrical conductivity measurement test was conducted. KCl with 1 mM concentration was as the electrolyte solution in our study, and the values of electrical current were measured by an electrometer (Model 6430, Keithley, USA). The schematic sketches of the measurements for electric current in microchannel and nanochannel are presented as the inset figures in Fig. 9a and b, respectively. The experiments were carried out under DC power (applied by an Ag electrode) with an increment of 2 V for 3-s duration. Figure 9a presents the measured I - V curves of microchannels in three different nanofluidic chips, and a linear relationship between current and voltage was observed. Moreover, as the effect of EDL in microchannels was negligible and the dimensional sizes of microchannels in different nanofluidic devices were identical, the values of current in different chips were nearly the same. It is evident from Fig. 9b that the values of current in different nanofluidic devices were distinct due to different nanochannel sizes. For KCl solution of 1 mM concentration, the value of λ Д was about 10 nm, thus the diffuse layer thickness of EDL was found as 30~50 nm [57]. Consequently, EDL got overlapped along the depth (60 nm) of nanofluidic chip A; however, no overlapping was observed in nanofluidic chip C (depth of 120 nm). However, it was difficult to determine whether EDL got overlapped or not in nanofluidic chip B (depth of 80 nm). It assumes that the effective surface charges (δ n ) in all nanochannels are identical as the charge density of a surface is material property [58, 59]. The concentration of the ions in a nanochannel depends on the EDL field, the stronger the EDL field, the higher the ion concentration in the nanochanel [44]. In the present study, the EDL field in nanofluidic chip A is the strongest as the highest ratio of the DEL thickness to the nanochannel height, which signifies that the ion concentration in the nanochannel of nanofluidic chip A is the highest. Согласно формуле. (10), the nanochannel of nanofluidic chip A is more conductive due to the higher ion concentration. Hence, the value of electrical current in nanofluidic chip A was the largest, whereas nanofluidic chip C yielded the smallest value. In addition, at larger width sizes, EDLs did not overlap along the width directions of nanochannels. In nanofluidic chip B, when the value of applied electric field was lower than 25 V, a linear relationship was noticed between current and applied voltage; however, a limiting region appeared as the value of applied voltage increased and finally, became liner again as the electrical field increased further, this phenomenon belongs to ohmic-limiting-overlimiting current characteristic [60, 61]. The results of electrical current measurement revealed that the nanofluidic devices fabricated by the proposed method were effective, the pile-ups of the nanochannels A, B, and C had almost no influence on the performance of the nanofluidic devices.
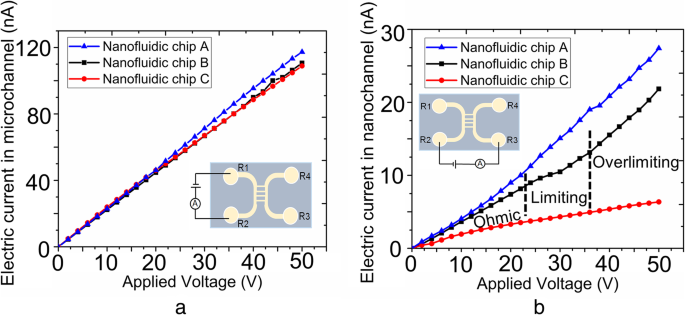
Electric current measurement results based on the fabricated nanochannel devices, the cross-section size (depth × width) of nanochannels for nanofluidic chip A, B, and C are 60 × 500 nm, 80 × 680 nm and 120 × 690 nm, respectively. а Current in microchannels. б Current in nanochannels. The insets display the schematic sketches of the measurements
Выводы
In the present research, nanochannels with controllable sizes (sub-100-nm depth) were fabricated by AFM tip-based nanomilling, and for the first time, the machined nanochannels were applied to prepare nanofluidic devices. The multichannel nanofluidic devices were prepared in four steps:(1) fabrication of nanochannels by AFM tip and piezoelectric actuator, (2) fabrication of microchannels by lithography, (3) transfer of micro- and nanochannels, and (iv) bonding. Further, nanochannel sizes were controlled by changing the driving voltages and frequencies inputted to the actuator. The heights of the wall obtained during first transfer were smaller than the original machining size, whereas the widths were larger than the original machining size. The experiment results revealed that during second transfer process, nanochannel sizes affected PDMS weight ratios. Finally, micro-nanofluidic chips with three different nanochannel sizes were obtained by bonding a PDMS nanochannel chip on a PDMS microchannel chip. Moreover, the electrical current measurement experiment was conducted on the fabricated nanofluidic chips, and it was found that the values of current were affected by nanochannel sizes. Therefore, PDMS nanofluidic devices with multiple nanochannels of sub-100-nm depth can be efficiently and economically fabricated by the proposed method.
Compared with other fabrication approach, the proposed method for fabrication of the nanofluidic devices in the study is easy to use and low cost; besides, the nanochannels with controllable dimension size can be obtained easily. However, the commercial AFM system cannot equip with a large-scale high-precision stage due to the spatial limitation; thus, the maximum fabrication length of the nanochannel is confined as 80 μm. In addition, the tip wear cannot be neglected after long-term fabrication due to the high machining speed, which should be investigated in future work.
Сокращения
- AFM:
-
Атомно-силовой микроскоп
- DC:
-
Постоянный ток
- EDL:
-
Electric double layer
- KCL:
-
Potassium chloride
- ПК:
-
Polycarbonate
- PDMS:
-
Полидиметилсилоксан
- PSD:
-
Position-sensitive photodetector
Наноматериалы
- Высечка:ускоренный курс по процессу изготовления
- Блог:понимание процесса изготовления PDMS
- Самые популярные методы изготовления композитов
- Различные способы финишной обработки добавляют функциональную ценность проектам по изготовлению металлов
- Использование 3D-принтера для улучшения производственного процесса — видео
- Ваш путеводитель по процессу резки металла
- Изготовление технологической трубы требует творческого планирования маршрута
- Изготовление технологических трубопроводов требует соблюдения точных спецификаций
- Сколько времени занимает процесс изготовления?
- Преимущества пескоструйной обработки для вашего индивидуального проекта по изготовлению металлоконструкци…