Бытовая электроника:гибридные композитные покрытия
SABIC продемонстрировал в недавнем исследовании, что крышка толщиной 1 миллиметр может соответствовать всем соответствующим отраслевым спецификациям производительности для очень тонких ноутбуков или планшетов. Источник, все изображения | САБИК
Потребительская электроника - это динамичный рынок с довольно коротким временем цикла между поколениями продуктов. От своих смартфонов, умных часов, планшетов и портативных компьютеров потребители хотят более высокую скорость работы, более длительные батареи, большую надежность и больше функций при более низкой цене и весе. Чтобы удовлетворить потребительский спрос, производители оригинального оборудования запрашивают у поставщиков материалы с высокой эстетикой и свободой дизайна, отличной ударопрочностью и высокой жесткостью - что означает качество на этом рынке - при небольшом весе и тонкостенном сечении. Им также нужны рентабельные методы обработки с высокой повторяемостью, которые удовлетворяют мировые производственные потребности в десятках миллионов единиц в год. Это давление сначала подтолкнуло рынок к использованию легких металлов для изготовления крышек / ящиков и рам, а теперь подталкивает его к решениям из металла / композита и полностью композитных материалов.
Технико-экономическое обоснование, проведенное компанией SABIC (Берген-оп-Зум, Нидерланды), включало использование двух типов термопластичных композитов для изготовления крышки ноутбука / планшета толщиной 1 миллиметр. Исследование показало, что конструкция из гибридного термопластичного композита может стать жизнеспособным решением для непростого рынка бытовой электроники.
Тестовый пример
С 2012 года SABIC сделала ряд инвестиций в разработку собственных армированных однонаправленным (UD) волокном термопластичных композитных лент (см. «Эволюция в армированные непрерывными волокнами»), что расширило сферу компетенции компании в области инжекции коротких и длинных волокон. волокнистые термопластические материалы (LFT) и позволили SABIC расширить ассортимент термопластичных композитов с более высокими эксплуатационными характеристиками. В 2015 году компания приобрела контрольный пакет акций производителя ленты Fiber Reinforced Thermoplastics BV (FRT, Lelystad, Нидерланды), а в 2017 году она стала партнером и стала миноритарным инвестором Airborne (Гаага, Нидерланды), производителя оборудования и разработчика композитных материалов. линий.
Поскольку SABIC и Airborne разработали и создали технологию для быстрого и рентабельного производства высококачественных термопластичных ламинатов на основе ленты в форме сетки для действительно крупных рынков (см. «Высокоскоростное высокопроизводительное производство термопластичных композитов»), команда начал искать тестовый пример. Этот демонстратор станет важным маркетинговым инструментом для подтверждения концепций дизайна термопластичных композитных ламинатов, изготовленных из композитных лент, наложенных поверх композитов, армированных прерывистыми волокнами. Также было бы важно протестировать инструменты прогнозного проектирования, разработанные командой для обеих технологий материалов, и продемонстрировать высокоскоростной производственный процесс, развивающийся в Нидерландах.
«Мы решили специализироваться на приложениях для бытовой электроники», - объясняет Джино Франсато, мировой лидер SABIC в области композитных материалов. «Этот рынок очень интересен, потому что существует реальная цель перейти на легкие материалы, чтобы сделать наши мобильные телефоны и ноутбуки легче и тоньше. И поскольку они зарабатывают миллионы и миллионы, мы решили принять вызов, который предлагал этот рынок ».
«Мы решили начать с чего-то достаточно сложного, но не слишком комплекс », - объясняет Скотт Дэвис, штатный научный сотрудник SABIC, специализирующийся на глобальных прикладных технологиях. Верхняя крышка очень тонкого ноутбука или даже планшета, которую команда надеялась в конечном итоге превратить в компоненты смартфона, казалась хорошим местом для начала. «Мы работали с простой общей геометрией, прямоугольником, который все еще должен был сохранять высокий эстетический вид и предлагать много сложностей на стороне B, включая функции крепления», - продолжает Дэвис. «Мы должны были сделать крышку очень тонкой, но при этом соответствовать сложным требованиям к отклонению, которые широко распространены в отрасли. И, конечно же, нам нужно было создать очень стабильный продукт с помощью нового сложного производственного процесса ».
Поскольку они не работали с реальным дизайном клиента, а только создавали защитную крышку для экрана, они использовали общую геометрию. На самом деле, отмечает Дэвис, когда они начали вырезать инструменты для инъекций для внутренней разработки, они даже не были уверены, будут ли они делать обложку для планшета или ноутбука, поэтому обложка была разработана для того, чтобы работать и с тем, и с другим. «Было много проблем, чтобы подготовить композитное решение для крупносерийного производства», - добавляет Дэвис. «На самом деле, одновременно много чего происходило - разработка ленты, разработка ламината и разработка процессов - и мы не могли дождаться, пока все эти вещи будут завершены, чтобы начать наш инструментарий, и именно так мы закончили этот дизайн». Завершив базовый дизайн, команда сосредоточилась на других деталях, таких как лучший способ установки ворот, какие виды перекрытий необходимы между ламинатной вставкой и формовочной массой, как обеспечить автоматическое размещение внутри инструмента, как справиться с коэффициентом ( линейное) тепловое расширение (CLTE или CTE), несоответствие между двумя композитами и способы создания легко воспроизводимой детали.
Выполнение сложных требований
Цель заключалась в разработке верхнего кожуха толщиной 1 миллиметр, обеспечивающего высокую жесткость и отвечающего всем эксплуатационным и эстетическим требованиям, особенно испытанию на прогиб центральной точки регулярно прикладывать к крышкам ноутбуков, чтобы оценить нагрузки, необходимые для повреждения основного экрана. Требования к нагрузке / прогибу различаются в зависимости от производителя оборудования, устройства и модели, но обычно допускается прогиб не более 3-5 миллиметров при давлении 40-120 Ньютон - ситуация, которая имитирует нагрузки, оказываемые пальцем или локтем, прижатым к крышке, как пользователь-человек встает. Во многих отраслях промышленности стратегия прохождения таких испытаний заключается в увеличении толщины секции, но этот рынок ценит более тонкие конструкции, которые освобождают место для более крупных батарей и других компонентов без увеличения размера или веса устройства. Следовательно, команде потребовалось использовать другую стратегию проектирования, чтобы предотвратить повреждение экрана, а именно выбрать более жесткие материалы (через ламинатную вставку) и использовать геометрию (например, ребристость путем литья под давлением). Но сначала нужно было указать материалы.
Один из этих материалов, поликарбонат (ПК), уже широко используется в этой отрасли для изготовления крышек и других компонентов из-за его превосходного внешнего вида и высокой ударной вязкости. Самыми большими слабыми сторонами полимера являются химическая стойкость и царапины на поверхности, но покрытие, краска или их сочетание, нанесенное на большинство покрытий, обычно преодолевает эти потенциальные проблемы.
«Поскольку сверхлегкие компьютеры настолько тонкие, пространство внутри корпуса очень дорогое, поэтому деформации и механические характеристики становятся действительно критическими», - отмечает Франсато. «Хотя вы хотели бы использовать стекло [армирование] с точки зрения затрат, нам пришлось использовать углеродное [волокно], чтобы получить необходимую нам жесткость». В результате все оцениваемые слоистые материалы на ленточной основе представляли собой разновидности поликарбоната, армированного углеродным волокном, - эти сорта тогда находились в разработке совместно с FRT, дочерней компанией SABIC.
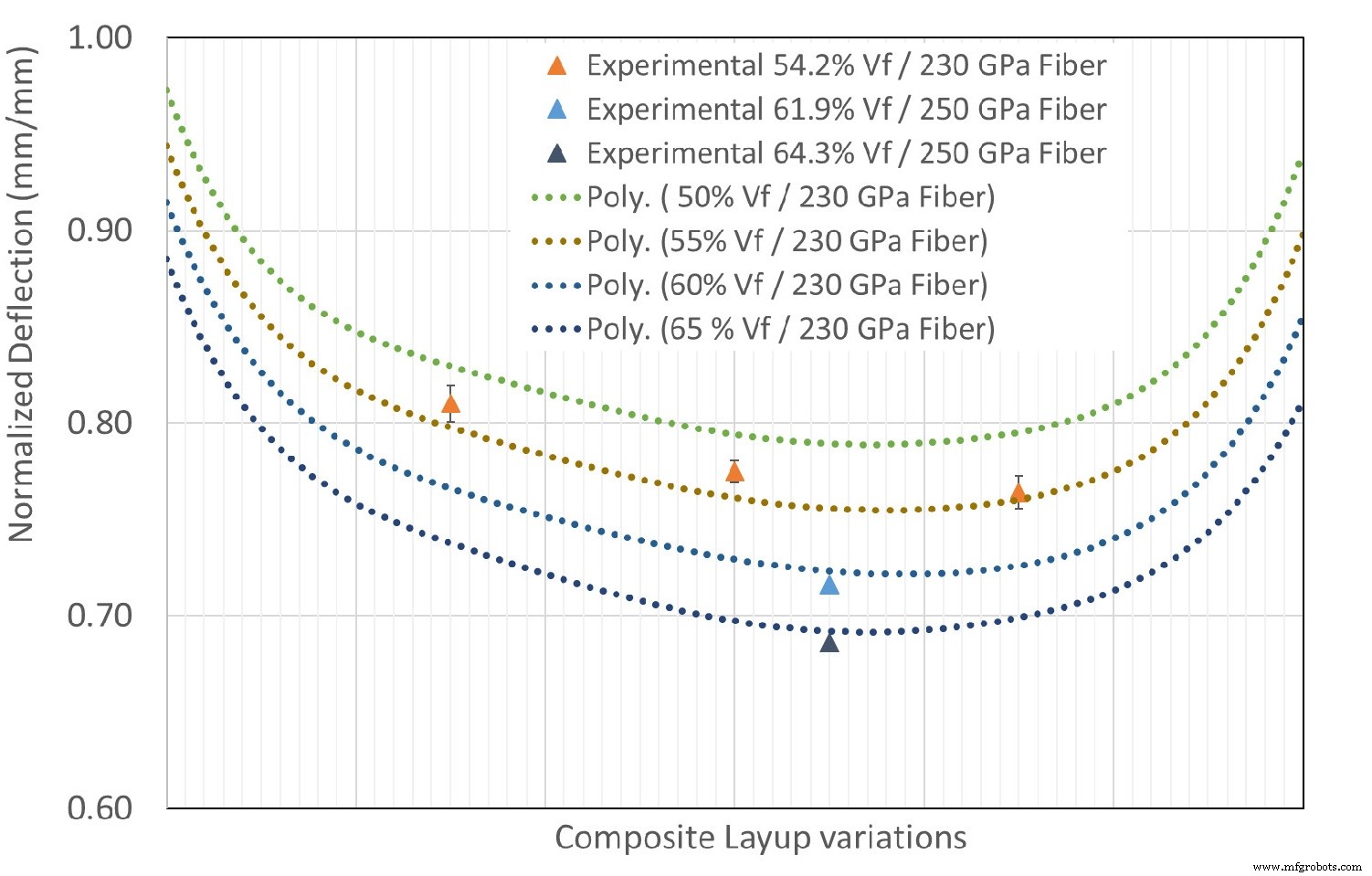
SABIC разработала прогнозные модели для моделирования типа и архитектуры ламината (с литьем для формования и без него) в сравнении с характеристиками формованных деталей и сообщает о достижении сильной корреляции между прогнозами и экспериментальными результатами. Утверждается, что инструменты прогнозного проектирования ускоряют разработку материалов.
Компаунд для формования требует другого подхода. Первоначально стратегия заключалась в использовании LFT-компаунда с более длинными волокнами, но по ряду причин - включая высокие эстетические требования, размер детали и стратегию вентиляции - компаунды с короткими волокнами лучше соответствовали требованиям проекта. Другой проблемой был тип используемого волокна. «Компаунды для инъекций с коротким углеродом действительно сложны в эксплуатации и при этом обладают высокой эстетикой, - продолжает Франсато, - поэтому для нашего материала для литья под давлением мы остановились на сортах, армированных коротким стекловолокном». LNP Engineering Plastics, Inc., дочерняя компания SABIC (Экстон, Пенсильвания, США), предлагает множество марок стекловолокна / ПК с хорошей эстетикой и жесткостью, которые популярны среди OEM-производителей устройств, поэтому команда сосредоточилась на них.
Хотя полностью аморфный ПК менее склонен к короблению, чем полукристаллические полимеры, исследователей все же беспокоят различия в CLTE между сильно армированными и анизотропными лентами из углеродного волокна UD и более изотропными, прерывистыми сортами из короткого стекловолокна для повторного формования при более низких нагрузках волокна. «В таких тонких стенах очень мало места для ошибки, поэтому мы должны были тщательно учитывать небольшие различия в CLT», - объясняет Дэвис. «И это даже не касается всех обычных проблем, с которыми вы сталкиваетесь при литье под давлением, таких как расположение ворот, рисунки заливки, давление упаковки и вязальные линии. Все эти факторы были смоделированы и проверены с помощью физических испытаний ».
После выбора материалов инженеры SABIC провели несколько итераций по заполнению пресс-формы, структурному анализу и моделированию коробления, чтобы оценить укладку ламината, геометрию и комбинации материалов для оптимизации жесткости для испытания на нагрузку / прогиб, а также другие требования к производительности и стоимости. Компания заявляет, что разработала комплексные и точные инструменты моделирования композитов (доступные для клиентов и работающие с общими конструктивными кодами и кодами обработки), которые могут быстро моделировать и моделировать архитектуру ламината, состав компаунда для формования с перекрытием, а также различные варианты обработки и инструментов по сравнению с производительностью отлитых деталей. Утверждается, что эти инструменты обеспечивают тесную корреляцию между прогнозами и измеренными характеристиками и идеально подходят для ускорения разработки нестандартных материалов.
Готовы к прайм-тайму
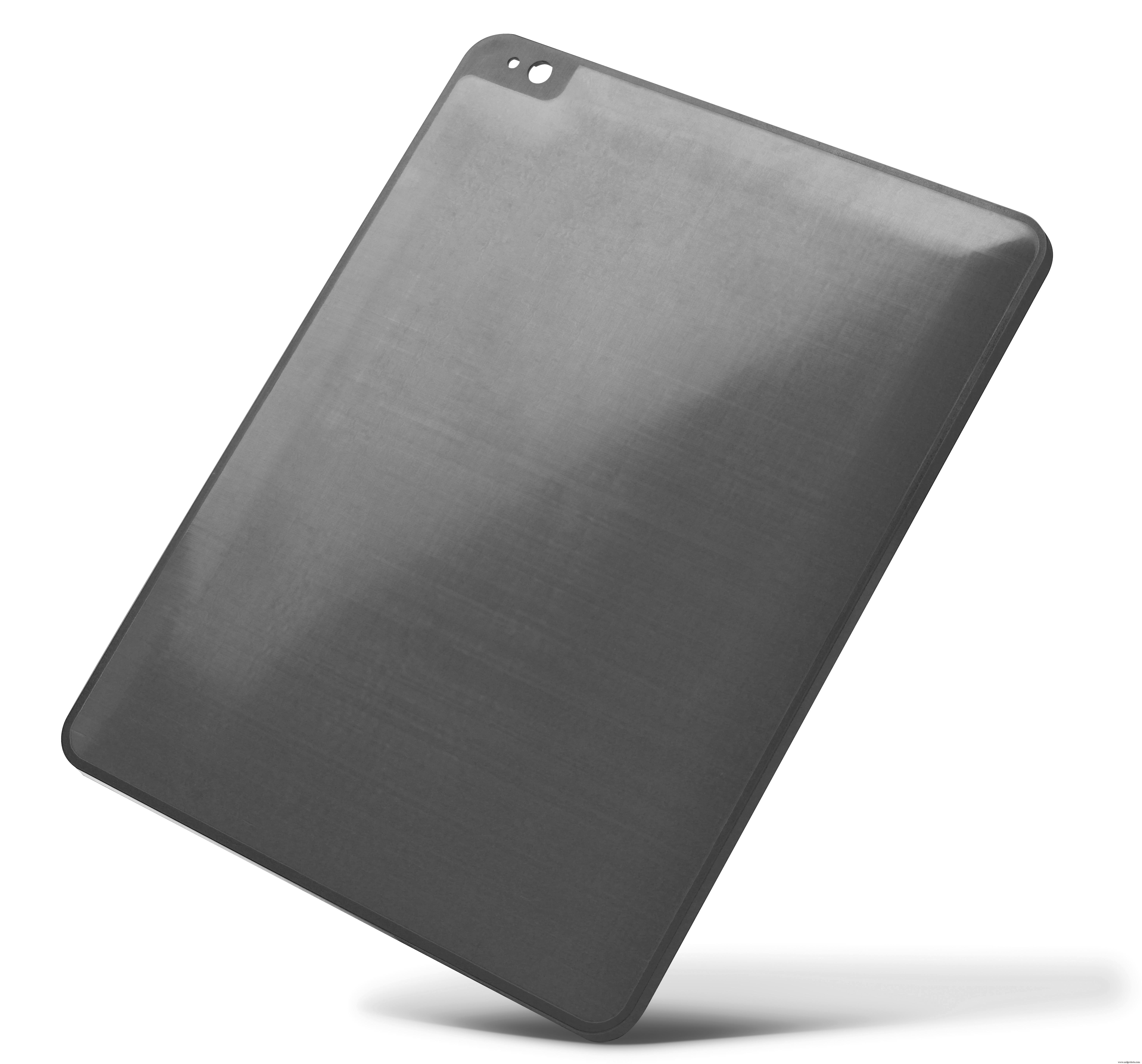
Передняя сторона окончательной крышки ноутбука / планшета, которая была изготовлена с использованием многослойной вставки на основе поликарбонатной ленты, армированной углеродным волокном, с отформованной смесью короткого стекла / сополимера поликарбоната, комбинации, которая отвечает всем соответствующим механическим и эстетическим требованиям в 1- деталь толщиной миллиметра.
Последний демонстрационный образец представляет собой ламинатную вставку, изготовленную из семи слоев разрабатываемых лент UDMAX из углеродного волокна / ПК (объемная доля волокна 55%), затем консолидированных, обрезанных, предварительно отформованных и снова обрезанных до окончательной формы сетки перед формованием под давлением с 40% волокна. -весовая фракция THERMOCOMP D452 короткое стекловолокно / сополимер ПК (марка, оптимизированная для высокой текучести и высокой эстетики и уже широко используемая в этом сегменте). Комбинация обеспечивает покрытие с высокой жесткостью и прочностью при небольшой массе и толщине сечения, а также включает в себя многочисленные детали трехмерного дизайна, особенности крепления и хорошую эстетику, тем самым используя лучшее из каждого материала. Сообщается, что чехол прошел все необходимые отраслевые испытания и в настоящее время оценивается производителями оборудования.
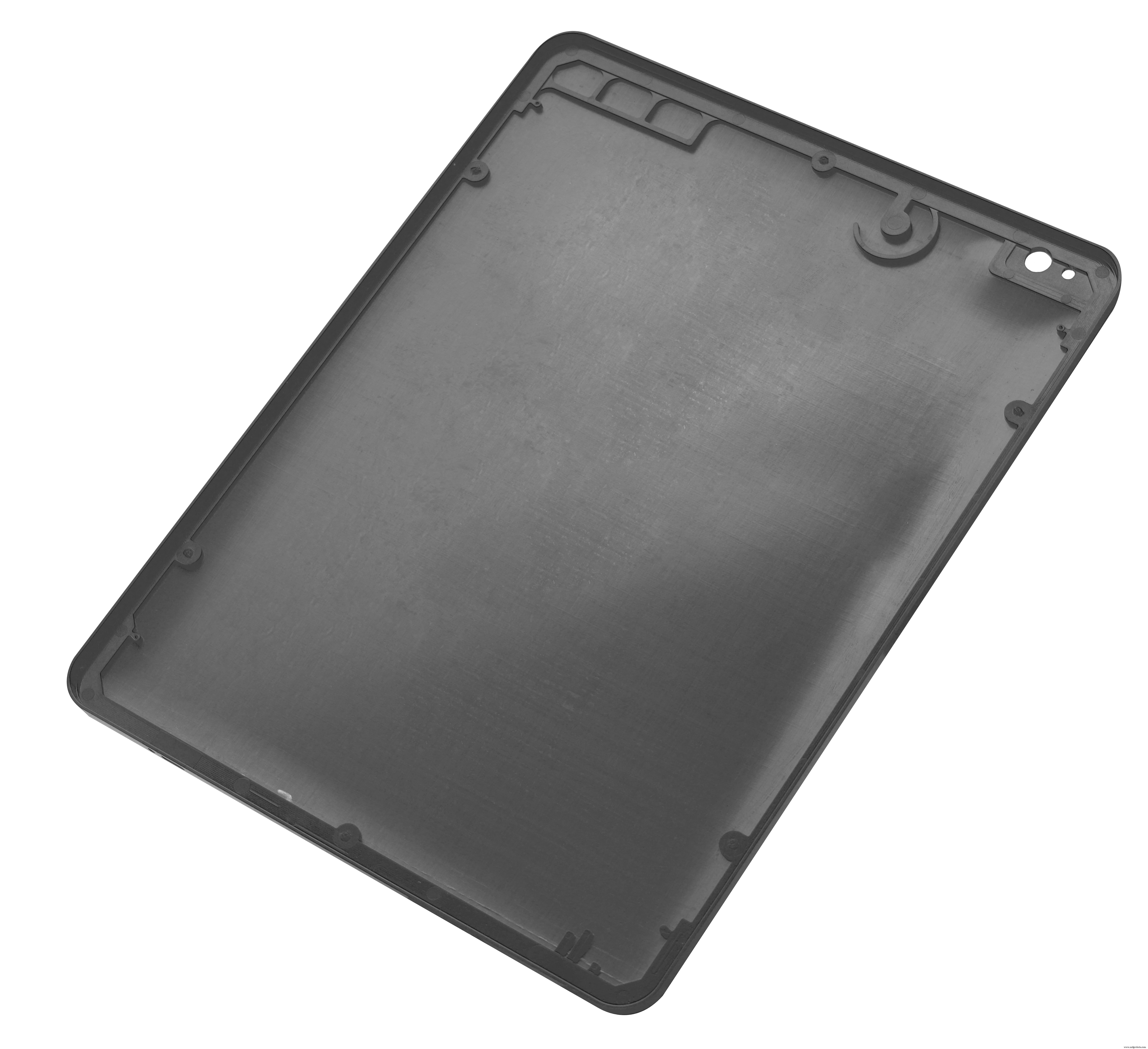
Оборотная сторона готовой обложки.
Работа между Airborne и SABIC также принесла свои плоды для достижения целей SABIC на рынке бытовой электроники. О партнерстве было объявлено в 2018 году, и в этом году были предоставлены дополнительные сведения о том, что обе компании называют своей производственной линией цифровых композитов, которая может производить четыре консолидированных ламинатных вставки чистой формы из термопластичных композитных лент в минуту или 1,5 миллиона ламинатов в год с единая производственная линия. Система считается гибкой (с точки зрения архитектуры и материалов) и быстрой. Начиная с 2020 года Airborne будет использовать эту линию для производства ламината для коммерческого использования в бытовой электронике, став ресурсом, который, как надеются обе компании, значительно увеличит проникновение термопластичных композитов в этот высококонкурентный и быстро развивающийся сегмент.
волокно
- Материалы:однослойный гибкий графит для бытовой электроники
- Solvay увеличивает емкость термопластичного композитного материала
- Колесо из термопласта выходит на неровную дорогу
- Fraunhofer вводит в эксплуатацию автоматизированные производственные ячейки Engel для НИОКР термопластичных компо…
- Термопластические ленты продолжают демонстрировать потенциал для создания композитных аэроструктур
- Avient выпускает влагостойкий нейлоновый термопластический композит с длинными волокнами
- INEOS Styrolution для создания производственной площадки для термопластичного композита StyLight
- Xenia представляет термопластичные композитные компаунды CF / PP
- NIARs NCAMP, квалифицирующий термопластический композит TenCate
- Композит + металл:гибридная технология полого профиля