Индивидуальные инструменты, закрепление помогают придать роторам форму
Разработав более точный процесс обработки для сопряжения со спиральными роторами, модели нагнетателя Whipple Supercharger могут более эффективно нагнетать воздух в двигатель для увеличения мощности. Индивидуальные зажимные и формовочные инструменты позволяют компании точно фрезеровать роторы нагнетателя за один установ на токарно-фрезерном станке с осью B.
Компания Fresno’s Whipple Superchargers, основанная бывшим руководителем гоночной бригады и владельцем автомобиля Артом Уипплом в 1987 году, производит двухвинтовые нагнетатели для автомобильных и морских гонщиков, а также для других, стремящихся улучшить характеристики своих двигателей. Эти типы «прибавителей мощности» (турбокомпрессоры и закись азота и другие) вводят в двигатель дополнительный воздух сверх того, что двигатель может тянуть сам по себе. Больше воздуха означает, что можно добавить больше топлива, существенно увеличивая рабочий объем двигателя, а также его мощность.
Ключевым моментом здесь является точное бесконтактное зацепление двух спиральных роторов внутри корпуса нагнетателя. В конструкции Whipple мужской ротор имеет три спиральных лепестка, а женский — четыре, объясняет дизайнер нагнетателя Гарретт Брайт. Они вращаются навстречу друг другу и чрезвычайно тесно. Когда лепестки каждого из них проходят мимо впускных отверстий для воздуха, воздух попадает в ловушку между роторами и корпусом. Вращение ротора постепенно уменьшает пространство, занимаемое воздухом, сжимая его. Сжатие продолжается до тех пор, пока внутреннее пространство лепестков не станет открытым для выпускного отверстия, через которое воздух выбрасывается с давлением выше атмосферного во впускной коллектор, расположенный над двигателем.
Эффективность нагнетателя зависит от эффективности уплотнения между сопрягаемыми роторами и корпусом. Ранее Whipple использовала только роторы, изготовленные и поставленные сторонней компанией. Он по-прежнему использует поставленные роторы для некоторых моделей своих нагнетателей. Однако с тех пор компания начала проектировать и обрабатывать свои собственные роторы собственными силами, а разработанный ею процесс обработки позволяет получать более цилиндрические и точные роторы, чем те, что поставляются ее поставщиком, в результате чего конструкции нагнетателя на 5% эффективнее, чем те, которые были предоставлены ее поставщиком. с помощью прилагаемых роторов.
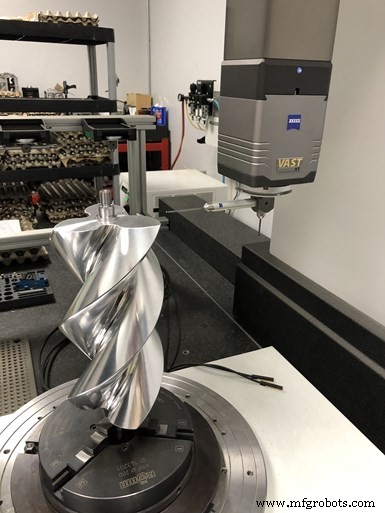
Измерения, проведенные на этой КИМ, позволили компании Whipple определить точность поставляемых роторов и роторов в машинах собственного производства. Его цель — добиться зазора между сопрягаемыми роторами в 125 микрон, чего теперь можно добиться благодаря внутренним возможностям многозадачной обработки.
Брайт объясняет, что компания Whipple решила изготовить свои собственные роторы после того, как увидела результаты измерений роторов своего поставщика, сделанных на ее координатно-измерительной машине (КИМ) Zeiss Accura. Эта КИМ оснащена поворотным столом, а также технологией сканирования Zeiss Vast и опцией Gear Pro в измерительном программном обеспечении Calypso. Брайт говорит, что это программное обеспечение особенно эффективно для измерения сопрягаемых роторов, поскольку он может назначать определенные контрольные точки на винтовых профилях охватываемого и охватывающего роторов, где они встречаются, чтобы определить зазор между ними в этих точках. Он определил, что профиль каждого ротора должен составлять ±63 микрона с целью достижения зазора примерно в 125 микрон. Whipple не получал этого от поставщика роторов.
Обработка собственными силами
Собственный процесс обработки роторов с использованием формообразующих инструментов аналогичен процессу поставщика, но с модификациями крепления для повышения жесткости.
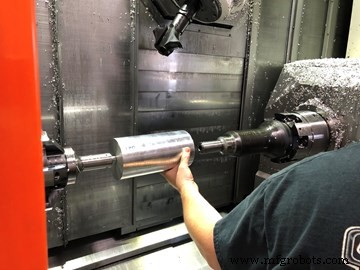
Когда оператор загружает алюминиевую заготовку ротора 6061 в токарно-фрезерный станок, главный шпиндель станка, а затем вспомогательный шпиндель зажимают выступающие стальные шейки вала.
Несколько лет назад компания приобрела для этой цели токарно-фрезерный станок Mazak Integrex e-420H-S II с фрезерной головкой с осью B. Фактически этот токарно-фрезерный станок не выполняет токарную обработку.
Цилиндрические алюминиевые заготовки ротора 6061 сначала просверливаются в центре на другом станке, чтобы в них можно было запрессовать стальной вал. Когда оператор загружает заготовку в Integrex, главный шпиндель станка, а затем вспомогательный шпиндель зажимают выступающие шейки вала. Затем ось B станка резко наклоняется, чтобы сориентировать инструмент нестандартной формы, который соответствует желаемому профилю канавки ротора под этим углом. Наконец, инструмент вращающейся формы перемещается вдоль оси Z по мере того, как ротор медленно вращается, создавая каждую канавку за несколько проходов.
Первоначально компания Whipple использовала удлиненные цанги ER с выдвижным механизмом для зажима шейки вала. Увеличенная длина требовалась для размещения заготовок вдали от контршпинделя, чтобы обеспечить достаточный зазор для шпинделя оси B, чтобы наклоняться над патроном контршпинделя настолько, насколько это было необходимо для размещения формного инструмента. Однако функция отвода этих цанг делала загрузку заготовок ротора трудоемкой и сложной задачей. Затягивание цангового патрона (приводящее к отводу) создавало чрезмерную нагрузку на главный шпиндель, а это означало, что вспомогательный шпиндель оси W должен был вдавливаться, чтобы уменьшить нагрузку. В противном случае может возникнуть вибрация или плохое качество поверхности. В результате операторы постоянно зажимали и зажимали до тех пор, пока большая часть нагрузки не была устранена, что обычно занимало 10 минут. Кроме того, компания Whipple постоянно заменяла цанговые патроны из-за их износа, вызванного многократным затягиванием и ослаблением.
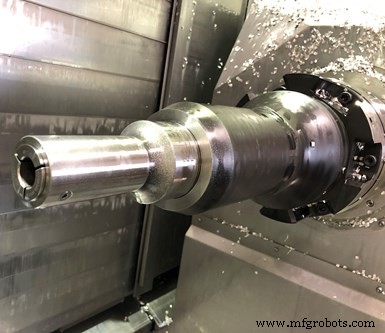
В отличие от использовавшихся ранее цанг ER, цанги длины не оттягивают заготовки и создают нагрузку на главный шпиндель, которую необходимо устранить. Это сократило время настройки с 10 до двух минут.
По совету Келлена Буша, инженера Mazak по применению, который работал с Whipple над этим проектом, компания связалась с Hainbuch, чтобы разработать альтернативный подход к закреплению. Том Чемберс, менеджер по продажам Hainbuch, объясняет, что разработанное компанией специальное решение для закрепления не только обеспечивает увеличенный радиус действия, необходимый для того, чтобы ось B машины могла наклоняться на требуемый угол без помех, но также обеспечивает более высокую жесткость при упрощении переналадки. Во многом это возможно благодаря тому, что вместо возвратных цанг используются цанговые зажимы. Чемберс говорит, что цанговые зажимы «зажимаются в пространстве», что означает, что заготовки ротора не будут двигаться, когда цанги зажаты. В результате к главному шпинделю не прикладывается дополнительная нагрузка, которую пришлось бы снимать. Переключение теперь занимает всего две минуты.
Формовочные инструменты Kyocera Unimerco, которые Whipple использует для обработки своих роторов (как и поставщик роторов Whipple), на самом деле обычно не используются для резки металла. Андерс Варга, менеджер по продажам Kyocera Unimerco, говорит, что этот тип инструмента обычно используется для резки дерева, композитов и других волокнистых материалов. Это в первую очередь связано с давлением, которое будет оказываться на инструмент в результате большой площади контакта между металлической заготовкой и длинными режущими кромками пластины. То, что эти инструменты можно использовать в этом приложении для обработки роторов, говорит о жесткости станка с интерфейсом шпинделя Capto и его нестандартным креплением.
Использование формовочных инструментов, которые соответствуют профилю винтовой канавки ротора (профили были уточнены Брайтом), устраняет необходимость полировки, которая может потребоваться, если для вырезания канавки использовалось несколько концевых фрез. Роторы обрабатываются таким образом, чтобы их кулачки были максимально большими, но немного меньшего размера, чтобы можно было нанести запатентованное покрытие. Whipple обычно держит под рукой два инструмента для черновой обработки и три инструмента для чистовой обработки обоих роторов. В инструментах используются пластины из мелкозернистого карбида без покрытия. Вставки для черновых инструментов крепятся к корпусам инструментов с помощью винтов; к ним припаяны отделочные инструменты.
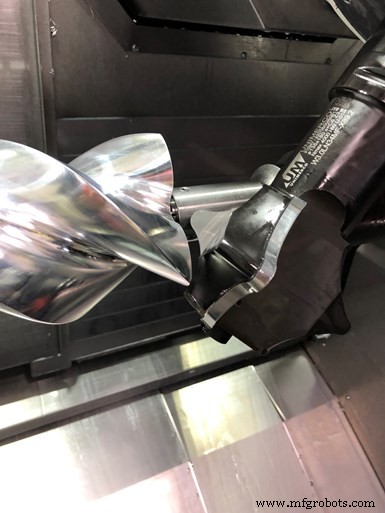
Используя инструменты формы, Whipple не имеет выполнить вторичную чистовую обработку, как если бы для создания канавок ротора использовались концевые фрезы.
Теперь этот процесс обработки не только достигает целевого зазора Брайта в 125 микрон между сопрягаемыми роторами, но и обеспечивает более постоянную цилиндричность ротора от начала до конца. Он говорит, что при оригинальном подходе к креплению разница в цилиндричности одного конца ротора по сравнению с другим может достигать 10 микрон. Он был уменьшен до 1 микрона. Время цикла ротора также немного меньше. Время цикла для ротора с наружной резьбой составляет 14 минут, а для ротора с внутренней резьбой — 20 минут. Но для Уиппла это подливка. Его основные цели заключались в достижении более высокой точности обработки роторов и ускорении переналадки, и обе цели были реализованы.
Промышленное оборудование
- Mecademic Robotics выходит на огромные рынки со своим крошечным роботом
- Schilling Robotics интегрирует программное обеспечение Energid в своего подводного робота Gemini
- Служба Rapid Tooling и ее эффективное применение
- Как инструменты, напечатанные на 3D-принтере, могут изменить будущее прототипирования
- Инструменты для станков швейцарского типа
- Преодоление трудностей
- Установление бережливых связей
- Думаете о том, чтобы начать работать с Live Tooling? Вот что вам нужно знать
- 5 ключевых преимуществ изготовления металлоконструкций на заказ
- Что такое кевлар? Краткое руководство