Как 5 крупнейших производителей автомобилей используют 3D-печать
3ERP охватывает множество различных способов, которыми производители автомобилей извлекают выгоду из преимуществ, которые 3D-печать выводит на передний план. По мере того, как технологии становятся все более популярными в автомобильной промышленности, многие компании обращают на это внимание, но многие используют их в разных целях и в разных целях. Эти потребности могут охватывать все:от инструментов до запасных частей/управления цепочками поставок, запчастей для конечного использования и даже автомобилей.
Интересно посмотреть, как далеко продвинулась эта технология, как она используется крупными именами в отрасли и как они видят ее применение в своих будущих производственных цепочках. Цель этой статьи — дать представление о том, как крупнейшие мировые производители автомобилей используют 3D-печать в своих рабочих процессах.
БМВ
Поскольку большая часть 3D-печати используется для небольших производственных циклов, существует много возможностей для настройки и добавления сложности с использованием уникальных элементов, которые позволяет 3D-печать. BMW не привыкать к таким формам проектирования и производства, используя 3D-печать при предварительной разработке, проверке и тестировании автомобилей, а также при создании концептов и демонстрационных автомобилей. Они используют эту технологию для больших объемов, но меньшие производственные партии позволяют им персонализировать продукты в точном соответствии с потребностями своих клиентов.
Компания широко использует аддитивное производство, отмечая, что они потенциально видят «большой будущий потенциал для серийного производства и новых предложений для клиентов (по мнению экспертов BMW в Германии). Они использовали эту технологию для улучшения как пластиковых, так и металлических компонентов. Они наиболее известны тем, что сотрудничали с HP для производства продуктов на своих крупномасштабных производственных системах.
Как и многие другие компании в этом списке, BMW использует его как средство производства деталей, которые невозможно создать с помощью других технологий. Хорошим примером этого является верхняя крышка родстера i8. Изготовление крепления для этого компонента было бы невозможно с использованием традиционного процесса литья. Помимо расширения возможностей дизайна, напечатанная на 3D-принтере деталь автомобиля более долговечна и весит меньше, чем предыдущие версии.
Точно так же BMW представила гоночный болид iFE.20 Formula E с охлаждающим валом, напечатанным на 3D-принтере из льняного волокна. Деталь была продемонстрирована в конце 2019 года. По сравнению с обычными углеродными материалами лен обладает большей поглощающей способностью и большей ударопрочностью, что может быть выгодно на уличных трассах с их неровностями и краш-барьерами, на которых проходит Формула Е. Это сделало его первым гоночным автомобилем BMW, созданным рабочей командой, детали которого изготовлены из возобновляемых текстильных волокон, что также делает его экологически безопасным.
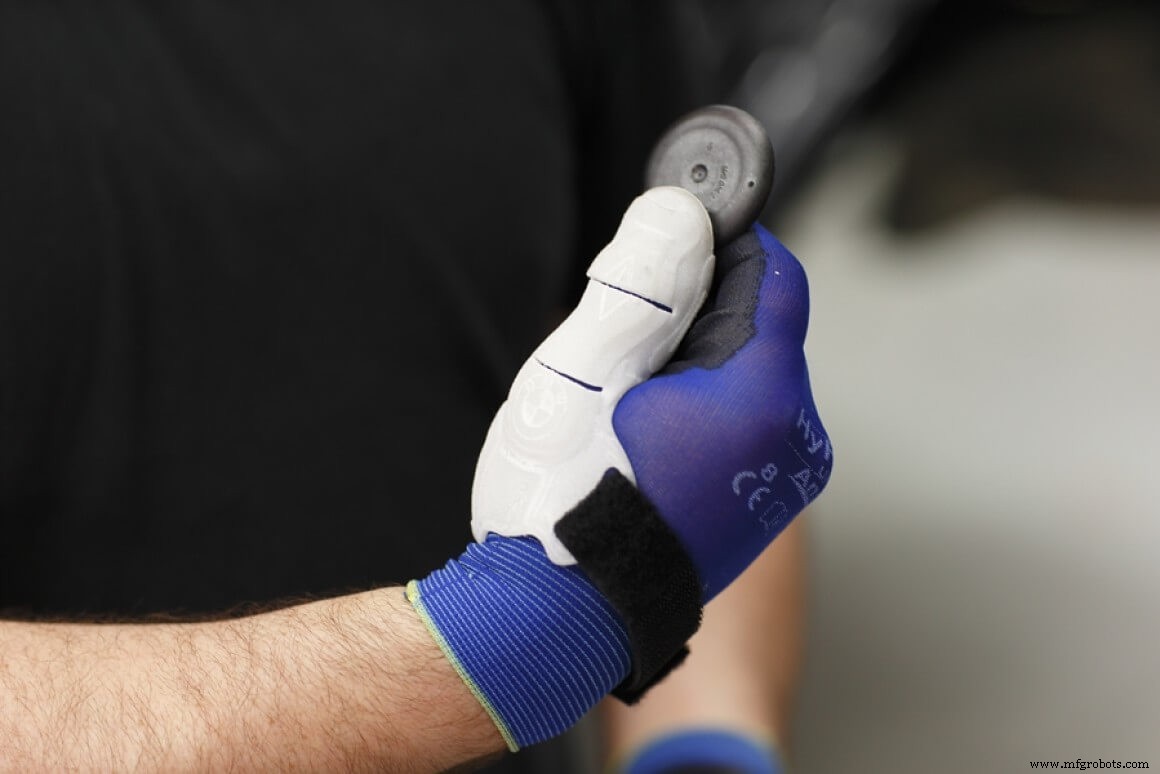
Перчатки BMW с защитой большого пальца
Компания также использует 3D-печать для инструментов и безопасности. Хорошим примером этого являются специальные перчатки, которыми они заделывают пробки сливных отверстий. Эти стопоры должны быть установлены вручную пальцами инженера, что означает большую нагрузку на большие пальцы. К счастью, они придумали решение для 3D-печати, которое можно было надеть на рабочие перчатки.
Помимо работы над собственными автомобилями, инженеры компании помогали сторонним проектам. Одним из примеров является разработка сделанных на заказ 3D-печатных сидений для британской баскетбольной команды Паралимпийских игр. Используя 3D-сканирование тела и последние разработки в области аддитивного производства, инженеры BMW создали целый парк инвалидных колясок, позволяющих игрокам демонстрировать более высокий уровень спортивного мастерства.
Форд
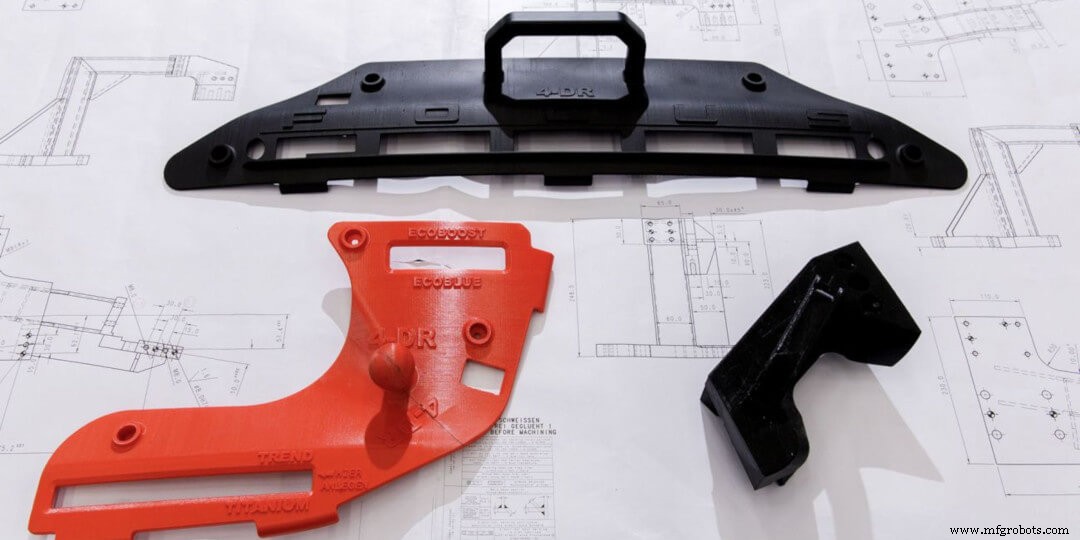
Приспособления и приспособления Ford
Что касается приверженности 3D-печати, Ford стремится освоить эту технологию. Компания создала центр аддитивного производства и широко использовала его операции в своих рабочих процессах. Что касается создания отпечатков на пластике и металле, они давно сотрудничают с различными компаниями, такими как Ultimaker, Stratasys и GE Additive, которые предоставляют машины для всех видов аддитивных приложений по всей производственной цепочке.
Они также используют 3D-печать, чтобы сократить расходы и время на оснастку, поскольку компания обнаружила, что быстрее изготавливать собственные детали на объекте, чем ждать поставщиков и другие подобные вещи. Они также применяют те же принципы к зажимным приспособлениям и приспособлениям, которые они разрабатывают на объектах по всему миру.
За последние несколько десятилетий они расширили свои операции по 3D-печати, производя как металлические, так и пластиковые компоненты. Как заявляет компания:«За последние несколько десятилетий Ford напечатал более 500 000 деталей и сэкономил миллиарды долларов и миллионы рабочих часов. Если изготовление прототипа традиционными методами заняло бы 4–5 месяцев и стоило бы 500 000 долларов США, то деталь, напечатанная на 3D-принтере, может быть изготовлена за считанные дни или часы и стоит несколько тысяч долларов ".
Точно так же различные дочерние компании Ford хвастаются своими AM-отбивными, в первую очередь команды разработчиков Shelby GT500. В этом году они за несколько дней напечатали на 3D-принтере самые многообещающие модели нового GT500, что значительно ускорило этапы усовершенствования и тестирования. Такой темп позволяет им быстро постепенно настраивать Shelby GT500, добавляя новые физические конструкции с головокружительной скоростью. Они также разработали новый гибридный дизайн крыла со спойлером, который команда называет «качели». Этот новый дизайн является важным фактором впечатляющих аэродинамических возможностей GT500.
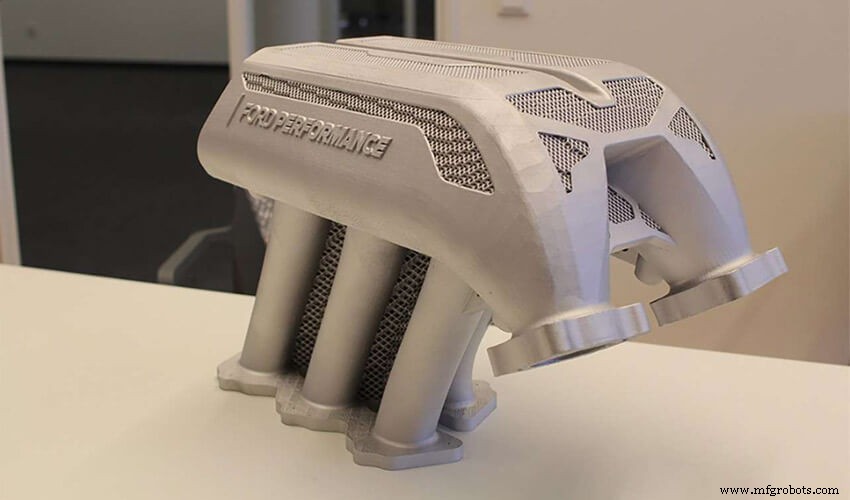
Двигатель EcoBoost
Еще в феврале компания установила еще одну важную веху в области 3D-печати. Их подразделение Ford Performance, занимающееся высокопроизводительными компонентами, напечатало на 3D-принтере то, что, как они утверждают, является самой большой металлической автомобильной деталью для рабочего автомобиля в истории автомобилестроения. Металлическая деталь была установлена в Hoonitruck, Ford F-150 1977 года выпуска с 3,5-литровым двигателем V6 EcoBoost с двойным турбонаддувом. Сама деталь представляет собой алюминиевый входной патрубок, напечатанный с помощью Concept Laser X LINE 2000R компании GE Additive.
Вольво
Volvo не является самым известным пользователем автомобильной 3D-печати, но в последние годы добилась больших успехов в этом направлении. Как и многие другие компании из этого списка, Volvo использует 3D-печать для изготовления инструментов и управления цепочками поставок. Использование 3D-печати оказалось особенно полезным при пополнении запасов машин компании новыми отпечатками деталей, снятых с производства. Volvo в основном использует пластиковые детали, напечатанные на 3D-принтере, и в ближайшем будущем планирует реализовать металлические детали.
По состоянию на 2018 год компания использовала аддитивное производство в основном для создания прототипов и оснастки. «Поскольку для прототипирования нам нужно производить небольшие партии деталей, это хороший способ увидеть, что работает», — говорит Фредрик Андерссон, инженер-разработчик по установке трансмиссии колесных погрузчиков в Volvo CE [строительное оборудование]. «У нас много знаний, и мы можем быстро и легко вносить изменения с помощью 3D-печати. Благодаря этому время вывода нового продукта на рынок сокращается, что приносит большую пользу нашей компании .”
Увеличенная скорость прототипирования была чрезвычайно полезна для компании, как доказывают различные новые технологии, которые они тестировали. Например, инженеры Volvo разработали новые корпуса водяных насосов для автомобилей компании A25G и A30G. Они запустили симуляции как средство оптимизации конструкции внутренних каналов в корпусе, но им нужно было построить прототип для проведения функциональных испытаний для проверки новой конструкции. Стоимость инструмента для этого проекта составила бы приблизительно 9 090 долларов США, а стоимость деталей – около 909 долларов США. Срок изготовления прототипа должен был составлять минимум 20 недель. С другой стороны, 3D-печать прототипа стоила 770 долларов и заняла всего две недели.
Однако в 2019 году компания повысила планку своих процессов AM, особенно в своем филиале Volvo Trucks. Их завод в Нью-Ривер-Вэлли (NRV) в Дублине, штат Вирджиния, в этом году попал в заголовки мировых производственных компаний. В основном они используют SLS, но также пробуют другие методы AM. Это конкретное предприятие производит более 500 производственных инструментов и приспособлений, используемых в цехах, изготовленных с использованием 3D-печати. Этот объект также является крупным центром автомобилестроения в Северной Америке.
Помимо коммерческих автомобилей, компания также разрабатывает строительную технику. Разумеется, 3D-печать также повлияла на этот аспект деятельности компании. Volvo применила 3D-печать для модернизации своих самосвалов с шарнирно-сочлененной рамой и, таким образом, сократила стоимость прототипирования на десятую часть. Это также позволило им сократить затрачиваемое время с 20 до всего лишь 2 недель.
ГМ
General Motors и другие ее филиалы являются основными пользователями (и разработчиками) технологии 3D-печати. По состоянию на 2018 год GM экономила 300 000 долларов в год на инструментах и добилась значительных успехов в разработке новых технологий с использованием альтернативных источников топлива. В прошлом году ведущий автопроизводитель объявил, что к 2023 году планирует выпустить по всему миру 20 новых моделей с электродвигателями и топливными элементами.
Хотя их операции по 3D-печати в основном касались прототипирования, они расширяются. В дальнейшем компания планирует расширить свои печатные операции, чтобы производить «десятки тысяч деталей в масштабе по мере совершенствования технологии». », — сказал Кевин Куинн, директор по аддитивному дизайну и производству в GM. Этот план, скорее всего, будет реализован в течение следующих 5 лет.
Технический центр Уоррена компании ежегодно производит около 30 000 прототипов деталей. Детали состоят как минимум из девяти видов материалов с использованием комбинаций пластмасс, металлов и порошков. Они в основном используются для прототипирования, но компания также рассматривает детали для конечного использования. Они также владеют лабораториями HRL вместе с Boeing, который прекратил производство алюминиевого сплава с помощью 3D-печати.
Дэн Гришабер, директор GM по глобальной производственной интеграции, заявил, что на большинстве заводов GM сейчас есть 3D-принтеры. Компания планирует увеличить его еще больше, по крайней мере, на своих североамериканских заводах. Этот шаг, вероятно, позволит GM ежегодно экономить миллионы долларов на производственных затратах. GM уже давно является инвестором 3D-печати и ее различных дочерних технологий. Они применяют его для быстрого создания инструментов и аксессуаров для рабочих на своих заводах. Только в этом году компания заявила, что внедрение машины для 3D-печати стоимостью 35 000 долларов сэкономило компании 300 000 долларов за два года. Хотя производство инструментов является основной ролью, которую играет принтер, вполне возможно, что компания увеличит роль аддитивного производства в своей повседневной деятельности.
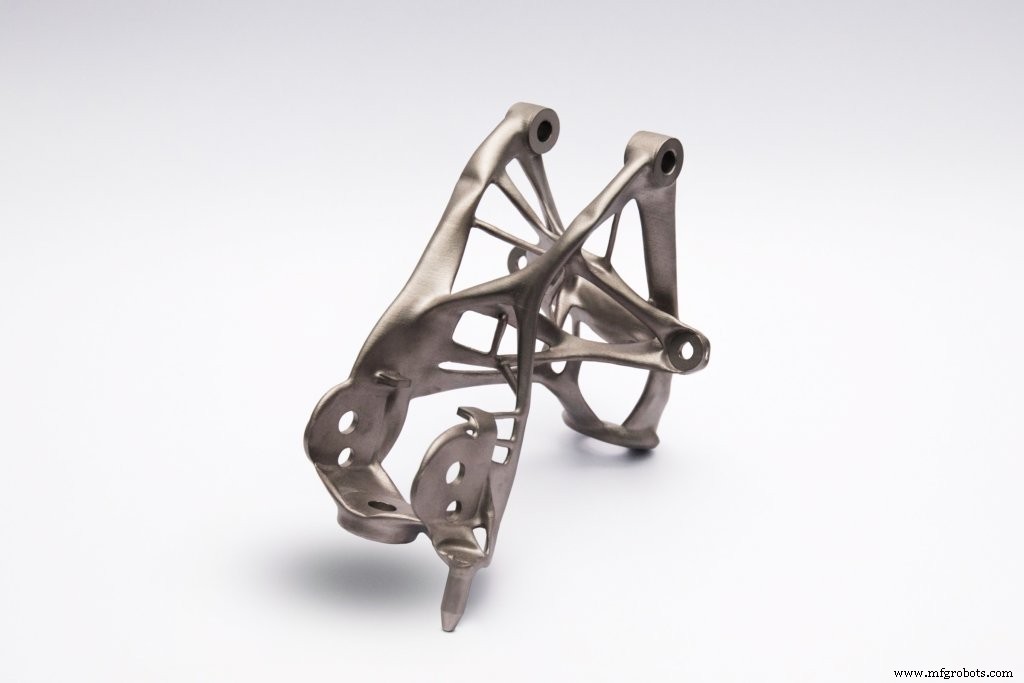
Кронштейн GM разработан в сотрудничестве с Autodesk
Их партнерство с Autodesk принесло пользу в производстве легких 3D-печатных деталей, которые могли бы помочь автопроизводителю достичь своих целей по добавлению автомобилей на альтернативном топливе в свою линейку продуктов. В рамках этого же сотрудничества в 2019 году обе компании продемонстрировали кронштейн сиденья, напечатанный на 3D-принтере из нержавеющей стали и разработанный с использованием технологии Autodesk.
В начале 2019 года GM рассматривала новое дизайнерское приложение для 3D-печати. В сотрудничестве с Michellin они стремились создать новый тип шин с превосходной износостойкостью. Шина Uptis все еще находится в стадии разработки, но компании перешли к этапу испытаний. Они утверждают, что шины будут на 100% экологичными, прочными и смогут прослужить еще дольше. Они также являются гораздо более экологичной альтернативой с меньшим количеством отходов во время производства. Недавно инженеры использовали парк электромобилей Chevrolet Bolt для тестирования новых шин в Мичигане и предложили сделать их доступными для широкой публики в 2024 году.
Порше
Porsche использует 3D-печать для самых разных целей, от изготовления основных компонентов до переосмысления цепочки поставок для своих старых моделей. В настоящее время Porsche использует 3D-печать для производства очень специфических запасных частей, но не так широко. Это связано со строгими стандартами качества, которые они должны соблюдать, чтобы обеспечить безопасность на должном уровне. Компания также работает с меньшим общим количеством произведенных единиц, поскольку они больше относятся к классическим и роскошным автомобилям.
Для разработки снятых с производства компонентов, таких как рычаг выключения сцепления на Porsche 959, компания использует лазерное плавление. Они используют порошковую инструментальную сталь и извлекают деталь намного эффективнее, чем это было бы возможно с помощью альтернативных методов.
Использование 3D-печати также позволило компании перейти к печати по требованию, что позволило значительно снизить затраты, связанные с материалами, транспортировкой и хранением. Это также выгодно, поскольку эти детали не пользуются большим спросом, и часто их постоянное производство обходится дорого. Наиболее известным примером сотрудничества Porsche с Markfordged является возрождение этих классических деталей.
В основном они используют SLM и SLS для производства различных деталей. Porsche заявил, что детали, напечатанные на 3D-принтере, во многих случаях превосходят старые. Хотя в настоящее время они печатают ограниченное количество деталей, с 2018 года они расширяют ассортимент и тестируют будущие компоненты.
Станок с ЧПУ
- Как мы используем молибден?
- Насколько экологически безопасна промышленная 3D-печать?
- Как использовать функцию в VHDL
- Как использовать процедуру в VHDL
- Как использовать станок для резки акрила для резки акрила
- Датчик инструмента фрезерного станка с ЧПУ по дереву, как им пользоваться?
- Как 3D-печать используется в производстве пресс-форм
- Как производители могут использовать аналитику для улучшения качества обслуживания клиентов
- Как работает офсетная печать?
- Как использовать шлифовальный станок