Процессы термической обработки:виды, методы, процедура, применение (PDF)
В этой статье вы узнаете, что такое процесс термообработки. ? Его методы , типы и цель , процедура , приложение термической обработки. Термическая обработка является важной операцией в процессе производства деталей машин и инструментов.
Что такое термическая обработка?
Термическая обработка определяется как операция, включающая нагрев и охлаждение металла или сплава в твердом состоянии для получения определенных желаемых свойств без изменения состава.
Процесс термической обработки проводится для изменения размера зерна, модификации структуры материала и снятия напряжений, возникающих в материале после горячей или холодной обработки давлением.
- Термическая обработка проводится для улучшения обрабатываемости.
- Для улучшения магнитных и электрических свойств.
- Для повышения стойкости к износу, нагреву и коррозии, а также по многим другим причинам.
Термическая обработка состоит из нагревания металла вблизи или выше его критической температуры, выдерживаемого в течение определенного времени, при этом окончательно охлаждают металл в какой-либо среде, которая может быть воздухом, водой, рассолом или расплавленными солями. Процесс термической обработки включает отжиг, поверхностную закалку, отпуск, нормализацию и закалку, азотирование, цианирование и т. д.
Типы процессов термообработки
Ниже приведены различные типы процессов термообработки:
- Отжиг
- Нормализация
- укрепление
- Закалка
- Азотирование
- Цианирование
- Индукционная закалка
- Закалка пламенем
- Что такое процесс литья металла? Полное руководство
- Список механических свойств материалов
Виды термической обработки
1. Отжиг
Отжиг — один из важнейших процессов термической обработки. Это одна из наиболее широко используемых операций при термической обработке железа и стали, определяемая как процесс размягчения.
Нагрев от 30 - 50 °C выше верхней критической температуры и охлаждение с очень медленной скоростью в результате поиска в печи. Основная цель отжига — сделать сталь более пластичной и ковкой, а также снять внутренние напряжения. Этот процесс делает сталь мягкой, чтобы ее можно было легко обрабатывать.
1.1 Цель отжига
- Размягчает сталь и улучшает ее обрабатываемость.
- Чтобы уменьшить размер зерна и удалить газы.
- Удаляет внутренние напряжения, возникшие в ходе предыдущего процесса.
- Чтобы получить желаемую пластичность, пластичность и прочность.
- Он изменяет электрические и магнитные свойства.
1.2 Процедура отжига
В зависимости от содержания углерода сталь нагревают до температуры примерно на 50–55 °C выше ее критического температурного диапазона. Выдерживается при этой температуре определенное время в зависимости от типа печи и характера работы. Затем стали дают постоянно остывать внутри печи.
1.3 Применение отжига
Применяется для отливок и поковок.
2. Нормализация
Нормализация. Основная цель нормализации — снять внутренние напряжения, возникшие после процесса холодной обработки давлением. При этом сталь нагревают на 30–50°C выше ее верхней критической температуры и охлаждают на воздухе.
Улучшает механические и электрические свойства, обрабатываемость и прочность на растяжение. Нормализация – это процесс термической обработки, проводимый для восстановления нормального состояния конструкции.
2.1 Цель нормализации
- Содействовать единообразию структуры.
- Для обеспечения измельчения зерна.
- Чтобы добиться желаемых изменений в свойствах стали.
2.2 Процедура нормализации
Сталь нагревают до температуры примерно на 40-50°С выше ее верхней критической температуры. Выдерживается при этой температуре непродолжительное время. Затем сталь охлаждают в неподвижном воздухе при комнатной температуре, что называется закалкой на воздухе.
2.3 Применение нормализации
- Применяется в отливках и поковках для улучшения структуры зерна и снятия напряжений.
- Применяется после холодной обработки, такой как прокатка, штамповка и ковка.
3. Закалка
Закалка. Основная цель процесса закалки — сделать сталь твердая жесткая. В этом процессе сталь нагревают на 30–40 °C выше верхней критической температуры, а затем продолжают охлаждать до комнатной температуры путем закалки в воде или масле. Это процесс, противоположный отжигу.
3.1 Цель усиления
- При закалке повышается твердость стали.
- Износостойкий
- Позволяет стали резать другие металлы.
3.2 Процедура усиления защиты
Сталь нагревается выше критического диапазона температур. Он выдерживается при этой температуре в течение определенного периода времени. Затем сталь быстро охлаждают в среде закалки.
Закалочная среда выбирается в зависимости от желаемой степени твердости. В качестве закалочных сред используются воздух, вода, нефть, масла и расплавы солей. Тонкие шлифы лезвий таких ножей охлаждают на воздухе. Широко используемой средой является вода, но она приводит к образованию пузырьков на поверхности металла.
Поэтому для предотвращения этого используется солевой раствор. Масло используется, когда есть риск деформации на трещинах и подходит для легированных сталей. Расплавы солей используются для охлаждения тонких срезов для получения ударопрочных изделий без трещин.
3.3 Применение усиления
Применяется для зубил, кувалд, ручных молотков, кернеров, метчиков, плашек, фрез, лезвий ножей и шестерен.
4. Закалка
Отпуск:Когда в процессе закалки стальной образец затвердевает, он становится хрупким и имеет высокое остаточное напряжение. Это операция, используемая для изменения свойств стали, упрочненной закалкой, с целью повышения ее полезности.
Закалка или волочение приводят к снижению хрупкости и снятию внутренних напряжений, возникающих при закалке. Сталь должна быть закалена после процесса закалки.
Отпуск делится на три категории в зависимости от пригодности стали.
- Низкотемпературный отпуск.
- Среднетемпературный отпуск.
- Высокотемпературный отпуск.
4.1 Цель закалки
- Для снятия внутреннего напряжения, вызванного закалкой.
- Для уменьшения хрупкости.
- Повысить пластичность, прочность и ударную вязкость.
- Для повышения износостойкости.
- Для получения желаемых механических свойств.
4.2 Процедура закалки
Сталь после закалки в процессе закалки повторно нагревают до температуры, несколько превышающей диапазон температур, в котором она должна использоваться, но ниже нижней критической температуры. Температура здесь варьируется от 100°C до 700°C.
Повторный нагрев производится в ванне с маслом, расплавленным свинцом или расплавленной солью. Образец выдерживают в ванне некоторое время до равномерного прогрева, время зависит от состава и желаемого качества стали. Теперь образец вынимают из ванны и дают ему медленно остыть на воздухе.
4.3 Применение закалки
Он применяется к режущим инструментам, инструментам и зубчатым колесам, которые упрочняются в процессе закалки.
5. Азотирование
Азотирование — это процесс поверхностного или поверхностного упрочнения, при котором газообразный азот используется для получения твердой корки металла. В этом процессе сталь нагревают в присутствии аммиачной среды.
Из-за этого атом азота осаждается и делает материал твердым. Объекты индукционной закалки и закалки пламенем нагреваются кислородно-ацетиленовым пламенем.
5.1 Цель азотирования
- Для упрочнения поверхности стали на определенную глубину.
- Повысить устойчивость к износу и усталости.
- Для повышения коррозионной стойкости.
5.2 Процедура азотирования
Это делается в электропечи, где поддерживается температура от 450° до 510°С. Деталь хорошо обработана и обработана и помещена в герметичный контейнер, снабженный выходной и входной трубками, через которые циркулирует газообразный аммиак.
Емкость с деталью помещают в печь и пропускают через нее газообразный аммиак, пока печь нагревается.
В процессе нагревания из аммиака выделяется газообразный азот в виде атомарного азота, который вступает в реакцию с поверхностью детали, образуя нитрат железа.
Глубина входа зависит от продолжительности времени, проведенного при температуре азотирования. Деталь вынимается и не требует ни закалки, ни дальнейшей термообработки.
5.3 Применение азотирования
- Применяется для упрочнения поверхности среднеуглеродистых легированных сталей.
6. Цианирование
Цианирование:в этом процессе сталь нагревают в присутствии цианида натрия. Благодаря этому атомы углерода и азота оседают на поверхности стали и делают ее твердой.
6.1 Цель цианирования
- Этот метод эффективен для увеличения предела выносливости деталей среднего и малого размера, таких как шестерни, валы, поршневые пальцы и т. д.
- Для повышения твердости поверхности.
- увеличить износостойкость.
- Чтобы придать чистый, яркий и приятный вид закаленной поверхности.
6.2 Продукция для цианирования
Детали, подлежащие обработке, погружают в ванну с расплавленной цианидной солью, поддерживаемую при температуре 950°C. В качестве расплавленных солей используются хлорид натрия, карбонат натрия, цианид натрия и кальцинированная сода.
Погруженное изделие оставляют в расплавленной цианистой соли при температуре 950°С примерно на 15-20 минут. При разложении цианида натрия из монооксида углерода выделяются азот и углерод, которые диффундируют в поверхность, что приводит к ее отверждению. Затем деталь вынимают из ванны и закаливают в воде или масле.
6.3 Применение цианирования
- Он применяется к небольшим изделиям, таким как шестерни, втулки, винты, штифты и небольшие ручные инструменты, для которых требуется тонкая и прочная износостойкая поверхность.
7. Науглероживание
Науглероживание:в этом процессе сталь нагревают в присутствии углерода. Благодаря этому атомы углерода оседают на поверхности металла и делают его твердым.
8. Упрочнение корпуса или поверхностное упрочнение
Основная цель этого процесса - сделать единственную внешнюю поверхность стали твердой, а внутреннюю сердцевину - мягкой. Это процесс науглероживания, т. е. насыщения поверхностного слоя стали углеродом, или какой-либо другой процесс, при котором оболочка затвердевает, а сердцевина остается мягкой.
8.1 Цель усиления защиты
- Для получения твердости и износостойкости деталей машин.
- После закалки получается прочная сердцевина.
- Для получения более высокого предела выносливости и высоких механических свойств сердечника.
Цель термической обработки стали
Ниже приведены цели термообработки.
- Для улучшения механических свойств, таких как прочность на растяжение, твердость, пластичность, ударопрочность и устойчивость к коррозии.
- Улучшение обрабатываемости.
- Для снятия внутренних напряжений металла, возникающих при холодной или горячей обработке давлением.
- Чтобы изменить или уточнить размер зерна.
- Улучшение магнитных и электрических свойств.
- Повысить устойчивость к износу и коррозии.
- Для увеличения твердости поверхности.
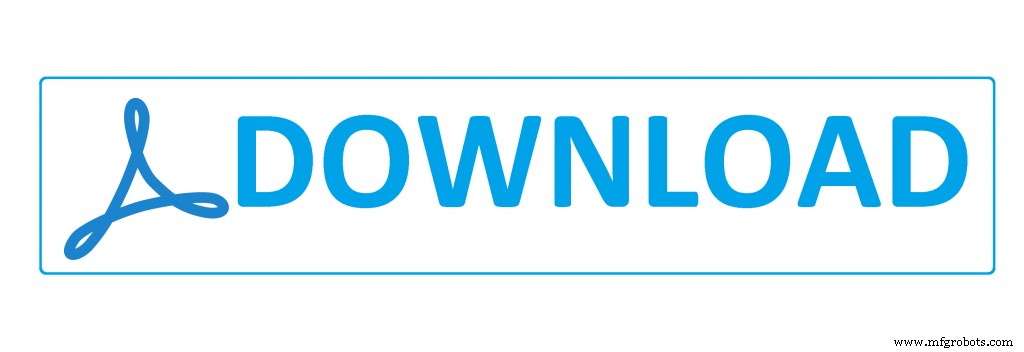
Заключение
Итак, теперь мы надеемся, что развеяли все ваши сомнения относительно процесса термообработки. Если у вас все еще есть сомнения относительно процесса термообработки или методы, типы, приложения вы можете спросить в комментариях.
У нас также есть сообщество Facebook для вас, ребята. Если хотите, вы можете присоединиться к нашему сообществу, вот ссылка на нашу группу в Facebook.
Вот спасибо за прочтение. Если вам понравилась наша статья, поделитесь ею с друзьями. Если у вас есть какие-либо вопросы по какой-либо теме, вы можете задать их в разделе комментариев.
Подпишитесь на нашу рассылку, чтобы получать уведомления о новых публикациях.
Промышленные технологии
- Термическая обработка титанового сплава
- Что такое 3D-печать? Принцип работы | Типы | Приложения
- Что такое сглаживание? 6 различных типов и методов
- Что такое термическая обработка? - Процесс и методы
- Определение металлического литья, типы и процессы
- Виды термической обработки литья в песчаные формы
- Термообработка прецизионных деталей
- Типы процессов обработки на токарных станках с ЧПУ
- Термообработка алюминиевых отливок
- Различные типы процессов газовой сварки и их применение