Что такое процесс термической обработки – виды, методы, преимущества
В этой статье мы узнаем, что такое процесс термообработки а также о различных типах процессов термообработки. в деталях.
Что такое процесс термообработки?
Термическая обработка относится к комбинации нагревания и охлаждения металла или сплава в твердом состоянии с целью получения желаемых свойств. Изменения свойств являются результатом микроструктурных изменений в материале, полученных в результате операций термообработки.
Термическая обработка — это процесс нагревания и охлаждения металлов с использованием заранее определенных методов для получения желаемых свойств. Как черные, так и цветные металлы проходят термическую обработку перед использованием. Со временем было разработано множество различных методов. Даже сегодня металлурги постоянно работают над улучшением результатов и экономической эффективности этих процессов.
Для этого они разрабатывают новые графики или циклы для производства различных сортов. Каждый график относится к разной скорости нагрева, выдержки и охлаждения металла. Эти методы, если следовать им скрупулезно, могут производить металлы различных стандартов с удивительно специфическими физическими и химическими свойствами.
Основы термической обработки
Хотя железо и сталь составляют подавляющее большинство термообрабатываемых материалов, сплавы алюминия, меди, магния, никеля и титана также могут подвергаться термообработке.
Процессы термообработки требуют трех основных этапов. Или мы можем сказать, что стадии термической обработки:
- Нагрев до заданной температуры
- Выдерживание при этой температуре в течение соответствующего времени.
- Охлаждение в соответствии с предписанными методами
Температура может достигать 2400 °F и время при температуре может варьироваться от нескольких секунд до целых 60 часов и более .
В печи одни материалы охлаждаются медленно, а другие должны быть закалены. . Обработка при -120°F или ниже требуется для некоторых криогенных процессов . Вода, рассол, масла, растворы полимеров, расплавленные соли, расплавленные металлы и газы являются некоторыми примерами закалочной среды. У каждого есть свой набор характеристик, которые делают его идеальным для конкретных задач. С другой стороны, 90 процентов деталей закалены в воде, масле, газе или полимерах.
А. Этап нагрева
На этапе нагрева основной целью является обеспечение равномерного нагрева металла. Медленное нагревание обеспечивает равномерный нагрев. Если вы нагреваете металл неравномерно, одна секция может расширяться быстрее, чем другая, что приводит к деформации или растрескиванию секции металла. Вы выбираете скорость нагрева на основе следующих факторов:
1. Теплопроводность металла: Металлы с высокой теплопроводностью нагреваются быстрее, чем металлы с низкой теплопроводностью.
2. Состояние металла: Инструменты и детали, которые ранее подвергались закалке или напряжению, должны нагреваться медленнее, чем инструменты и детали, которые не подвергались закалке.
<сильный>3. Размер и поперечное сечение металла: Чтобы внутренняя температура была близка к температуре поверхности, более крупные детали или детали с неровным поперечным сечением должны нагреваться медленнее, чем мелкие детали. В противном случае вы рискуете растрескаться или чрезмерно деформироваться.
Б. Этап замачивания
Цель стадии замачивания — поддерживать нужную температуру металла до тех пор, пока не примет форму желаемая внутренняя структура. «период замачивания ” относится к тому, как долго металл хранится при соответствующей температуре. Вам понадобится химический анализ и масса металла, чтобы определить правильную продолжительность времени. Период замачивания для неровных поперечных сечений можно определить по наибольшему сечению.
Как правило, вы не должны доводить температуру металла от комнатной до температуры выдержки за один шаг. Вместо этого медленно нагревайте металл чуть ниже температуры, при которой структура изменится, а затем держите его там до тех пор, пока температура не станет одинаковой по всему металлу. После этого «предварительного нагрева », вы можете быстро нагреть температуру до конечной температуры, которая вам потребуется. Чтобы предотвратить деформацию деталей более сложной конструкции, может потребоваться несколько слоев предварительного нагрева.
С. Стадия охлаждения
На этапе охлаждения вы захотите вернуть металлу комнатную температуру, но есть разные способы сделать это в зависимости от типа металла. Для этого может потребоваться охлаждающая среда, такая как газ, жидкость, твердое вещество или их комбинация. Скорость охлаждения определяется металлом и средой, используемой для охлаждения. В результате выбранные вами варианты охлаждения оказывают значительное влияние на желаемые свойства металла.
Закалка быстрое охлаждение металла на воздухе, в масле, воде, рассоле или другой среде. Большинство закаленных металлов быстро охлаждаются при закалке, поэтому закалка обычно связана с закалкой; однако закалка или другое быстрое охлаждение не всегда приводит к закалке. Медь, например, отжигают с помощью закалки в воде, а другие металлы закаляют с помощью медленного охлаждения.
Цель термической обработки
Однако они служат одной или нескольким из следующих целей:
- Повысить обрабатываемость
- Снять внутреннее напряжение.
- Улучшение механических свойств, таких как пластичность, прочность, твердость, ударная вязкость и т. д.
- Измените размер зерна.
- Повышение устойчивости к нагреву и коррозии.
- Изменить электрические и магнитные свойства.
- Изменить химический состав.
- Удалить газы
Преимущества термообработки
После термической обработки материалы:
- Более прочный продукт.
- Сталь становится жестче и прочнее.
- Легче сваривать.
- Становится более гибким.
- Повышает износостойкость.
- Увеличение общего срока службы детали.
Термическая обработка проводится по разным причинам. Некоторые процедуры смягчают металл, а другие затвердевают. Они также могут влиять на электрическую и тепловую проводимость этих материалов.
Некоторые методы термической обработки снимают напряжения, вызванные предыдущими процессами холодной обработки давлением. Другие придают металлам желаемые химические свойства. Выбор наилучшего метода в конечном итоге определяется типом металла и требуемыми свойствами.
В некоторых случаях металлическая деталь может подвергаться многократной термообработке. Например, некоторые суперсплавы, используемые в авиастроении, могут пройти до шести различных этапов термообработки, чтобы оптимизировать их для конкретного применения.
Типы процесса термообработки
Вышеупомянутым целям термической обработки может служить один или несколько из следующих процессов термической обработки:
<сильный>1. Отжиг
<сильный>2. Нормализация
3. Закалка
4. Закалка
5. Закалка корпуса:
а.) Науглероживание
б.) Цианирование
в.) Азотирование
6. Упрочнение поверхности
а.) Индукционная закалка
б.) Закалка пламенем
7. Диффузионное покрытие
1. Отжиг
Отжиг является одной из наиболее важных широко используемых операций при термической обработке стали.
Отжиг — это термическая обработка в металлургии и материаловедении, которая изменяет физические, а иногда и химические свойства материала, чтобы повысить его пластичность и уменьшить его твердость, что делает его более пригодным для обработки. Это влечет за собой нагрев материала выше его температуры рекристаллизации, поддержание этой температуры в течение соответствующего времени, а затем охлаждение.
Цель отжига заключается в получении одного или нескольких из следующих эффектов:
- Смягчить сталь.
- Улучшение обрабатываемости.
- Увеличить или восстановить пластичность и прочность.
- Снять внутреннее напряжение.
- Уменьшить или устранить структурную неоднородность.
- Уточнить размер зерна
- Подготовить сталь к последующей термообработке.
2. Нормализация
Нормализация это процесс термической обработки, используемый для придания металлу большей пластичности и прочности после его термической или механической закалки. Нормализация — это процесс нагревания материала до высокой температуры, а затем его охлаждения до комнатной температуры путем воздействия на него воздуха комнатной температуры после того, как он был нагрет. Этот нагрев и медленное охлаждение меняют микроструктуру металла, снижая его твердость и повышая пластичность.
Когда сталь холодная, структура деформируется, а металл может быть хрупким и ненадежным. Внутренняя структура горячедеформированной поковки также может быть искажена из-за обработки при очень низкой температуре. Также видно, что переменная температура отделки приводит к различной структуре поковок с одинаковым содержанием углерода. Точно так же, если отливка разливается при несколько неопределенной температуре и охлаждается с разной скоростью в разных частях, она может оказаться ненадежной. Поэтому нормализация используется, в частности, для следующих
Цель нормализации заключается в получении одного или нескольких из следующих эффектов:
- Для устранения крупнозернистой структуры.
- Для устранения внутренних напряжений, которые могли быть вызваны работой.
- Для улучшения механических свойств стали
Помимо всех этих целей, он может быть использован для повышения в определенной степени прочности среднеуглеродистых сталей (по сравнению с отожженными), для улучшения обрабатываемости низкоуглеродистых сталей, улучшения структуры сварных швов и т. д. Р>
3. Закалка
Операция закалки применяется ко всем инструментам и некоторым ответственным деталям машин, предназначенным для особо тяжелых условий эксплуатации, а также ко всем деталям машин из легированной стали.
Целями закалки с последующим отпуском являются:
<сильный>1. Развить высокую твердость, чтобы противостоять износу и позволить резать другие металлы.
2. Для повышения прочности, эластичности, пластичности и ударной вязкости.
Процесс состоит из:
1. Нагрев стали до температуры выше критической точки.
2. Выдерживание при этой температуре в течение значительного периода времени.
3. Закалка (быстрая смена) в ванне с водой, маслом или расплавленной солью.
4. Закалка
Закалка , в металлургии, процесс улучшения свойств металла, в частности стали, путем нагревания его до высокой температуры, но ниже точки плавления, и последующего охлаждения, обычно на воздухе. Процесс ужесточается за счет снижения хрупкости и внутренних напряжений.
Когда кусок стали вынимают из закалочной среды, как уже говорилось, он становится твердым, хрупким и, помимо других неблагоприятных характеристик, будет иметь серьезные неравномерно распределенные внутренние напряжения. Как правило, отпуск восстанавливает пластичность и снижает твердость, что приводит к некоторому снижению твердости. Таким образом, основными объектами закалки являются следующие:
- Для стабилизации структуры металла.
- Для уменьшения внутренних напряжений, возникающих при предыдущем нагреве.
- Для уменьшения твердости, возникающей при закалке, и повышения пластичности металла.
- Чтобы придать металлу восемь структурных условий в сочетании с ударной вязкостью и ударопрочностью.
Для закалки требуется:
- Повторный нагрев стали после закалки до температуры ниже точки Ac1 (линия psk на рис. 6.6).
- Удерживание бита в течение значительного времени.
- Медленное охлаждение. Желательно, чтобы температура стали поддерживалась не менее 4-5 минут на каждый миллиметр сечения.
5. Повышение безопасности
А. Науглероживание
Самый старый известный метод получения твердой поверхности стали — это цементация . или науглероживание . Сталь, используемая для этой цели, обычно представляет собой низкоуглеродистую сталь с содержанием углерода около 0,15%, которая не поддается заметной термообработке. В ходе процесса внешний слой превращается в высокоуглеродистую сталь с содержанием углерода от 0,9 до 1,2 %. Если он подвергнется надлежащей термической обработке, он будет иметь чрезвычайно твердую внешнюю поверхность и мягкую пластичную сердцевину.
Б. Цианирование
Цианирование представляет собой процесс получения твердой поверхности низкоуглеродистой или среднеуглеродистой стали путем погружения стали в ванну с расплавленной солью, содержащей цианид, поддерживаемую при температуре от 800°C до 900°C, и последующей закалки стали в воде или масле. Твердость, создаваемая этой обработкой, обусловлена присутствием соединений азота, а также углерода в поверхностном слое.
С. Азотирование
Азотирование это процесс получения твердого поверхностного слоя только на легированных сталях. Азотирование состоит в основном из нагрева стали в атмосфере газообразного аммиака при температуре от 500°C до 650°C без дальнейшей термической обработки. Аммиак диссоциирует, а образующийся азот соединяется с элементами в стали с образованием нитридов. Эти нитриды придают поверхности исключительную твердость. Твердый поверхностный слой обычно толщиной от 0,2 до 0,4 мм образуется за 50 часов.
Азотирование является последней операцией после формообразования и термической обработки. Таким образом, после подделки последовательность операций следующая:(a) закалка в масле при температуре от 850°C до 900°C, (b) отпуск от 600°C до 650°C, (c) черновая обработка, (d) стабилизация (для снятия внутренних напряжений) при температуре от 525°C до 550°C, (e) окончательная обработка и, наконец, (f) азотирование.
Азотирование используется на многих изнашиваемых деталях автомобилей, самолетов и дизельных двигателей, а также на многочисленных различных деталях, таких как валы насосов, датчики, волочильные штампы, шестерни, муфты и оправки. Его использование ограничено расходами, необходимыми для лечения, и полученным сравнительно тонким корпусом.
6. Упрочнение поверхности
А. Индукционная закалка
Введение Нагрев оказался удовлетворительным для многих операций поверхностной закалки, требуемых на опорных поверхностях коленчатых валов, распределительных валов, полуосей и подобных изнашиваемых поверхностей. Он отличается от обычной практики цементации тем, что состав поверхности стали не изменяется, а закалка осуществляется за счет чрезвычайно быстрого нагрева и закалки изнашиваемой поверхности, что не влияет на внутреннюю сердцевину. Твердость, полученная при индукционной закалке, такая же, как и при обычной обработке, и зависит от содержания углерода.
Б. Закалка пламенем
Процесс закалки стали путем ее нагревания пламенем кислородно-ацетиленовой горелки известен как закалка пламенем . который, как и процесс индукционной закалки, основан на быстром нагреве и закалке поверхности водой. Пламя направляется на нужную часть, не нагревая оставшуюся часть работы, чтобы эффективно воздействовать на нее. Преимущества в пользу его применения следующие:
- Поскольку он быстро нагревается, пламенный нагрев удобен, когда требуется твердость только на ограниченной глубине, а остальная часть сохраняет свою первоначальную прочность и пластичность.
- Нагрев пламенем позволяет и практично закалить часть или всю деталь, которая слишком велика или слишком неудобна для помещения в печь.
- Время, необходимое для нагрева, меньше при нагреве пламенем, чем при нагреве в печи.
7. Диффузионное покрытие
Диффузионное покрытие или металлическая фиксация , представляет собой процесс пропитки поверхности стали алюминием, хромом, кремнием, бором, бериллием и другими элементами.
Диффузионное покрытие осуществляется путем нагревания и выдерживания стальных деталей в непосредственном контакте с одним из вышеперечисленных элементов, который может находиться в твердом, жидком или газообразном состоянии. Этот процесс придает стали ряд ценных свойств, среди которых высокая жаростойкость, коррозионная стойкость и износостойкость. Во многих случаях сталь с диффузионным покрытием может использоваться вместо высоколегированной стали.
Векторная диаграмма
Каждый металлический сплав имеет свою фазовую диаграмму. Как указывалось ранее, термообработку проводят в соответствии с этими схемами. Они изображают структурные изменения, происходящие при различных температурах и химических составах.
Давайте возьмем в качестве примера фазовую диаграмму железо-углерод, потому что она наиболее известна и широко изучается в университетах.
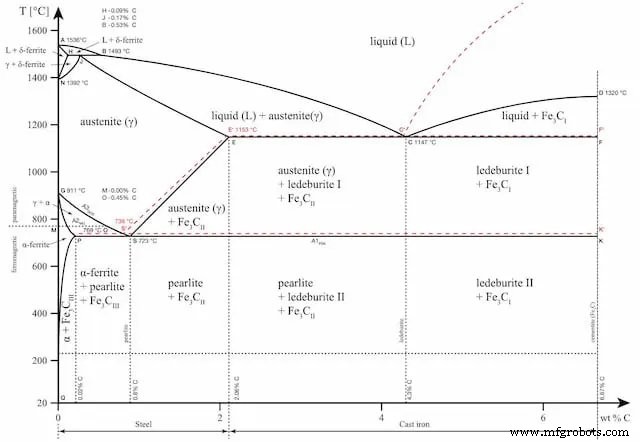
Фазовая диаграмма железо-углерод является полезным инструментом для изучения поведения при термической обработке различных углеродистых сталей. Ось x представляет содержание углерода в сплаве, а ось y представляет температуру.
Обратите внимание, что предел, при котором сталь становится чугуном, составляет 2,14 процента углерода.
На диаграмме показаны различные области, в которых металл может находиться в различных микросостояниях, таких как аустенит, цементит и перлит. Эти области обозначены границами A1, A2, A3 и Acm. Когда через эти интерфейсы проходит значение температуры или содержания углерода, происходят фазовые изменения.
- A1:Верхний предел фазы цементита/феррита.
- A2:предел, при котором железо теряет свой магнетизм. Температура, при которой металл теряет свой магнетизм, также называется температурой Кюри.
- A3:граница раздела, которая отделяет фазу аустенита + феррита от фазы γ (гамма) аустенита.
- Acm:граница раздела, отделяющая γ-аустенит от поля аустенита + цементита.
Фазовая диаграмма является важным инструментом для определения того, будет ли термическая обработка полезной. Каждая структура придает конечному продукту различные качества, и в соответствии с этим выбирается термообработка.
Этапы процесса термообработки
Проще говоря, термическая обработка — это процесс нагревания металла, выдержки его при этой температуре, а затем обратного охлаждения. В процессе металлическая деталь будет претерпевать изменения в своих механических свойствах. Это связано с тем, что высокая температура изменяет микроструктуру металла. А микроструктура играет важную роль в механических свойствах материала.
Окончательный результат зависит от множества различных факторов. К ним относятся время нагрева, время выдержки металлической детали при определенной температуре, скорость охлаждения, окружающие условия и т. д. Параметры зависят от метода термообработки, типа металла и размера детали.
В ходе этого процесса свойства металла будут меняться. Среди этих свойств — электрическое сопротивление, магнетизм, твердость, ударная вязкость, пластичность, хрупкость и коррозионная стойкость.
Отопление
- Металлические детали помещены в печь
- Детали реактивного двигателя отправляются в печь
- Как мы уже обсуждали, микроструктура сплавов будет изменяться во время термической обработки. Нагрев осуществляется по заданному тепловому профилю
- Сплав может находиться в одном из трех различных состояний при нагревании. Это может быть механическая смесь, твердый раствор или их комбинация.
- Механическая смесь аналогична бетонной смеси, в которой цемент связывает песок и гравий. Песок и гравий все еще видны как отдельные частицы. В металлических сплавах механическая смесь удерживается основным металлом.
- С другой стороны, в твердом растворе все компоненты гомогенно смешаны. Это означает, что их невозможно идентифицировать по отдельности даже под микроскопом.
- Каждое состояние приносит с собой разные качества. Возможно изменение состояния путем нагрева по фазовой диаграмме. Однако охлаждение определяет окончательный результат. Сплав может оказаться в одном из трех состояний, в зависимости исключительно от метода.
Удержание
- Во время выдержки или этапа замачивания , металл выдерживается при достигнутой температуре. Продолжительность зависит от требований.
- Например, поверхностное упрочнение требует только структурных изменений поверхности металла для повышения поверхностной твердости. В то же время другие методы нуждаются в единообразных свойствах. В этом случае период удержания больше.
- Время замачивания также зависит от типа материала и размера детали. Для более крупных деталей требуется больше времени, когда целью являются однородные свойства. Просто сердцевине большой детали требуется больше времени, чтобы достичь необходимой температуры.
Охлаждение
- После завершения этапа выдержки металл необходимо охладить в установленном порядке. На этом этапе также происходят структурные изменения. Твердый раствор при охлаждении может остаться прежним, полностью или частично превратиться в механическую смесь, в зависимости от различных факторов.
- Различные среды, такие как рассол, вода, масло или принудительный воздух, регулируют скорость охлаждения. Последовательность названных выше охлаждающих сред находится в порядке убывания эффективной скорости охлаждения. Рассол поглощает тепло быстрее всего, а воздух — медленнее.
- В процессе охлаждения также можно использовать печи. Контролируемая среда обеспечивает высокую точность, когда необходимо медленное охлаждение.
Какие металлы подходят для термической обработки?
Хотя черные металлы составляют большую часть термообработанных материалов, медь, магний, алюминий, никель, латунь и титановые сплавы также могут подвергаться термообработке.
Примерно 80% термообработанных металлов составляют различные марки стали. Чугун, нержавеющая сталь и различные марки инструментальной стали — это черные металлы, которые можно подвергать термической обработке.
Черные металлы обычно подвергаются таким процессам, как закалка, отжиг, нормализация, снятие напряжений, цементация, азотирование и отпуск.
Методы термической обработки, такие как отжиг, старение и закалка, используются для меди и медных сплавов.
Алюминий подходит для отжига, термообработки на твердый раствор, естественного и искусственного старения и других методов термообработки. Термическая обработка алюминия является точным процессом. Объем процесса должен быть установлен, и его необходимо тщательно контролировать на каждом этапе, чтобы гарантировать достижение желаемых характеристик.
Очевидно, что не все материалы пригодны для различных видов термической обработки. Точно так же один материал может не принести пользы от всех методов. В результате каждый материал следует изучать отдельно, чтобы добиться желаемого результата. Отправной точкой является использование фазовых диаграмм и доступной информации об эффектах вышеупомянутых методов.
Термообработка сталей
Термическая обработка стали – это нагрев и охлаждение металлов с целью изменения их физико-механических свойств без изменения их формы. Термическая обработка — это метод упрочнения материалов, но ее также можно использовать для изменения механических свойств, таких как формуемость, механическая обработка и т. д.
Чаще всего применяется в металлургии, но термическая обработка металлов также может использоваться при производстве стекла, алюминия, стали и множества других материалов.
Мы постарались охватить все аспекты термической обработки, начиная с того, что представляет собой процесс термической обработки, затем типы процессов термической обработки, включая такие методы, как отжиг, цементация, отпуск, нормализация и многие другие. Мы также обсудили преимущества и недостатки процесса термообработки.
Если вам понравилась статья, пожалуйста, поделитесь ею с друзьями.
Промышленные технологии
- Что такое сглаживание? 6 различных типов и методов
- Что такое штамповка? - Типы, операции и применение
- Что такое кастинг? - Определение| Виды литья
- Что такое ковка? - определение, процесс и типы
- Что такое металлизация? - Определение, типы и преимущества
- Что такое гальванизация? - определение, методы, процесс
- Что такое термическая обработка? - Процесс и методы
- Что такое литье металлов? - определение, типы и процесс
- Что такое номер плавки?
- Процесс термообработки металлических деталей с ЧПУ