Вагранка – детали, принцип работы, применение
В этой статье мы поговорим о вагранке, частях вагранки, схеме вагранки, зонах в вагранке, работе вагранки.
Основная цель в вагранке производить железо желаемого состава, температуры и свойств по требуемой ставке наиболее экономичным способом. Кроме того, у этой печи есть много явных преимуществ перед другими типами, например, простота в эксплуатации , непрерывность производства и увеличение производительности в сочетании с высокой степенью эффективности.
В разных литейных цехах используются различные типы плавильных печей в зависимости от количества металла, которое необходимо плавить за один раз, и характера работ, выполняемых в цехе. Только вагранка используется в литейных цехах для плавки рафинированного чугуна вместе с ломом, описан ниже.
Детали вагранки
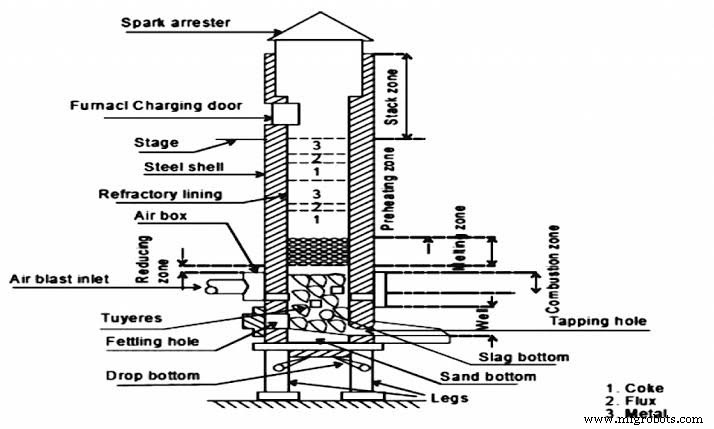
Вагранка состоит из вертикального цилиндрического стального листа толщиной от 6 до 12 мм, футерованного внутри кислотоупорным кирпичом или кислотой. трамбовочная глина. Используемые огнеупорные кирпичи или глина для трамбовки состоят из оксида кремния. кислота (SiO2) и глинозем (Al2O3). Футеровка обычно толще в нижней части, где температура выше, чем в верхней части.
Оболочка монтируется либо на кирпичный фундамент, либо на стальные колонны. В конструкции стальной колонны, используемой на большинстве современных вагранок, днище обечайки снабжено откидными дверцами, через которые в конце плавки может быть выгружен мусор, состоящий из кокса, шлака и т. д. В вагранках с откидным дном рабочее дно засыпается формовочной смесью, которая покрывает откидные створки.
Это дно наклонено к металлическому выпускному отверстию, расположенному в самой нижней точке в передней части купола. Наоборот это кран , а несколько выше него находится еще одно отверстие, называемое шлаковым отверстием. , что позволяет удалить шлак.
Постоянный объем воздуха для горения получают от моторизованного вентилятора. Воздух проходит от нагнетателя через трубу, называемую ветровой трубой (впускное отверстие для подачи воздуха), сначала в круглую рубашку вокруг корпуса, называемую ветровая коробка . а затем в печь через ряд отверстий, называемых фурмами. которые предусмотрены на высоте от 450 до 500 мм над рабочим днищем или ложем вагранки.
Эти фурмы обычно их 4, 6 или 8 в зависимости от размера купола, и они могут быть установлены в один или несколько рядов. Общая площадь фурм должна составлять от одной пятой до одной шестой площади поперечного сечения вагранки внутри футеровки на уровне фурм. Обычно фурмы имеют размер 50×150 мм или 100×300 мм. Иногда для повышения эффективности плавки предусмотрены вспомогательные фурмы.
В дутьевой трубе предусмотрен клапан для регулирования подачи воздуха. В зависимости от размеров вагранки, вида выплавляемого чугуна и плотности шихты напор воздуха может составлять от 250 мм до 400 мм вод. ст. для малых и средних печей и от 400 мм до 850 мм вод. ст. печь больших размеров.
Иногда устанавливают измеритель объема, чтобы узнать объем проходящего воздуха. Количество воздуха, необходимое для плавки одной тонны чугуна, зависит от качества кокса и соотношения кокса и железа. Многолетняя практика показывает, что для плавки одной тонны железа в вагранке при соотношении железа к коксу 10:1 требуется около 800—900 м3 воздуха. Для более низкого соотношения потребуются большие объемы воздуха.
Предусмотрена загрузочная дверца, через которую в печь подаются металл, кокс и флюс, расположенная на высоте от 3 до 6 м над фурмами, в зависимости от размера вагранки. Большая площадка или сцена обычно окружает купол на уровне около 300 мм ниже низа загрузочного люка.
Оболочка обычно продолжается от 4,5 до 6 м над загрузочным люком, образуя дымоход. В верхней части печи конический колпачок, называемый искрогасителем, предотвращает выход искры наружу. Задержанная искра охлаждает искры и позволяет дыму выходить из отверстия. Иногда вагранка может быть снабжена коллектором, слесарем и осадителем, чтобы свести к минимуму загрязнение атмосферы.
Зоны в вагранке
На основе реакций горения весь ствол вагранки можно разделить следующим образом:
Зона тигля :- Он находится между верхней частью песчаного слоя и нижней частью фурм. Здесь скапливается расплавленное железо. Это также называется колодцем. или очаг .
Зона горения или окисления:- Обычно он расположен от 150 до 300 мм. над вершиной из фурм. Весь кислород воздушного дутья расходуется здесь за счет фактического горения, происходящего в этой зоне. При этом выделяется много тепла, которое отсюда поступает в другие зоны.
Тепло также выделяется из-за окисления кремния и марганца. Благодаря этому высокому нагреву, температура которого составляет 1550—1850°С, расплавленные капли чугуна стекают в горн. В этой зоне происходят химические реакции:
C + O2 —–> CO2 + тепло
Si + O2 —–> SiO2 + тепло
2 Mn + O2 —–> 2 MnO2 + тепло
Редукционная зона :- Он простирается от верхней части зоны горения до верхней части коксового слоя. В этой зоне происходит восстановление СО2 до СО и температура в коксовом слое падает примерно до 1200°С. За счет восстановительной атмосферы шихта защищена от любого окислительного воздействия. В этой зоне протекает реакция:
CO2 + C (кокс) —-> 2 CO-тепло
Зона плавления:- Он начинается от первого слоя металлошихты над коксовым слоем и простирается до высоты 900 мм. В этой зоне развивается самая высокая температура для полного сгорания кокса и, таким образом, здесь расплавляется железо. Температура в этой зоне составляет около 1600°С. В этой зоне также происходит значительное поглощение углерода расплавленным металлом в соответствии со следующими реакциями:
3 Fe + 2 CO—–> Fe3C + CO2
Зона предварительного нагрева или зона зарядки :- Он начинается над зоной плавления и доходит до нижней части загрузочной дверцы. Зона предварительного нагрева содержит ваграночную шихту в виде чередующихся слоев кокса, флюса и металла, где они предварительно нагреваются до температуры около 1100°С перед поступлением в зону плавки.
Зона стека :- Зона дымовой трубы простирается от зоны предварительного нагрева до вершины вагранки. Он уносит газы, образующиеся в печи, в атмосферу.
Вместимость вагранки
Производительность вагранки определяется как тонны расплавленного металла, получаемого за час плавки. Производительность (размеры) вагранки варьируется от 1 до 15 тонн (и более) выплавляемого чугуна в час. Размер зависит не только от площади поперечного сечения вагранки, но и от интенсивности расхода кокса.
Но интенсивность потребления кокаина подразумеваются тонны кокса, сжигаемые на 1 кв. м площади поперечного сечения вагранки в единицу времени. Замечено, что при площади купола 14 см в плане сжигается около 1 кг кокса в час. Диаметр купола колеблется от 1 до 2 м при высоте от 3 до 5 раз больше диаметра.
Вагранка работает
Различные этапы работы вагранки:
<сильный>1. Подготовка купола
Первой операцией при подготовке вагранки является удаление шлака. и отходы на футеровке и вокруг фурм от предыдущего запуска. Любые дефекты или битые кирпичи ремонтируются смесью огнеупорной глины и кварцевого песка или ганистером. Подготовку песчаного дна в куполе начинают сразу после завершения ямочного ремонта футеровки.
Нижние двери поднимаются и удерживаются в этом положении металлическими подпорками. Донный песок вводится через загрузочный люк и хорошо утрамбовывается вокруг футеровки и пересечения донных люков. Этот слой песка насыпается на высоту от 100 до 200 мм над чугунной дверью.
Поверхность песчаного дна наклонена со всех сторон в сторону выпускного отверстия, так что расплавленный металл может быть полностью слит из вагранки в любое время. Для удаления шлака предусмотрено отверстие диаметром около 35 мм, а летка сформирована вокруг деревянного шаблона диаметром около 20 мм. Перед обжигом вагранка должна быть тщательно высушена.
2. Стрельба из башенки
При растопке вагранки на песчаном дне зажигается огонь из растопочных дров. Это должно быть сделано за 2,5-3 часа до того, как потребуется расплавленный металл. Поверх раскаленных дров сооружается слой кокса. Когда дрова хорошо прогорят, кокс сбрасывают в колодец сверху несколькими порциями, следя за тем, чтобы и кокс начал гореть.
Кокс добавляют до уровня немного выше фурм и включают подачу воздуха с меньшей, чем обычно, скоростью продувки для воспламенения кокса. Как только над слоем топлива начинают появляться красные пятна, в вагранку вводят дополнительный кокс до высоты 700-800 мм над верхним рядом фурм.
Слой кокса должен быть полностью прогрет, прежде чем он будет доведен до окончательной высоты. Высота коксового слоя определяется с помощью измерительного стержня, предназначенного для определения расстояния от порога загрузочного люка до верха коксового слоя. Слой кокса, лежащий на песчаном дне перед началом плавки, называется пластовой шихтой. Количество кокса в слое зависит от давления воздуха, подаваемого в вагранку.
Высота загрузки слоя или коксового слоя очень важна для работы вагранки; он влияет на температуру, скорость плавления и химический состав. При прочих равных условиях низкий слой будет давать более холодный металл, чем высокий.
3. Зарядка вагранки
Как только коксовый слой будет доведен до нужной высоты и воспламенится равномерно по всему объему, из загрузочного люка загружаются чередующиеся слои чугуна, кокса и флюса (известняка) до тех пор, пока вагранка не будет заполнена. Подходящий лом также добавляется вместе с чугуном для контроля химического состава производимого чугуна. Доля этого лома обычно составляет от 25 до 50% от общего веса разливаемого металла.
При использовании наряду с чугуном значительных объемов стального лома в качестве раскислителя используется небольшое количество, скажем, от 2 до 4% ферромарганца. Масса металлошихты должна составлять от 10 до 15% часовой производительности вагранки. Целью добавления флюса является удаление примесей из железа и защита железа от окисления, снижение температуры плавления шлака и повышение его текучести для облегчения утилизации. Кроме известняка, в качестве флюса иногда используют плавиковый шпат и кальцинированную соду.
Требуемое количество известняка может составлять от 30 до 40 кг на тонну выплавленного чугуна или 25% веса загружаемого кокса. Соотношение выплавляемого металла и загружаемого кокса зависит от множества факторов. Поэтому невозможно дать определенные рекомендации по этому соотношению, которое может быть достигнуто на разных классах работ. Таблица 11.11 дана только в качестве руководства и показывает хорошую среднюю практику в отрасли. Чаще его соблюдают в соотношении 10:1. Это означает, что для плавки 10 тонн чугуна требуется 1 тонна кокса.
4. Замачивание железа
После того, как вагранка будет полностью заряжена до загрузочного люка, шихта должна пропитаться теплом около 45 минут. Заряд медленно нагревается, так как скорость продувки воздуха в это время поддерживается ниже нормальной (практически закрытой). Это приводит к намоканию железа.
5. Взрыв воздуха
По окончании периода замачивания включается полный поток. Перед включением дутья фурменные отверстия и выпускное отверстие держат закрытыми. Через несколько минут после дутья, скажем, около 10 минут, расплавленный металл начинает накапливаться в горне. Когда металл в вагранке начнет плавиться, скорость загрузки должна быть равна скорости плавки, чтобы печь оставалась полной в течение всей плавки. По окончании плавки загрузку прекращают, но дутье продолжают до расплавления всего металла.
6. Выстукивание и зашлаковывание
Первое вскрытие можно производить через 40-50 минут после включения полной продувки воздухом. За это время в очаге над песчаной подушкой собирается достаточное количество металла. Когда шлак накапливается в колодце, отверстие для шлака открывается, и шлак стекает, предпочтительно в тележку для легкого удаления. Расплавленный металл собирается в ковши и подается в изложницы для заливки. Та же процедура повторяется до тех пор, пока весь металл не расплавится и операция не закончится.
7. Закрытие купола
По окончании операции подачу газа прекращают, а подпорку под нижней дверью сбивают так, что нижние плиты распахиваются. Это позволяет остаткам купола падать на пол или в ведро. Затем их закаливают и удаляют из-под купола.
Как правило, вагранки работают непрерывно, как и доменные печи, но работают только в течение тех периодов, которые могут потребоваться. На многих литейных заводах период плавки не превышает 4 часов, но вагранки могут работать непрерывно 10 часов и более.
КПД вагранки
Термическая или плавильная эффективность вагранки в процентах выражается как:
(Тепло, используемое при предварительном нагреве, плавлении и перегреве) / (Потенциальное тепло в коксе + тепло от окисления Fe, Si, Mn + тепло в воздушном дутье) x 100
КПД вагранки колеблется от 30 до 50 процентов в зависимости от
1. Расход кокса или коксовое отношение, выраженное как обратное соотношение металла и топлива в процентах,
2. Скорость взрыва и
3. Средний размер кокса.
Требования к воздуху для вагранки
Для полного сгорания топлива в вагранке требуется около 8,4 м3 воздуха на 1 кг кокса при нормальном атмосферном давлении и температуре. При соотношении шрота к коксу шихты 10:1, что считается удовлетворительным показателем, расход кокса на тонну чугуна составит 1000/10 кг, т. е. 100 кг. Таким образом, объем воздуха, необходимый на тонну расплава, составляет>
8,4 х 100 =840 м3.
Чтобы обеспечить утечку и т. д., подаваемого воздуха обычно немного больше, т. е. около 900 м3 на тонну железа.
Размеры вагранки
Главные размеры купола выбираются на основе эмпирических данных. Таким образом, площадь поперечного сечения вагранки А. зависит от расчетной часовой производительности и определяется по формуле
A =π d^2/4 =Q/Q1 м^2
Где d — диаметр вагранки в свету, м, Q — расчетная производительность вагранки, т/ч, Q2 — удельная производительность на м2 площади поперечного сечения, т/ч. Как правило, Q1 =от 6 до 8 тонн в час.
Полезная высота вагранки (расстояние от оси основных фурм до нижней кромки загрузочного отверстия) зависит от диаметра и рассчитывается по соотношению Н :d =от 3 до 5.
Высота вагранки напрямую влияет на скорость плавки , расход топлива и температура и качество расплавленного металла . Если она слишком высока, кокс может раздробиться при падении загрузки; если она слишком низкая, то металл недостаточно прогревается, уменьшается тяга и снижается производительность вагранки.
Внутренний диаметр вагранки определяет количество потребляемого кокса и количество железа расплавлено в единицу времени. Выяснилось, что 14 см? площади вагранки сжигает около 1 кг кокса в час. Таким образом, для вагранки производительностью 3 тонны в час потребуется (3×100) или 300 кг кокса в час при соотношении металла и топлива 10:1. Таким образом, площадь купола будет равна (14×300) или 4200 см². Тогда внутренний диаметр будет
Квадратные корни из (4200×4)/π
=73 см (приблизительно)
Загрузка вагранки
Если желательны продукты однородного качества, следует уделить особое внимание загрузке вагранки. Обычно литейщику доступны несколько марок чугуна и лома. Для достижения желаемого состава литого металла эти марки необходимо регулировать и контролировать. Так как различные элементы в металле претерпевают химические изменения во время операции переплавки, необходимо учитывать их потери или прибавления при изготовлении шихты. Потеря или усиление различных элементов выглядит следующим образом.
<сильный>1. Углерод: Расплавленный металл поглощает углерод, проходя через раскаленный кокс, образующий слой. При правильном контроле условий плавления можно ожидать выигрыша в 0,15%. В то время как содержание углерода в металле увеличивается из-за поглощения углерода коксом, он немного теряется из-за окисления.
<сильный>2. Кремний: Кремний терпит некоторые потери из-за окисления, когда капли расплавленного железа стекают по фурмам. Потери могут составлять 10% кремния, присутствующего в шихте.
<сильный>3. Марганец: Марганец также имеет тенденцию теряться вместе с кремнием при плавлении. Потери могут составлять от 15 до 20% марганца, присутствующего в шихте.
<сильный>4. Сера: Сера извлекается из кокса, металлолома, флюса и т. д. Обычно предполагается, что прирост содержания серы составляет от 0,03 до 0,05%.
<сильный>
5. Фосфор: В содержании фосфора практически нет ни потерь, ни прибавок.
<сильный>6. Железо: Само железо также имеет тенденцию окисляться и теряться, но потери, которые весьма малы, можно предположить, что они составляют от 3 до 4 процентов.
Это было все о вагранке, ее зонах, операциях и деталях. Надеюсь, вам понравилась статья. Оставьте свой отзыв в комментариях ниже.
Промышленные технологии
- Датчик положения дроссельной заслонки - принцип работы и применение
- Датчик RVG - принцип работы и его приложения
- Датчик пульса:принцип работы и его применение
- Принцип работы датчика RTD и его применение
- Что такое 3D-печать? Принцип работы | Типы | Приложения
- Вагранка:принцип, конструкция, работа, преимущества, недостатки и применение
- Абразивно-струйная обработка – детали, принцип работы, применение
- Гидроабразивная обработка – принцип работы, области применения, преимущества
- Техническое описание Hc06:знакомство с выводами, функциями, приложениями и принципом работы
- Принцип работы процесса литья под давлением и его применение