Станок для резки пенопласта с ЧПУ Arduino
<основной класс="главный сайт" id="главный">
В этом уроке мы узнаем, как построить станок для резки пенопласта с ЧПУ на Arduino. Это типичный станок с ЧПУ, сделанный своими руками, потому что он сделан из простых и дешевых материалов, некоторых напечатанных на 3D-принтере деталей и имеет Arduino в качестве контроллера.
Вы можете посмотреть следующее видео или прочитать письменное руководство ниже.
Обзор
Вместо бит или лазеров основным инструментом этой машины является горячая проволока или специальный тип резистивной проволоки, которая сильно нагревается, когда через нее проходит ток. Горячая проволока плавит или испаряет пену при прохождении через нее, поэтому мы можем точно и легко получить любую желаемую форму.

Я сказал легко, потому что построить станок с ЧПУ на самом деле не так уж и сложно. Если вы новичок и думаете о создании своего первого станка с ЧПУ своими руками, просто следите за обновлениями, потому что я объясню, как все работает. Я покажу вам весь процесс ее создания, начиная с проектирования машины, подключения электронных компонентов, программирования Arduino, а также объясню, как подготовить ваши формы, создать G-коды и управлять машиной с помощью бесплатных программ с открытым исходным кодом. Итак, давайте углубимся в это.
3D-модель станка для резки пенопласта с ЧПУ Arduino
Для начала вот 3D модель этой машины. Вы можете скачать и 3D-модель ниже.
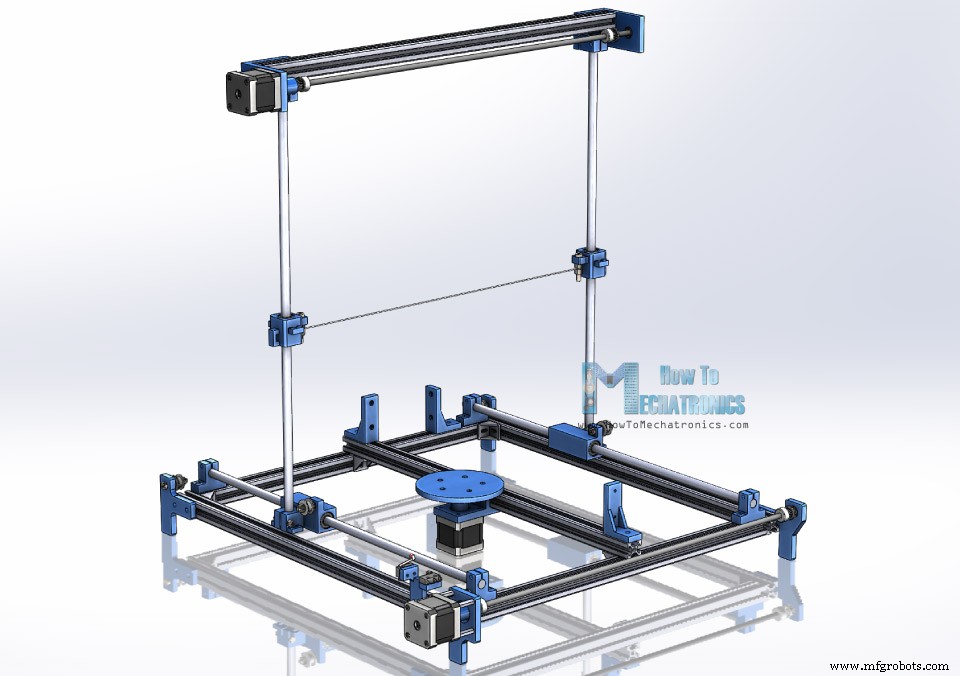
Вы можете найти и скачать эту 3D-модель, а также изучить ее в своем браузере на Thangs.
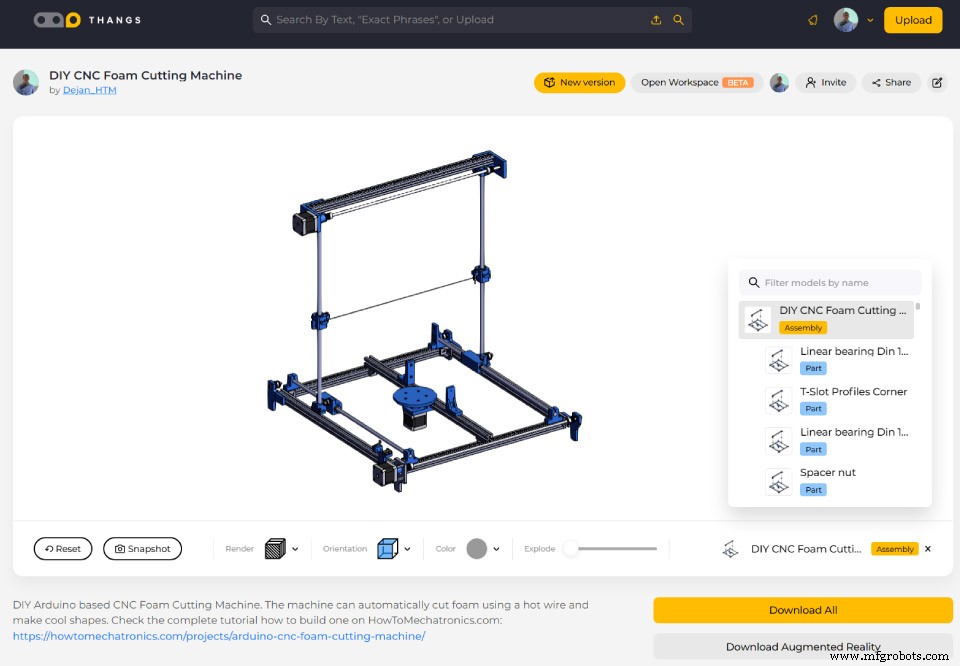
Загрузите 3D-модель сборки на Thangs.
Файлы STL для 3D-печати:
Базовая конструкция изготовлена из алюминиевых профилей с Т-образными пазами 20x20 мм. Я выбрал эти профили, потому что они просты в использовании, нам не нужно сверлить какие-либо отверстия или что-то еще при сборке, а также они многоразовые, мы можем легко разобрать и использовать их для других проектов. Движение каждой оси достигается с помощью линейных подшипников, скользящих по 10-миллиметровым гладким стержням. Я использовал по два стержня для каждой оси.
Выдвижные блоки могут выглядеть немного странно, но они спроектированы таким образом, что их можно легко распечатать на 3D-принтере как единую деталь, выполняя несколько функций. Так, например, на скользящем блоке X размещены два линейных подшипника, он удерживает стержень оси Y, удерживает шкив для ремня оси Y, а также имеет ручки для крепления ремня оси X.
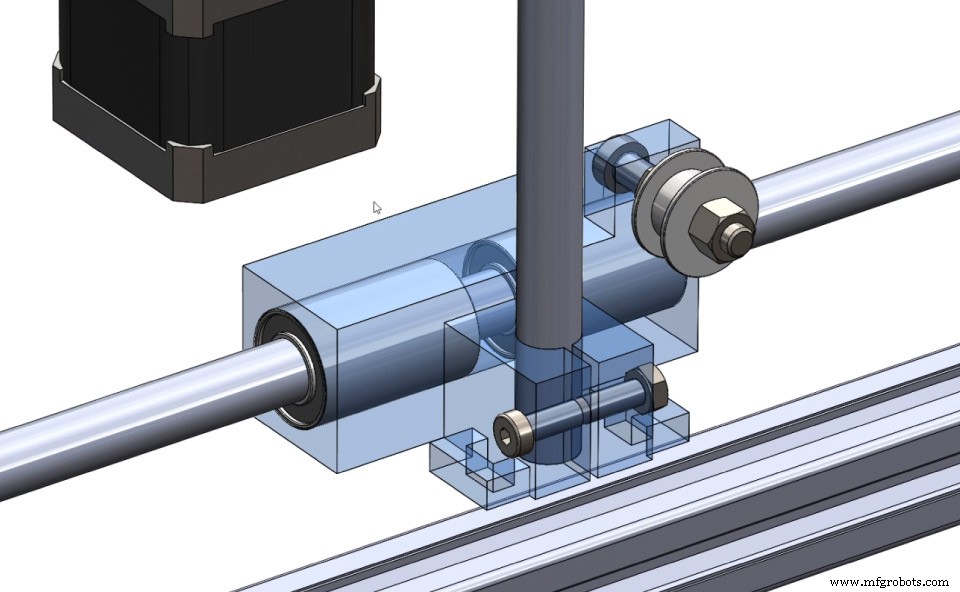
Для привода скользящих блоков мы используем шаговые двигатели NEMA 17. С помощью муфты вала, простого стержня с резьбой, двух шкивов и двух ремней мы можем одновременно равномерно приводить в движение два скользящих блока на каждой направляющей.
Здесь мы также можем заметить, что у нас есть третий шаговый двигатель, который позволяет машине создавать 2,5D-формы, и мы объясним, как это работает, чуть позже в видео.
В целом, с точки зрения конструкции и жесткости конструкция, вероятно, не так уж хороша, но я хотел сделать функциональную машину с минимальным количеством деталей, чтобы при этом выполнять свою работу.
Для 3D-печати деталей я использовал свой 3D-принтер Creality CR-10, действительно хороший 3D-принтер по разумной цене.
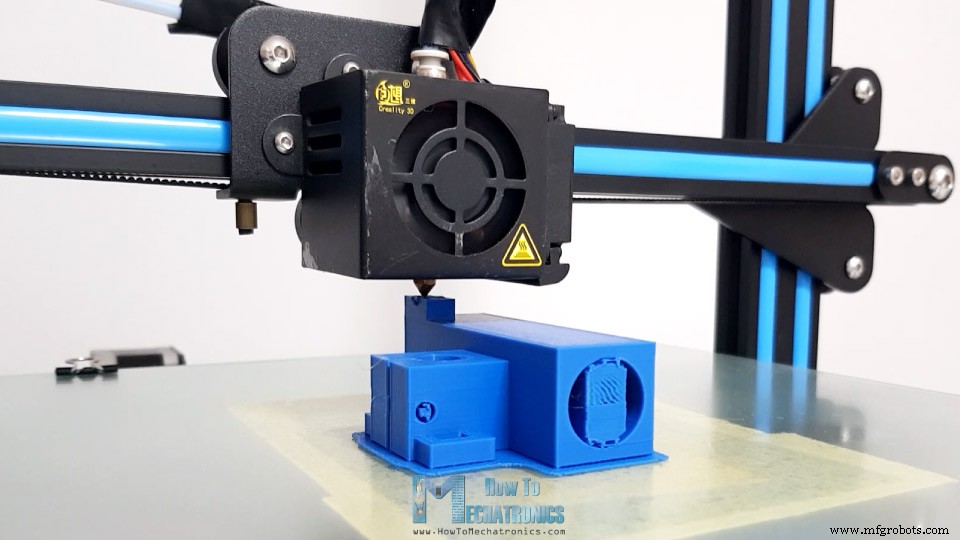
Обратите внимание, что некоторые детали, напечатанные на 3D-принтере, нуждаются в постобработке или перед использованием необходимо удалить вспомогательный материал.
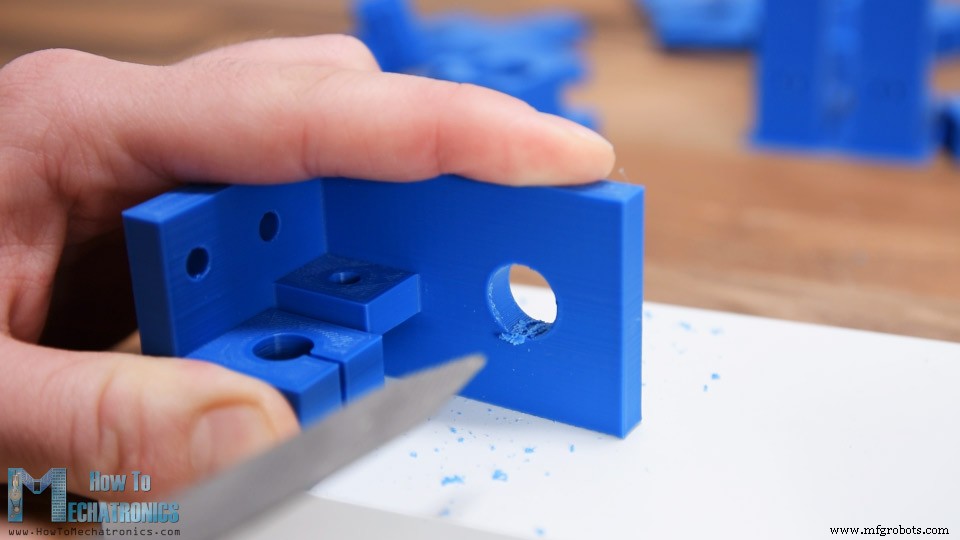
В некоторых случаях мне также приходилось использовать рашпиль для удаления лишнего материала, я думаю, из-за плохих настроек поддержки в программном обеспечении для нарезки.
Сборка ЧПУ
В любом случае, теперь у меня есть все материалы, и я могу приступить к сборке машины.
Вот список всех основных компонентов, используемых в этом станке с ЧПУ. Список компонентов электроники можно найти ниже в разделе, посвященном принципиальным схемам статьи.
- 6x 20x20 мм 500 мм алюминиевых профилей с Т-образными пазами…. Амазонка / Бангуд / AliExpress
- 4 стержня линейных направляющих 10 мм ………………….. Amazon / Бангуд / AliExpress
- 6 угловых кронштейнов с Т-образными пазами ………….. Amazon / Бангуд / AliExpress
- 50 гаек M5 для профилей с Т-образными пазами………………. Амазонка / Бангуд / AliExpress
- 6 линейных подшипников 10 мм ……………………… Amazon / Бангуд / AliExpress
- Ремень GT2 + зубчатый шкив + натяжной шкив …. Амазонка / + Натяжной шкив
- 2 подшипника 5x16x5 мм ……………………….. Amazon / Бангуд / AliExpress ….. Примечание. В видео я использую 6-миллиметровый подшипник, а также резьбовой стержень и шкивы GT2. Здесь я предлагаю использовать 5 мм, потому что эти размеры более распространены и их легко найти. Поэтому в загружаемые файлы STL я также включил две версии соединителей валов и монтажных кронштейнов, соответствующих этим размерам. Поэтому обязательно учитывайте это при 3D-печати этих деталей.
- Распорные гайки ………………………………… / Banggood / AliExpress
- Набор весеннего ассортимента……………….. Amazon / Бангуд / AliExpress
- Горячая проволока …………………………………………. Амазонка / AliExpress
- 2 резьбовых стержня по 50 см или любой стержень диаметром 6 или 5 мм в зависимости от внутреннего диаметра шкива.
- Болты и гайки из местного хозяйственного магазина:M3x30x8, M4x25x4, M4x30x4, M5x10/12x40, M5x15x8, M5x25x4, M5x30x4.
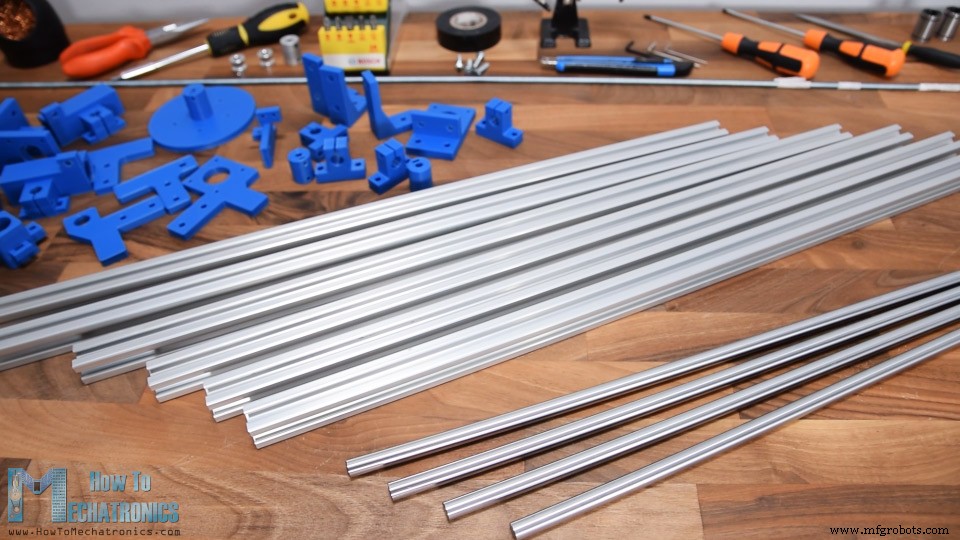
У меня были алюминиевые профили с Т-образными пазами длиной 60 см, поэтому, согласно 3D-модели, я обрезал каждый из них по размеру с помощью ручной пилы по металлу. Затем, используя угловые кронштейны, я собрал базовую раму. Далее я устанавливаю защелки вала для оси X. Видите ли, работать с профилями с Т-образными пазами так просто, нам просто нужны болты М5 и гайки с Т-образными пазами для крепления к ним всевозможных вещей.
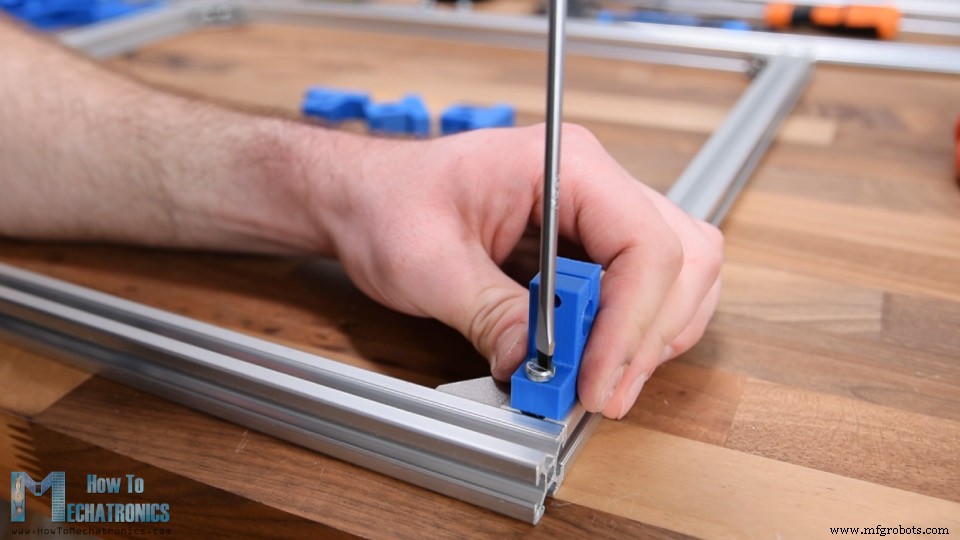
Затем я вставляю стержень вала через зажимы. Пока вставлена половина, нам также нужно добавить скользящий блок оси X. Мы просто помещаем в него два подшипника, а затем вставляем их на вал. Теперь мы можем вставить вал на другую сторону и с помощью болта M4 и гайки закрепить вал на месте. Я повторил этот процесс и для другой стороны.
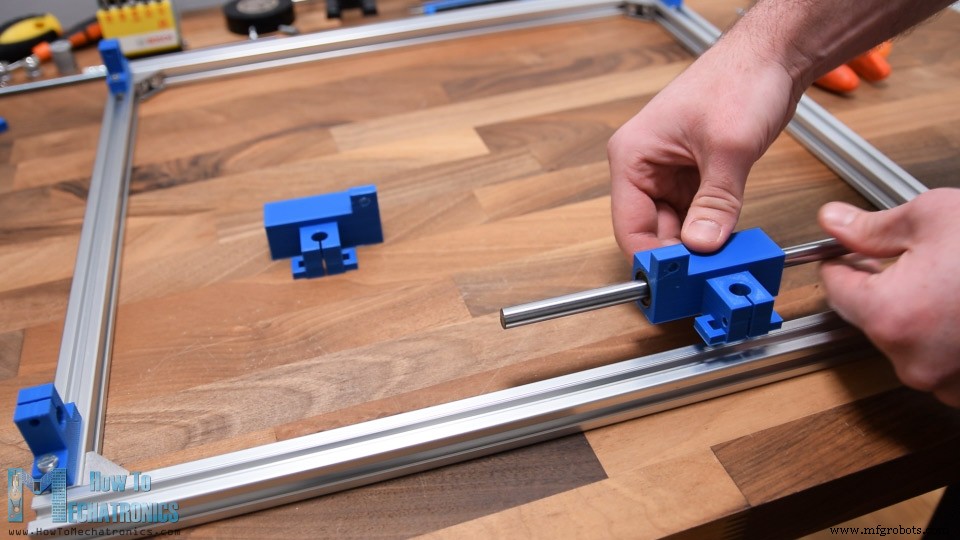
Далее нам нужно установить оси Y. Для этого сначала нам нужно вставить стержни в скользящие блоки оси X, расположить их заподлицо с нижней частью детали и закрепить с помощью гаек и болтов M4. Затем мы можем вставить скользящие блоки оси Y. В этих скользящих блоках используется только один линейный подшипник.
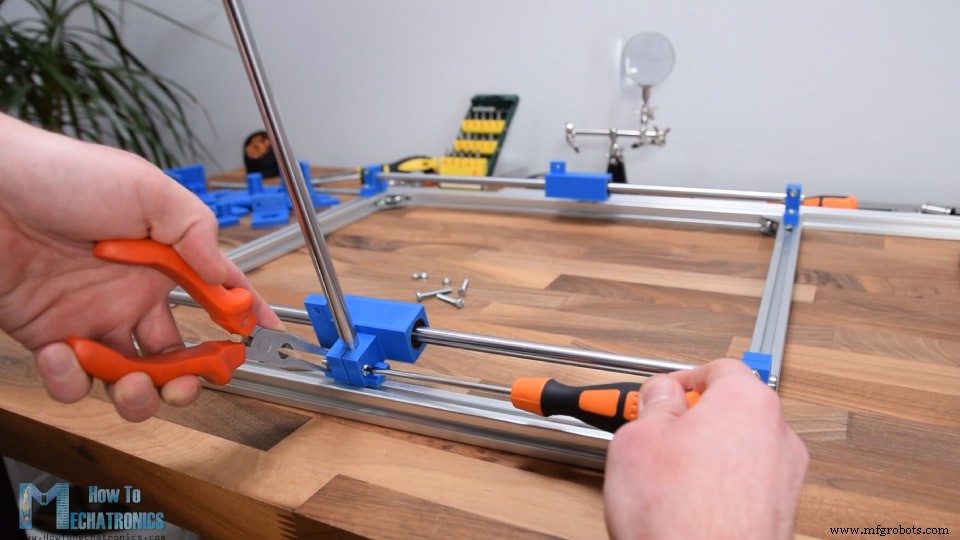
Поверх стержней оси Y нам нужно прикрепить монтажные кронштейны, которые будут соединять два стержня оси Y с профилем с Т-образным пазом сверху. Опять же, мы используем тот же метод для крепления их к стержням. Для крепления профиля с Т-образным пазом к монтажным кронштейнам я сначала добавил на них 3 болта М5 и гайки с Т-образным пазом. Затем я просто вставил профиль и закрепил болтами.
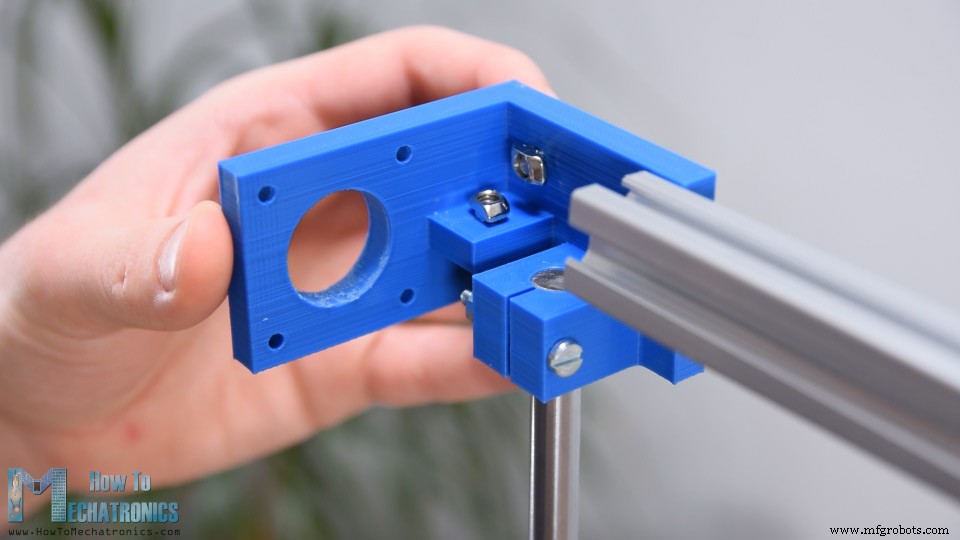
Итак, у нас построена основная конструкция, и мы можем свободно перемещаться как по оси X, так и по оси Y.
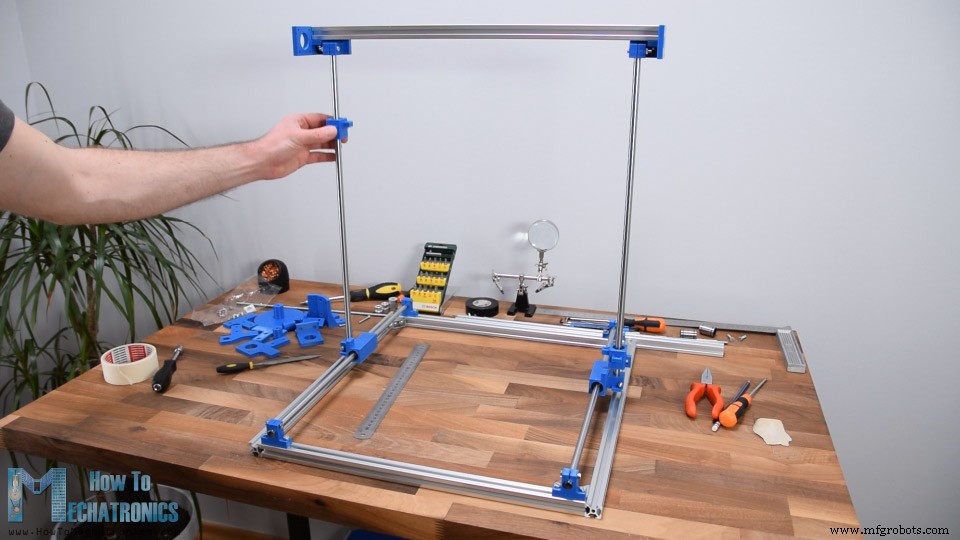
Далее я прикрепляю ножки к базовой раме. Опять же, это так просто сделать, используя профили с Т-образными пазами. Как только ножки будут закреплены, я собираюсь вставить первый шаговый двигатель для оси X. В этом случае я использую 20-миллиметровые прокладочные гайки, чтобы отдалить вал двигателя, чтобы позже я мог разместить ременный шкив рядом с опорой.
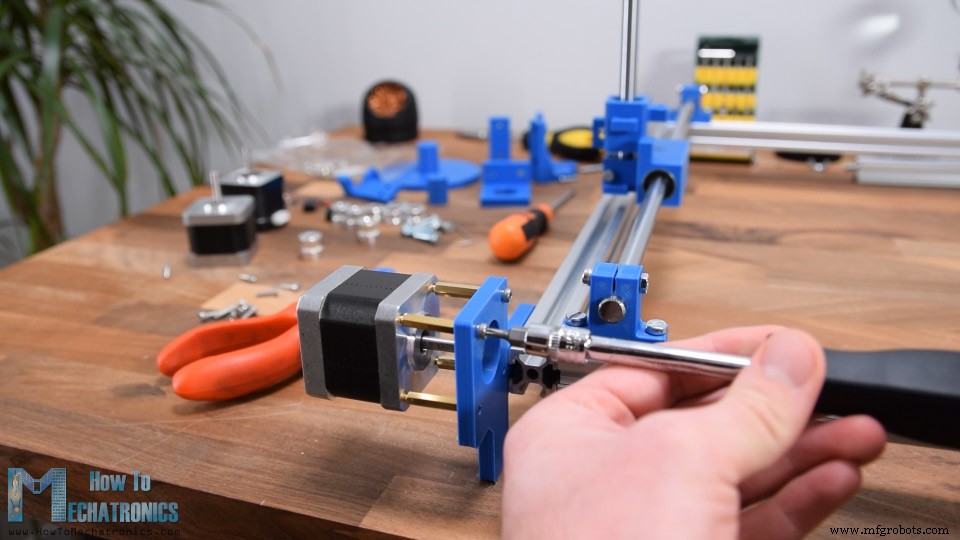
Итак, теперь у меня есть простой стержень с резьбой 6 мм, который будет приводить в движение два ремня одновременно. Поэтому сначала я обрезал его по размеру, поместил подшипник с внутренним диаметром 6 мм на противоположную ногу шагового двигателя и пропустил через него стержень с резьбой. Затем вставил гайку для крепления штока к подшипнику и два зубчатых шкива для ремней.
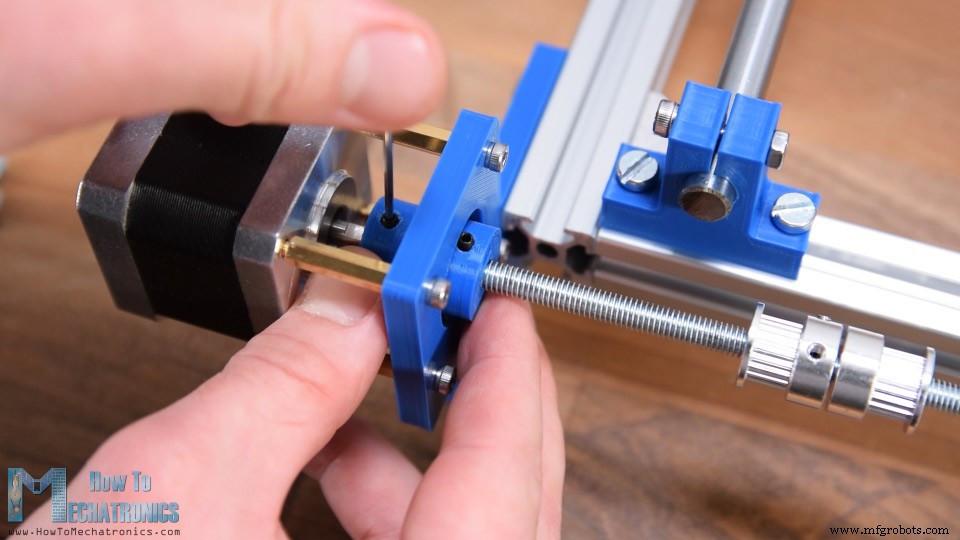
Для соединения резьбового стержня с шаговыми двигателями я напечатал на 3D-принтере муфту вала с отверстием 5 мм на стороне шагового двигателя и отверстием 6 мм на стороне стержня. Соединитель вала имеет прорези для вставки гаек M3, а затем, используя болты M3 или винты с резьбой, мы можем легко прикрепить его к валу двигателя и резьбовому стержню. Затем нам нужно расположить шкивы на одной линии с ручками выдвижных блоков, а также закрепить их установочными винтами.
На противоположной стороне машины мы можем вставить два натяжных ролика. Для этой цели я использовал несколько болтов и гаек M5.
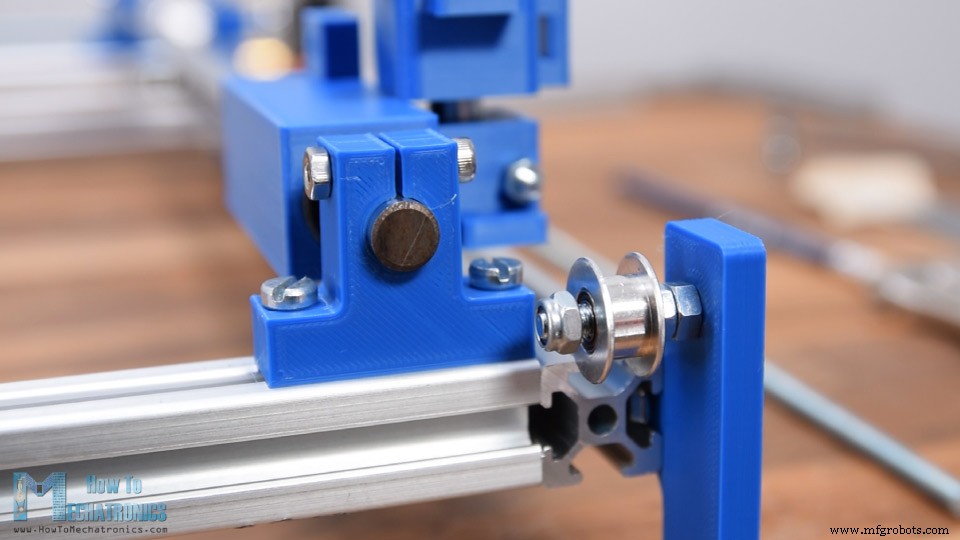
Итак, теперь мы готовы установить ремни GT2 для оси X. Сначала я вставил и закрепил ремень на выдвижном блоке с помощью стяжки. Затем я пропустил ремень вокруг зубчатого шкива, с другой стороны вокруг натяжного шкива, обрезал его до нужного размера и снова закрепил с другой стороны скользящего блока стяжкой.
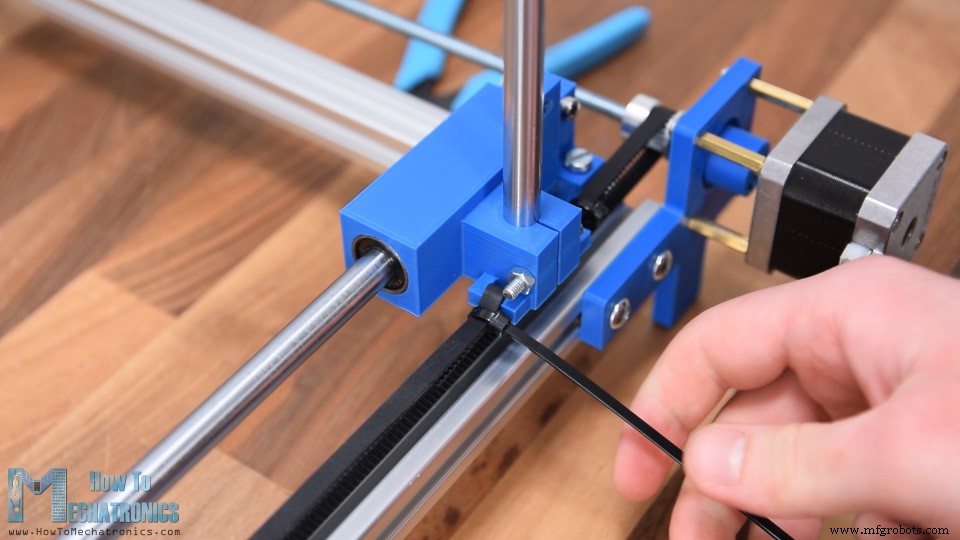
Я повторил этот процесс и для другой стороны. При закреплении другой стороны мы должны убедиться, что два скользящих блока находятся в одном и том же положении по оси X. Для этого мы можем просто переместить их к концу рельсов, чтобы мы могли натянуть ремень и закрепить его стяжкой. На этом механизм скольжения по оси X готов.
Связанный:Самодельный перьевой плоттер с автоматической сменой инструмента | Чертежный станок с ЧПУ
Далее таким же методом соберем механизм оси Y. Для крепления ремня к скользящему блоку снова используем стяжки. Здесь выдвижной блок имеет только одну ручку, и для того, чтобы закрепить ремень, я сначала привязал один конец ремня молнией, затем натянул ремень, чтобы он был достаточно тугим, и другой стяжкой зацепил оба конца ремня. Теперь я могу просто снять предыдущую стяжку и отрезать лишний пояс. Как упоминалось ранее, при закреплении ремня с другой стороны мы должны убедиться, что два скользящих блока находятся в одном и том же положении по оси Y. С этим механизм оси Y также сделан.
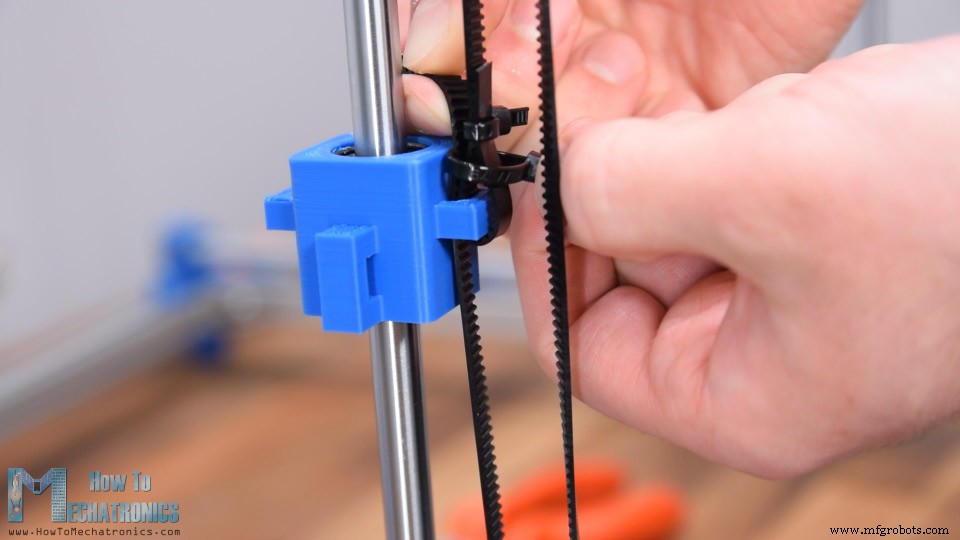
Далее я прикреплю еще один Т-образный профиль по оси X. Этот профиль будет служить для крепления к нему 3-го шагового двигателя, а также для размещения на нем кусков пенопласта. С помощью 3-го шагового двигателя мы можем создавать на этой машине 2,5-мерные или фактически трехмерные фигуры, например, шахматную фигуру.
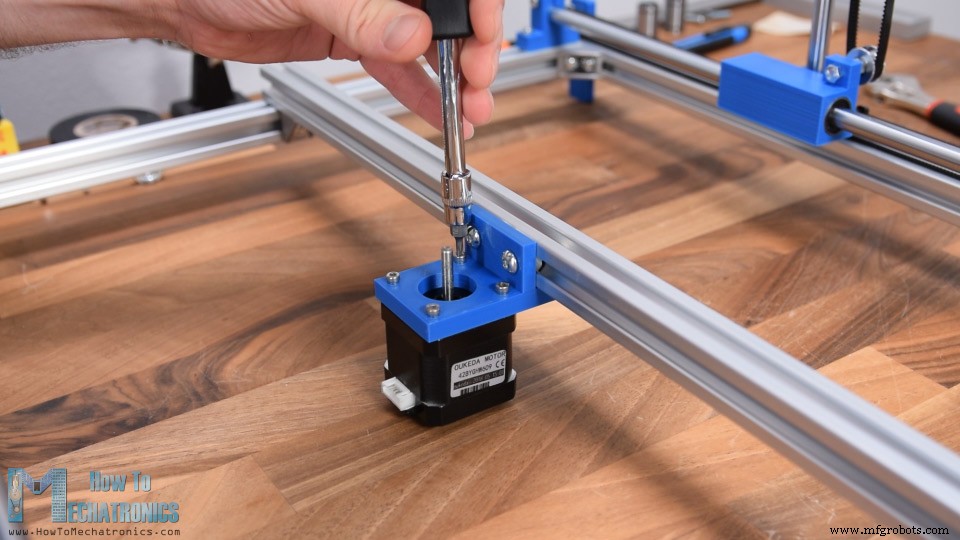
Итак, теперь нам нужно установить резистивный провод. Этот провод должен выдерживать высокие температуры, сохраняя при этом одинаковую температуру по всей длине. Обычно это нихромовая проволока или рыболовная проволока из нержавеющей стали, которые на самом деле недороги и их легко достать. Для правильной работы проволока должна быть натянута между двумя башнями или скользящими блоками, и вот как я это сделал. Я прикрепил болты M5 к обоим скользящим блокам и добавил к ним небольшие пружины растяжения.
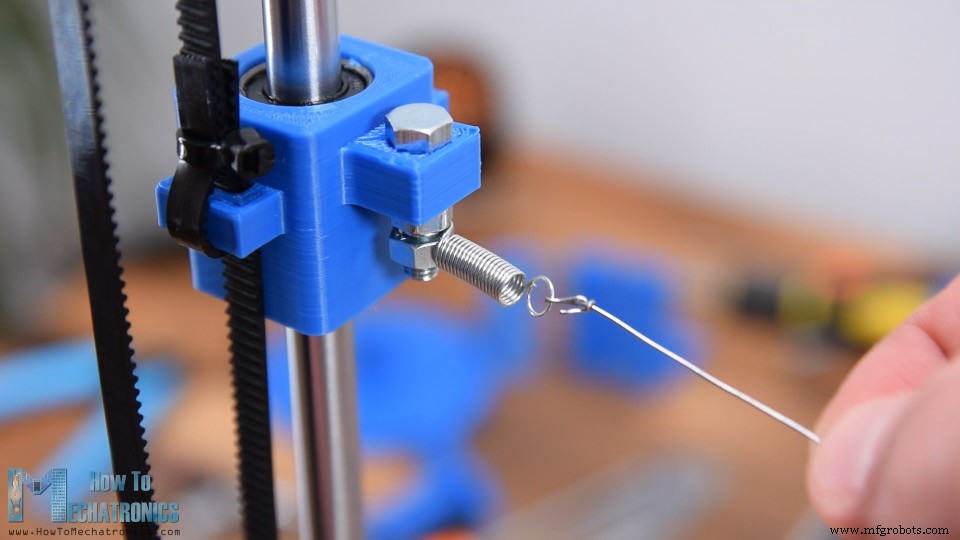
Затем я просто прикрепил проволоку к пружинам. Я натянул проволоку настолько, насколько позволяли пружины. Проволока должна быть натянута вот так с пружинами, потому что, когда она нагреется, она также увеличит свою длину, и пружины смогут это компенсировать.
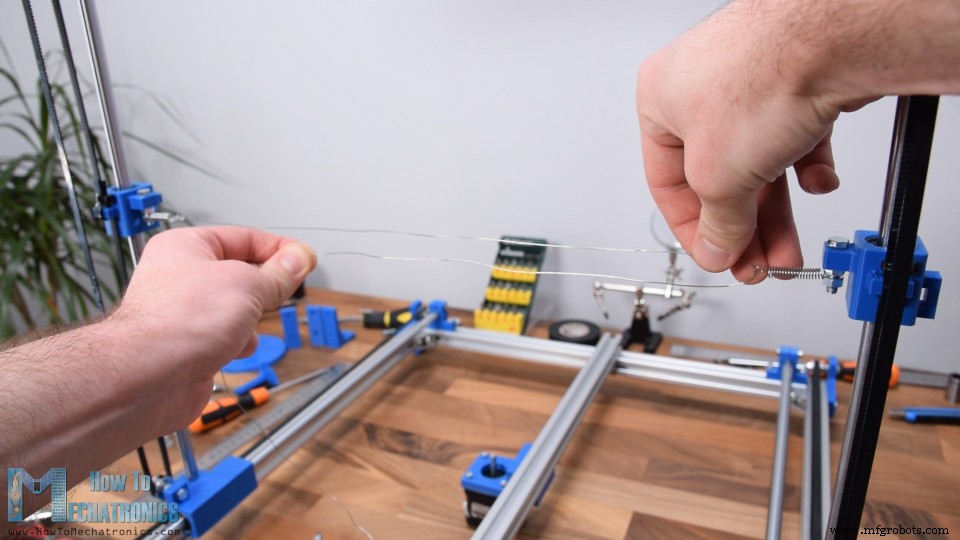
Итак, теперь мы можем соединить провод сопротивления с электрическими проводами. Мы будем использовать питание постоянного тока, поэтому полярность не имеет значения, важно, чтобы ток протекал по проводу, чтобы нагреться. Здесь убедитесь, что ваш электрический провод имеет достаточную галочку, чтобы поддерживать потребление тока от 3 до 5 ампер. В моем случае я использую провод 22-го калибра, но я бы точно рекомендовал провод 20-го или 18-го калибра.
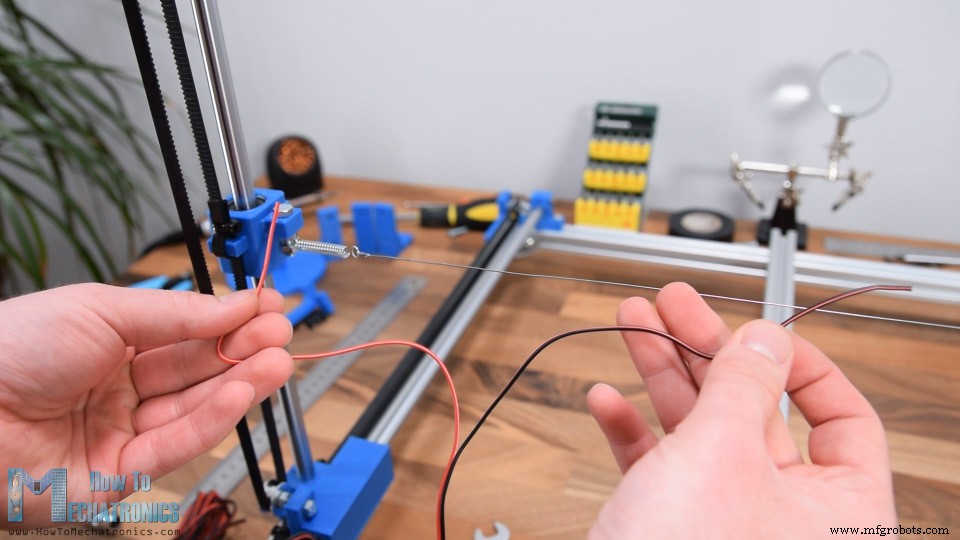
Сначала я прикрепил электрический провод между двумя гайками, чтобы ток мог проходить через катушку к проводу сопротивления. На самом деле это не сработало, и я покажу вам, почему через минуту. Я провел провод через ручки выдвижного блока, чтобы оставаться аккуратным и подальше от горячего провода.
Далее нам нужно установить концевые упоры или концевые выключатели станка с ЧПУ. Эти микроконцевые выключатели имеют 3 соединения:заземление, нормально разомкнутое и нормально замкнутое соединение. Первоначально я подключил их к нормально открытым соединениям, но после con
во время некоторых тестов я переключился на нормально замкнутое соединение, потому что так машина работает более стабильно.
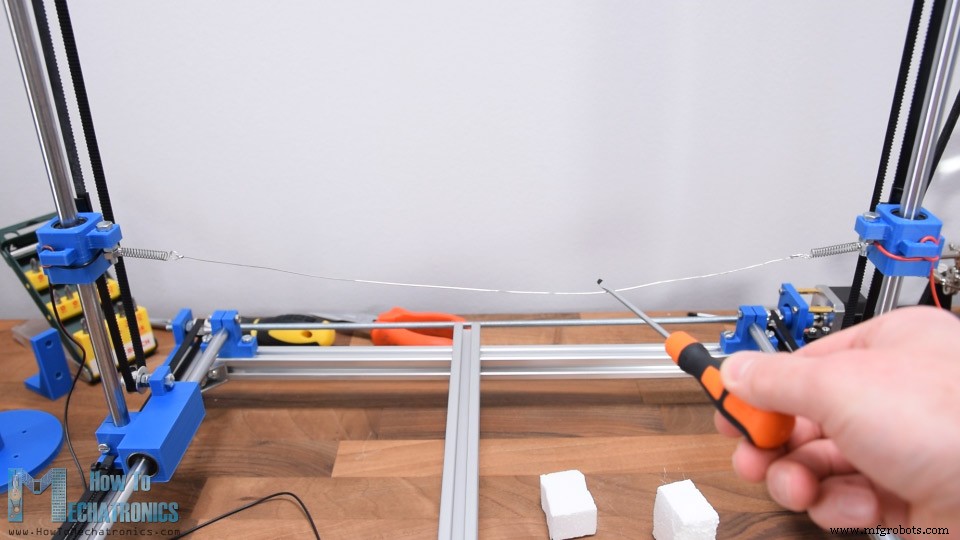
Проблема заключается в электрических помехах, создаваемых во время работы станка с ЧПУ, которые ложно срабатывают переключатели, как будто они нажаты, и приводят к остановке станка.
Схема резки пенопласта с ЧПУ Arduino
Далее мы можем подключить кабели шаговых двигателей, а затем посмотреть, как подключить все электронные компоненты. Вот принципиальная схема того, как все должно быть подключено.
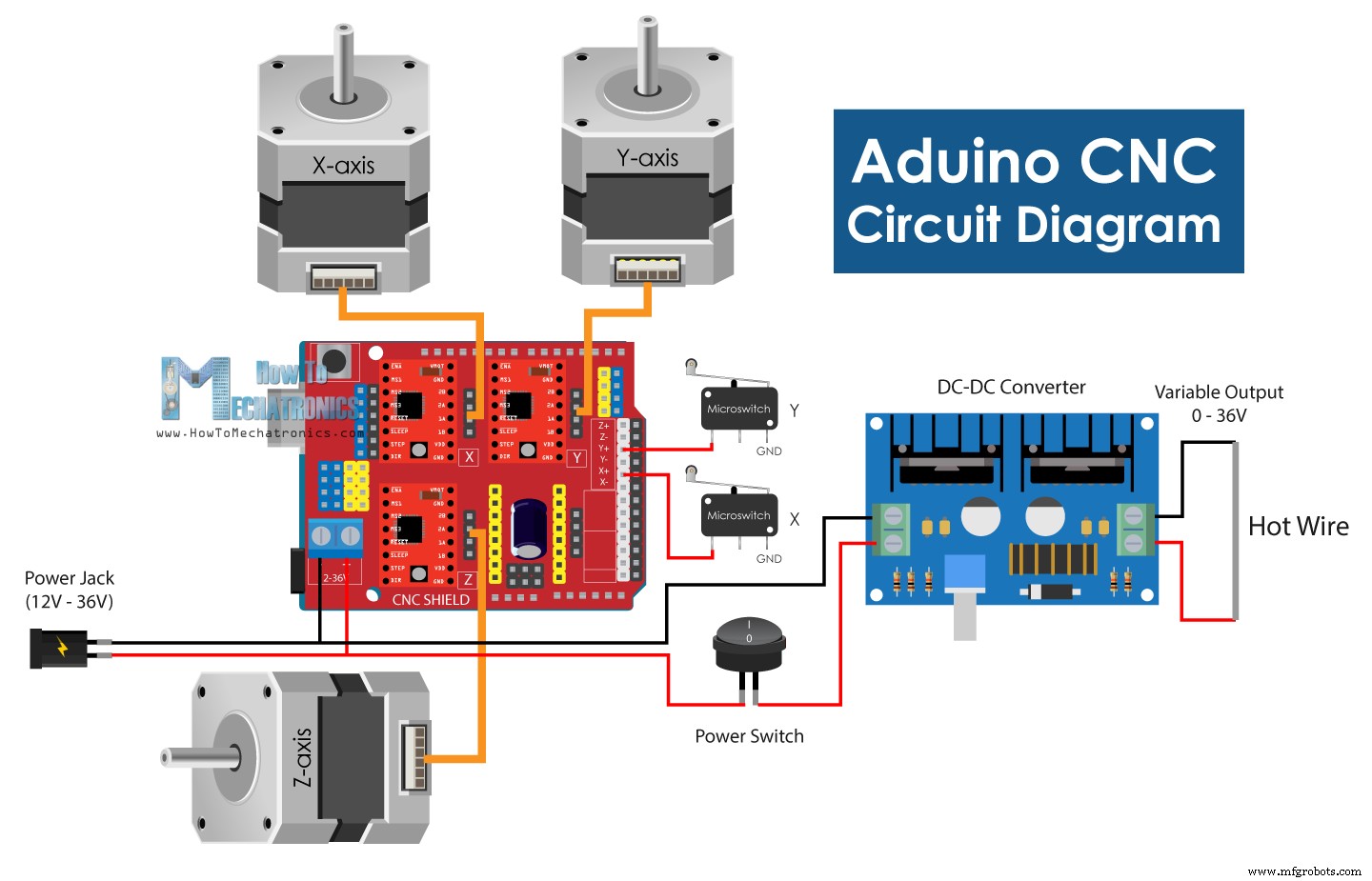
Конечно же, мозгом этого станка с ЧПУ является плата Arduino. Наряду с этим нам также понадобится Arduino CNC Shield, три шаговых драйвера A4988 и преобразователь постоянного тока в постоянный для управления температурой горячей проволоки.
Вы можете получить компоненты, необходимые для этого проекта, по ссылкам ниже:
- Шаговый двигатель — NEMA 17…………
- Драйвер шагового двигателя A4988……………….…
- Arduino CNC Shield …………………….. Amazon / Бангуд / AliExpress
- Ардуино Уно………………………………..…
- Преобразователь постоянного тока …………………………
- Концевой переключатель …………………………………….. Amazon / Бангуд / AliExpress
- Блок питания постоянного тока ………………………… Amazon / Banggood / AliExpress
Я напечатал на 3D-принтере подставку для электронных компонентов, которую прикрепил к одной стороне Т-образного паза. С помощью болтов M3 сначала я прикрепил плату Arduino к подставке, а затем поверх нее вставил плату Arduino с ЧПУ.
Далее нам нужно выбрать разрешение, при котором драйверы шаговых двигателей будут управлять двигателями с помощью некоторых перемычек. В моем случае я выбрал разрешение 16-го шага, добавив три перемычки к каждому драйверу, чтобы степперы двигались более плавно.
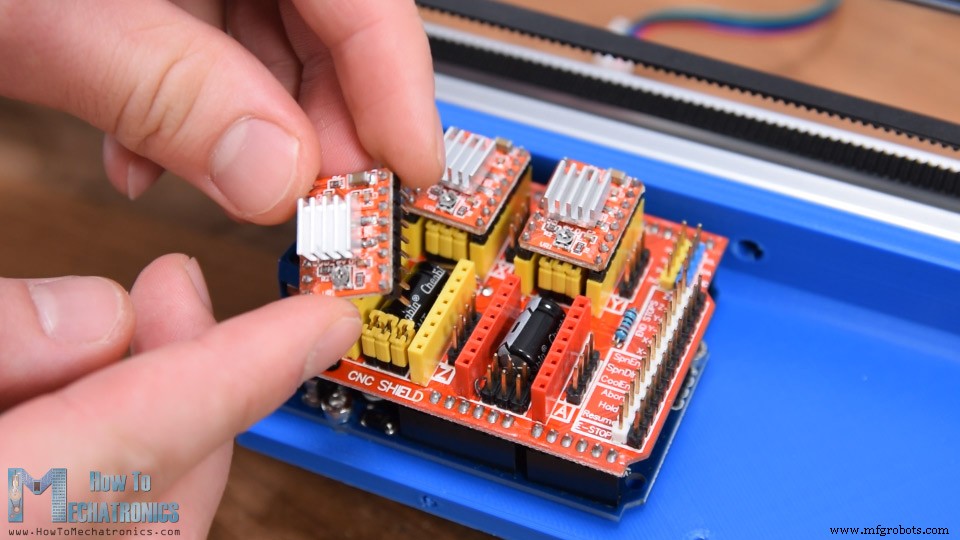
При размещении драйверов убедитесь, что их ориентация правильная, маленький потенциометр может быть индикатором того, что должно быть ориентировано на нижнюю часть экрана.
Я продолжил закреплять преобразователь постоянного тока на месте. Затем я подключил три шаговых двигателя к плате Arduino с ЧПУ, а также два концевых выключателя к концевым стопорным контактам X+ и Y+. Для питания станка я буду использовать блок питания 12В 6А постоянного тока. Плата Arduino CNC на самом деле может работать от 12 до 36 вольт, а также конкретный преобразователь постоянного тока, который я использую, может работать с теми же напряжениями. На вход преобразователя постоянного тока я добавил переключатель, чтобы я мог включать и выключать горячий провод отдельно. На выходе преобразователя постоянного тока я просто соединил два провода с двух концов провода сопротивления. Наконец, мы можем подключить и запитать Arduino через USB-порт, а плату Arduino с ЧПУ и шаговые двигатели — через штепсельную вилку постоянного тока.
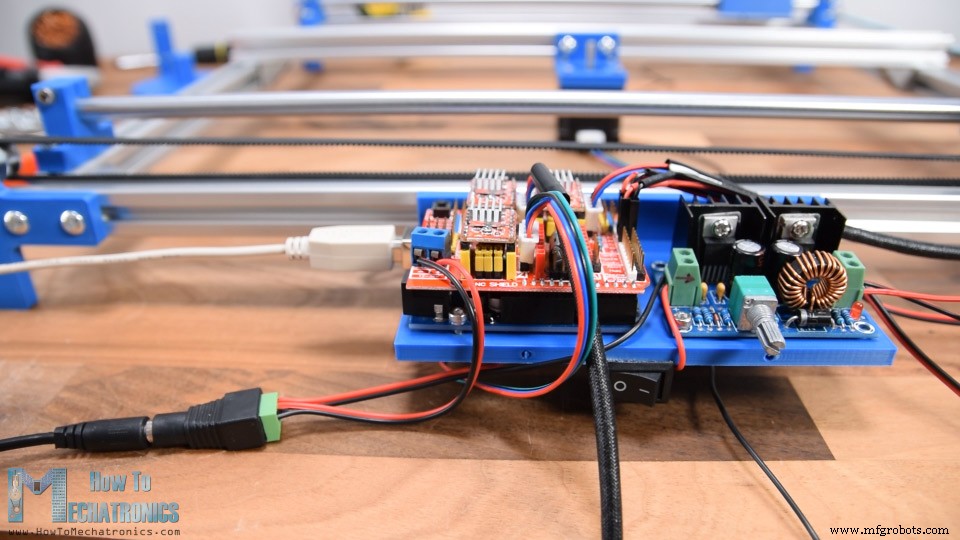
Итак, теперь пришло время проверить машину, работает ли она должным образом, и я начну с горячей проволоки. Вы можете видеть здесь, у меня есть 0 вольт на входе преобразователя постоянного тока, и как только я включаю переключатель, я получаю 12 вольт на входе. Затем на выходе преобразователя постоянного тока снова ноль вольт, но когда мы начинаем поворачивать потенциометр, мы можем регулировать выходное напряжение от 0 до 12 В, и поэтому ток течет через горячий провод и преждевременно его температуру.
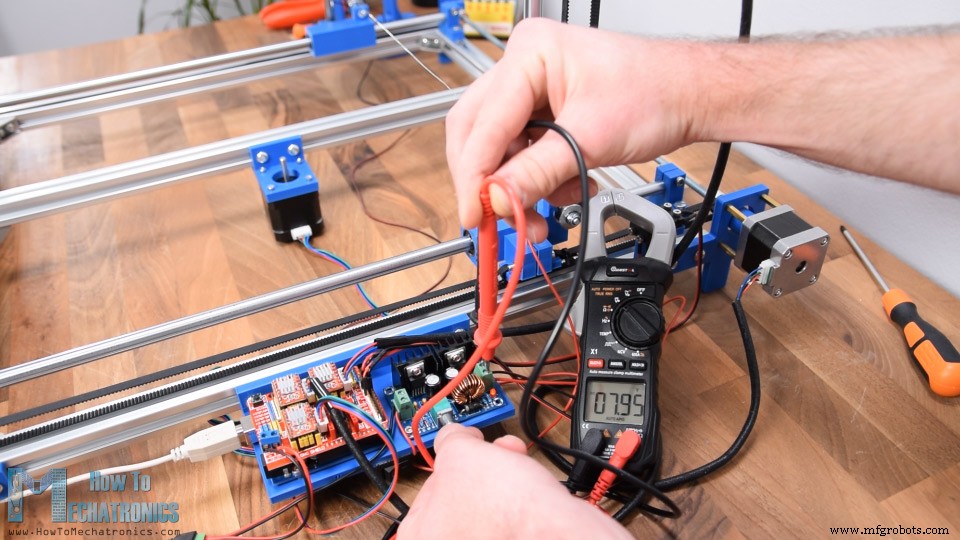
Лучший способ проверить, какое напряжение следует установить на выходе преобразователя постоянного тока, — попытаться разрезать кусок пенопласта. Горячая проволока должна прорезать пенопласт без особого сопротивления и изгиба.
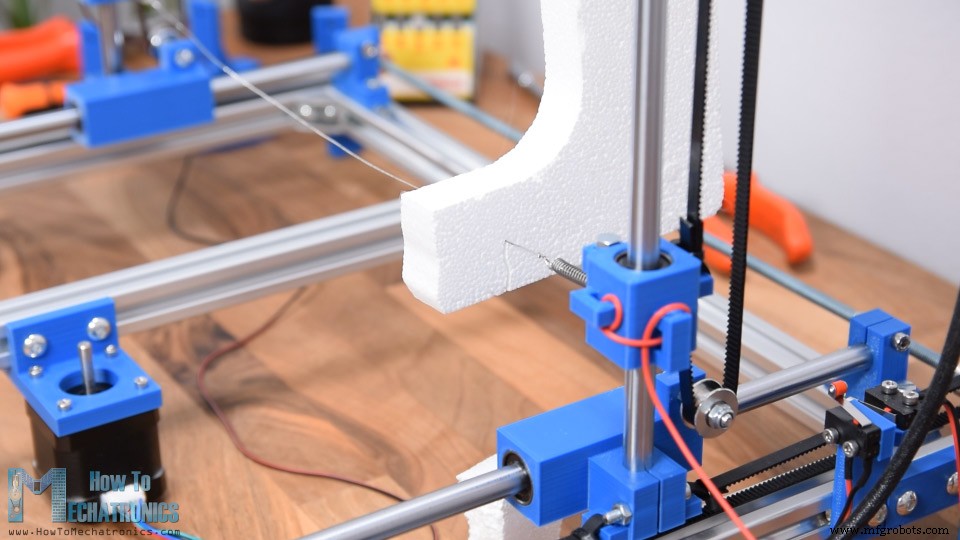
Тем не менее, после первоначального тестирования вы можете увидеть, что произошло с моей горячей проволокой. Он растянулся из-за жары, и пружины, которые должны были это компенсировать, не сработали.
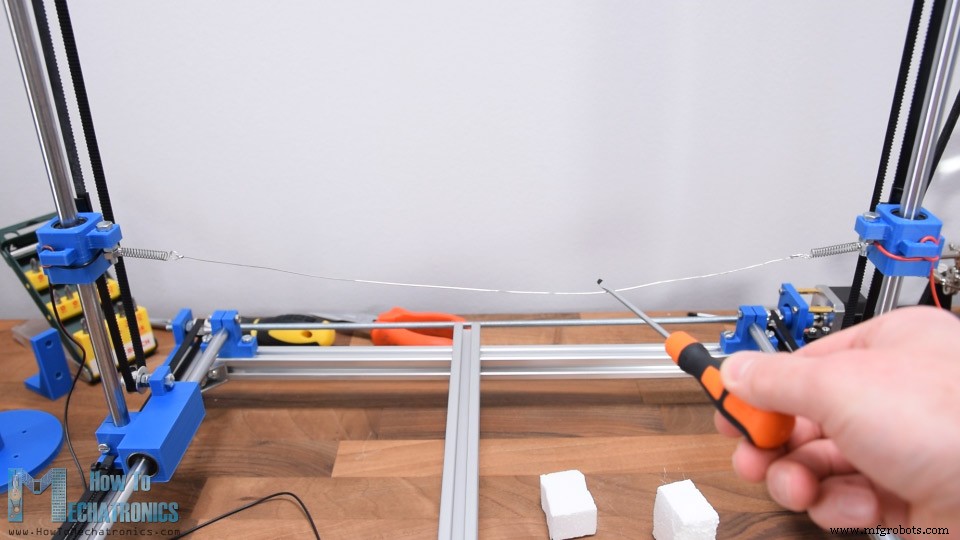
Собственно, пружины потеряли свою функциональность из-за перегрева, потому что при такой конфигурации ток протекал и по ним.
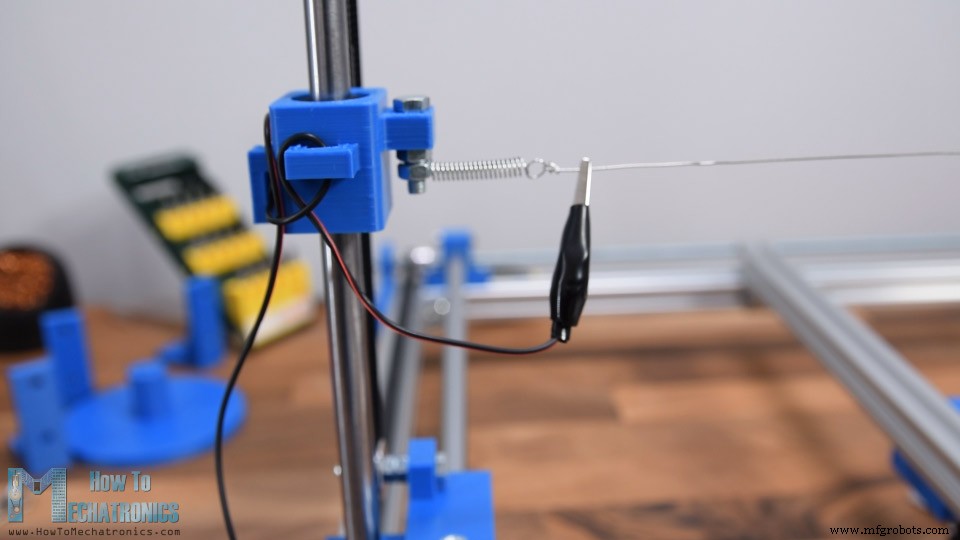
Итак, я заменил старые пружины на новые, и теперь я обошел пружины, подключив электрические провода напрямую к проводу сопротивления с помощью зажимов типа «крокодил».
Программное обеспечение для станков с ЧПУ Arduino
Хорошо, теперь пришло время оживить этот станок и превратить его в настоящий станок с ЧПУ.
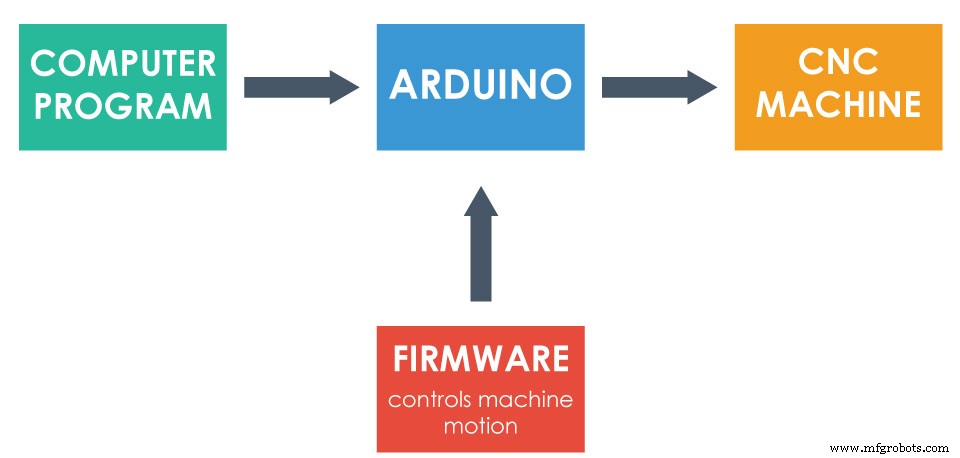
Для этого сначала нам нужно загрузить в Arduino прошивку, которая управляет движением машины. Самый популярный выбор для самодельных станков с ЧПУ — прошивка GRBL.
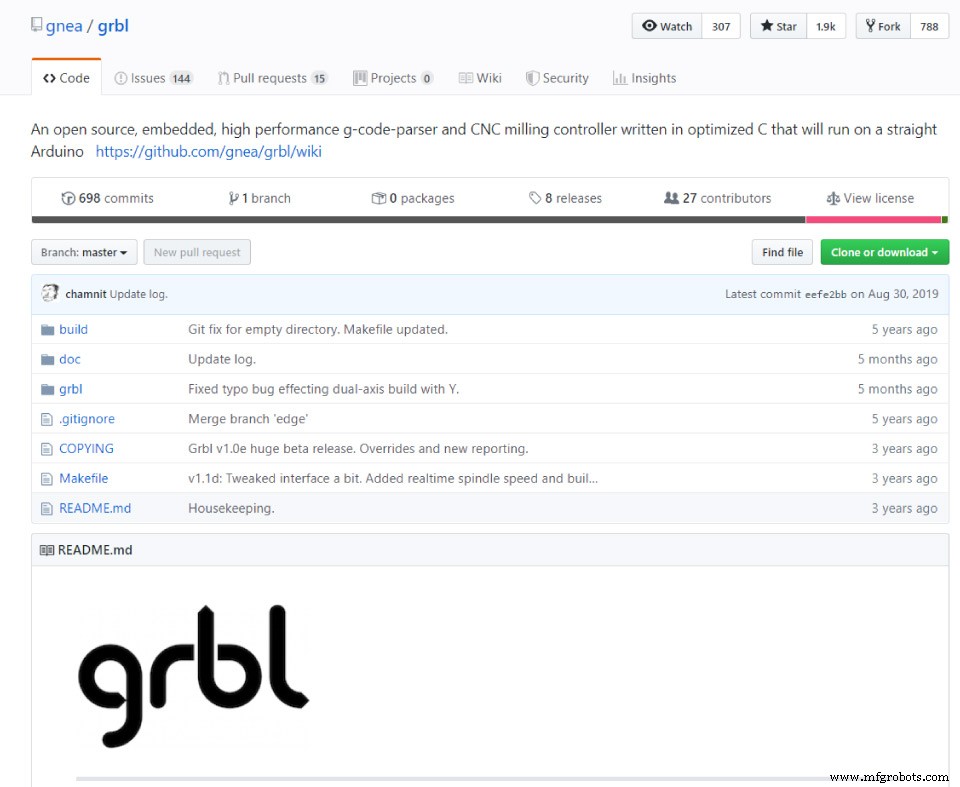
Это открытый исходный код, и мы можем загрузить его с GitHub.com. Как только мы загрузим его в виде zip-файла, мы можем извлечь его, скопировать папку «grbl» и вставить в каталог библиотеки Arduino. Затем мы можем открыть среду разработки Arduino и в меню «Файл»> «Примеры»> grbl выбрать пример grblUpload. Теперь нам нужно выбрать плату Arduino, которую мы используем, Arduino UNO, и выбрать COM-порт, к которому подключена наша Arduino, и, наконец, загрузить этот скетч в Arduino. После загрузки Arduino теперь знает, как читать G-коды и как управлять машиной в соответствии с ними.
Затем нам нужен какой-то интерфейс или контроллер, который будет общаться и говорить Arduino, что делать. Опять же, для этой цели я выбираю программу с открытым исходным кодом, и это универсальный отправитель G-кода.
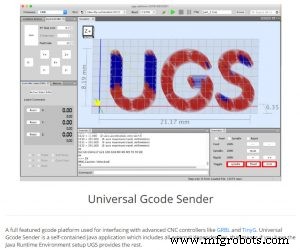
Я скачал версию платформы 2.0. Для запуска программы нам нужно распаковать zip-файл, перейти в папку «bin» и открыть любой из исполняемых файлов ugsplatfrom. На самом деле это программа JAVA, поэтому, чтобы иметь возможность запускать эту программу, сначала нам нужно установить JAVA Runtime Environment. Мы также можем скачать это бесплатно с официального сайта.
Итак, как только мы откроем программу Universal G-Code Sender, нам нужно запустить мастер установки, чтобы настроить машину.
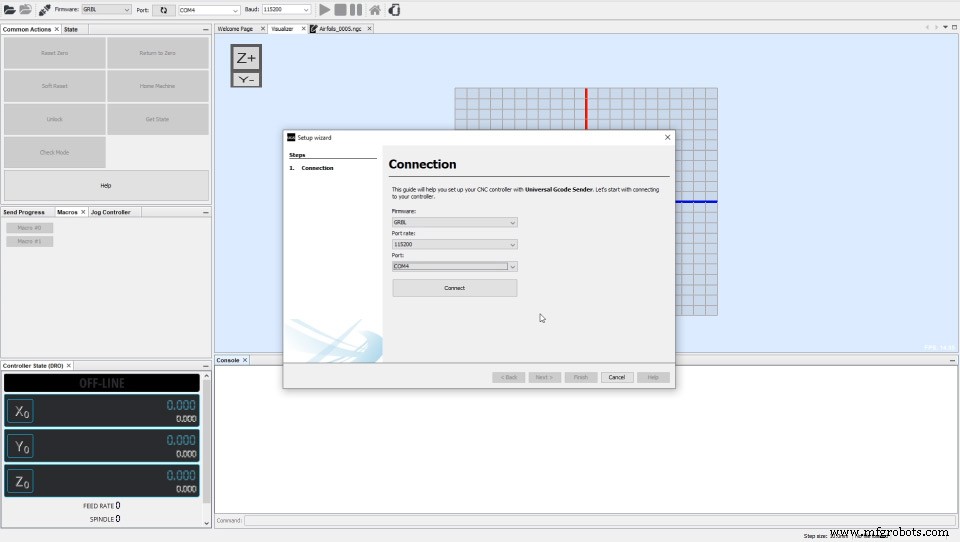
Здесь нам нужно просто выбрать правильный порт и подключить программу к Arduino. Как только соединение установлено, мы можем проверить направление движения моторов, нажимая кнопки. При необходимости мы можем изменить направление. Я выбрал положительные движения, чтобы перейти от исходного положения, где расположены концевые выключатели, к другим сторонам.
Далее нам нужно откалибровать шаги моторов, чтобы добиться правильных и точных движений. Как мы выбрали 16 го шаговое разрешение драйверов, а двигатели имеют 200 физических шагов, это означает, что потребуется 3200 шагов, чтобы двигатель совершил полное движение на 360 градусов. Теперь, в зависимости от типа трансмиссии или, в данном случае, размера шкивов, нам нужно рассчитать количество шагов, необходимых двигателю, чтобы машина переместилась на 1 мм. Значение по умолчанию здесь установлено на 250 шагов на мм. Итак, как только мы нажмем одну из этих кнопок перемещения, мотор сделает 250 шагов.
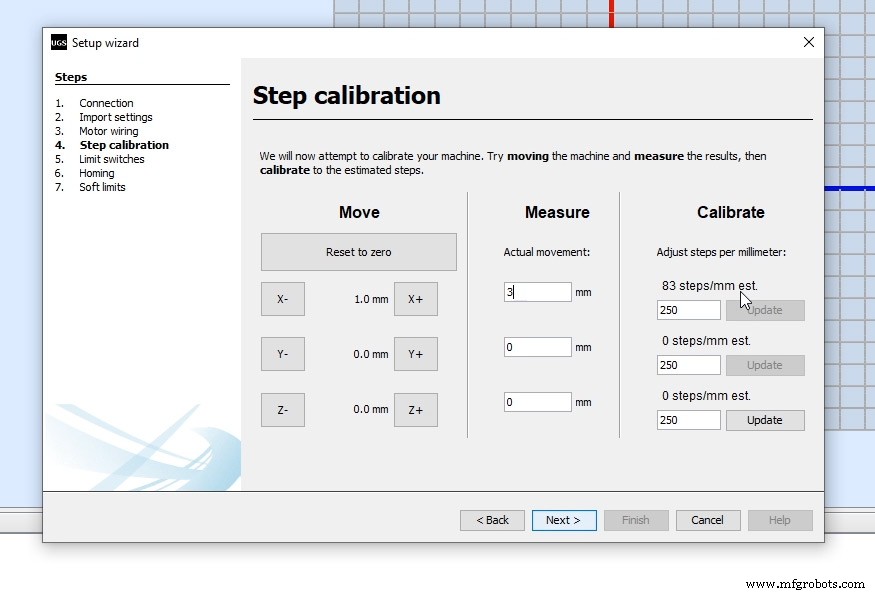
Теперь на самом деле, используя линейку, мы измеряем фактическое движение машины и вводим это число здесь, в программу. В соответствии с этим программа рассчитает и сообщит нам значение, которое мы должны изменить и обновить параметр шагов/мм. В моем случае это 83 шага/мм. Что касается оси Z, я установил ее на 400 шагов/мм, или это означает, что значение 1 мм для оси Z сделает поворот на 45 градусов.
Далее нам нужно проверить, правильно ли работают концевые выключатели. В зависимости от того, соединили ли мы их NO или NC, мы также можем инвертировать их здесь. Как я уже говорил, соединение NC работало лучше для меня. В любом случае, здесь мы должны заметить, что нам нужно отключить концевой выключатель оси Z, поскольку у нас его нет в нашей машине. Если мы не выключим его, мы не сможем вернуть машину домой. Для этого нам нужно перейти в папку grbl в библиотеке Arduino и отредактировать файл config.h.
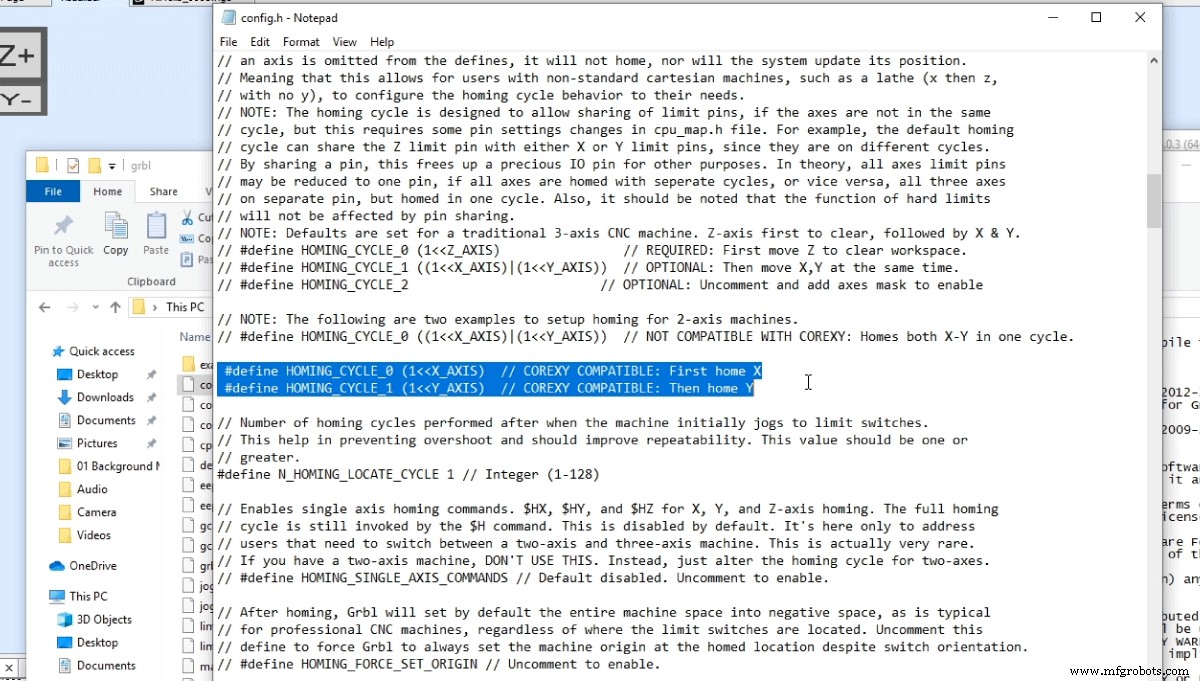
Здесь нам нужно найти линии цикла возврата в исходное положение и закомментировать набор по умолчанию для 3-осевого станка с ЧПУ и раскомментировать настройку для 2-осевого станка. Теперь нам нужно сохранить файл и повторно загрузить пример grblUpload в Arduino. Обратите внимание, что вам, вероятно, следует перезапустить программы еще раз, чтобы все заработало правильно.
Итак, теперь мы можем попытаться вернуть машину в исходное положение с помощью кнопки "Попробовать возврат". При нажатии машина должна начать двигаться к концевому выключателю X, а после нажатия она начнет двигаться по оси Y. При необходимости мы можем изменить направление концевых выключателей. В конце мастера настройки мы можем установить Soft Limits, которые фактически ограничивают максимальное расстояние, которое машина может пройти в каждом направлении. В моем случае это 45x45 см.
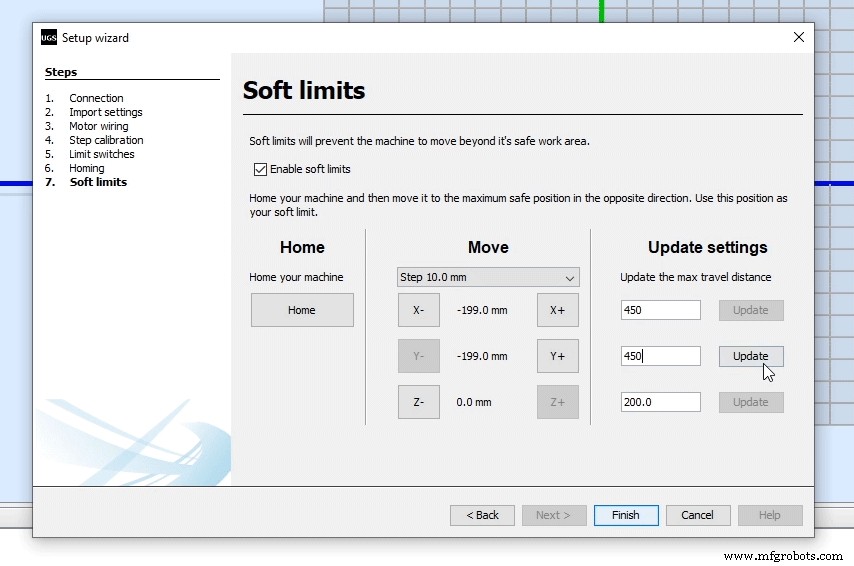
Итак, теперь программа готова к работе. Перед каждым использованием вы всегда должны перезагрузить машину, а затем вы можете делать все, что хотите. Во-первых, я бы посоветовал поиграть и протестировать контроллер Jog или вручную переместить машину. Также на этом этапе следует попробовать отрезать несколько кусков пенопласта, чтобы выяснить, какая скорость подачи или скорость движения будут наиболее подходящими для вас.
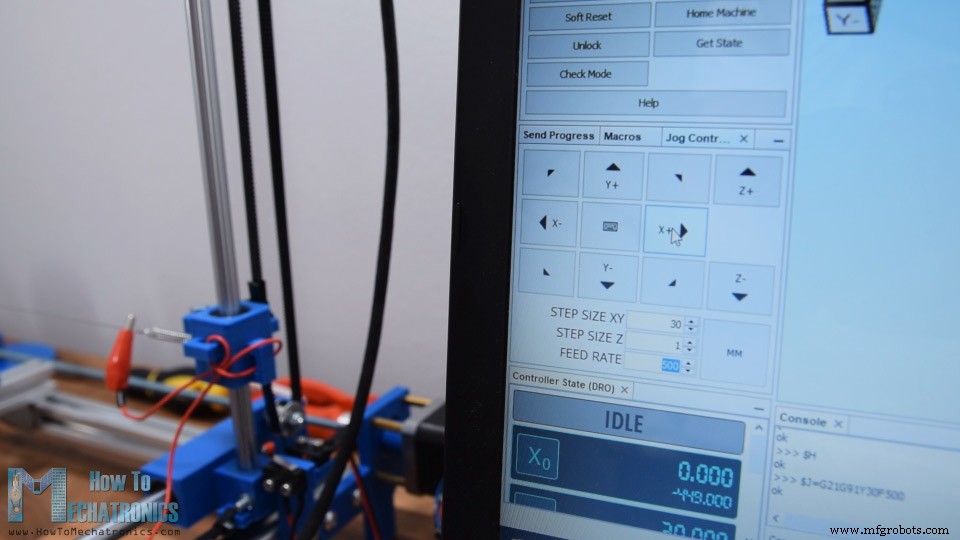
Таким образом, вам следует поэкспериментировать с температурой горячей проволоки и скоростью подачи, чтобы выяснить, что даст вам наиболее чистый и точный рез на кусках пенопласта.
Генерация G-кода для станка с ЧПУ
Наконец, в этом видео осталось посмотреть, как подготовить чертежи, чтобы станок с ЧПУ мог создавать из них формы. Для этой цели нам понадобится программное обеспечение для векторной графики, и снова я выбрал программное обеспечение с открытым исходным кодом, и это Inkscape. Вы можете скачать его с официального сайта бесплатно.
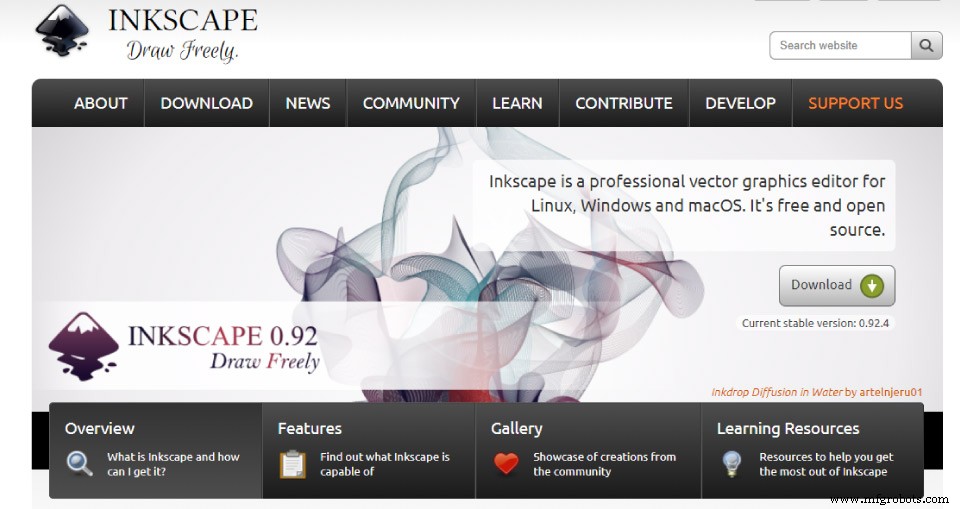
Я покажу вам два примера, как подготовить G-код для станка с ЧПУ Arduino с помощью Inkscape. Итак, сначала мы должны установить размер страницы в соответствии с размером нашей рабочей области, а именно 45x45 см. Для первого примера я скачал изображение логотипа Arduino и импортировал его в программу. С помощью функции Trace Bitmap нам нужно преобразовать изображение в векторный формат.
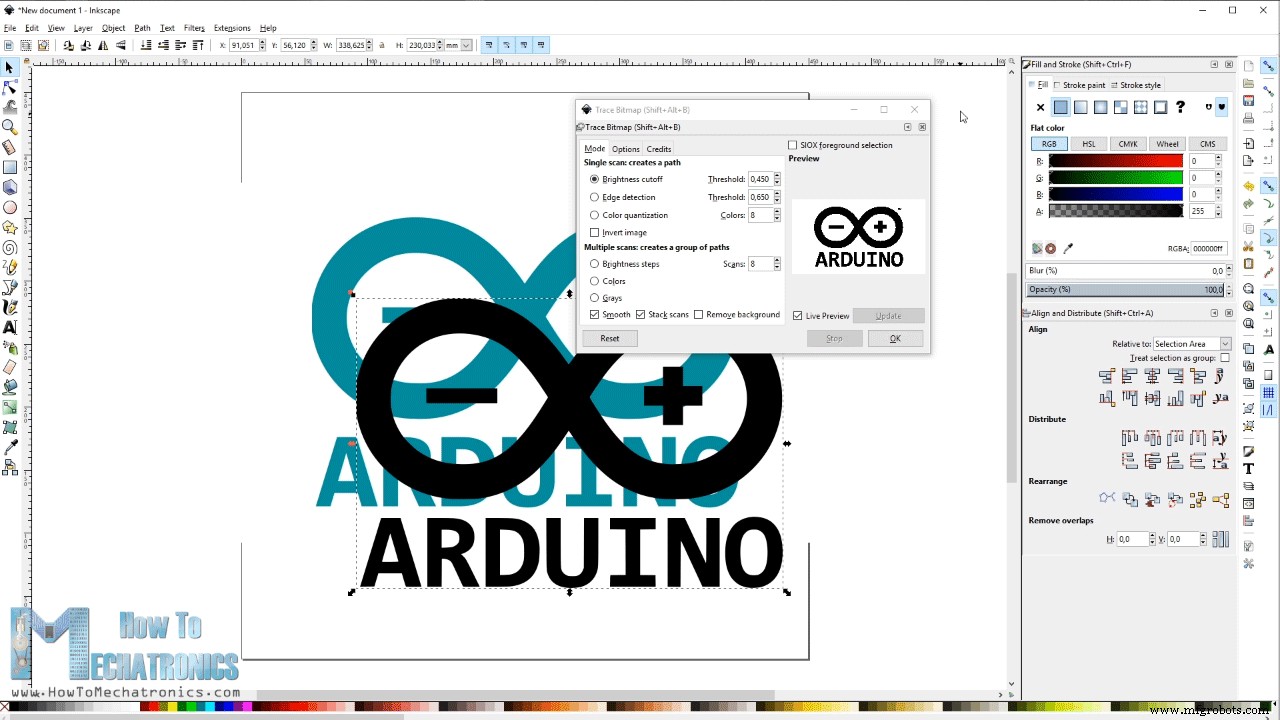
Теперь, чтобы иметь возможность разрезать эту фигуру горячей проволокой, нам нужно сделать форму непрерывной траекторией. Это связано с тем, что горячая проволока всегда присутствует в рабочей зоне, ее нельзя приподнять, например, немного, или отключить в случае лазера при переходе от одной буквы или формы к другой. Поэтому, используя простые квадраты, я соединил все отдельные части вместе. Мы делаем это, выбирая части, а затем используем функцию объединения. С другой стороны, внутренние замкнутые контуры должны быть открыты, и мы делаем это с помощью функции Difference.
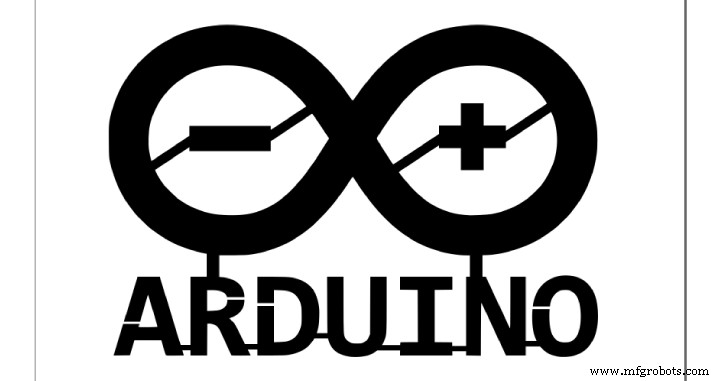
Итак, когда у нас есть готовый рисунок, мы можем использовать расширение Gcodetools для создания G-кода. Во-первых, нам нужно создать точки ориентации.
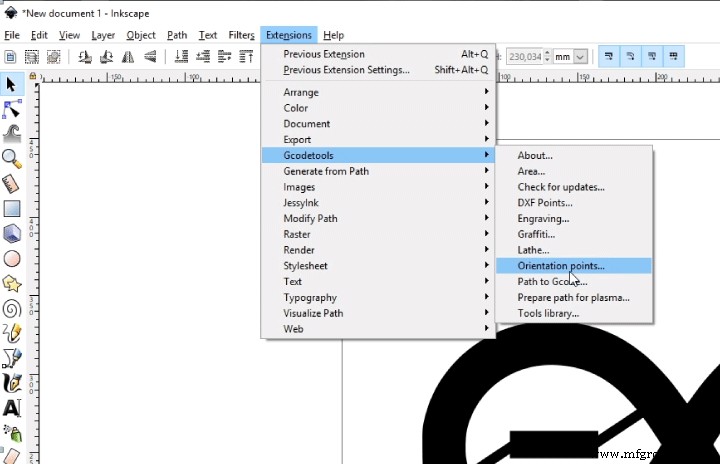
Затем мы можем масштабировать нашу модель до желаемого размера. Далее нам нужно перейти в библиотеку инструментов и с ее помощью определить инструмент, который мы используем для станка с ЧПУ Arduino. Мы можем выбрать цилиндр, поскольку проволока, очевидно, имеет цилиндрическую форму. Здесь мы можем изменить такие параметры, как диаметр инструмента, я установил его на 1 мм, а также скорость подачи. Остальные параметры в данный момент не важны. Наконец, теперь мы можем сгенерировать G-код для этой фигуры с помощью функции Path to Gcode.
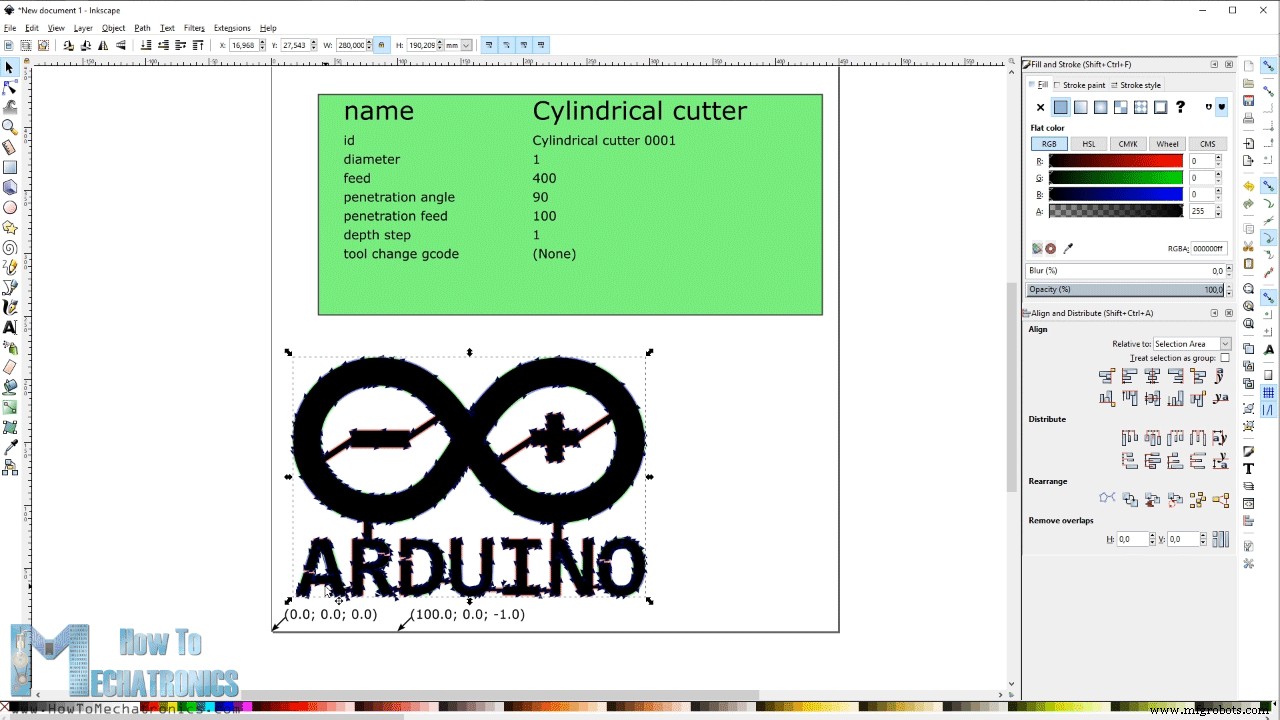
G-код — это просто набор инструкций, которые GRBL или Arduino могут понять и в соответствии с ними управлять шаговыми двигателями. Итак, теперь мы можем открыть G-код в программе отправки Универсального G-кода и через окно Визуализатора мы можем увидеть тот путь, который должна пройти машина.
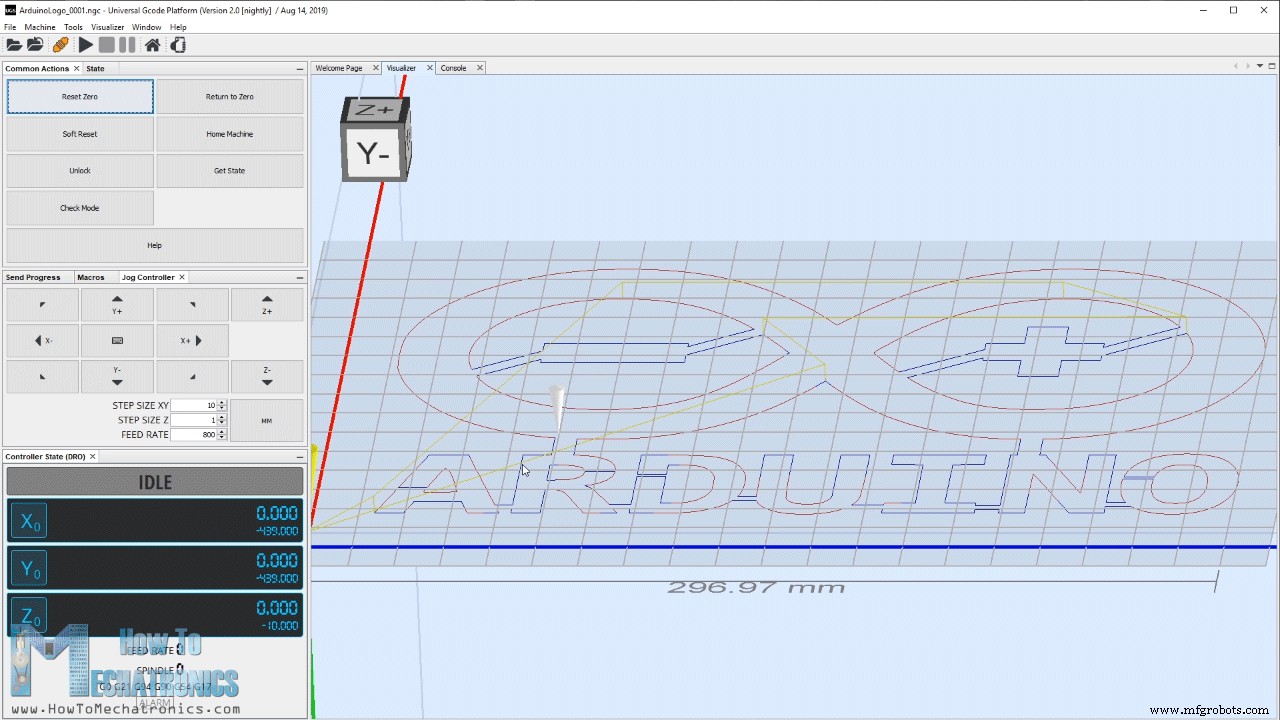
Тем не менее, мы можем заметить здесь желтые линии, которые обозначают пустое путешествие или путешествие по воздуху в случае использования биты или лазера. Как я упоминал ранее, в этом случае горячая проволока не может двигаться по этим ходам, потому что проволока прорежет материал и испортит форму. Здесь мы действительно можем заметить, что у нас нет единого пути для всей формы, потому что мы забыли открыть замкнутые области внутри логотипа. Таким образом, мы можем просто вернуться к чертежу, сделать эти замкнутые области открытыми, а затем снова сгенерировать G-код.
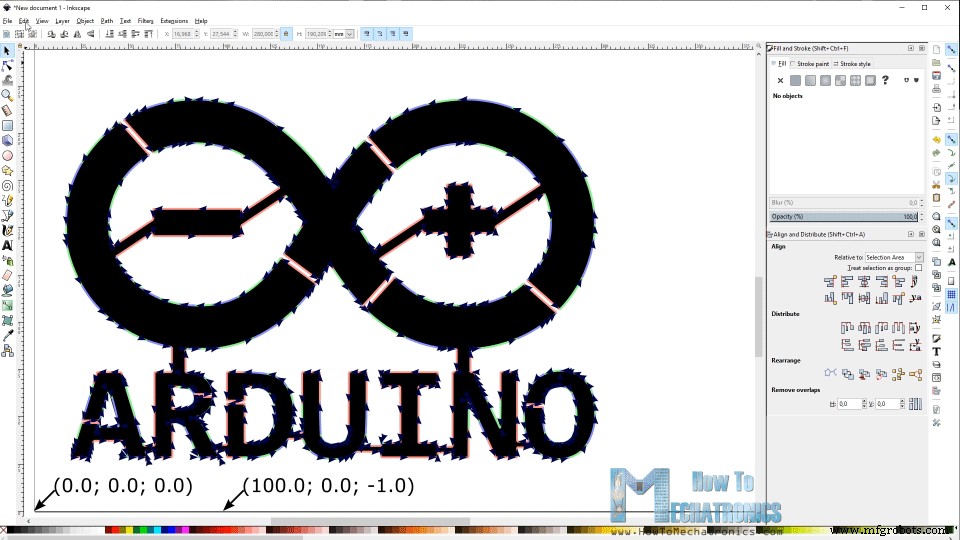
Еще одна вещь, которую следует упомянуть, это хорошая идея, чтобы выбрать собственную начальную точку, дважды щелкнув фигуру, выбрать узел и выбрать «Разорвать путь в выбранном узле». Теперь, если мы откроем новый G-код, мы увидим, что путь начинается с более поздней буквы А, проходит через всю фигуру и заканчивается на букве А.
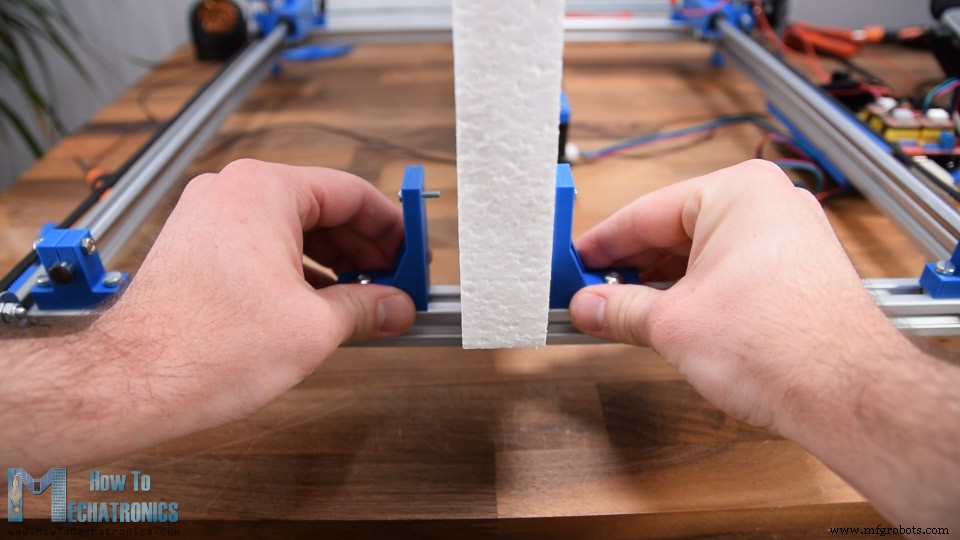
Для крепления деталей из пенопласта к станку с ЧПУ я сделал эти простые держатели с болтами M3, которые проникают в пенопласт и удерживают его на месте.
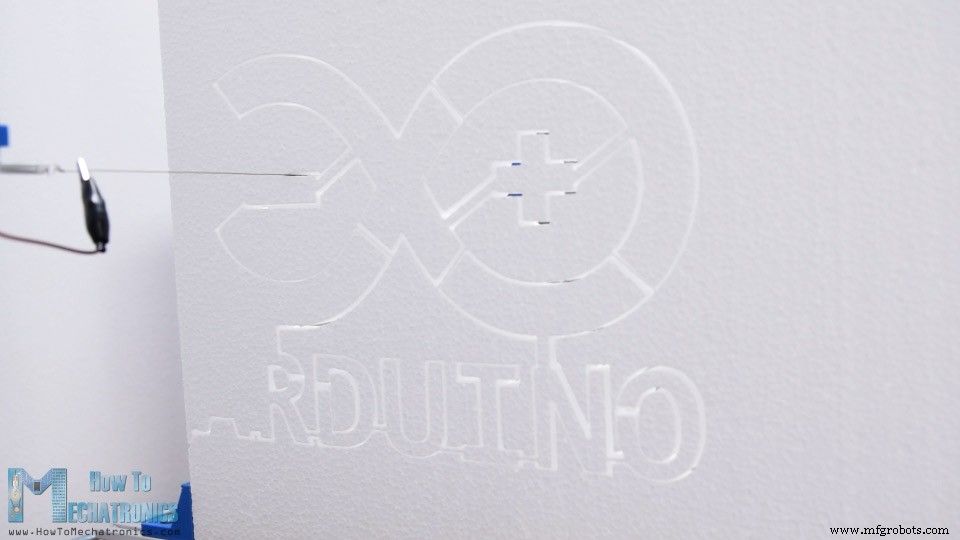
Хорошо, теперь я покажу вам еще один пример того, как сделать трехмерную фигуру. Мы сделаем квадратную форму столба, которую нужно разрезать с четырех сторон под углом 90 градусов друг к другу.

Я получил форму столба с помощью метода Trace Bitmap, показанного ранее. Теперь мы можем нарисовать простой прямоугольник размером с столб и вычесть столб из прямоугольника. Мы удалим одну из сторон, так как нам нужна только одна траектория профиля столба. Итак, это фактический путь, который должен пройти станок с ЧПУ, и после каждого прохождения нам нужно вращать 3-й й степпер 90 градусов.
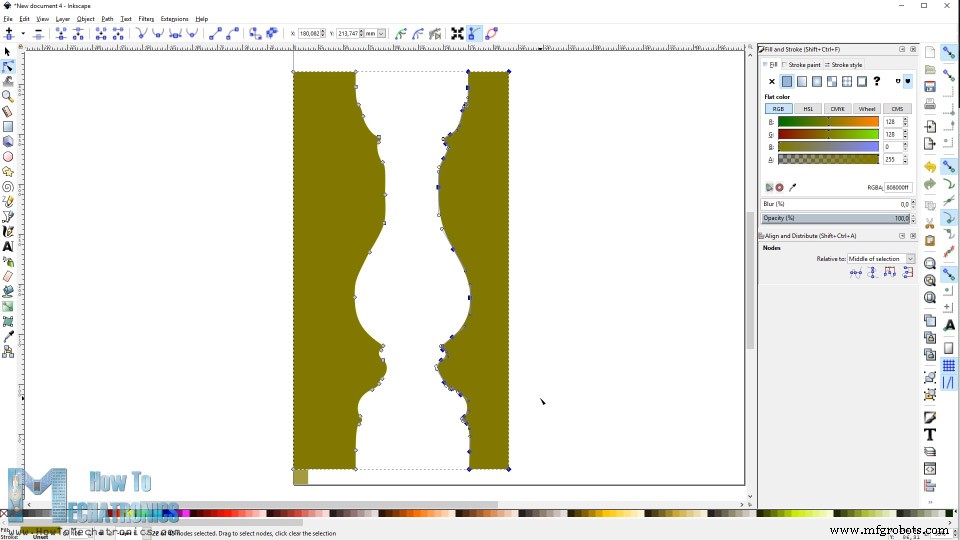
Чтобы сделать это при создании точек ориентации, нам нужно установить глубину Z на -8 мм. Затем в параметрах инструмента нам нужно установить шаг глубины на значение 2 мм. Теперь, после создания G-кода, мы можем открыть его в отправителе G-кода и увидеть, что машина сделает 4 прохода по одному и тому же пути с разницей в глубине 2 мм. В случае фрезерного станка с ЧПУ это будет означать, что каждый раз сверло будет углубляться на 2 мм для резки материала, но здесь, как показано ранее, мы устанавливаем ось Z на 45 градусов с каждым миллиметром или на 90 градусов для перемещения шагового двигателя Z на 2 мм. .
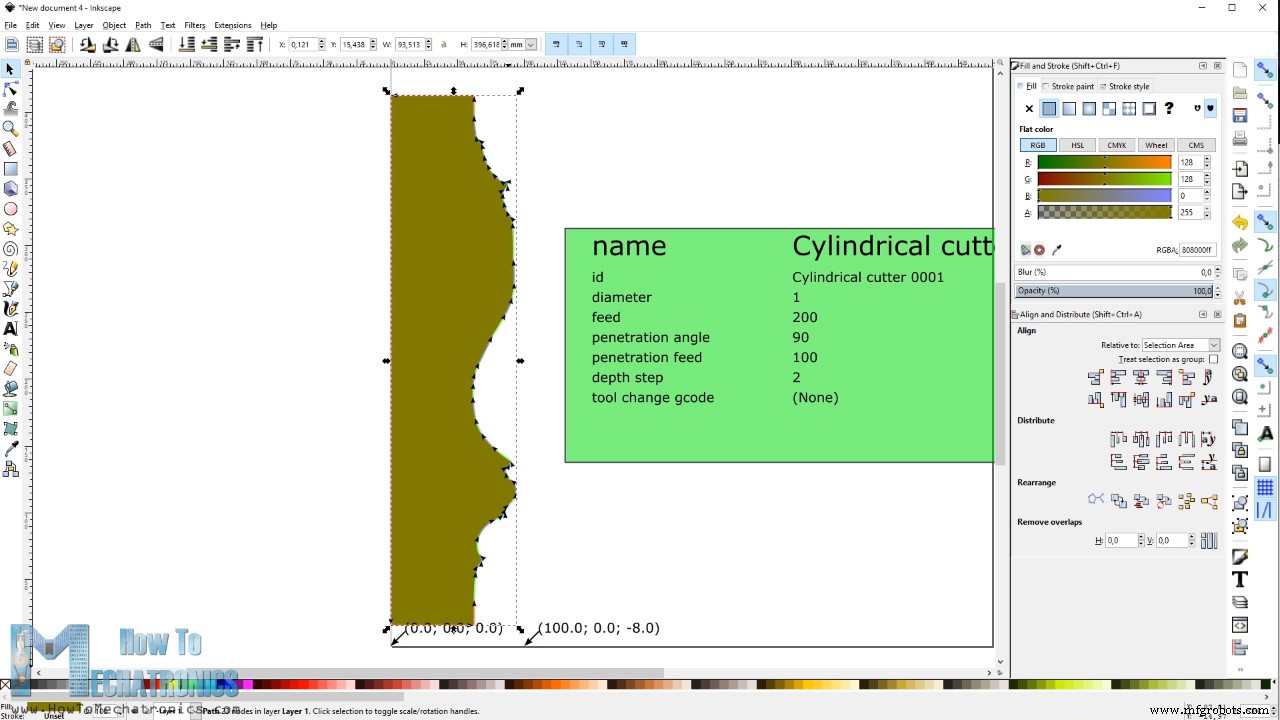
В любом случае, здесь нам также нужно немного изменить G-код. По умолчанию сгенерированный G-код после каждого прохода перемещает ось Z на значение 1 мм, что в случае фрезерного станка с ЧПУ означает, что он поднимает фрезу, когда требуется пустой ход.
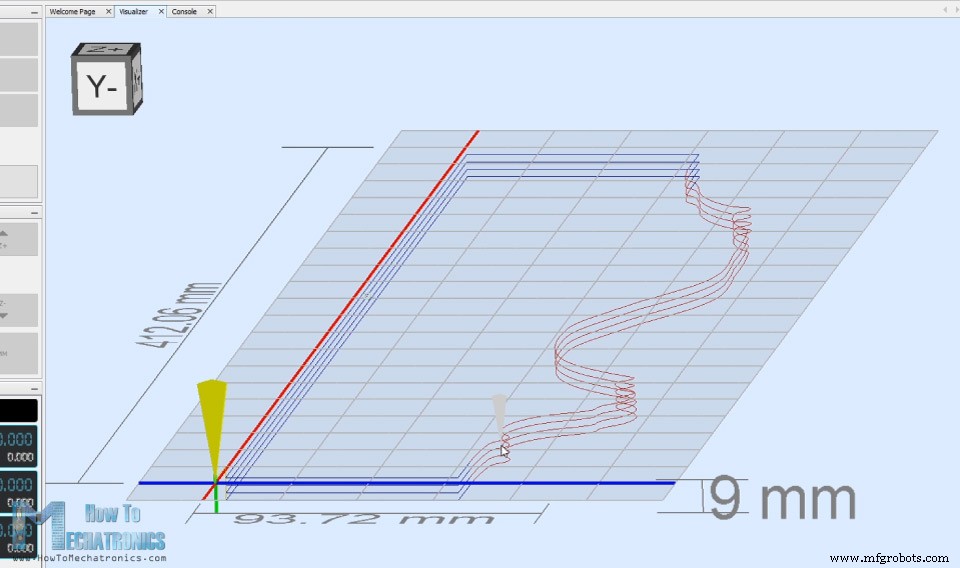
На самом деле, мы могли бы оставить G-код без изменений, но он будет делать ненужные движения по оси Z или вращать пенопласт без всякой причины. Поэтому после каждой итерации кода нам просто нужно изменить значения оси Z, чтобы они оставались на том же месте, не возвращаясь к значению 1 мм.
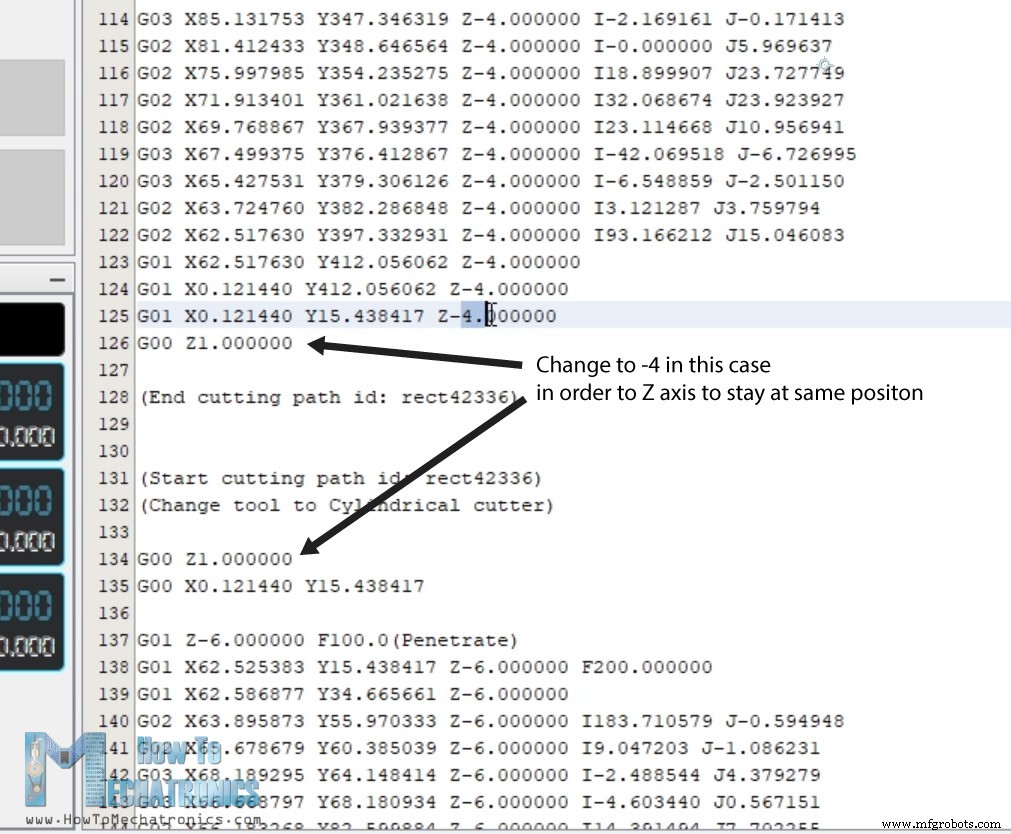
Для установки детали из пенопласта для создания 3D-формы мы используем эту платформу, которая содержит несколько болтов M3, которые вставляются в деталь из пенопласта и удерживают ее во время формирования.
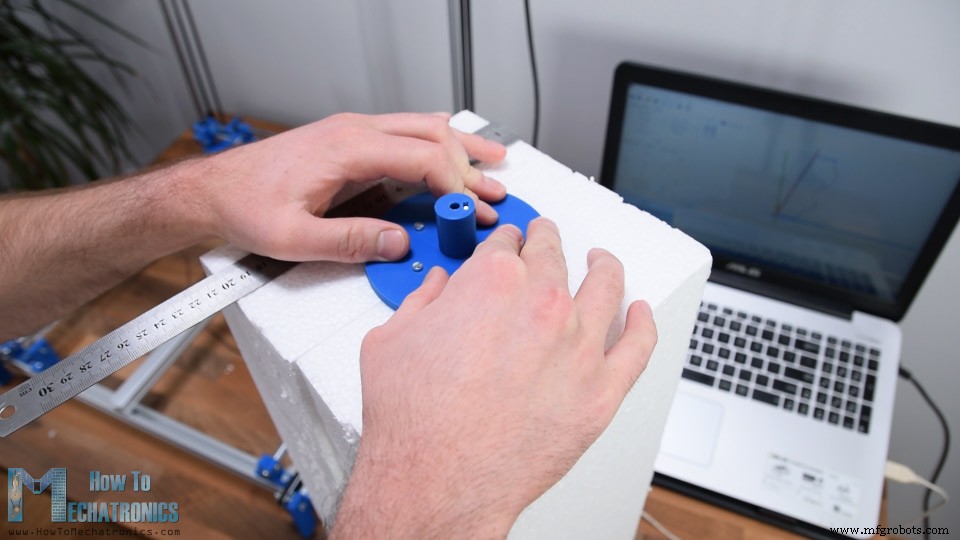
Перед запуском G-кода нам нужно вручную поднести горячую проволоку к куску пенопласта. Расстояние от центра до горячей проволоки должно быть столько, сколько мы хотим, чтобы наша фигура была галочкой. Или, если нам нужен точный размер, как на чертеже, нам нужно измерить расстояние от начала координат до центра фигуры на чертеже.
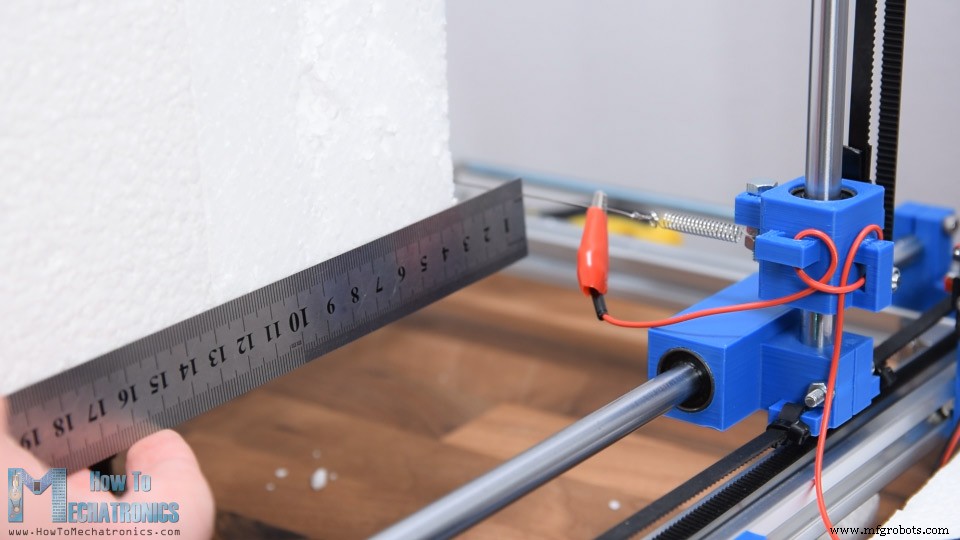
Затем нам нужно нажать кнопку «Сбросить ноль» в контроллере, чтобы сообщить программе, что она должна начинаться отсюда, а не из исходного положения. Вот и все, теперь нам просто нужно нажать кнопку «Воспроизвести», и станок с ЧПУ Arduino создаст 3D-форму.
Вы можете скачать файлы G-кода и файлы Inkscape для всех примеров здесь:
Так что это почти все для этого урока. Я надеюсь, что объяснение было достаточно ясным, и вы сможете сделать свой собственный станок с ЧПУ. Не стесняйтесь задавать любые вопросы в разделе комментариев ниже и проверять мою коллекцию проектов Arduino.
Производственный процесс
- Руководство по созданию прототипов с ЧПУ
- Станок с ЧПУ
- Полное руководство по режущим станкам с ЧПУ
- Что такое ЧПУ?
- Применение фрезы с качающимся ножом с ЧПУ
- Краткое сравнение станков с ЧПУ
- Использование доступного станка с ЧПУ для резки металла в домашних условиях
- 18 Глава 8:ЧПУ
- Введение в станок с ЧПУ Miller
- Полный обзор станков плазменной резки с ЧПУ